13 Overlooked Farm Spare Parts That Halt Operations — Pt. 1
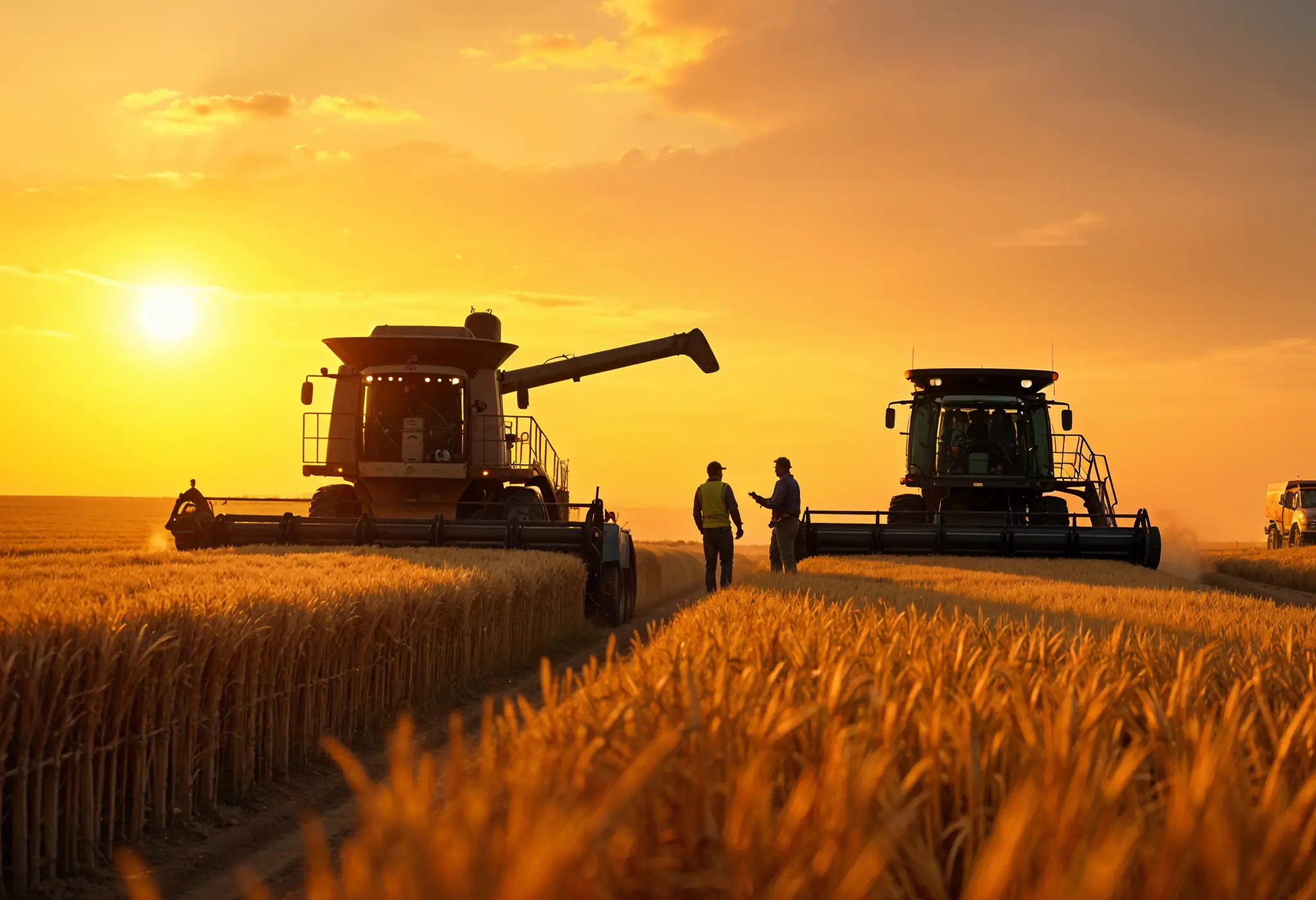
Farm equipment failure often hits when you least expect it—right in the middle of harvest. While you wait days for a part, your window shrinks to hours. The difference between smooth operations and costly downtime lies in critical spare parts management. The ag equipment spare parts market is booming—from $155.7B in 2023 to $189.4B by 2030—but supply chain delays and poor inventory planning still cripple farms. Studies show farmers can cut repair costs by 25% with better maintenance and spare parts control. Digital tracking and CMMS tools reduce errors by 95%. One broken air filter or hydraulic hose can bring everything to a stop.
This guide reveals 13 overlooked but essential farm equipment spare parts. In Part 1, we cover the first 7: air filters, hydraulic hoses, fuel injectors, battery cables, fuses and relays, starter motors, and hydraulic seals. Don’t wait for failure—prepare now.
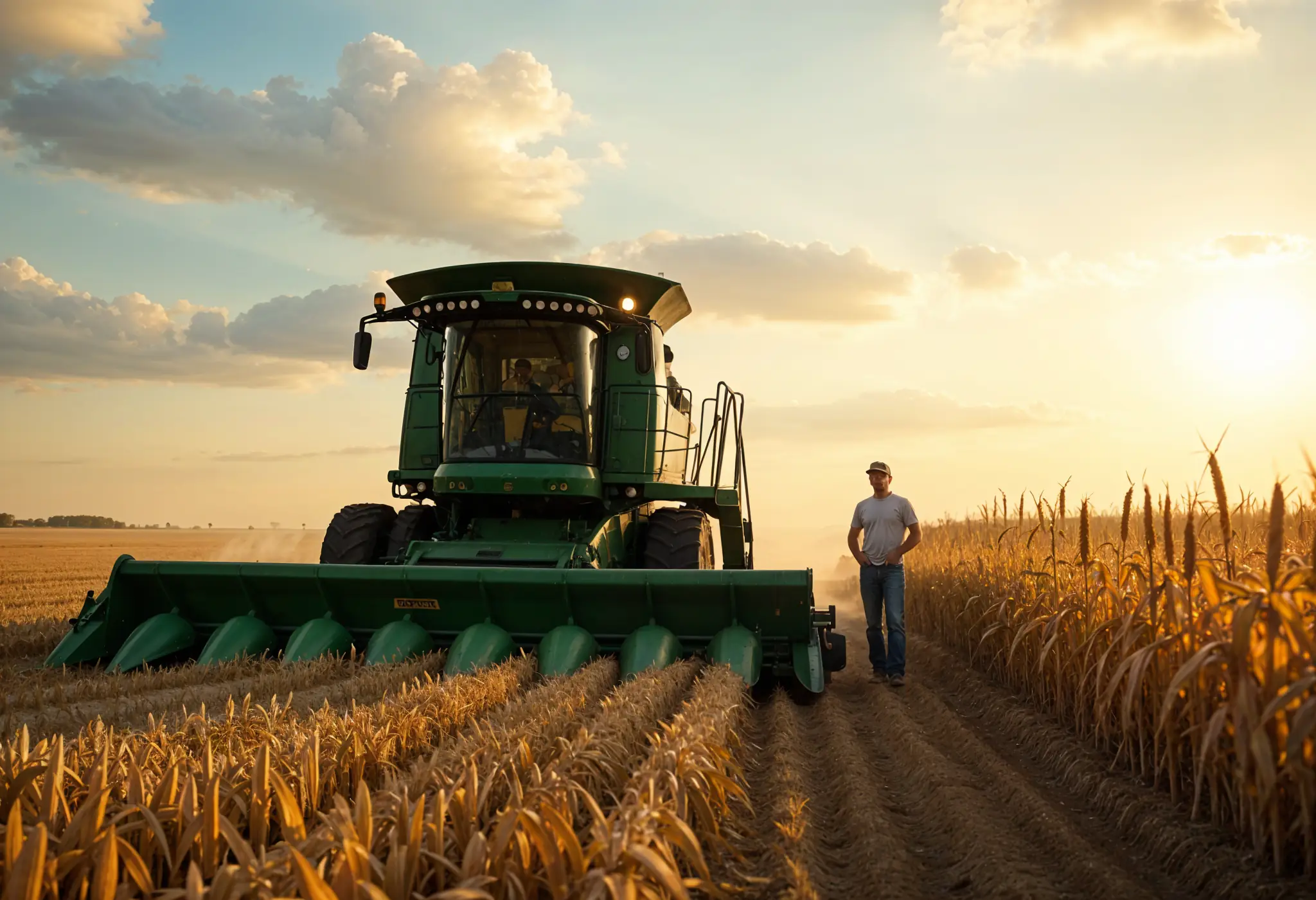
Air Filters
Air filters stand as the primary defense between your tractor's engine and catastrophic damage. When this simple component fails, the consequences often cost thousands in repairs. The humble air filter prevents dust, dirt, and debris from infiltrating your engine's combustion chamber, protecting vital internal components from premature failure.
Air Filters Function
Air filters maintain the precise air-to-fuel ratio essential for optimal engine combustion. They deliver clean, filtered air while trapping harmful particles that would otherwise enter and contaminate your system. Without this protection, abrasive materials quickly wear down pistons, cylinders, and other critical equipment parts. A properly functioning air filter ensures optimal air supply for efficient fuel burning, significantly extending engine life by preventing premature wear.
Why Air Filters Are Often Overlooked
Many farmers misjudge how rapidly these parts become compromised in agricultural environments. Standard maintenance schedules might suggest checking air filters every 100 hours, but dusty farm conditions often require daily inspections. The visual signs of filter degradation rarely appear until significant damage has already occurred. Some equipment owners attempt to extend filter life beyond recommended intervals to save money—a decision that inevitably leads to costlier repairs down the line and increased risk of business interruption.
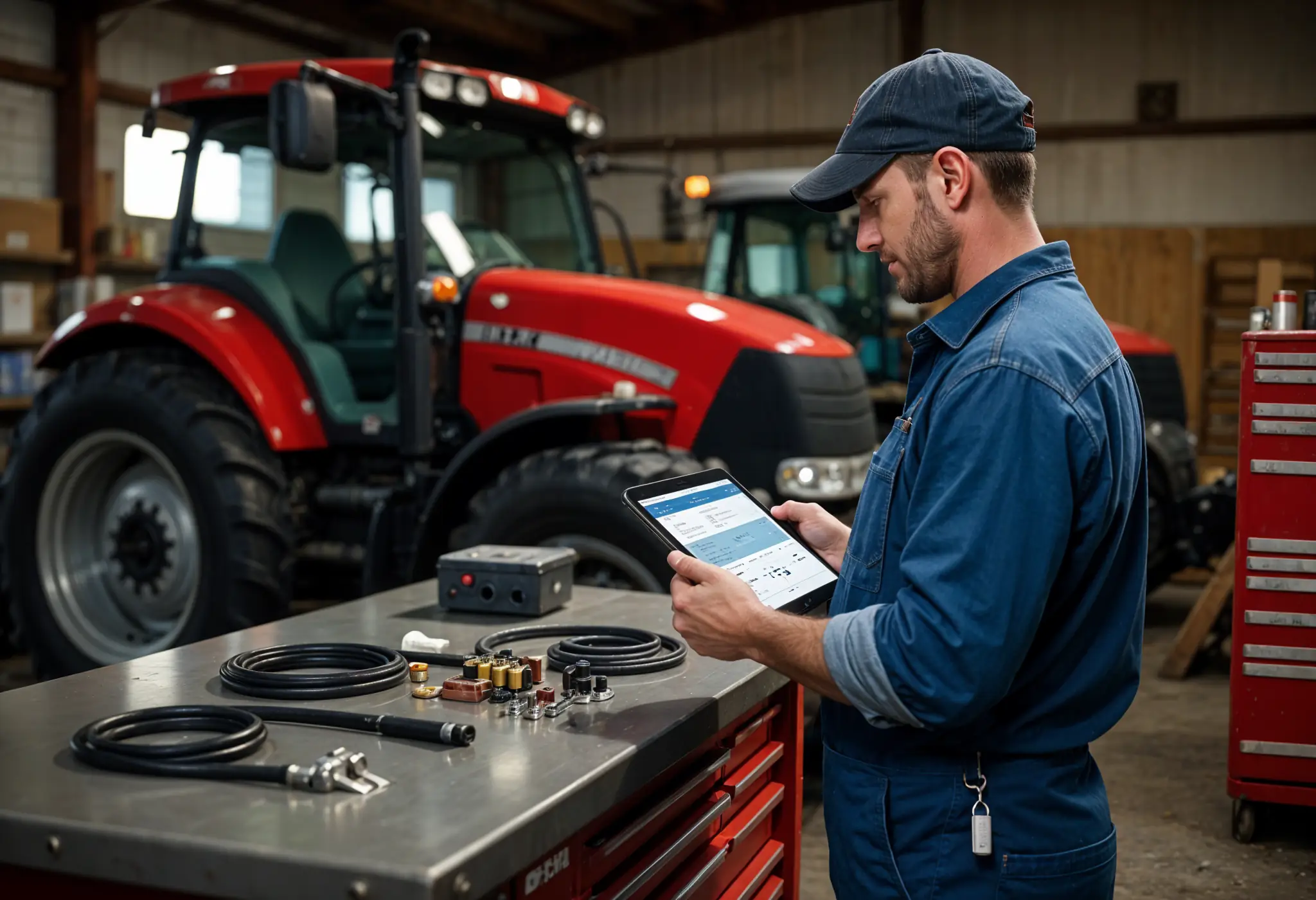
Consequences of Air Filter Failure
The fallout from neglecting this critical spare part hits both performance and profitability:
- Reduced Power and Performance: Clogged filters restrict airflow, forcing engines to work harder while delivering less power.
- Increased Fuel Consumption: Large combines consume 3-5 additional gallons per hour with filters that are 50-75% clogged, potentially costing $240 daily at $4/gallon.
- Engine Damage: When dust bypasses a damaged filter, it causes abrasive wear on cylinders, pistons, and bearings. Even small amounts of unfiltered air can inflict irreversible engine damage.
- Operational Downtime: Equipment failure during critical field operations directly impacts your productivity when you can least afford it.
Research from the University of Missouri found that simply replacing dirty air filters improved tractor engine output by 3.5% on average, saving approximately 105 gallons of fuel annually for a 140-horsepower tractor. This demonstrates the significant impact of proper spare parts operations on overall equipment effectiveness.
Avoid costly downtime before it strikes. Get expert help sourcing the exact critical spare parts your farm needs. Visit MCHPartsNYC.com to request a free quote and consultation now.
Hydraulic Hoses
Hydraulic hoses form the critical circulatory system of your farm equipment. When these components fail, operations stop immediately—often during crucial planting or harvest windows when downtime costs multiply by the hour.
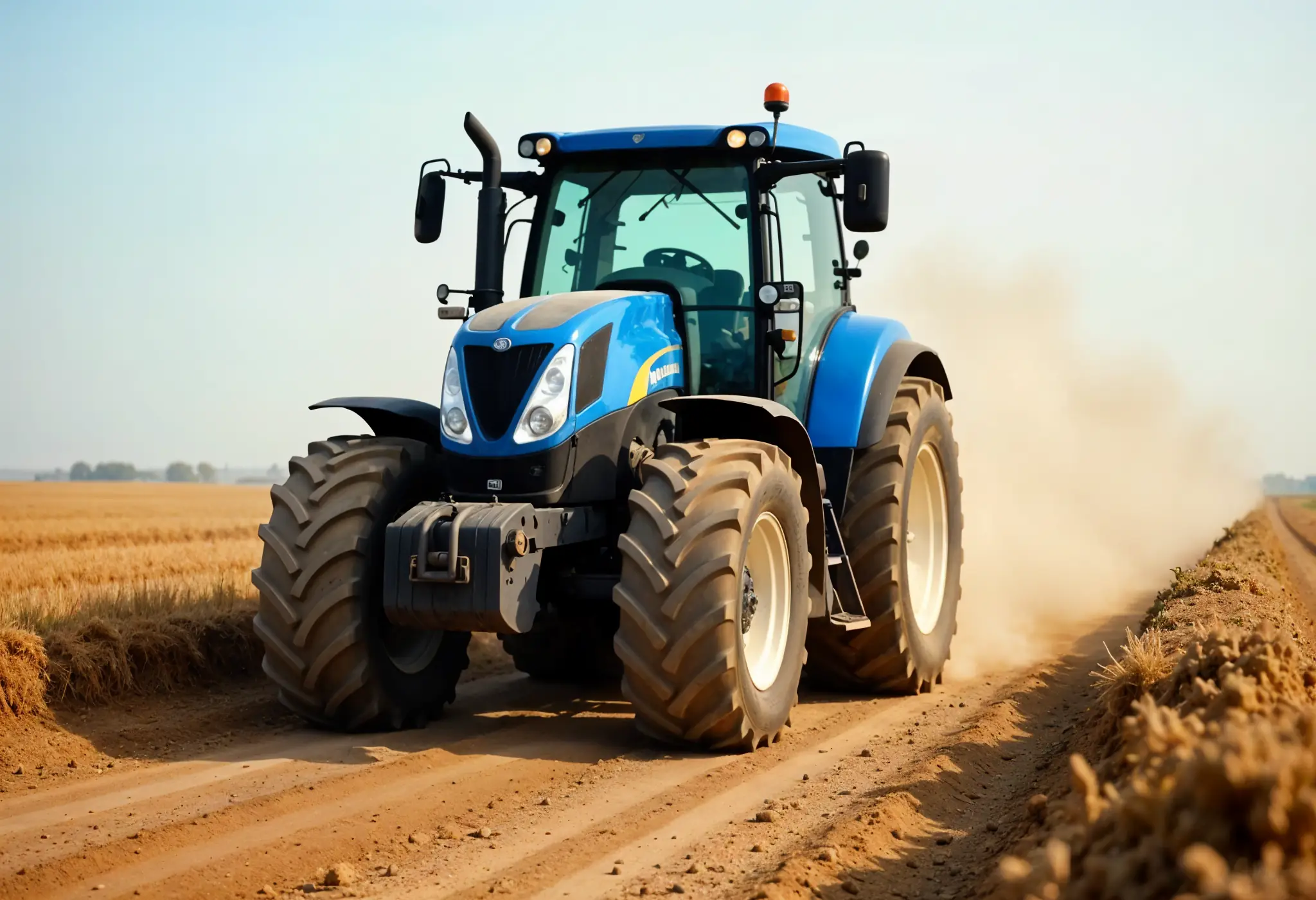
Hydraulic Hoses Role in Equipment
These flexible tubes deliver pressurized hydraulic fluid throughout your machinery, powering steering systems, brakes, and essential mechanical functions. They convert fluid energy into the mechanical force that drives your equipment forward. Even the most expensive tractor becomes useless when a single compromised hose fails. Unlike other components measured by hours of operation, these critical parts face degradation primarily from pressure cycles and environmental factors rather than simple runtime.
Common Failure Points in Hydraulic Hoses
Several vulnerabilities make hydraulic hoses among the most frequently replaced MRO spare parts on farm equipment:
- Abrasion damage develops when hoses rub against other components, wearing away protective layers until reinforcement becomes exposed
- Heat aging occurs in hoses near high-temperature areas, causing the material to harden and make crackling sounds when bent
- Environmental degradation from UV exposure, chemicals, and weather extremes rapidly accelerates deterioration
- Improper assembly with inadequately crimped fittings reveals itself quickly under operating pressure
- Age-related deterioration begins before you even install the hose—manufacturers recommend replacement after 4-5 years of regular use or maximum 10 years regardless of visible condition
Preventive Maintenance Tips for Hydraulic Hoses
Proactive maintenance significantly extends hose life while preventing catastrophic failures:
Establish regular inspection intervals—every three months or 400-600 hours for mobile equipment. Check routinely for leaks by wiping hoses clean and using cardboard to detect wet spots that indicate fluid escape. Ensure proper routing to prevent rubbing against other components, as even a slight 5° twist can reduce hose life by 70%.
Maintain comprehensive records of installation dates and replacement history. Never attempt to check for leaks using your hands—hydraulic fluid under pressure (between 1,000-3,000 psi) can penetrate skin and cause serious injury.
Fuel Injectors
Precision fuel injectors serve as the heart of your diesel engine's power system. Their failure can transform your productive equipment into idle machinery within seconds. Unlike older mechanical systems, today's high-pressure common-rail technology operates under brutal conditions, making these critical components particularly vulnerable when maintenance falls short.
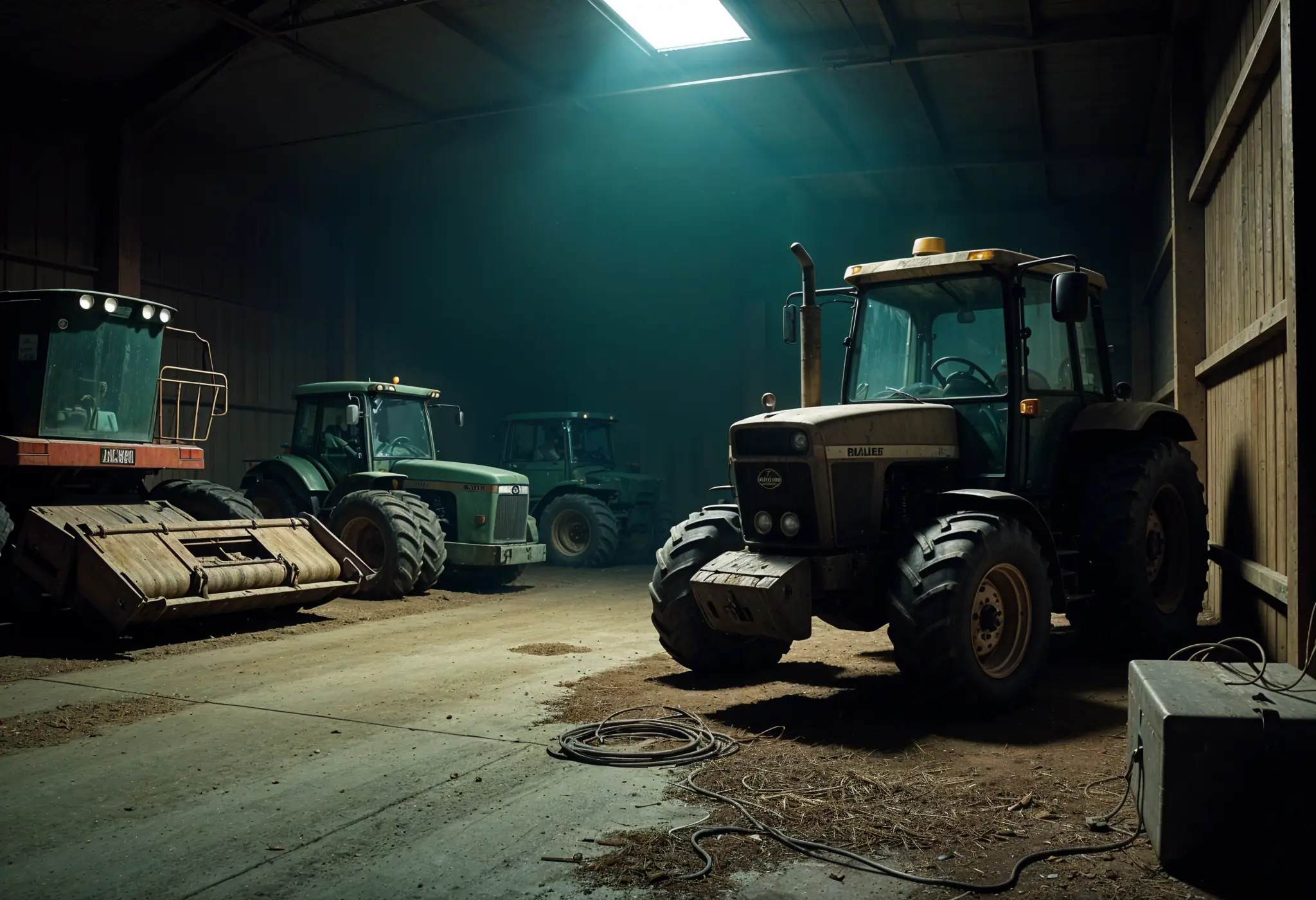
Fuel Injector Importance
Fuel injectors control the exact amount and timing of fuel delivery to your engine's combustion chambers. These sophisticated components atomize liquid fuel into microscopic particles essential for efficient burning and optimal power generation. Modern farm equipment injectors function under extreme pressures—commonly exceeding 30,000 psi—while enduring temperature peaks above 2,550°F. They represent a substantial portion of your engine's overall cost, with manufacturers confirming that the majority of diesel engine expense lives in the fuel system.
The precision engineering of these parts directly affects:
- Engine power output and torque
- Fuel efficiency and consumption rates
- Emissions control and environmental compliance
- Cold-weather starting reliability, especially in diesel applications
Signs of Failing Fuel Injectors
Your equipment will tell you when injectors need attention—if you know what to watch for:
Dirty fuel injectors cause inefficient combustion and noticeable power loss. Black exhaust smoke typically indicates over-fueling and possible injector cleaning needs. When your equipment misfires, idles roughly, loses power, consumes more fuel, or starts with difficulty, suspect injector problems.
Modern Tier 4 engines with high-pressure systems face unique challenges. Extreme operating temperatures (400-500°F) cause fuel breakdown and carbon deposits (coking) within injectors. These components operate with tolerances as tight as 1-3 microns—far smaller than a human red blood cell at 8 microns—which means even minimal deposits significantly reduce performance.
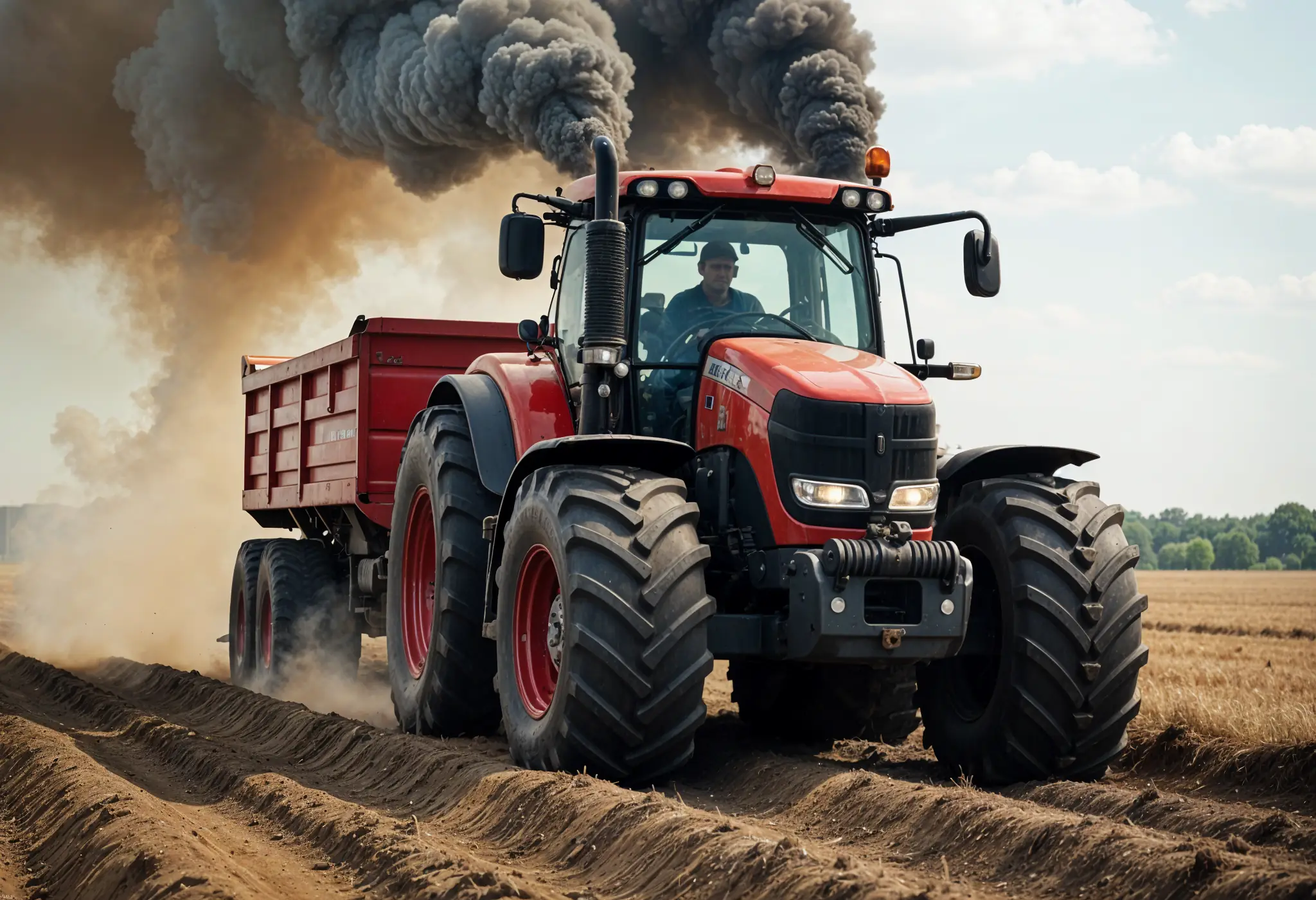
Fuel Injector Replacement Best Practices
Replacement costs range from $300 to $1,500 depending on equipment type and parts quality, yet proactive maintenance proves far more economical than emergency repairs during harvest or planting. Proper spare parts management and inventory optimization can help mitigate these costs and reduce lead times for critical components.
For mechanical injectors, professional service includes:
- Removing injectors for bench testing
- Documenting nozzle opening pressure and leakage rates
- Ultrasonic cleaning to remove deposits
- Replacing worn components
- Reassembling and testing spray patterns
Electronic injectors in newer equipment typically require complete replacement rather than servicing. Quality fuel additives with detergent components help prevent internal diesel injector deposits (IDID), improving fuel economy by up to 5% and power by 4.5%.
Battery Cables
Battery cables function as the primary power conduits for your farm equipment. These heavy-duty components might seem simple, but they serve as critical links between power sources and essential systems. When cables fail, even the strongest batteries become useless—leaving your equipment dead during crucial operational windows.
Battery Cables and Electrical Flow
Battery cables transfer energy from batteries to starters, alternators, and other vital electrical components. The integrity of these connections directly affects your equipment's starting capability and overall performance. Many farmers overlook these basic components until equipment suddenly refuses to start—often during critical harvest periods when every minute counts.
Hidden electrical problems frequently stem from compromised cables rather than the batteries themselves. A seemingly minor connection issue can completely disable tractors and harvesters worth hundreds of thousands of dollars. When battery cables deteriorate, electrical resistance increases, preventing sufficient current from reaching starting systems.
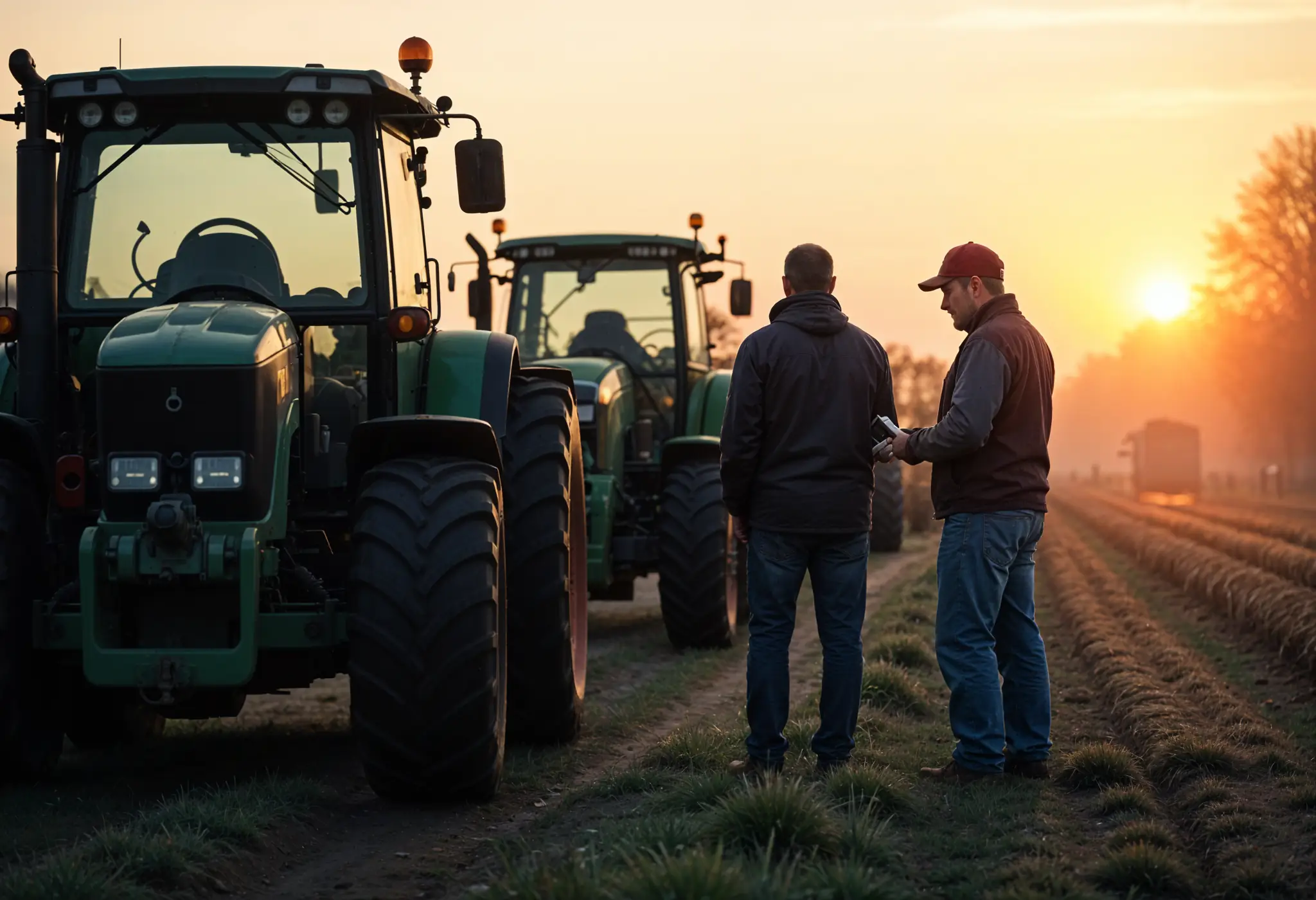
Why Battery Cables Fail
Four primary factors contribute to battery cable failures:
- Corrosion buildup: White powdery substances form between cable ends and battery terminals, creating resistance that blocks electrical flow
- Heat generation: Loose connections produce excessive heat that gradually melts components and damages terminal connections
- Internal wire degradation: Corrosion eventually penetrates protective coverings and attacks the copper or alloy wire inside
- Mechanical wear: Daily equipment vibration loosens terminals and causes cables to rub against other components
Even a thin, uniform black layer between battery posts and cable ends dramatically reduces electrical conductivity. This explains why many farmers unnecessarily replace batteries when the actual problem lies in the cabling system.
How to Inspect and Replace Battery Cables
Regular inspection prevents unexpected equipment failure during critical operational periods:
- Check for visible corrosion, fraying, or damaged insulation on cable surfaces
- Prepare a solution of 2-3 tablespoons baking soda per quart of water for cleaning
- Apply this mixture to corroded areas using a wire brush
- Clean both battery posts and cable ends until only shiny metal remains
For replacement, brass terminals (gold-colored) outperform lead alloy (silver-colored) alternatives. "OO" gauge welding cable offers superior flexibility compared to standard battery cables when constructing replacements.
When servicing batteries, always disconnect the negative cable first when removing and install it last when reconnecting to prevent dangerous shorts. After installation, apply general purpose grease or silicone spray to terminals—this simple step prevents future corrosion issues.
One missing part can stop your entire operation. Secure your inventory today with trusted, farm-grade components from MCHPartsNYC.com. Fast turnaround. No guesswork. Maximum uptime.
Fuses and Relays
Fuses and relays function as silent guardians in your farm equipment's electrical systems. These small components often make the difference between a minor inconvenience and catastrophic equipment failure. When electrical problems strike, having the right fuses and relays in your inventory can save thousands in repair costs and prevent crucial operational delays.
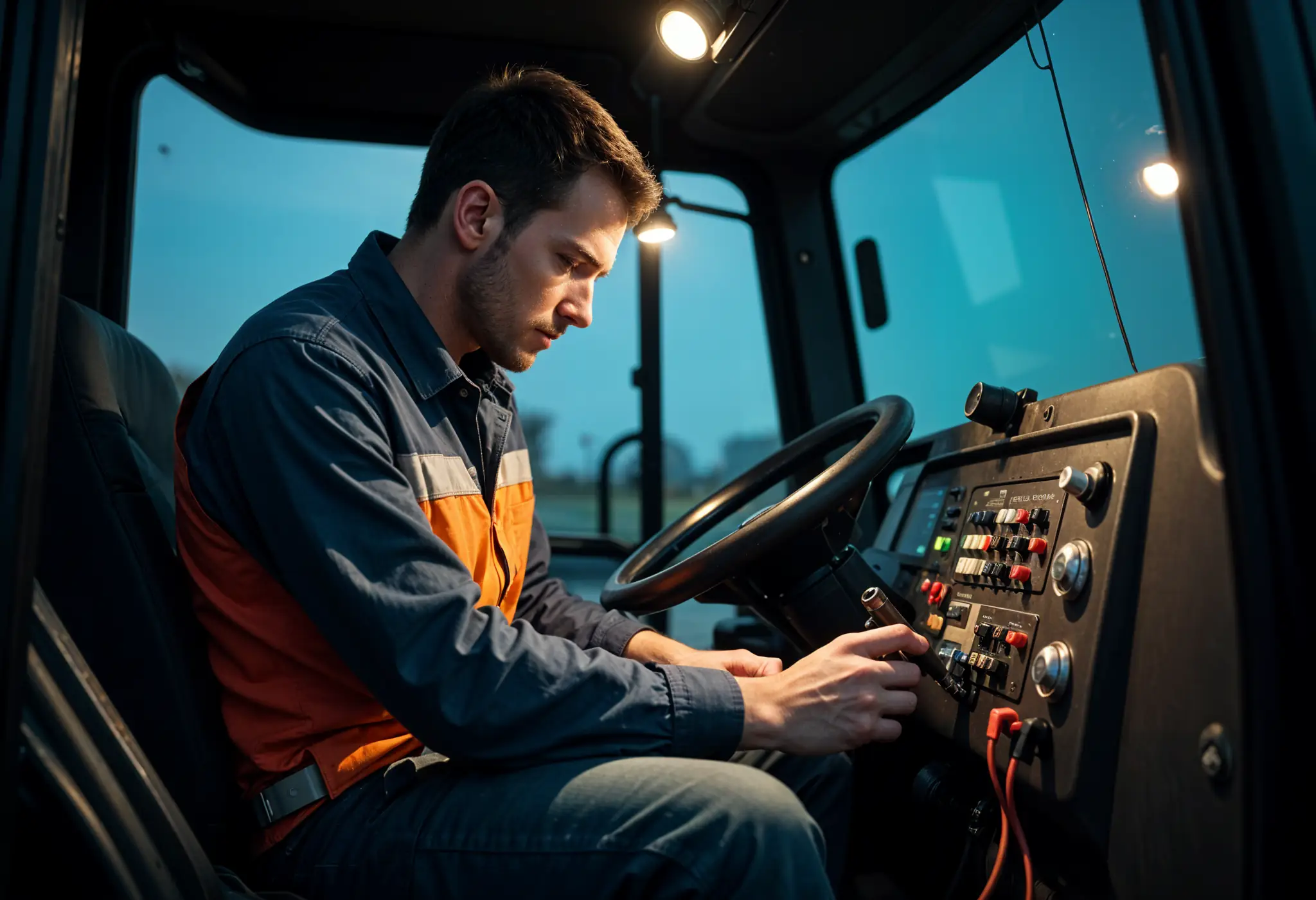
Fuses and Relays in Farm Equipment
Fuses serve as sacrificial protection devices within your machinery's electrical circuits. They feature specific amperage ratings—typically ranging from 5A to 30A with color coding (red, blue, yellow, green) that ensures proper identification and replacement. Relays operate as electrically-controlled switches, managing high-current circuits through low-current signals to protect sensitive components.
These critical parts protect essential farm systems including:
- Water pumps and irrigation controls
- PTO mechanisms and hydraulic systems
- Lighting systems and operator controls
- Engine management and starting systems
Overlooked Risks of Fuse Failure
The consequences of improper fuse management extend far beyond minor inconvenience. Using incorrect replacement fuses can severely damage your equipment's electrical system. A higher-rated fuse fails to provide adequate protection during current surges, potentially causing electrical fires or permanent equipment damage.
Some operators resort to dangerous shortcuts—replacing blown fuses with coins, foil, or higher-rated alternatives. This practice creates significant fire hazards. Without proper fuses, your equipment can malfunction, short circuit, or catch fire. Slow-blow fuses provide essential protection for motor startup surges but offer limited personal protection against electrical shocks.
Spare Parts Management for Fuses
Effective fuse inventory requires methodical planning:
Document all fuse locations and specifications for each piece of equipment. John Deere tractors typically house fuses in specific locations such as the hood cowl, load center, or near the battery. Maintain an organized stock of correctly-rated replacements, never substituting with different amperage ratings.
Establish regular electrical system inspection routines. Check for loose connections, corrosion, or heat damage around fuse boxes. For older equipment, consider installing additional fuse boxes to properly protect aftermarket accessories.
Implementing a computerized maintenance management system (CMMS) can greatly improve your spare parts management process, allowing for better tracking of fuse inventory and scheduled replacements. This proactive approach to maintenance spare parts inventory management can significantly reduce downtime and improve operational efficiency.
Don’t let supply chain delays stall your season. Partner with MCH Parts for reliable sourcing, expert support, and complete spare parts coverage. Start now at MCHPartsNYC.com.
Conclusion
Farm equipment failure doesn’t wait for convenience—it hits during planting, harvest, and other critical windows when downtime is most costly. Neglecting spare parts like air filters, hydraulic hoses, fuel injectors, battery cables, fuses, and relays leads to lost time, damaged machinery, and higher fuel and repair costs. With rising equipment prices and supply chain delays, efficient spare parts management is no longer optional. Digital tracking and CMMS tools, combined with a well-maintained inventory of critical spares, can dramatically improve uptime and reduce unexpected failures across your operation.
Visit MCHPartsNYC.com today for expert support in sourcing farm equipment spare parts. Get a free consultation and custom quote to protect your farm from preventable breakdowns.
We’ve covered the first 7 overlooked spare parts that can shut down your farm in an instant—but we’re not done yet. In Part 2, we dive into the remaining 6 silent saboteurs hiding inside your machines. From glow plugs that leave you stranded in the cold to worn belts that snap under pressure, these parts often fail without warning—and always at the worst time. Want to stay one step ahead of costly downtime? Don’t miss what’s coming next.
Read More
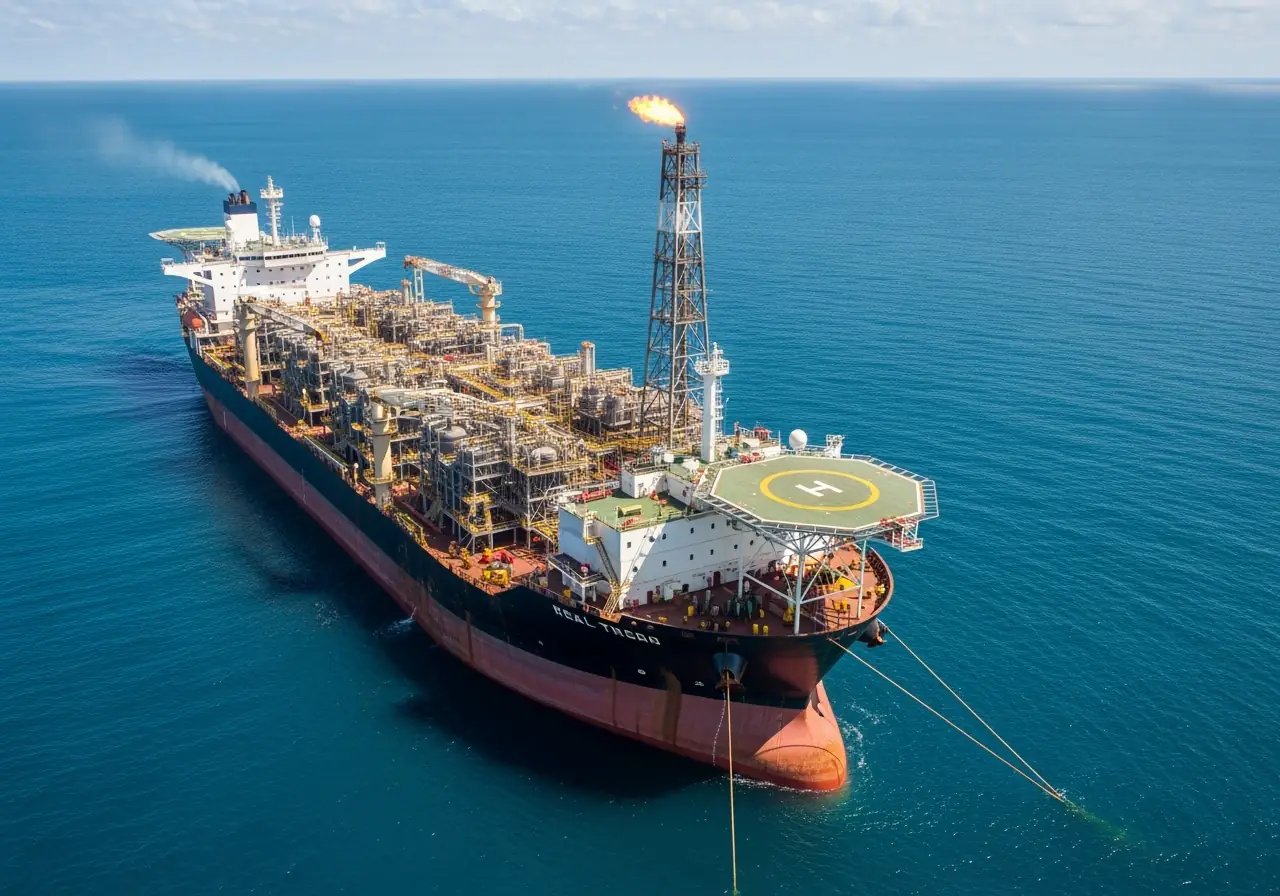
How FPSO Inspection Prevents Million-Dollar Shutdown Losses
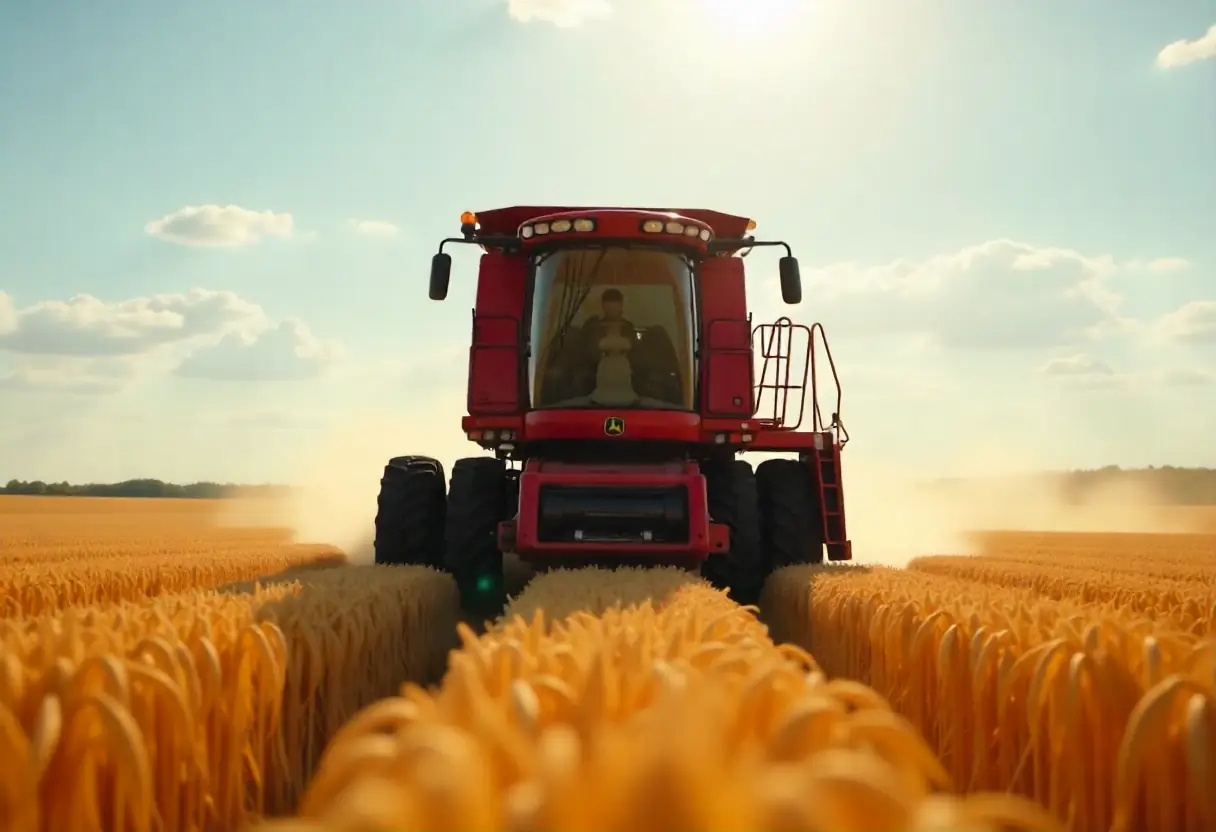
Fix It Before It Breaks: A Farmer's Guide to Combine and Harvester Maintenance
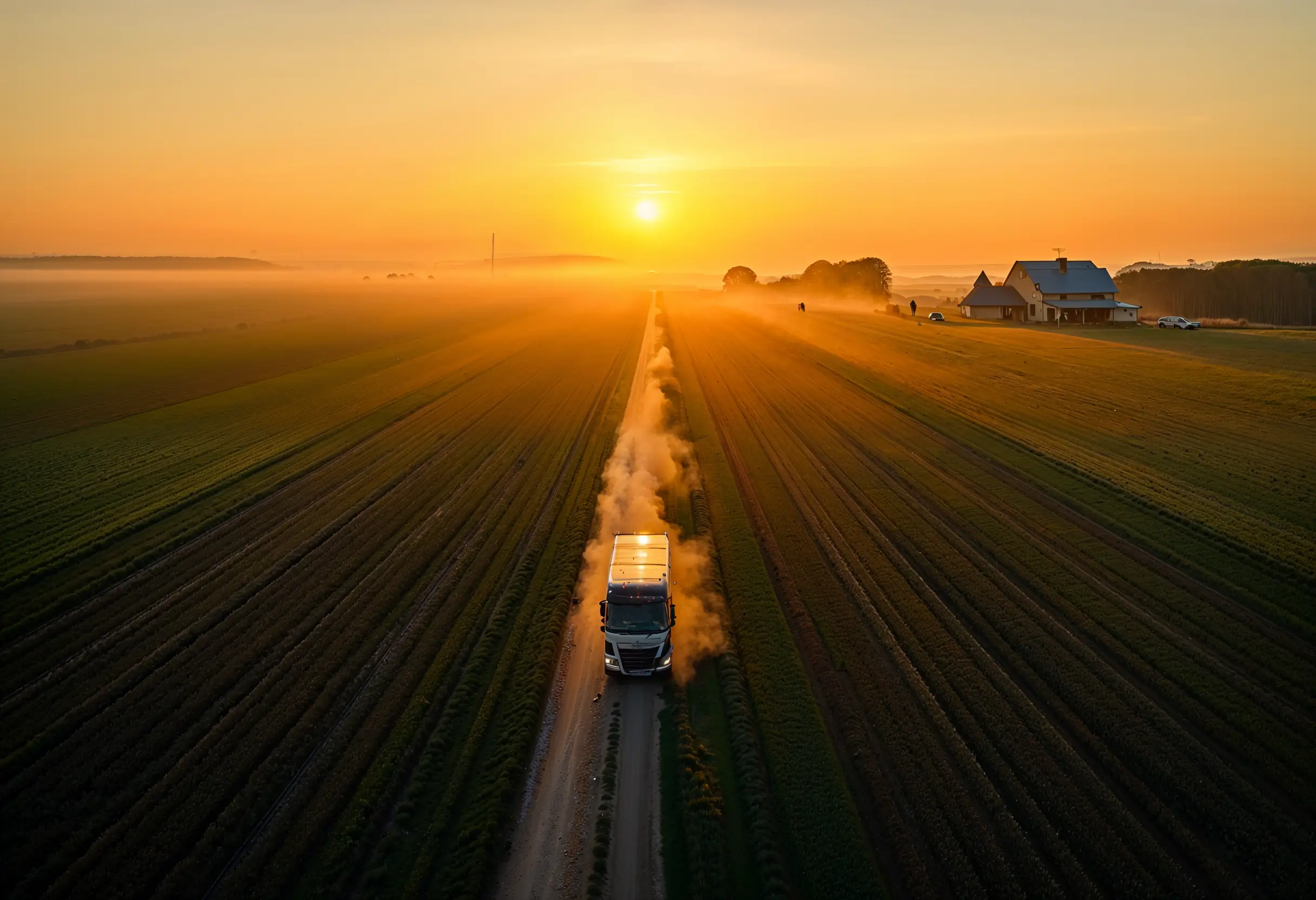
Why Fast Tractor Parts Delivery is Changing Modern Farming [2025 Guide]
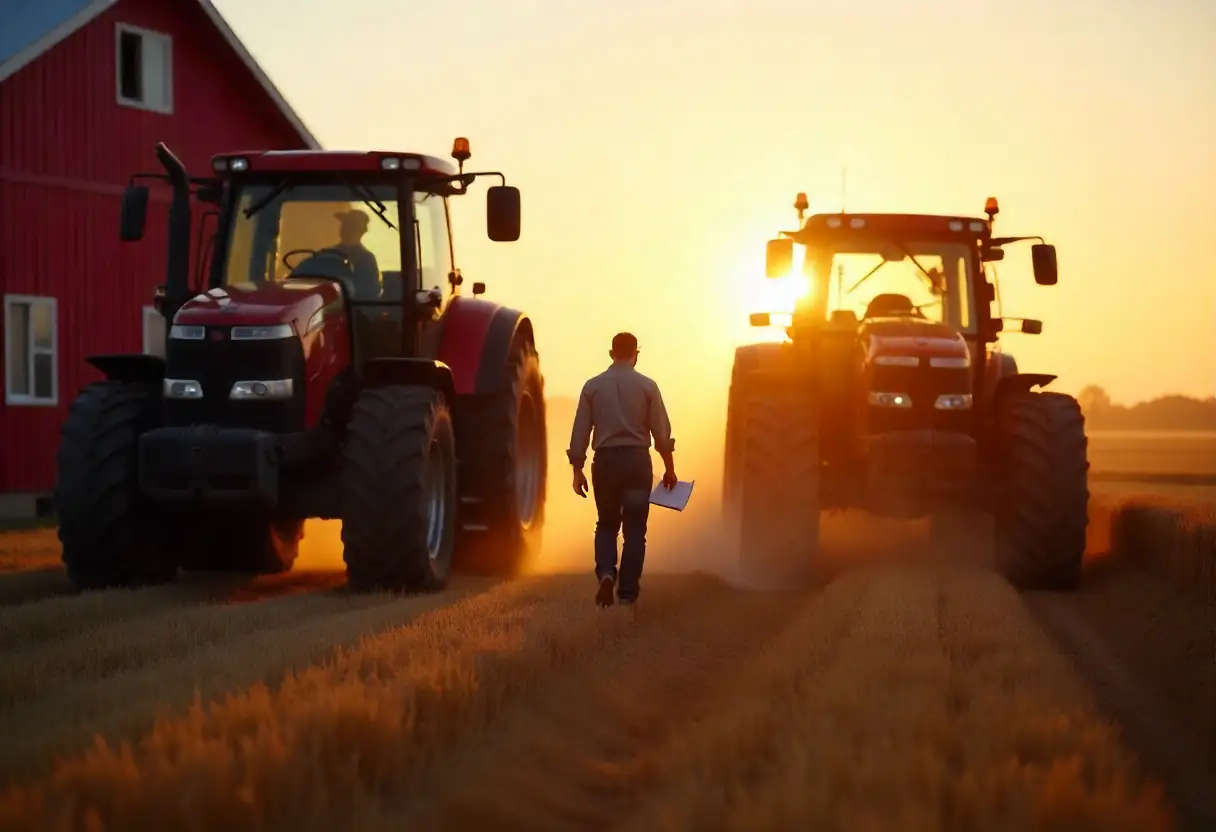
The Critical Farm Equipment Replacement Parts You Need Before Harvest 2025
.webp)
How to Double Your Farm Efficiency: Expert Guide to Smart Scaling
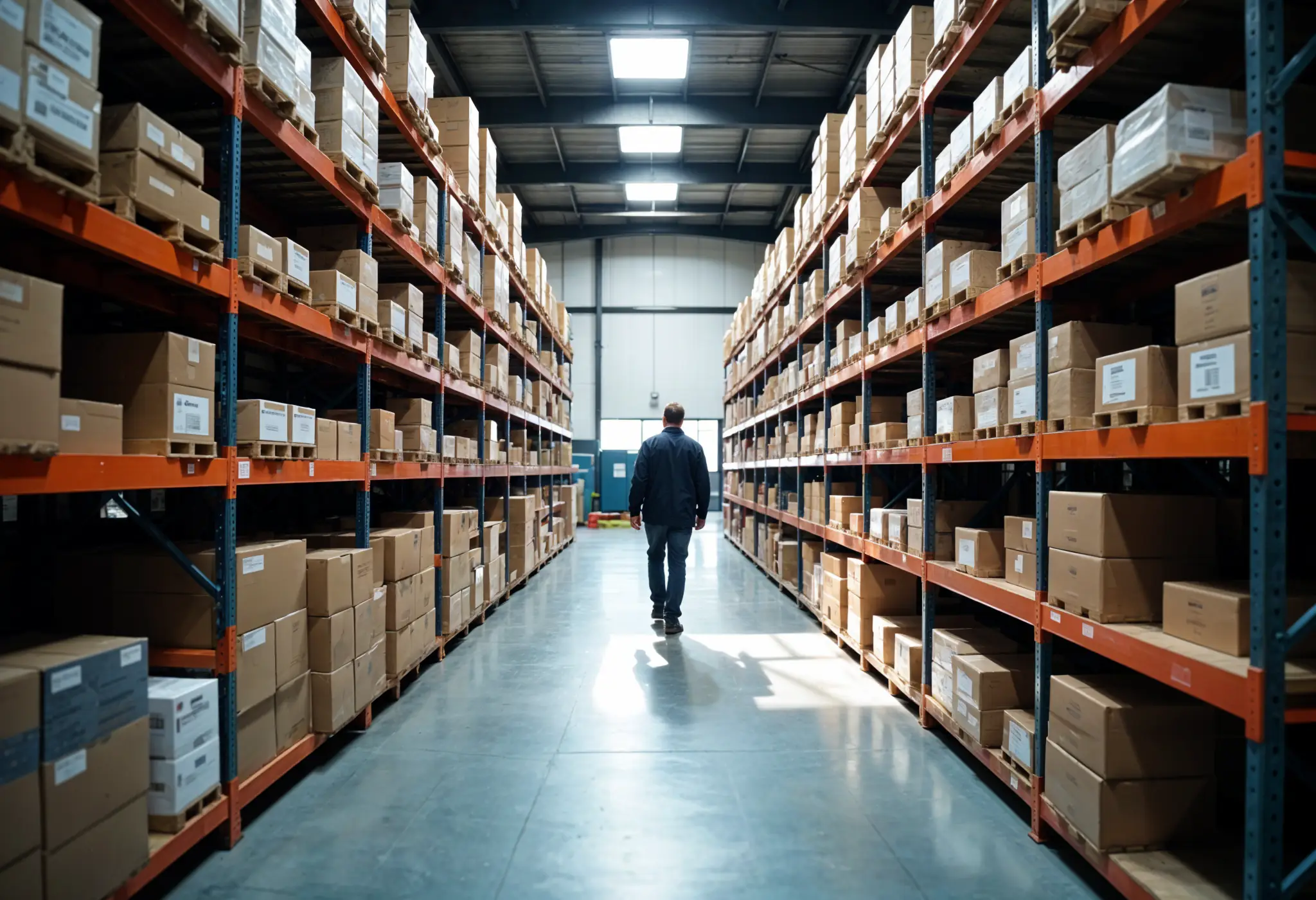
Cut Costs by 30%: Pre-Season Spare Parts Audit Checklist

Proven Success Factors for Agricultural Equipment Manufacturers in 2025
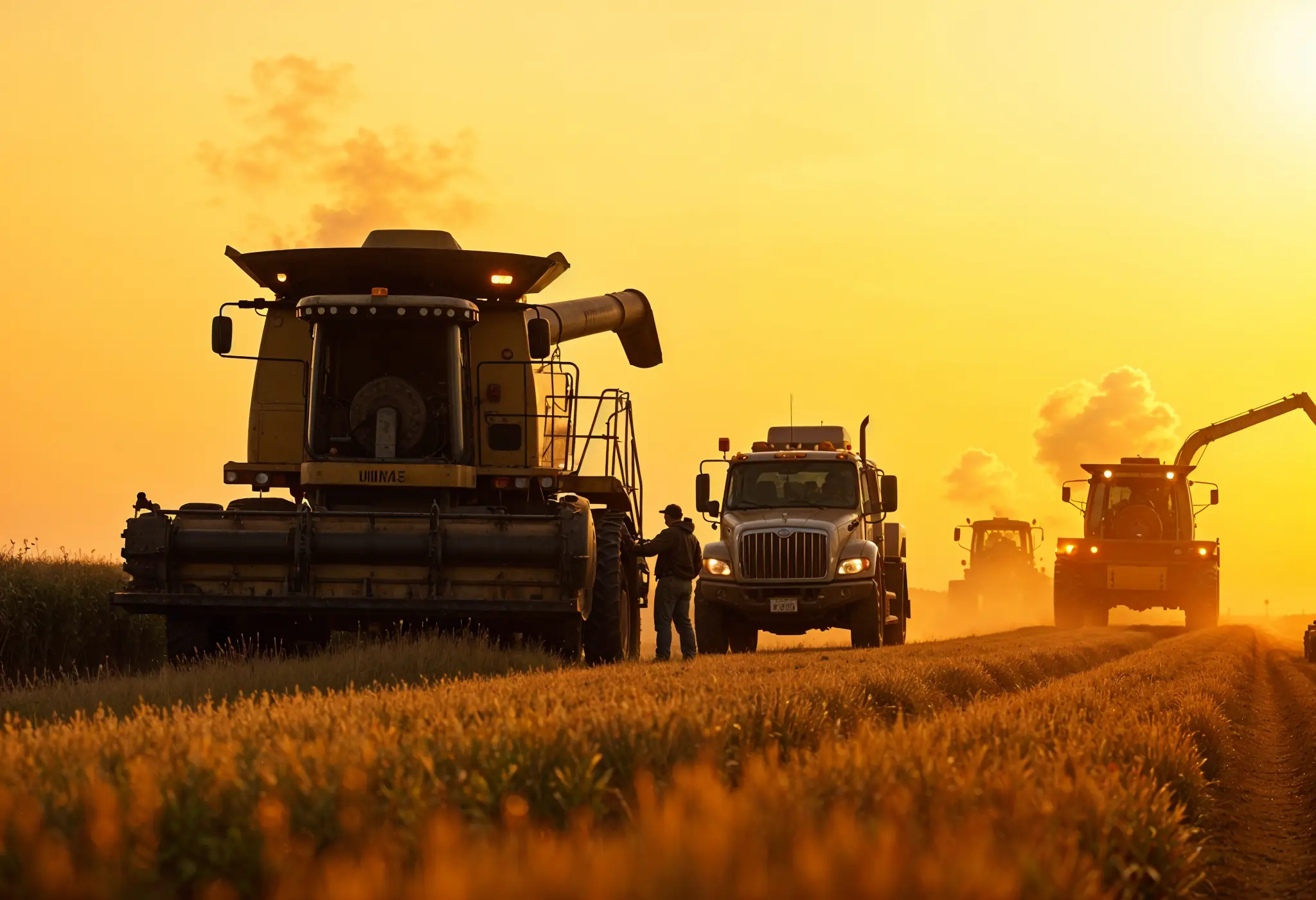
13 Overlooked Farm Spare Parts That Halt Operations — Pt. 2
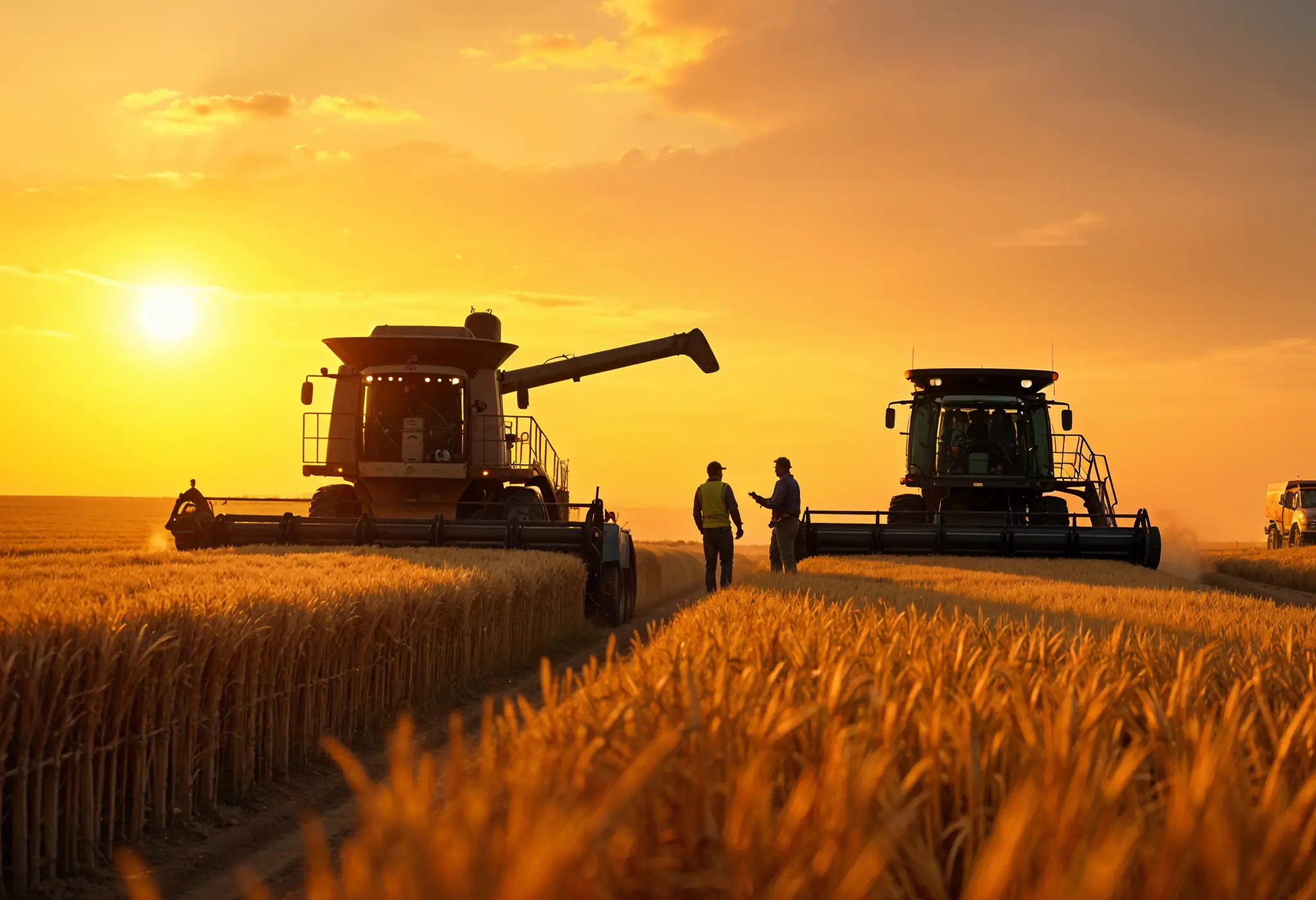
13 Overlooked Farm Spare Parts That Halt Operations — Pt. 1
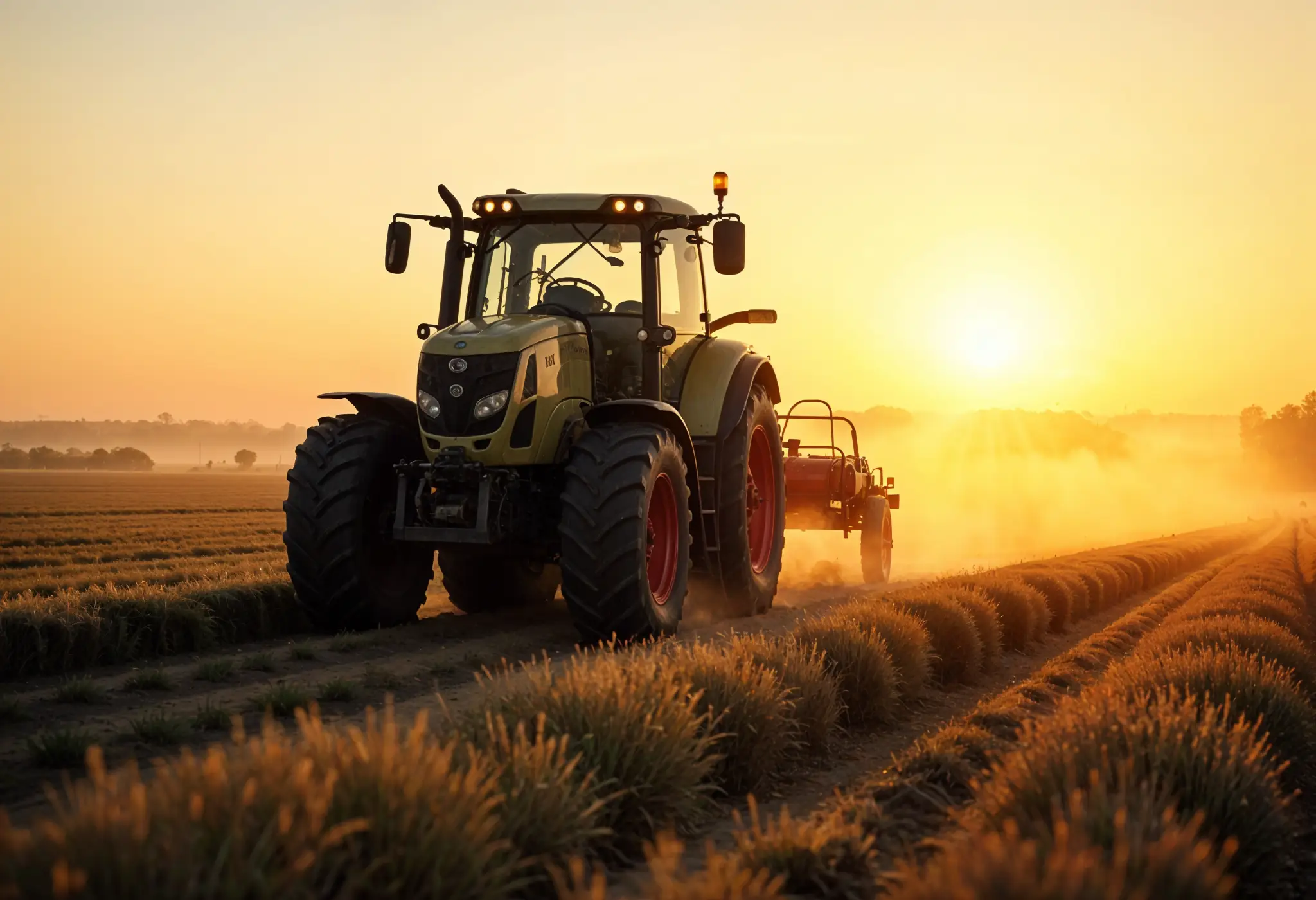
Top Hydraulic Components for Agricultural Equipment in 2025: Complete Guide
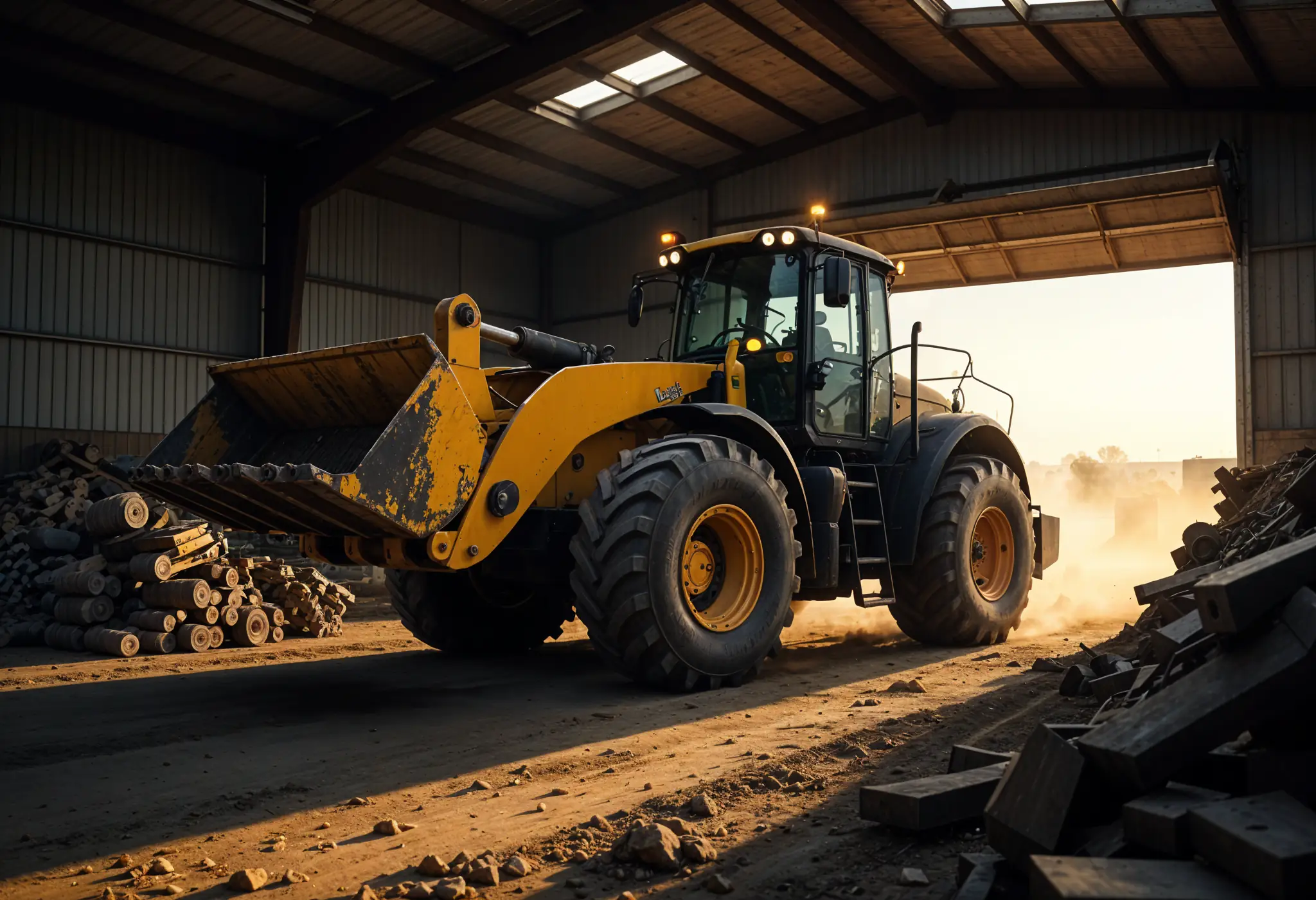
The Essential Farm Equipment Parts You Can't Afford to Run Out Of
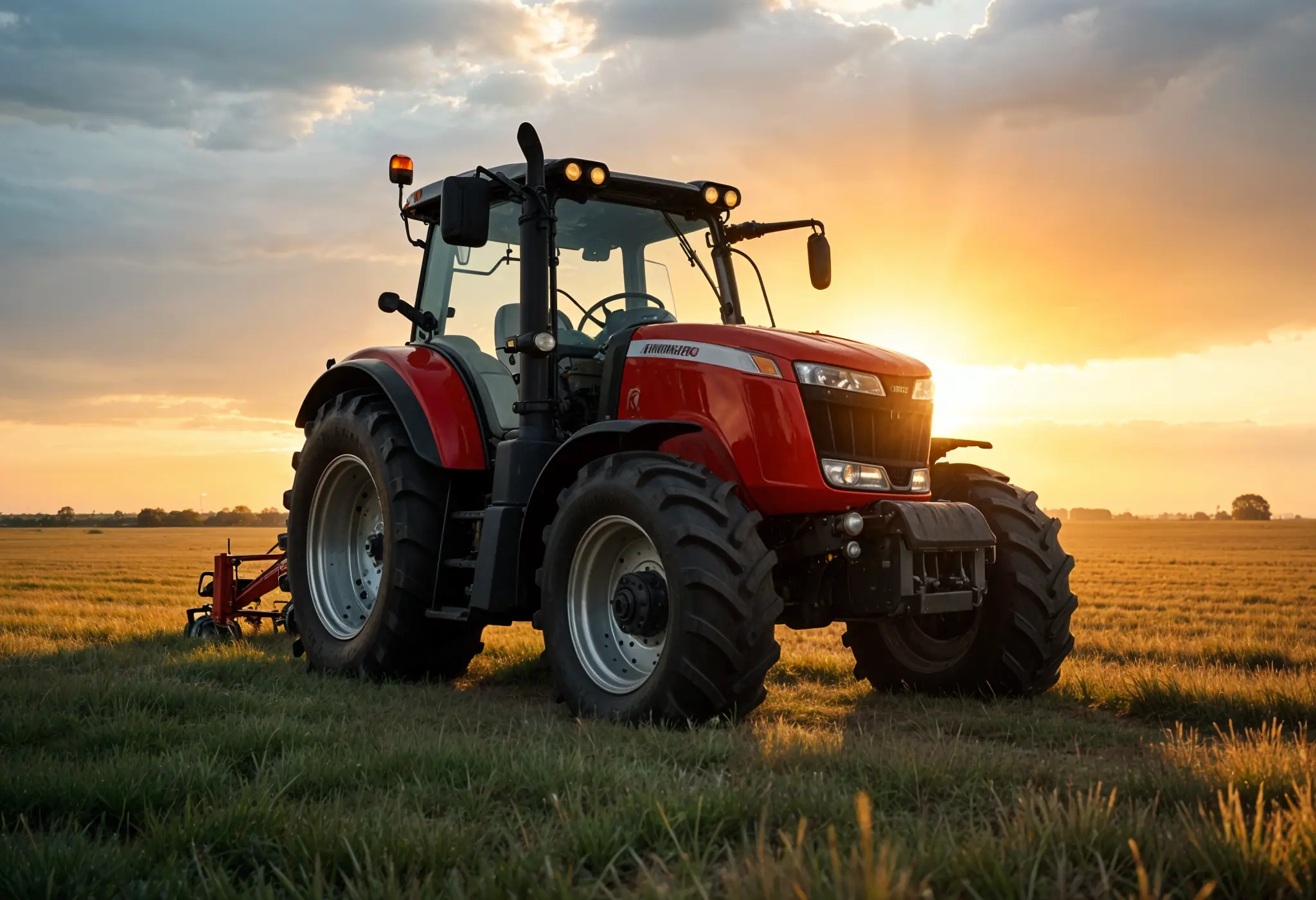
How to Service Farm Equipment: A Farmer's Guide to Zero Harvest Downtime
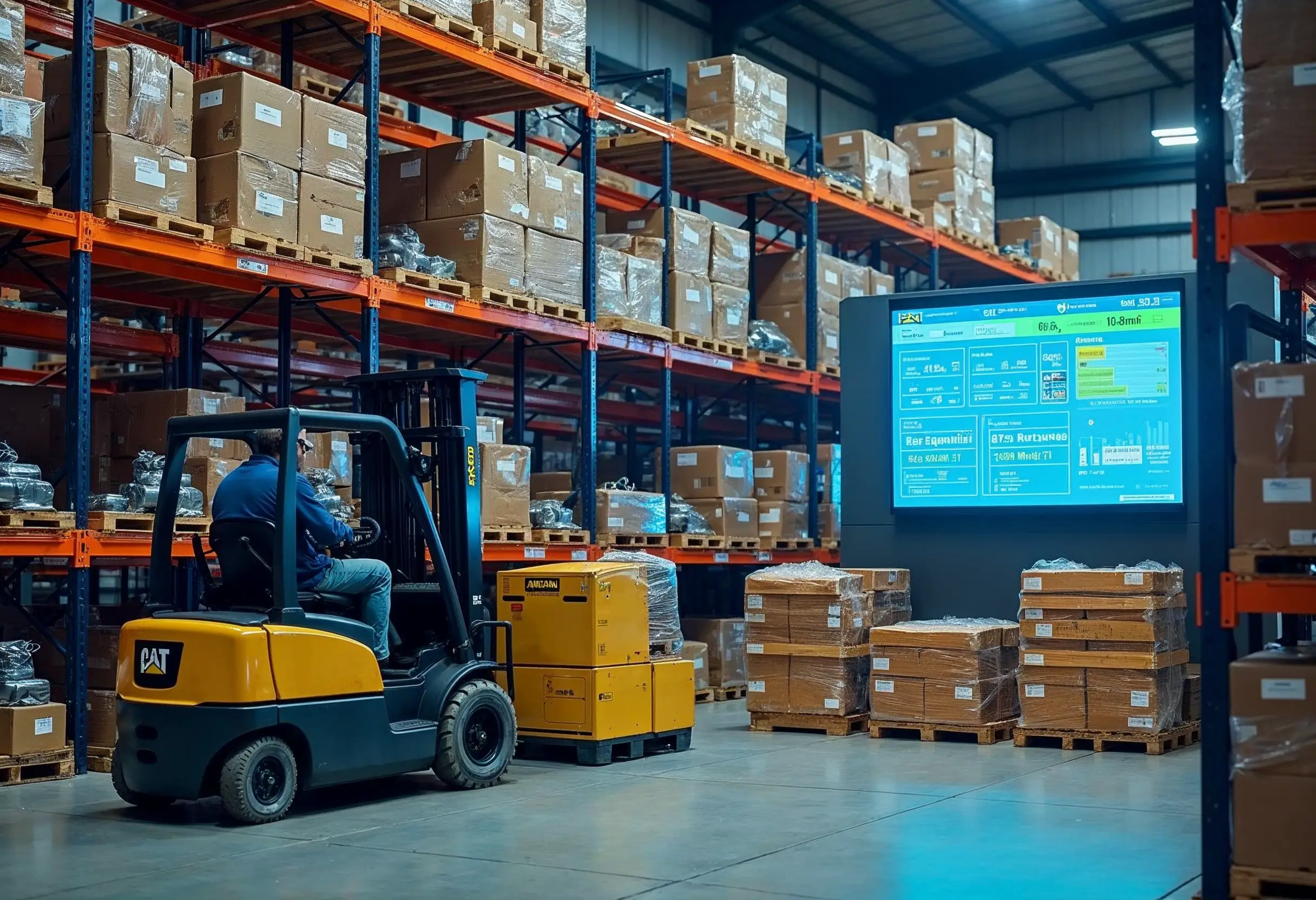
Construction Machinery Parts Suppliers: Expert Selection Guide
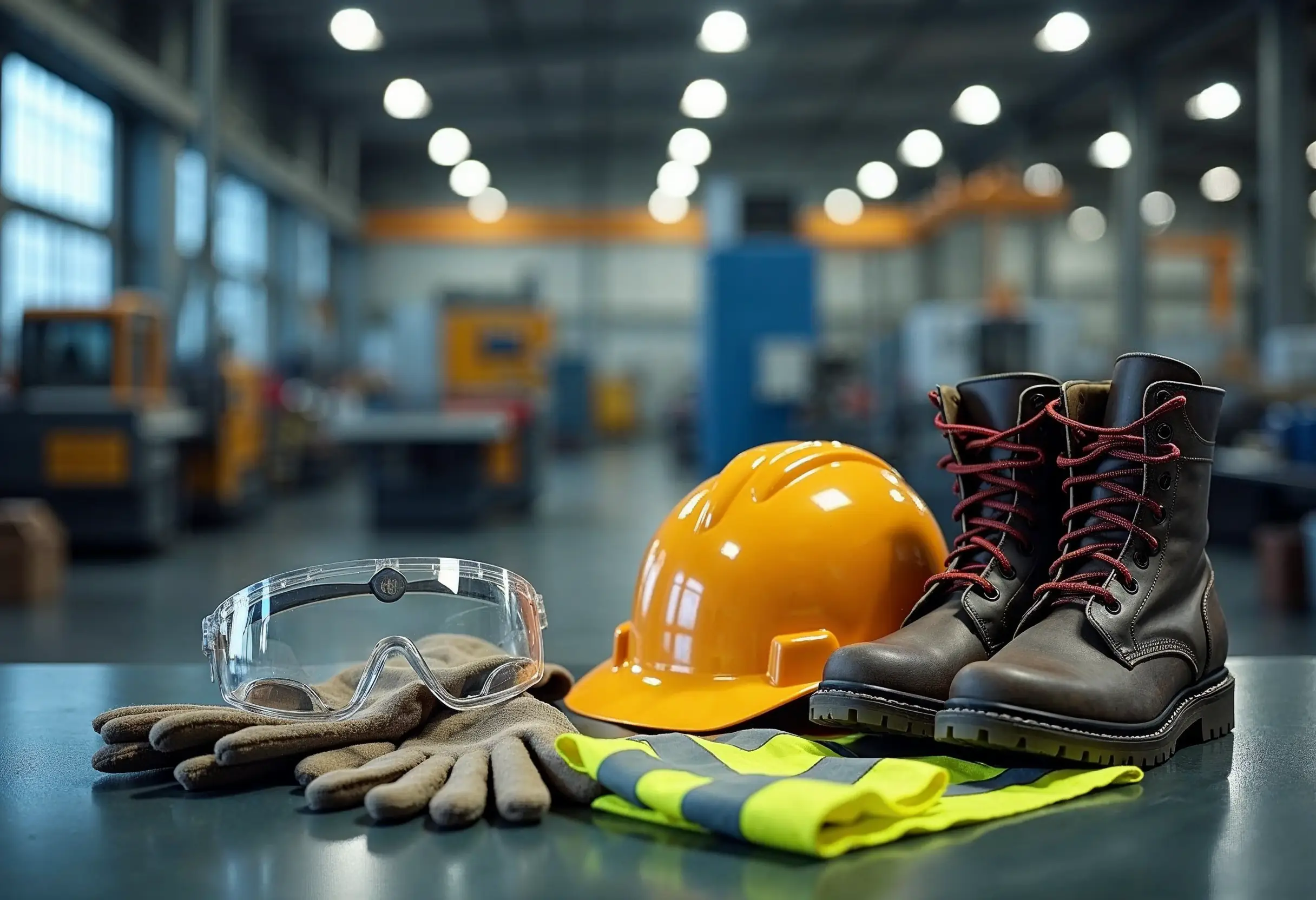
How to Apply Machine Safety Rules: From Selection to Installation
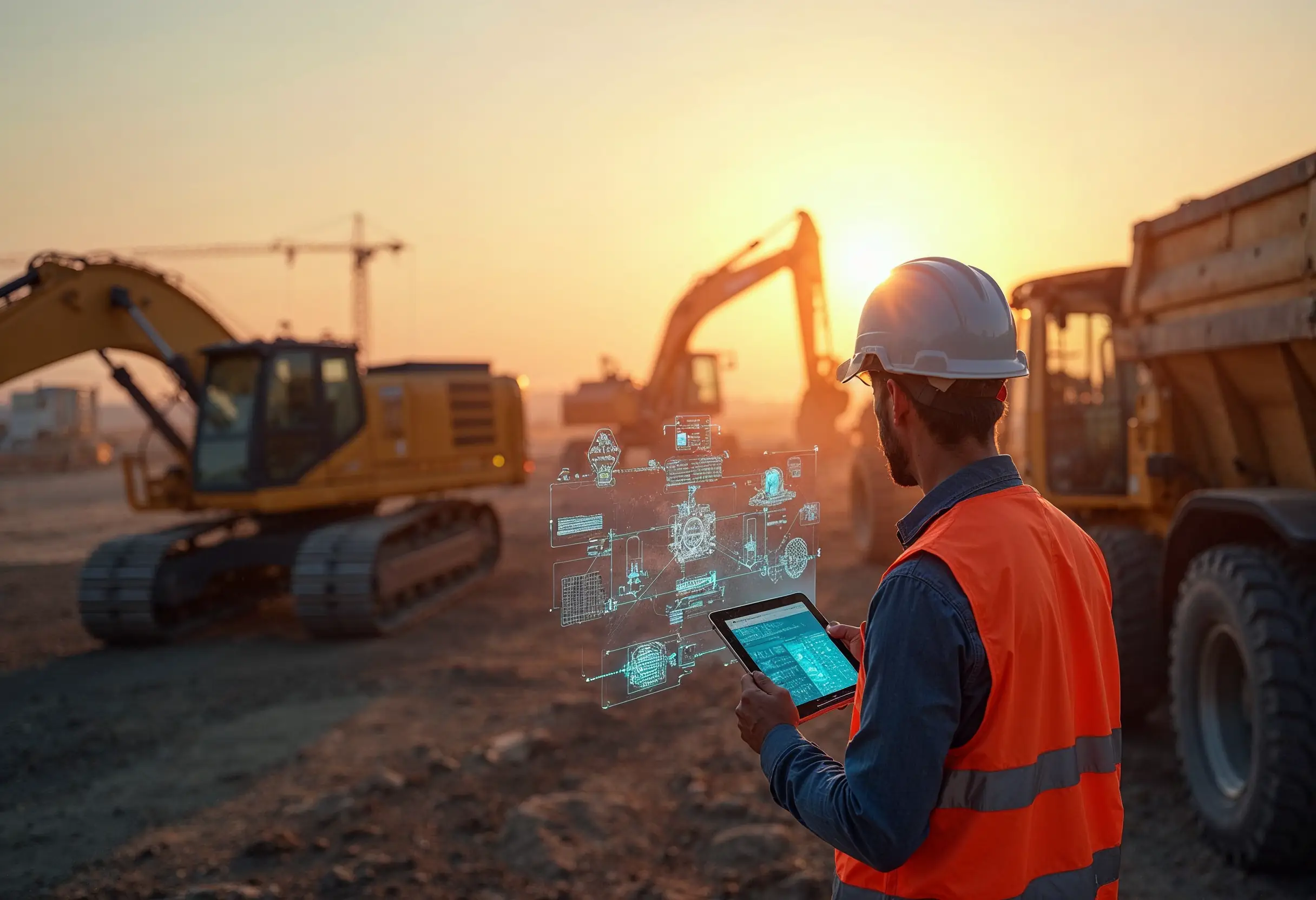
Smart Diagnostics Cut Heavy Equipment Failures by 73%
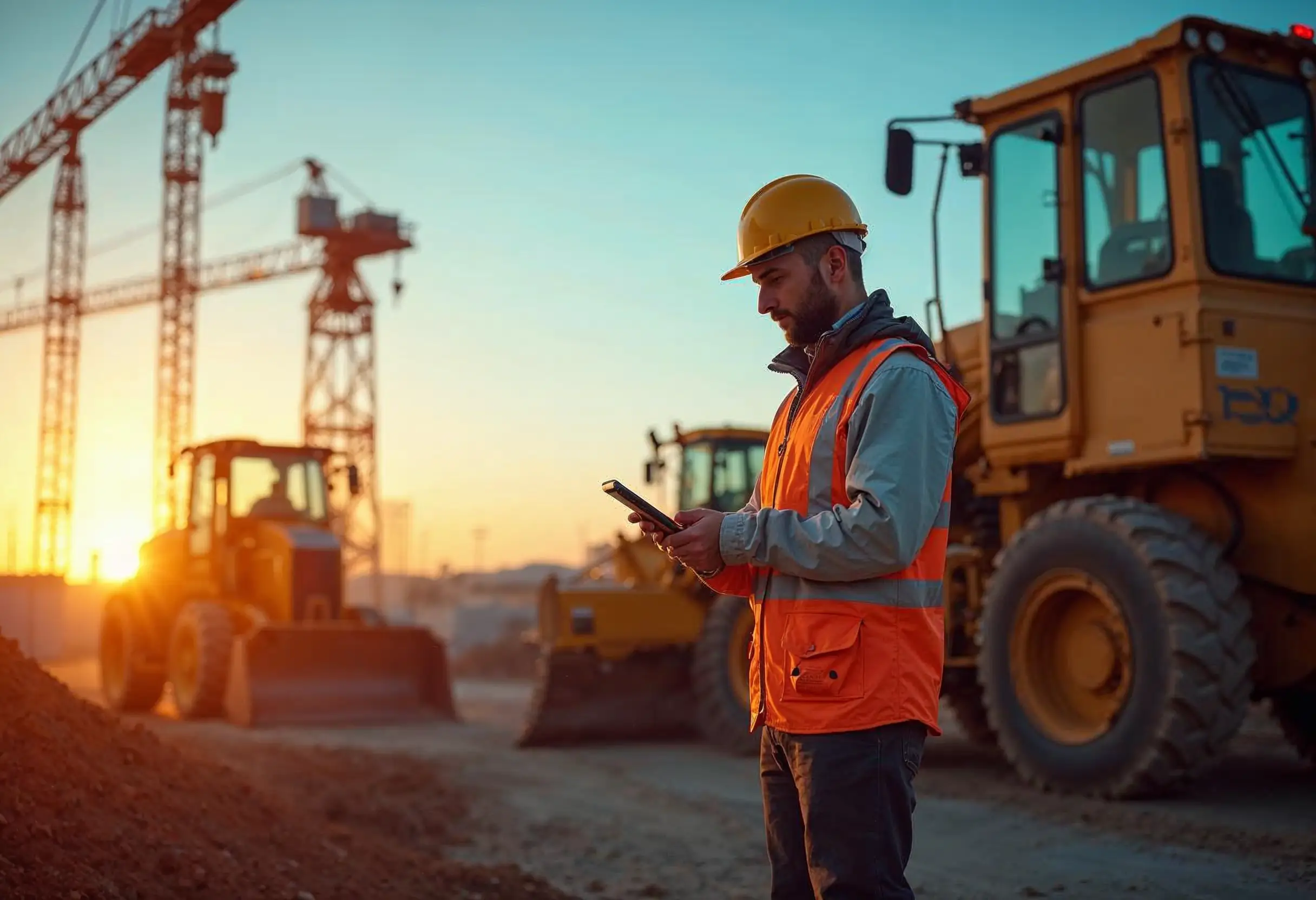
5 Ways to Assess the Environmental Impact of Heavy Construction Machinery
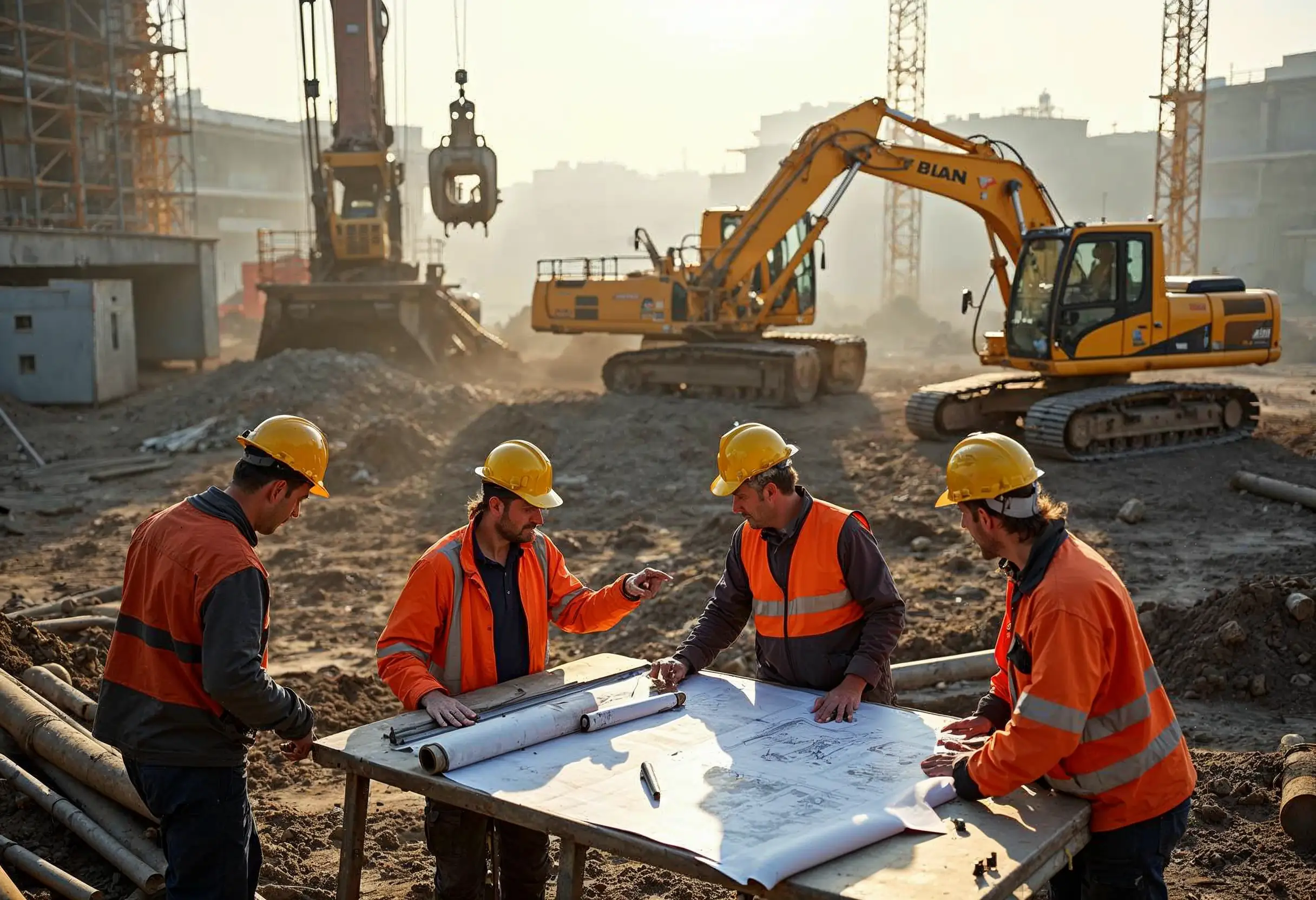
10 Smart Ways to Pick Construction Machinery for 2025 Projects
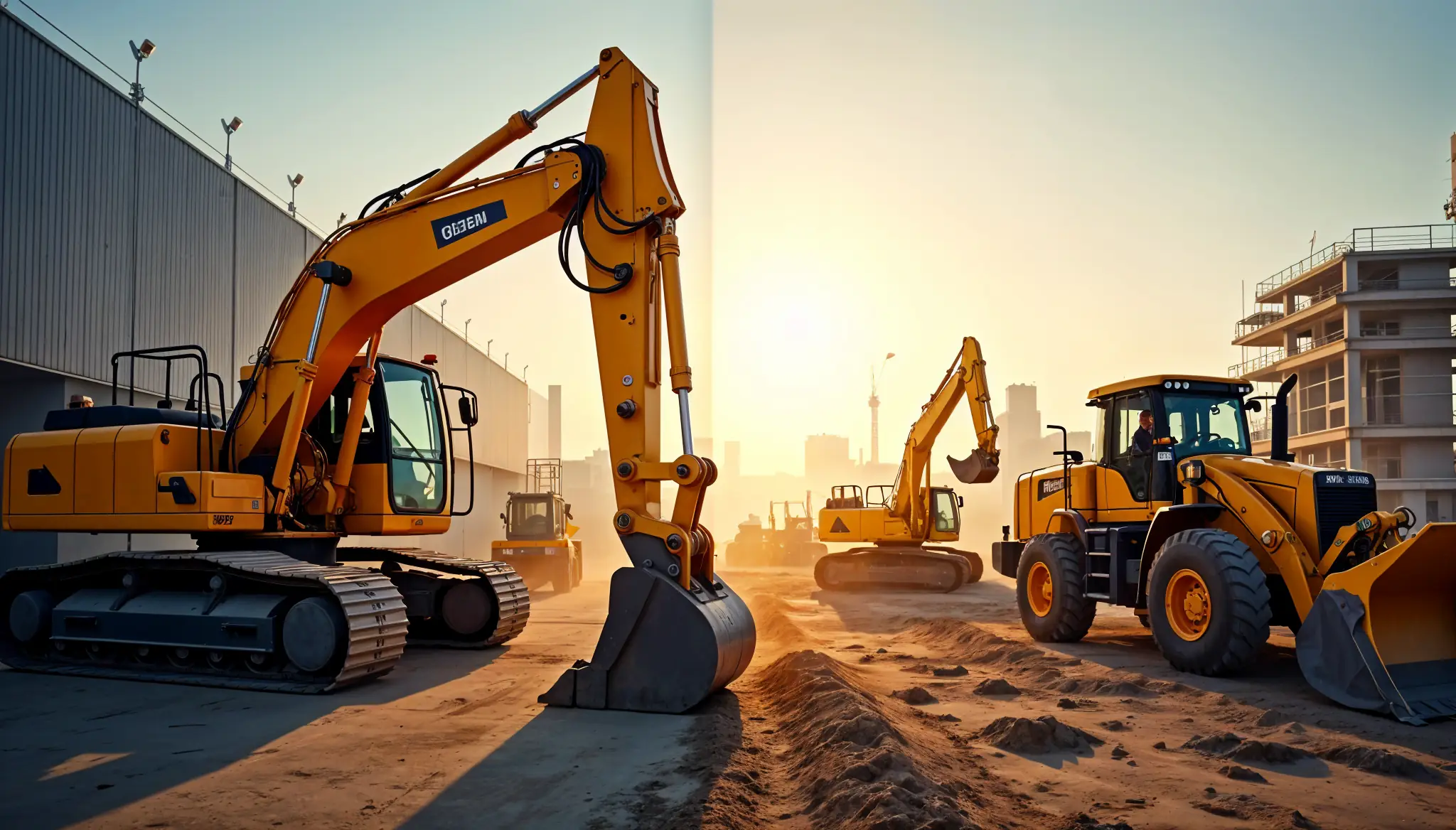
Rent vs Purchase Equipment: What Heavy Industry Experts Hide
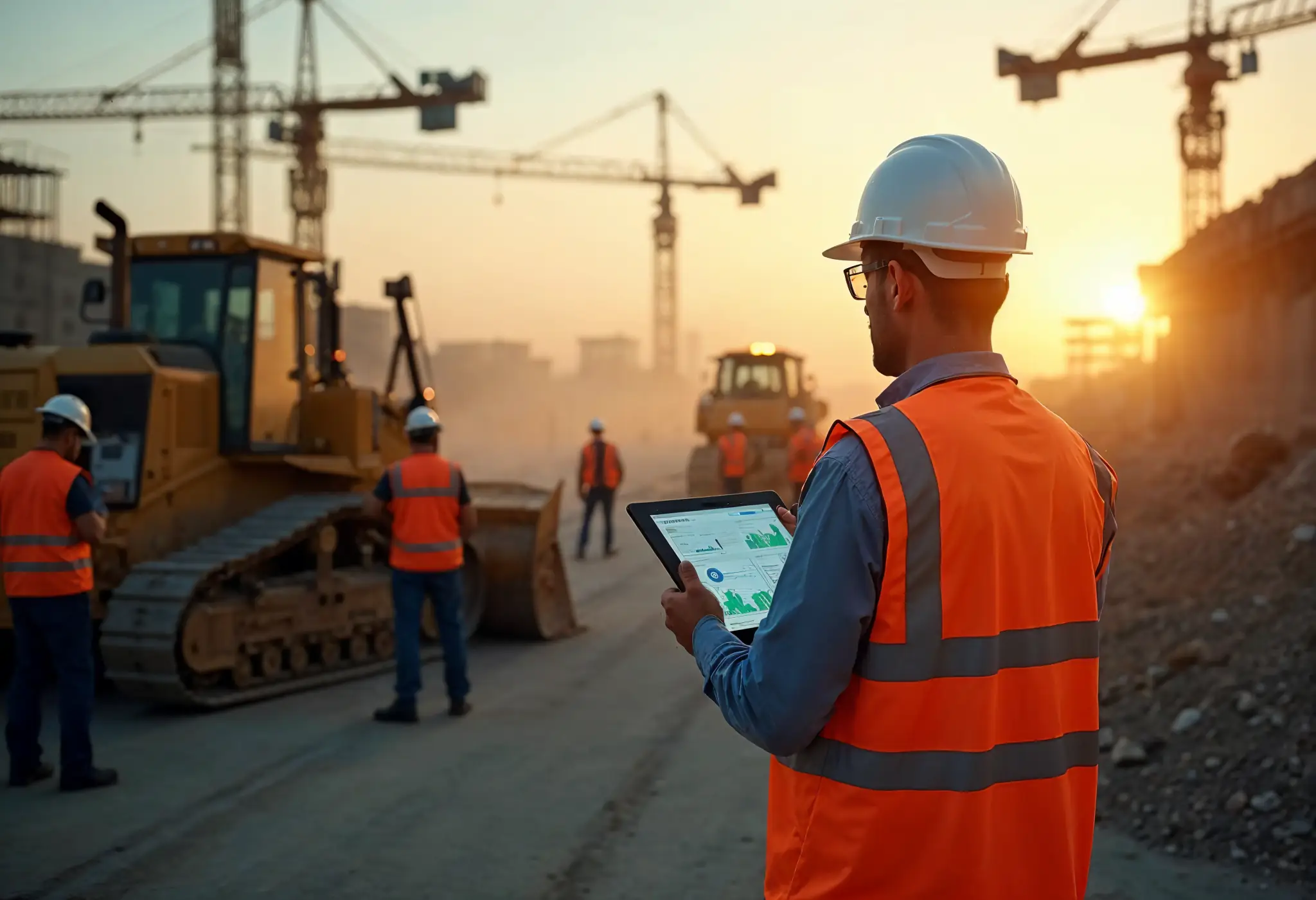
How to Implement a Construction Inventory Management System for Equipment Efficiency
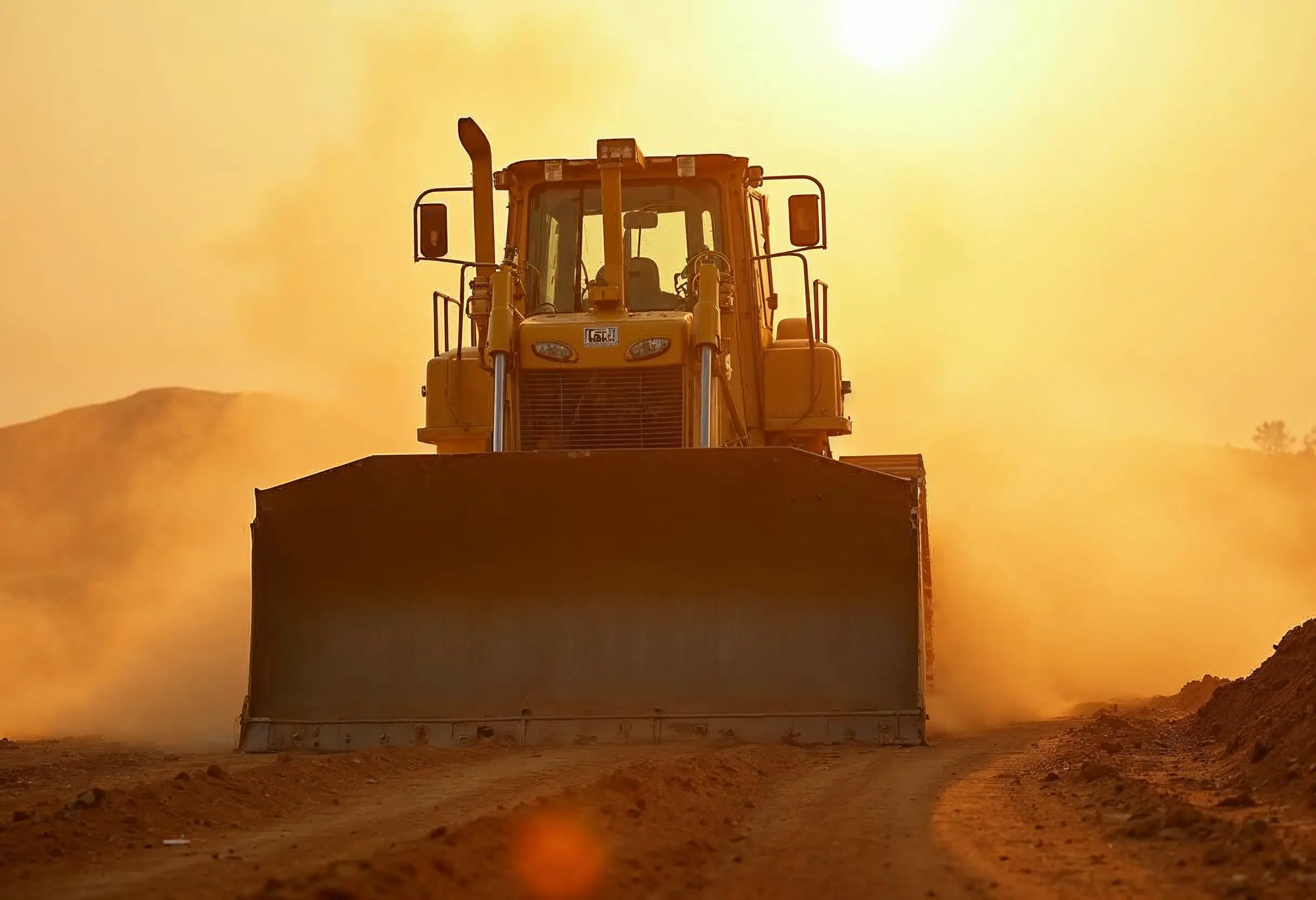
How to Extend Equipment Life Expectancy with Regular Maintenance
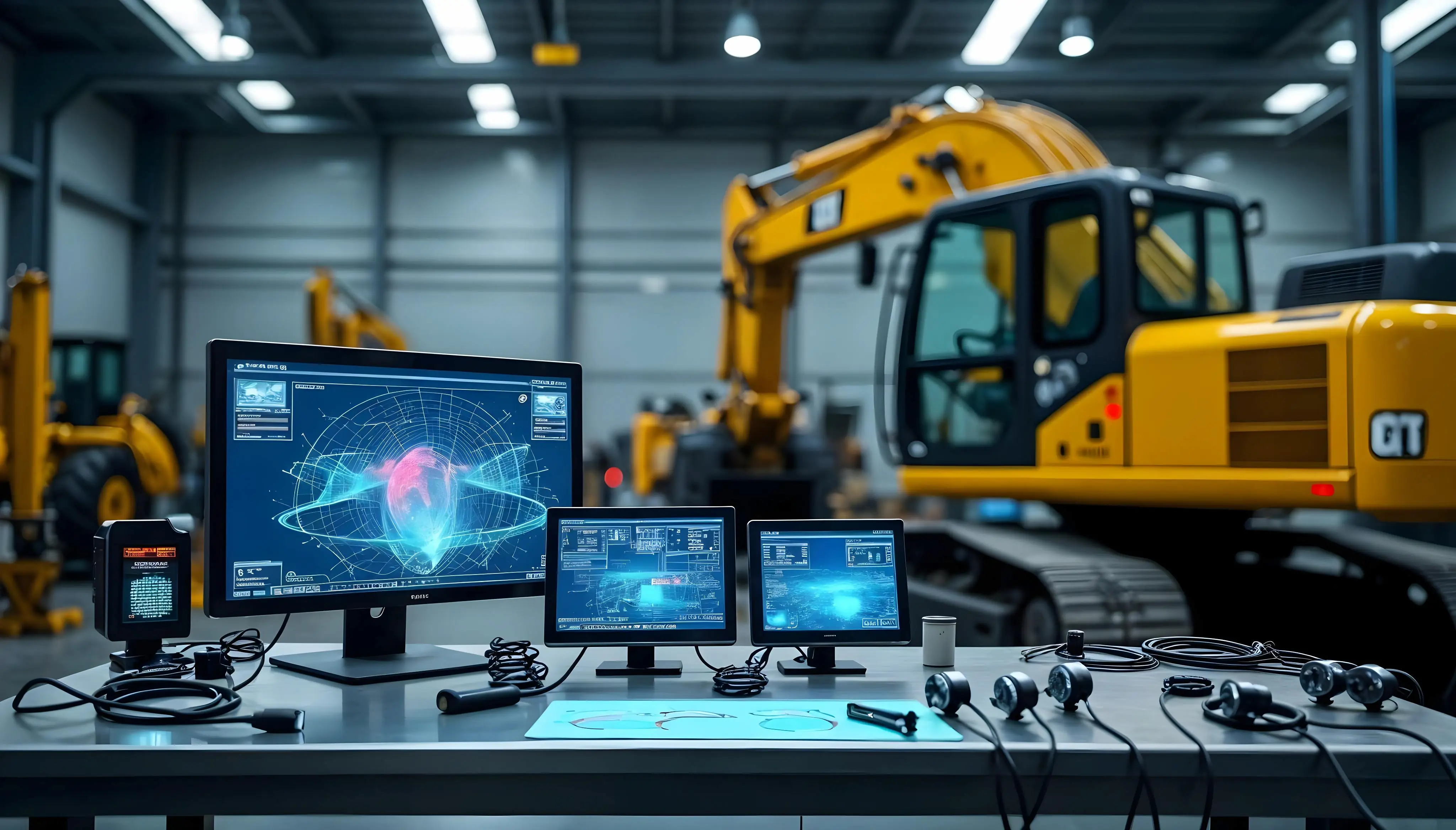
Advanced Heavy Equipment Diagnostic Tools: Ensuring Construction Machinery Quality
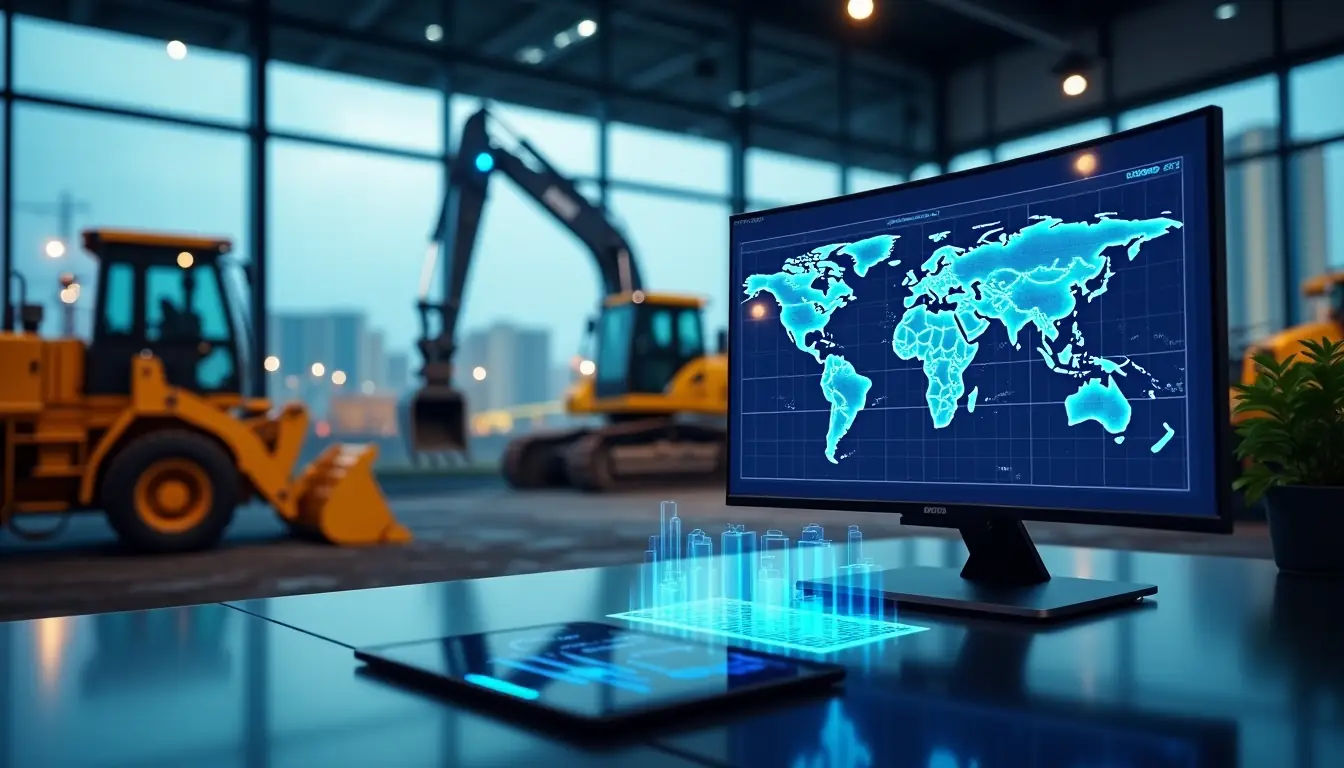
Essential Features Your Construction Equipment Inventory System Needs
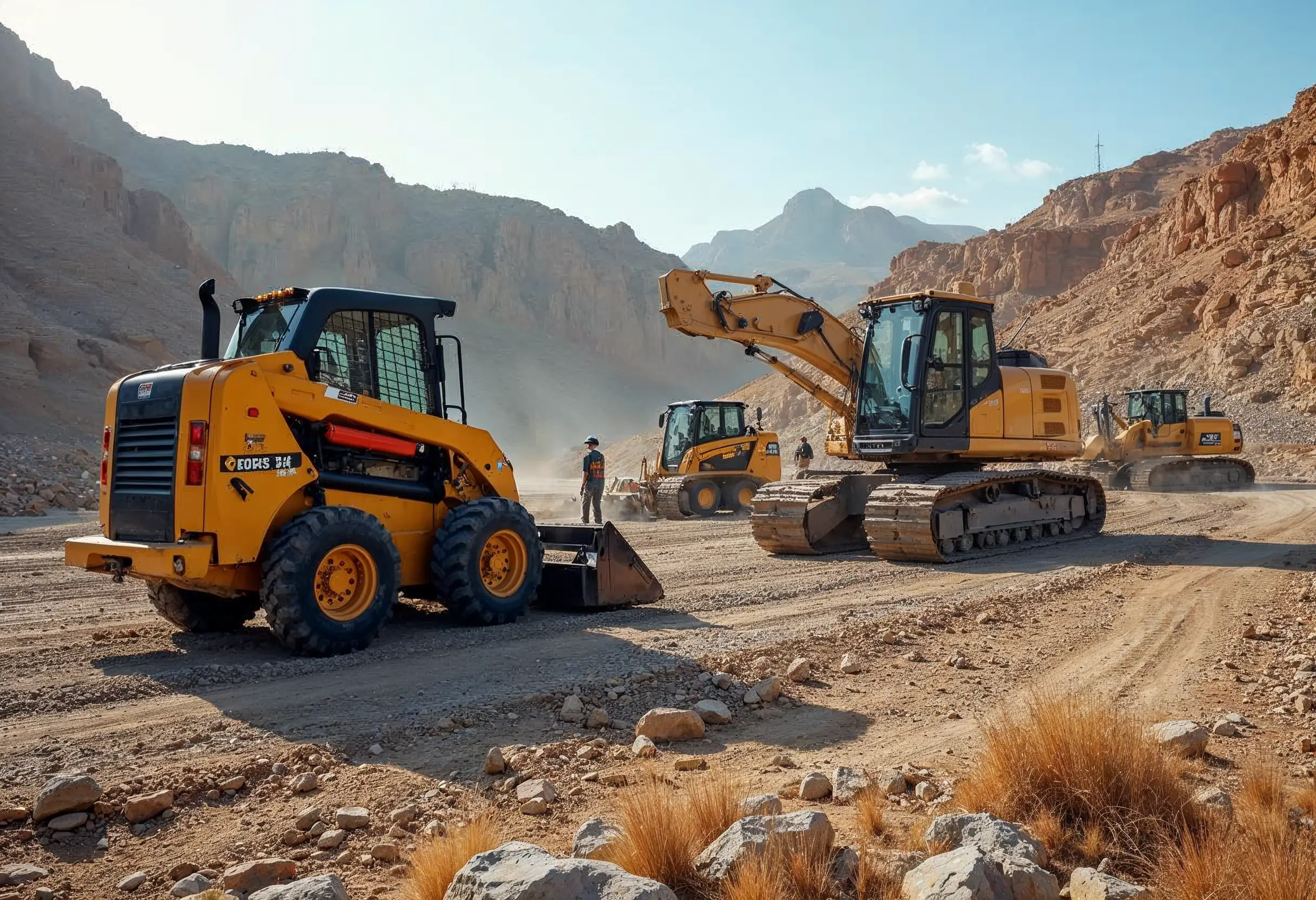
29 Quick Tips for Choosing Construction Equipment for Remote Locations
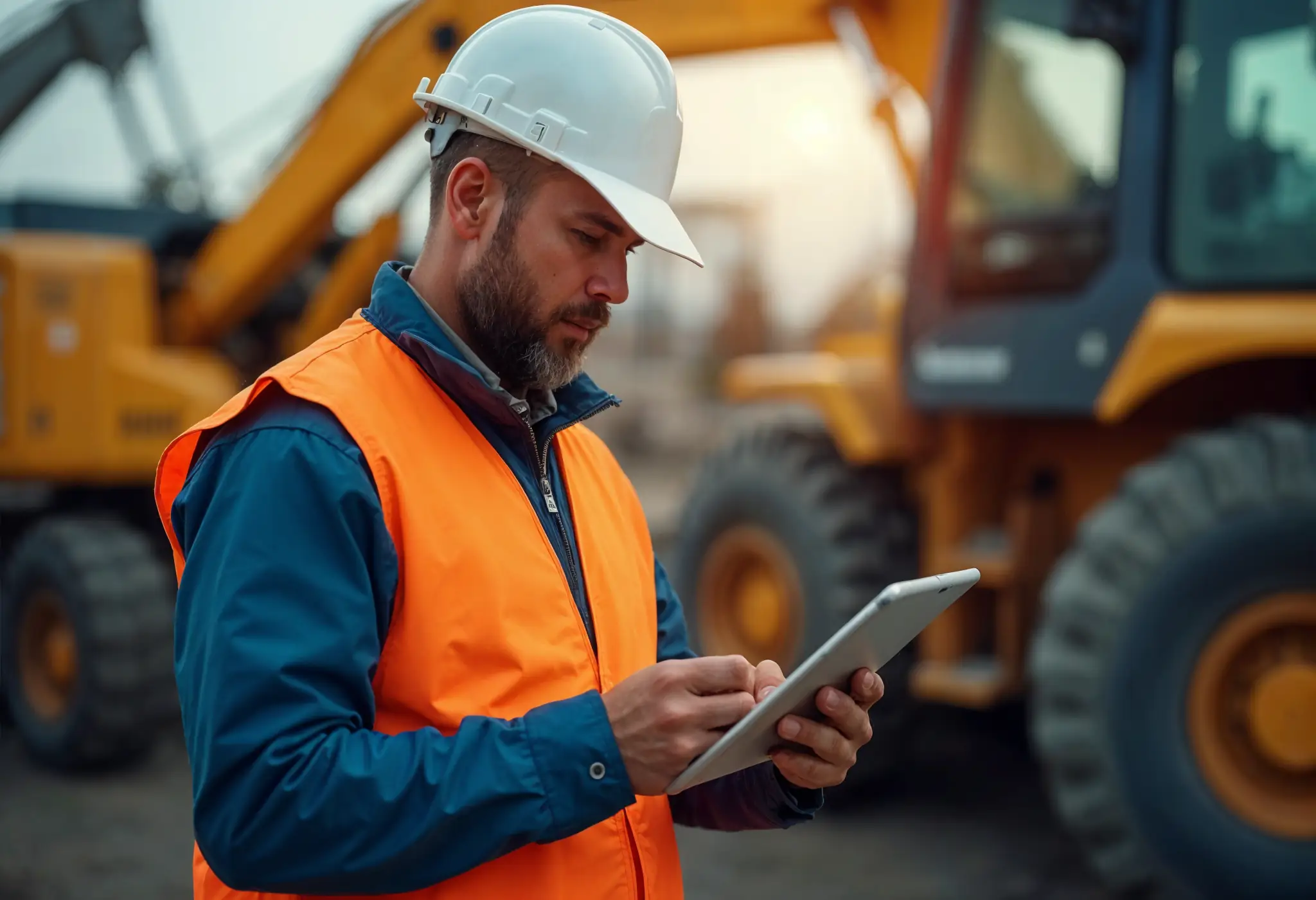
How to Select Construction Machinery with Optimal Equipment Maintenance in Mind
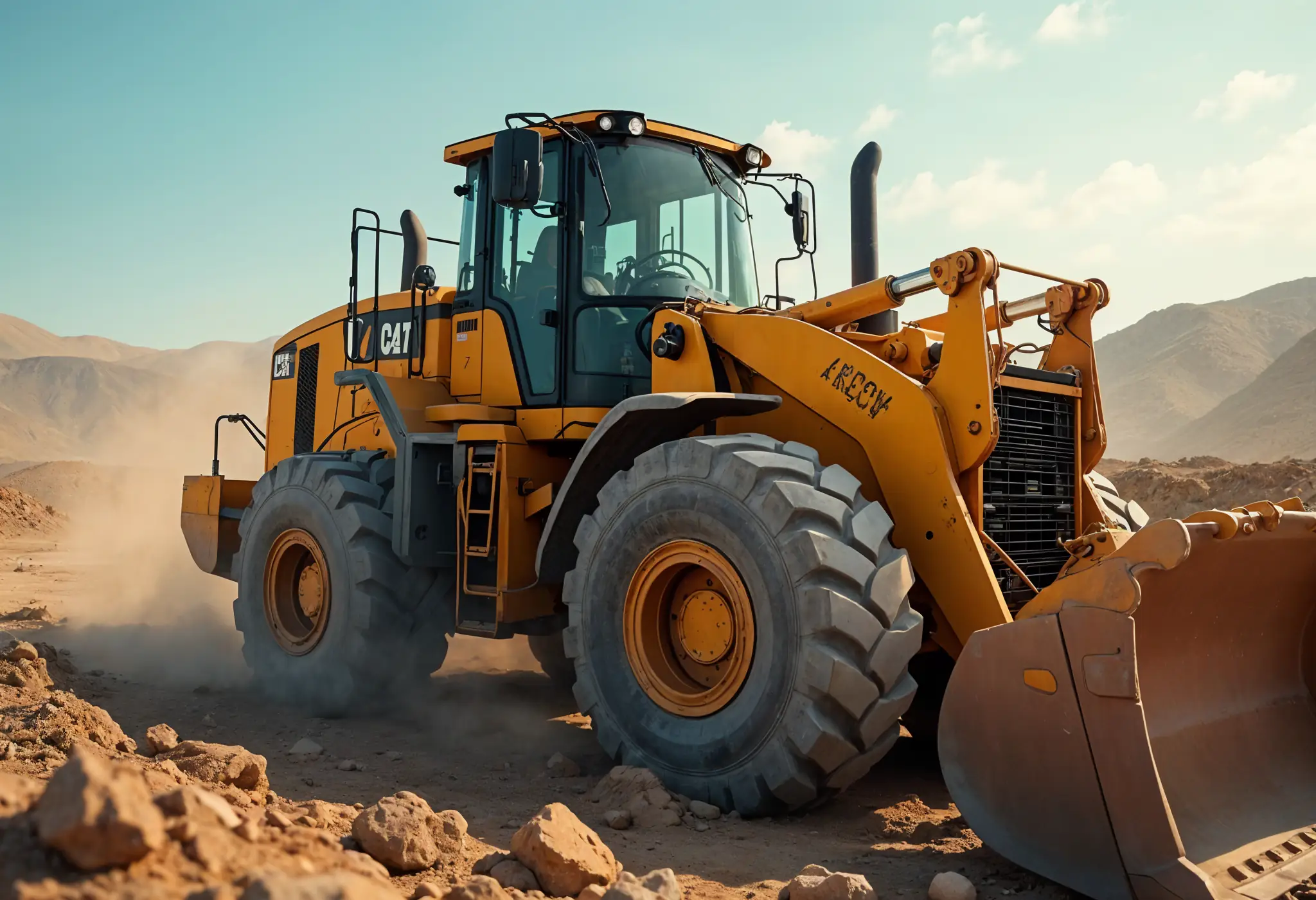
Top 25 Tips for Selecting Bulldozers for Construction Sites
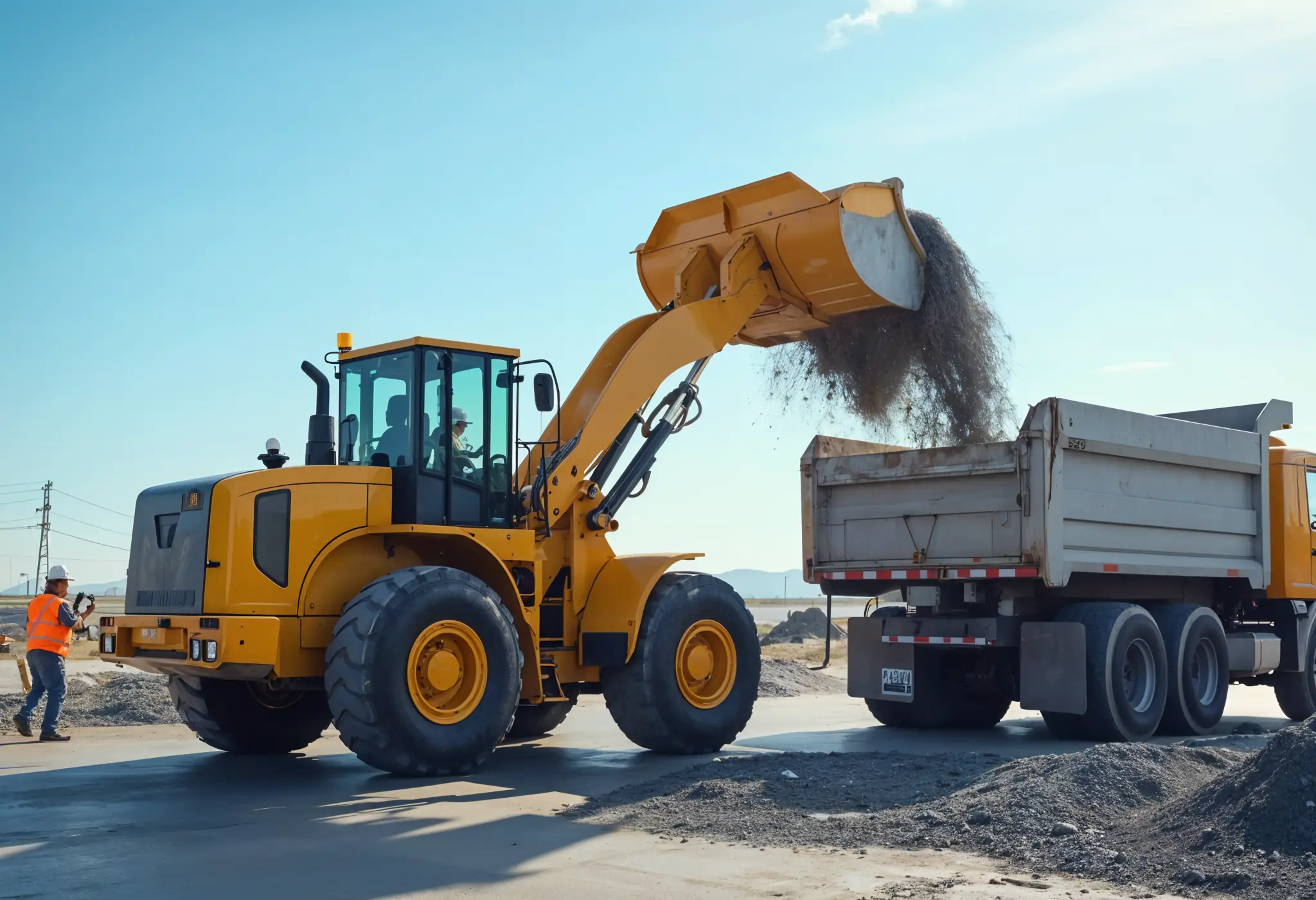
Which Construction Loader is Best for Your Project Needs?
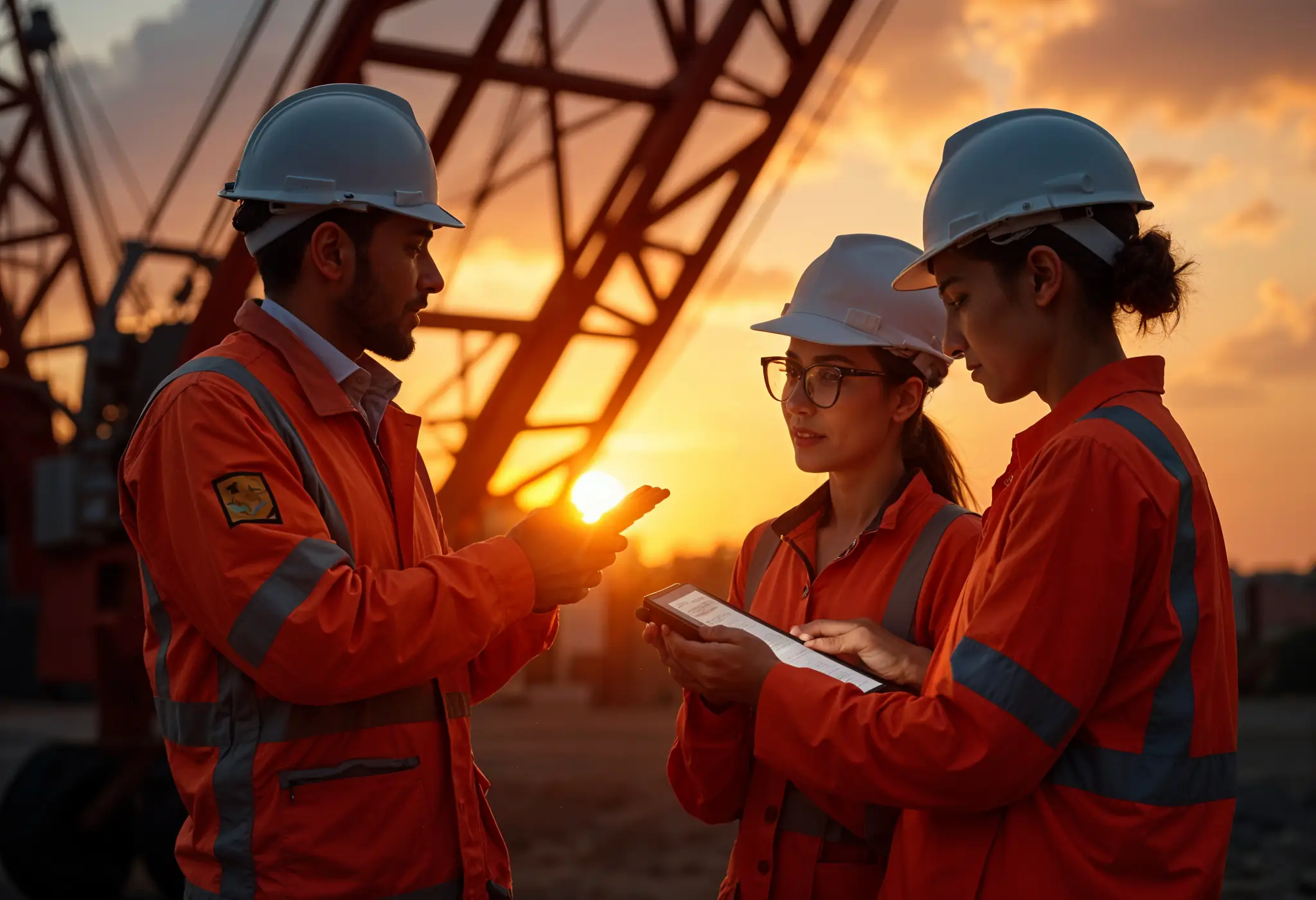
4 Key Steps to Form a Construction Machinery QC Team
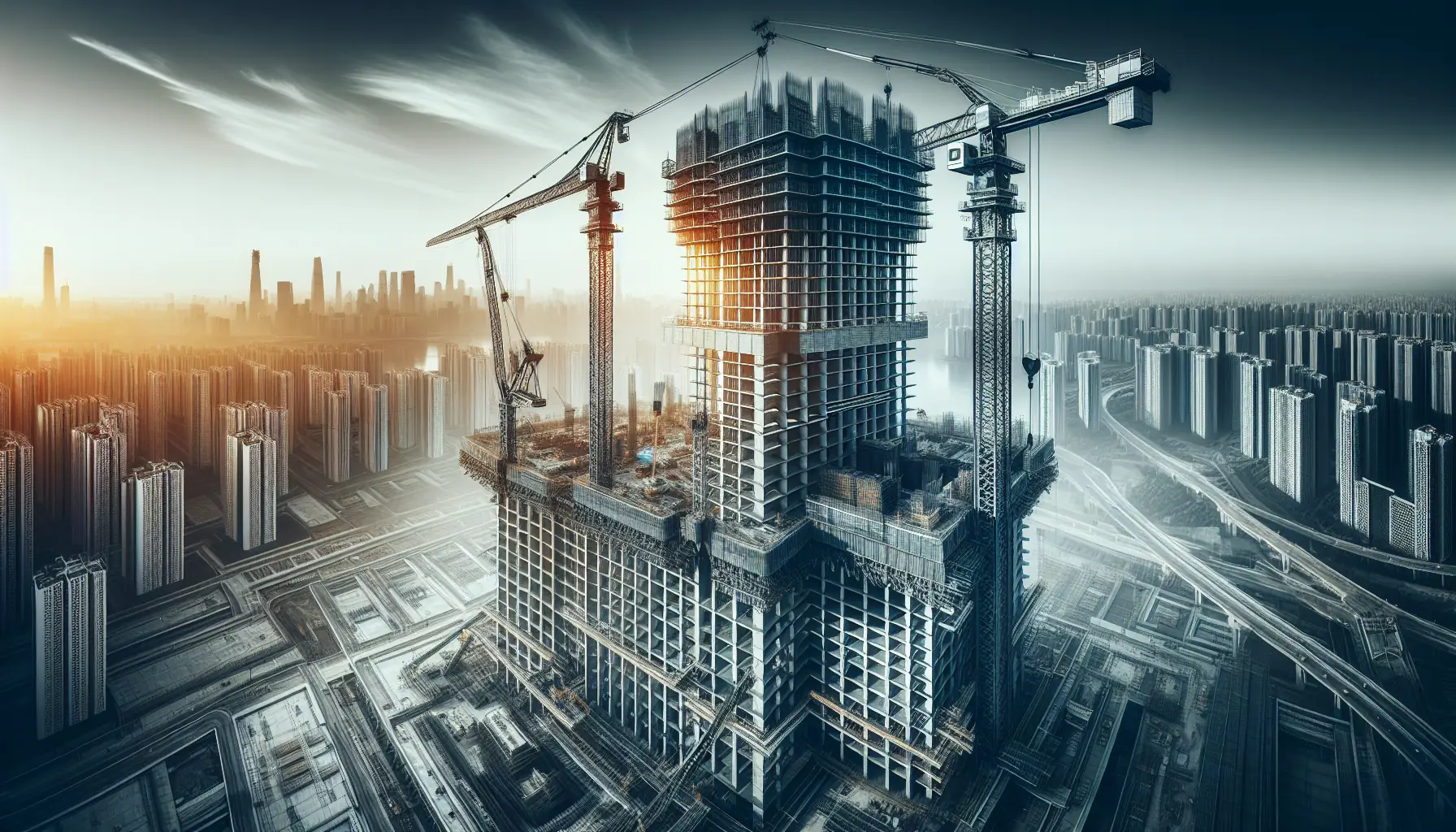
15 Essential Tips for Selecting the Perfect Crane for Construction
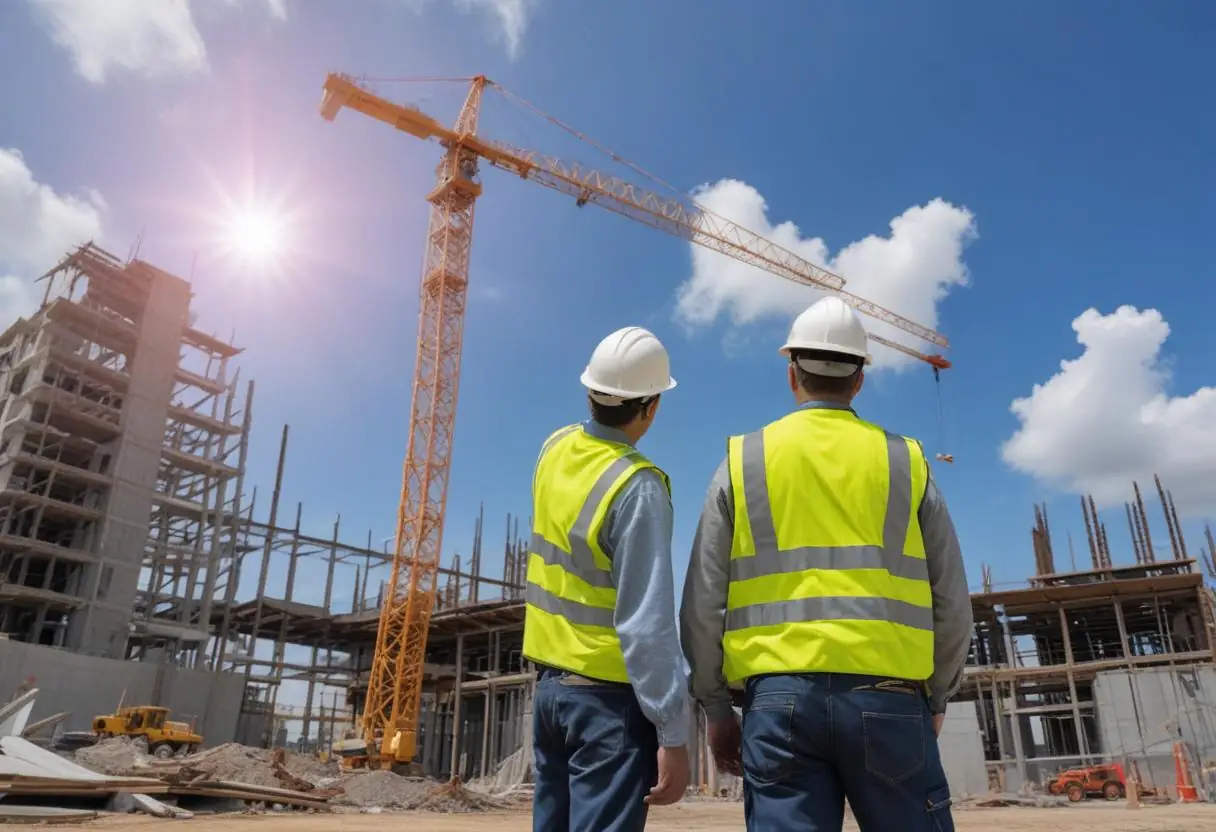
Maximize Savings: Multi-Purpose Construction Machinery for Lower Costs
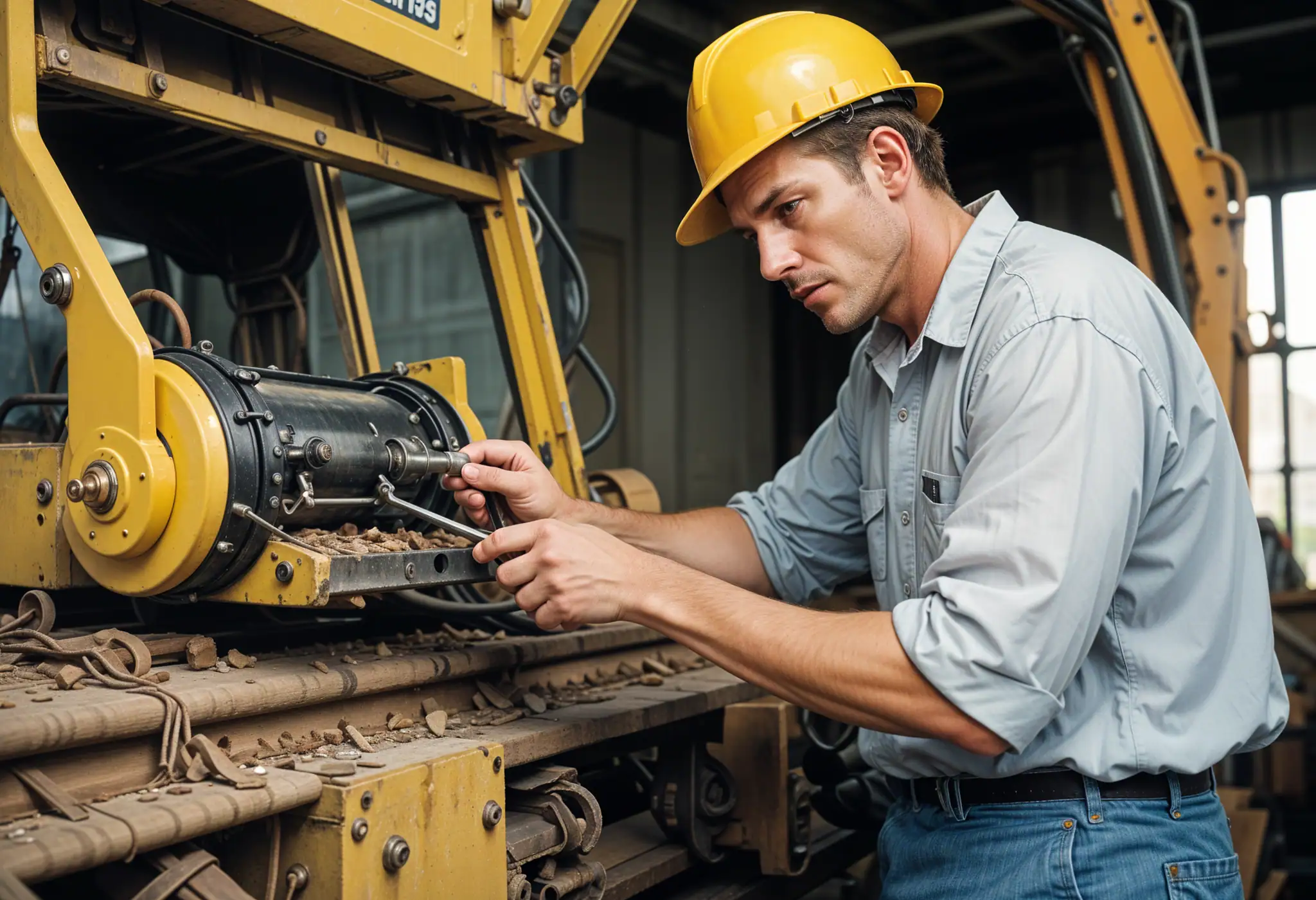
Affordable Heavy Equipment Parts: A Sourcing Guide
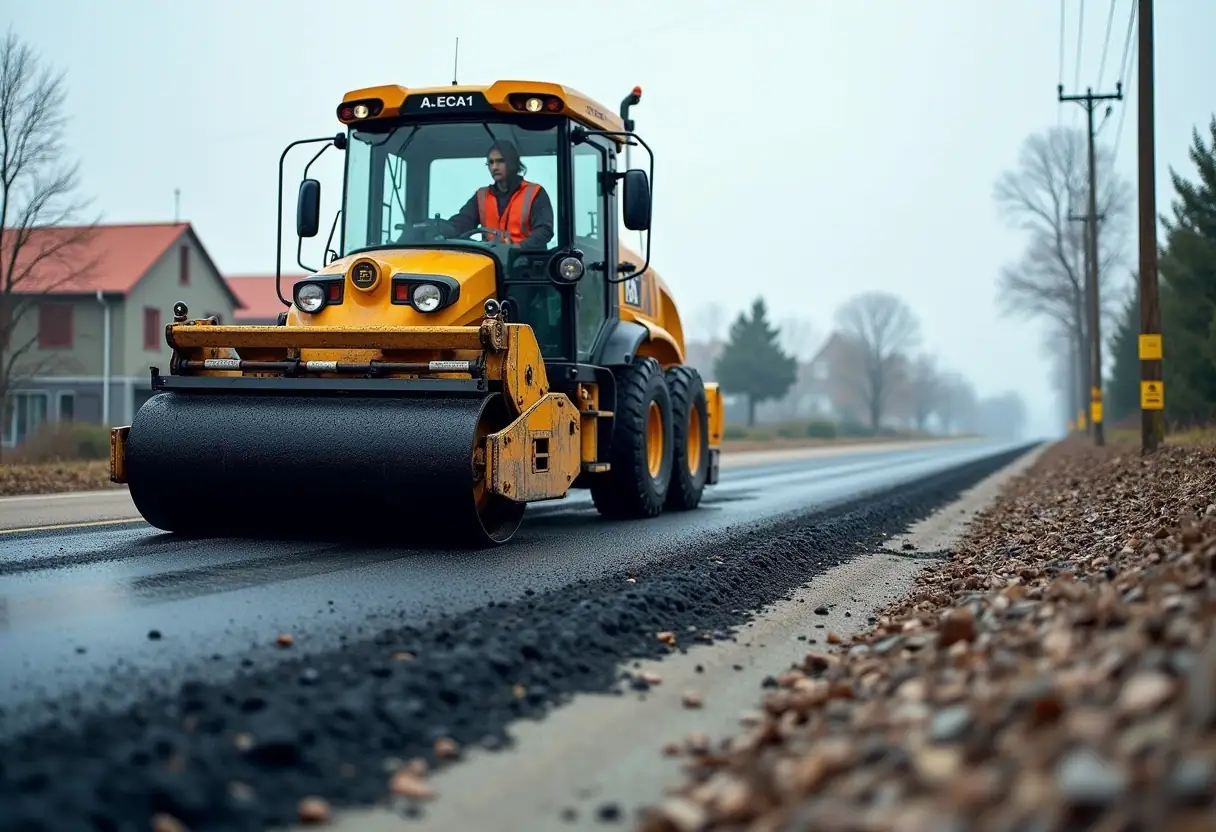
Choosing the Right Road Construction Equipment: A Complete Guide
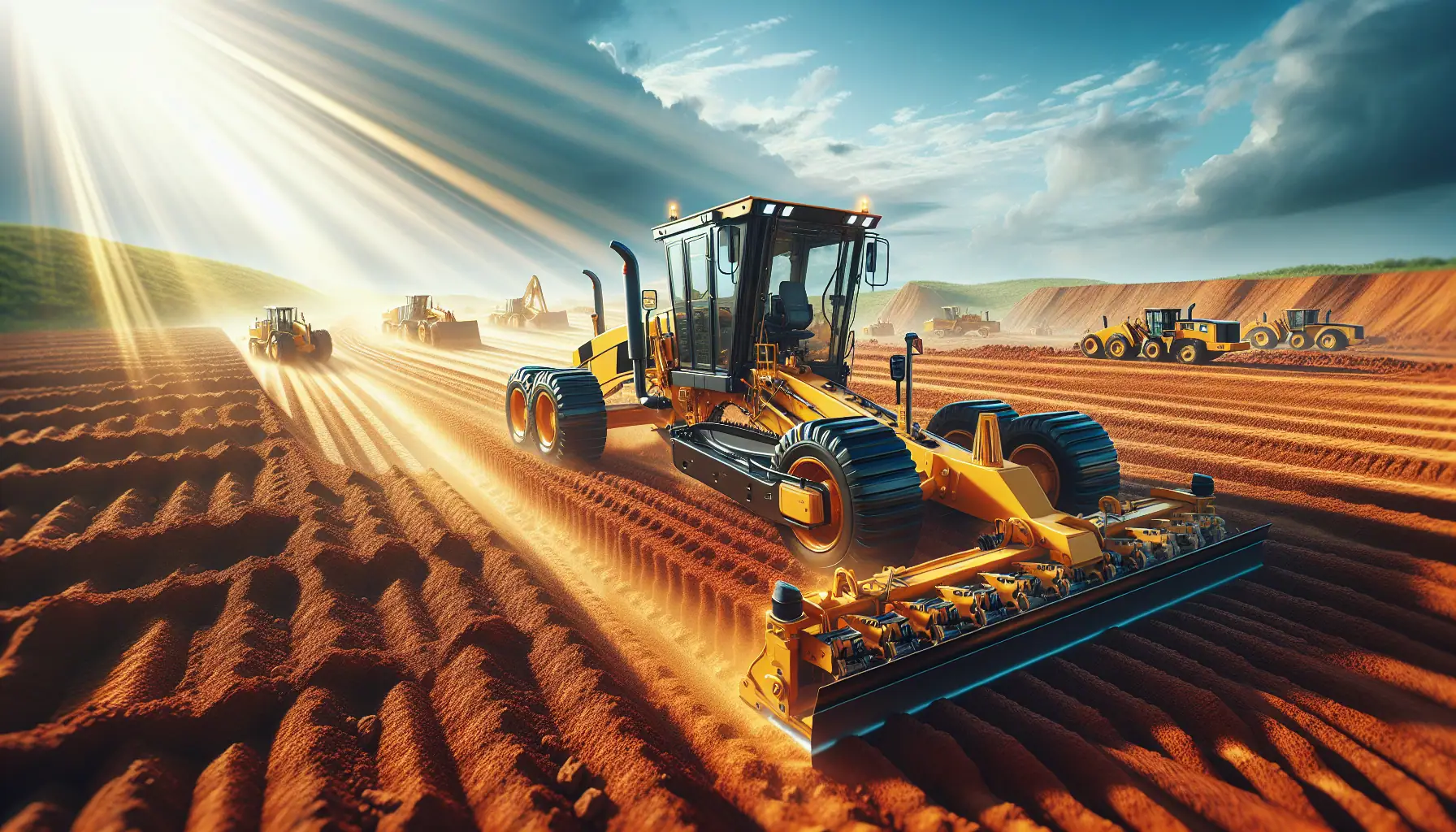
Motor Graders: Key Elements to Consider for Optimal Selection
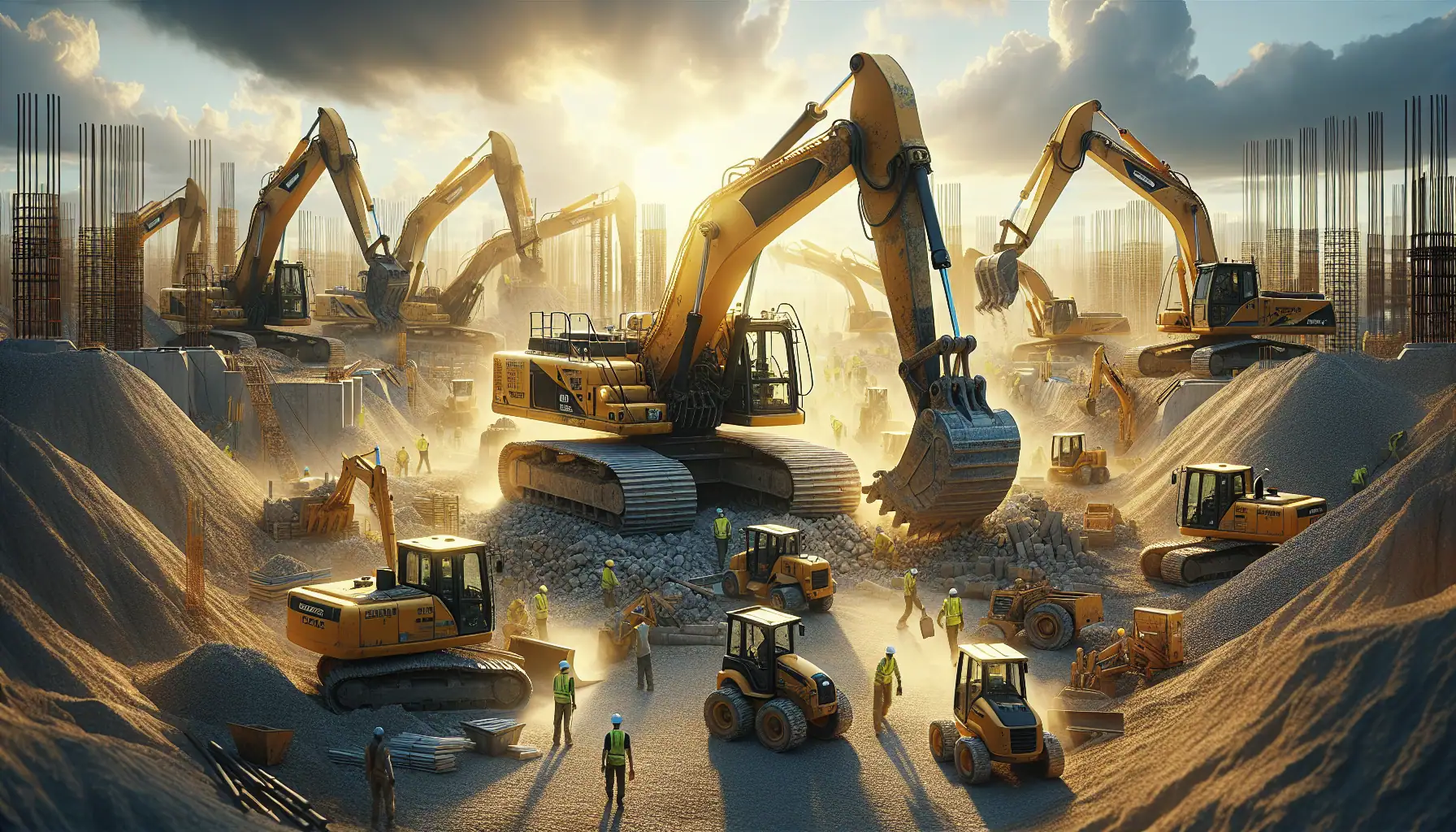
A Detailed Guide to Choosing Excavators for Construction Work
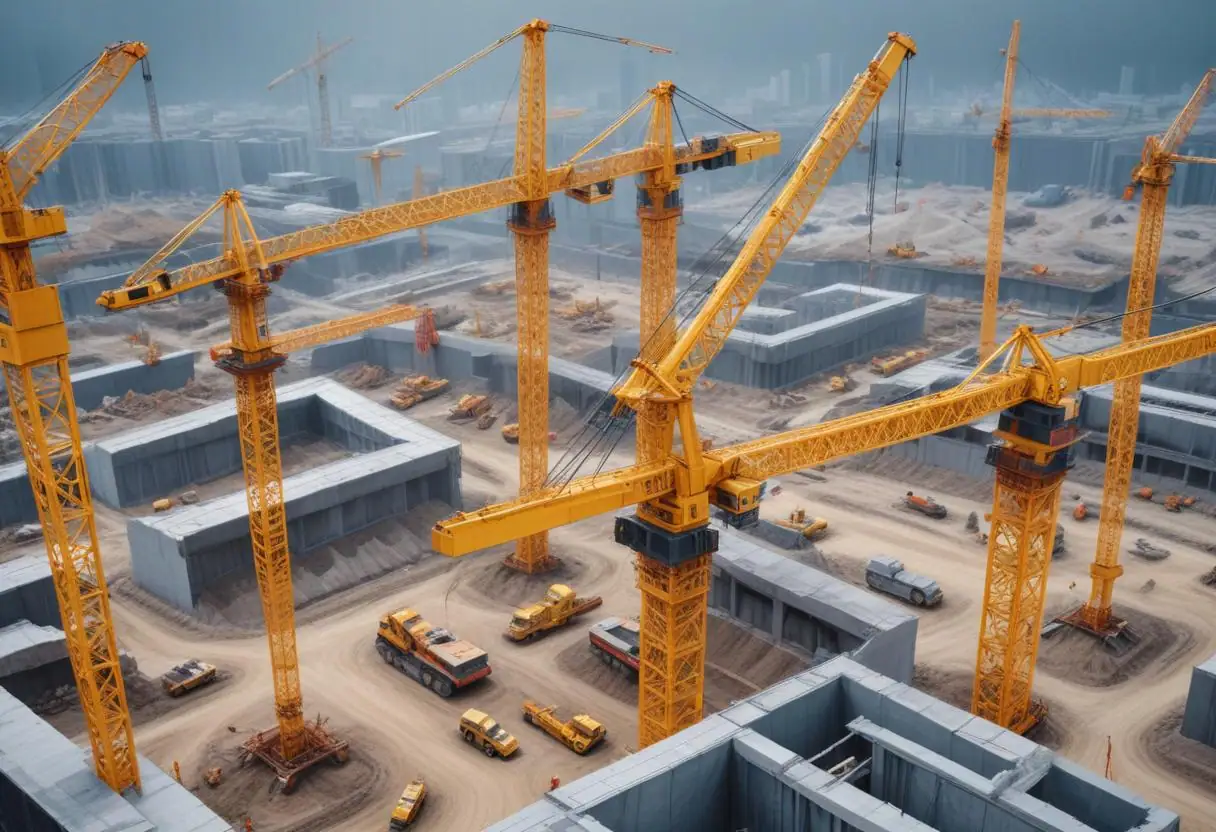
Top Tips for Choosing Cranes for Construction Projects
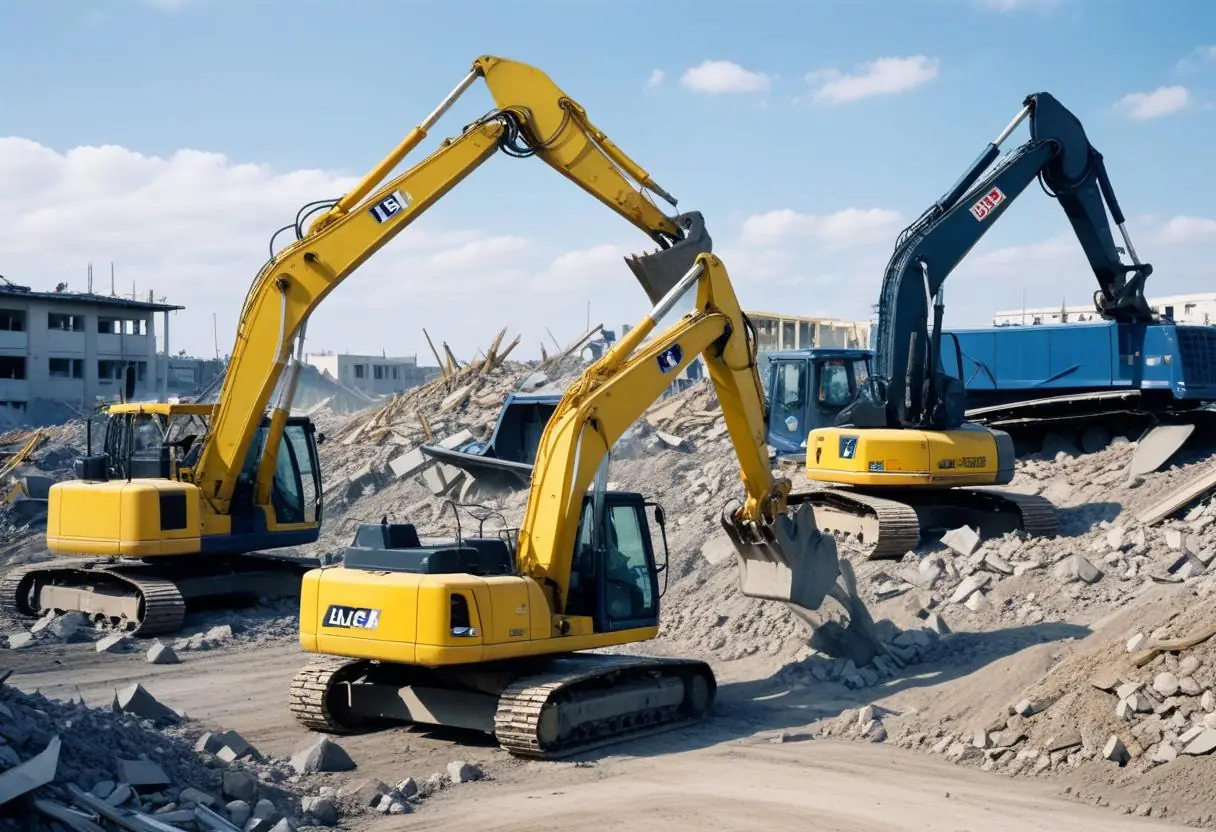
5 Top-Rated Demolition Machines for Construction Professionals
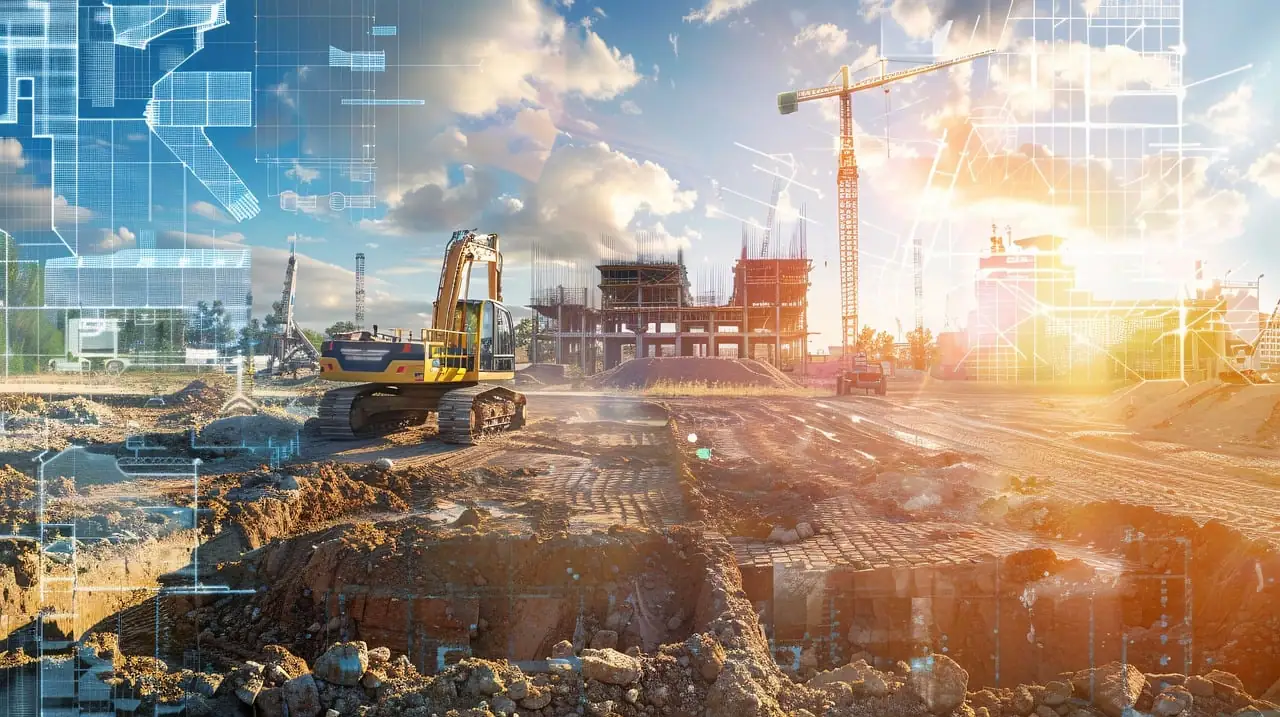
Expert Tips on Choosing Earthmoving Equipment for Large Projects
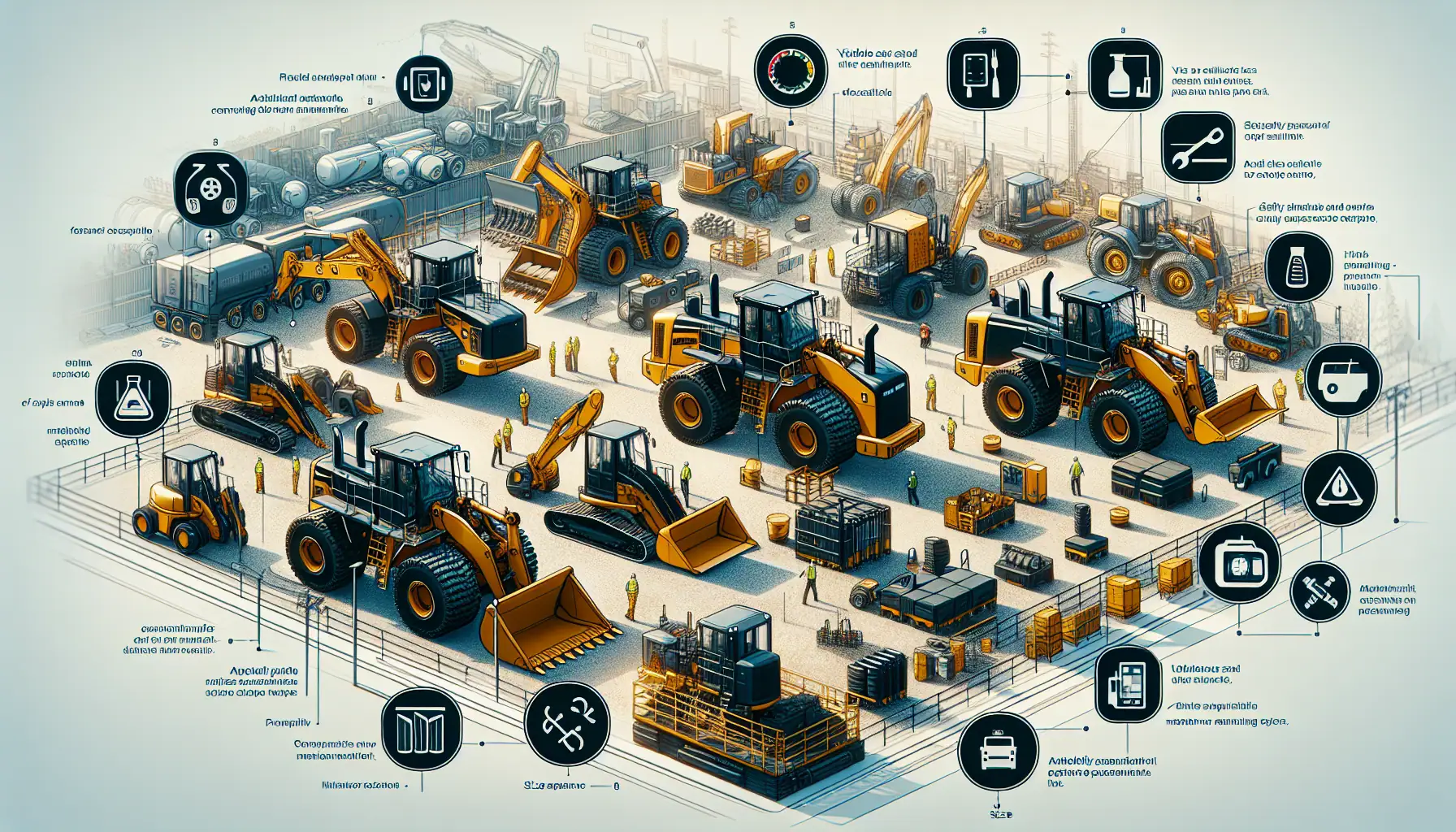
Top Functional Criteria for Selecting Heavy Construction Equipment
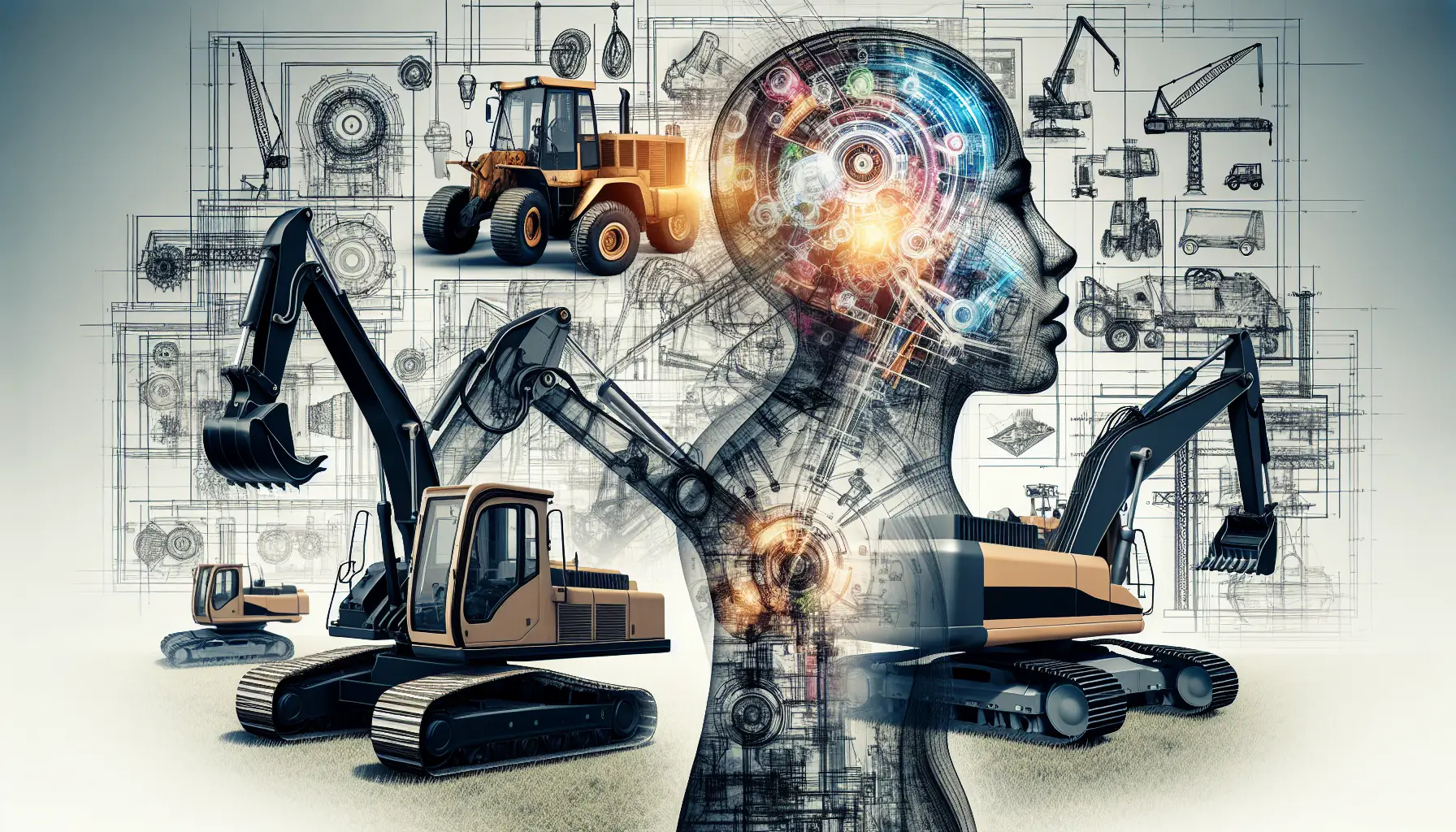
Construction Machinery: Detailed Guide to Equipment Specifications
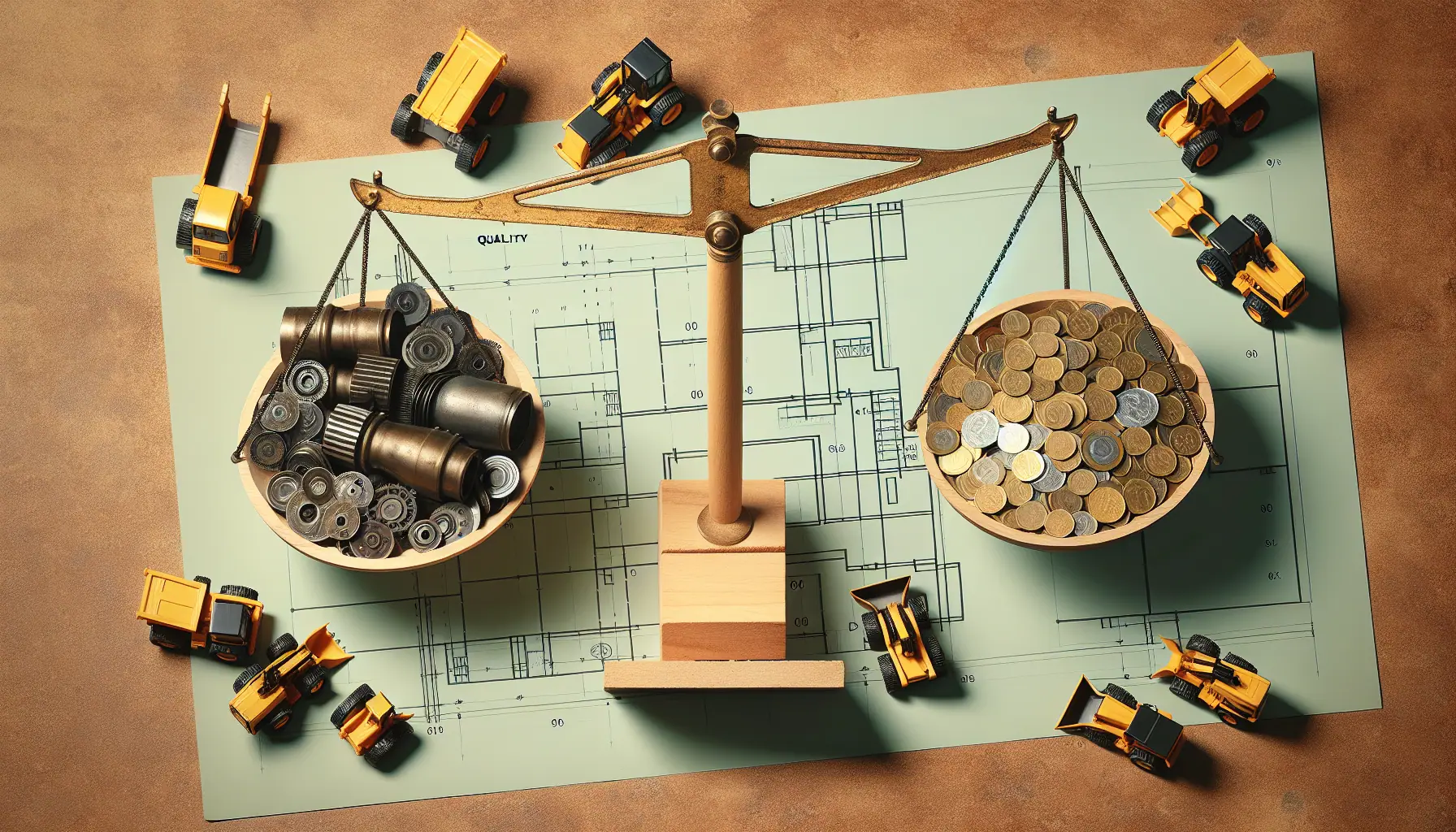
Heavy Machinery Prices: Key Factors in Cost and Quality Balance
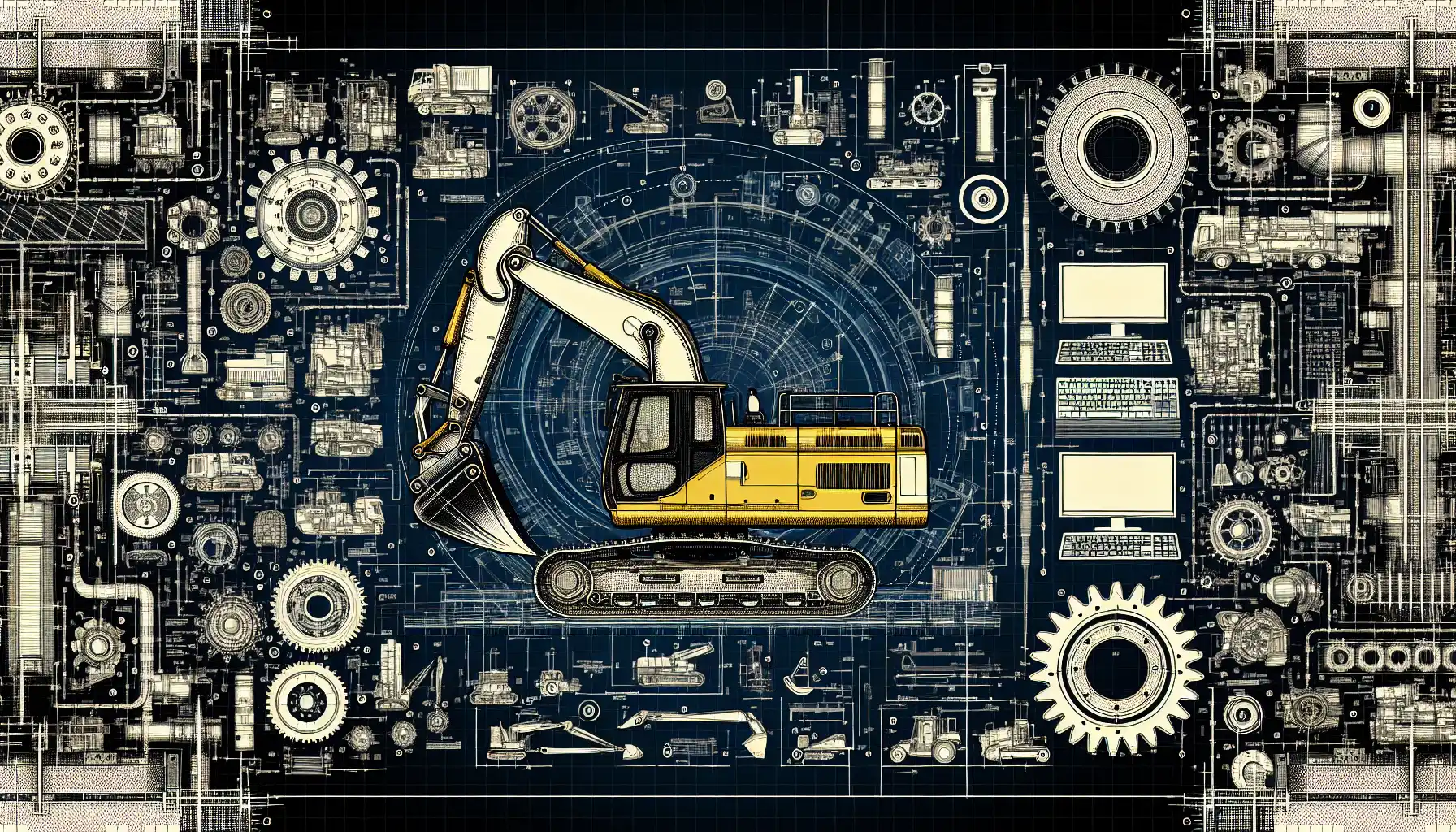
Best Construction Heavy Equipment Brands: Pros and Cons
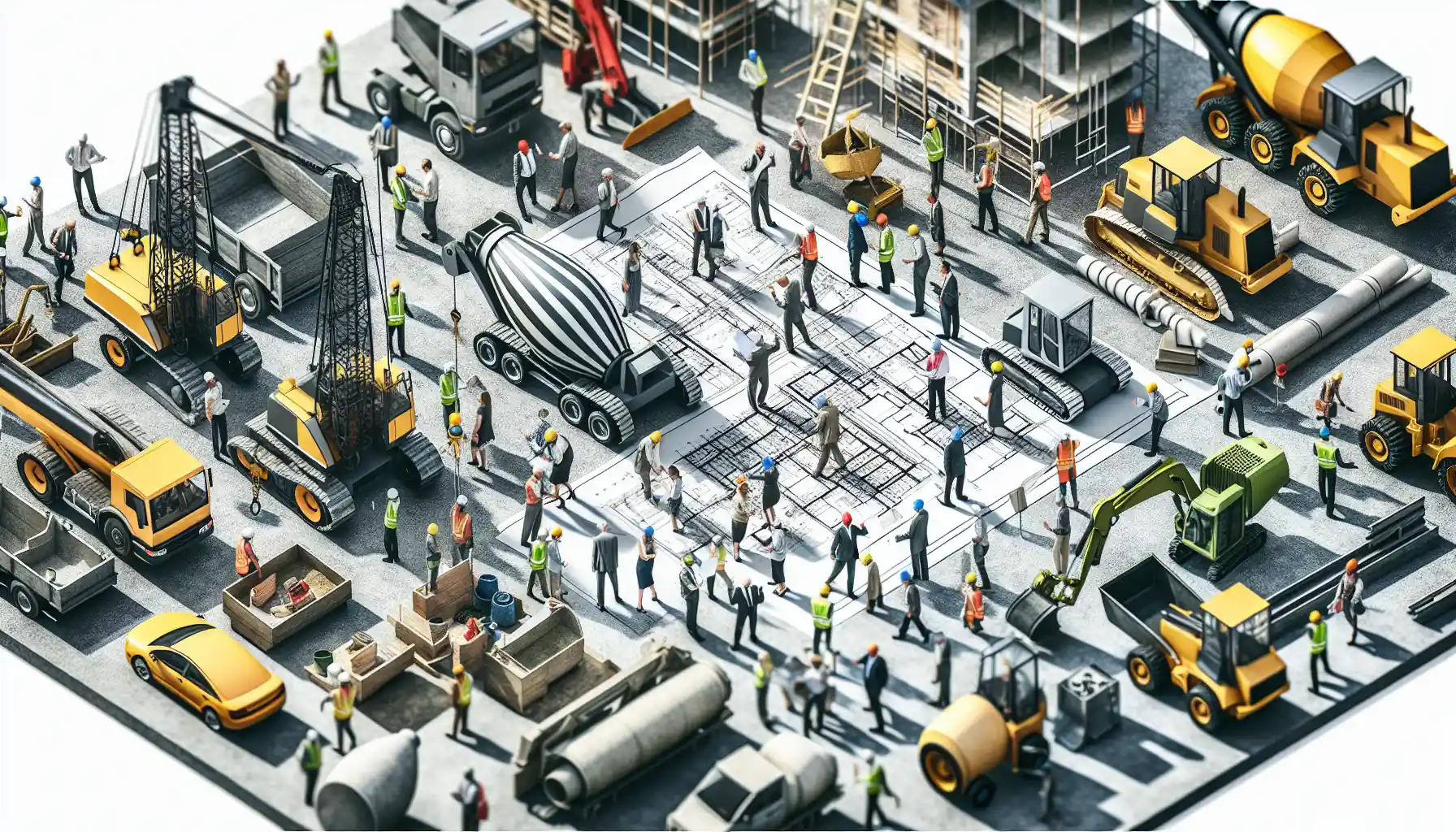
Construction Site Equipment: How to Determine Your Requirements
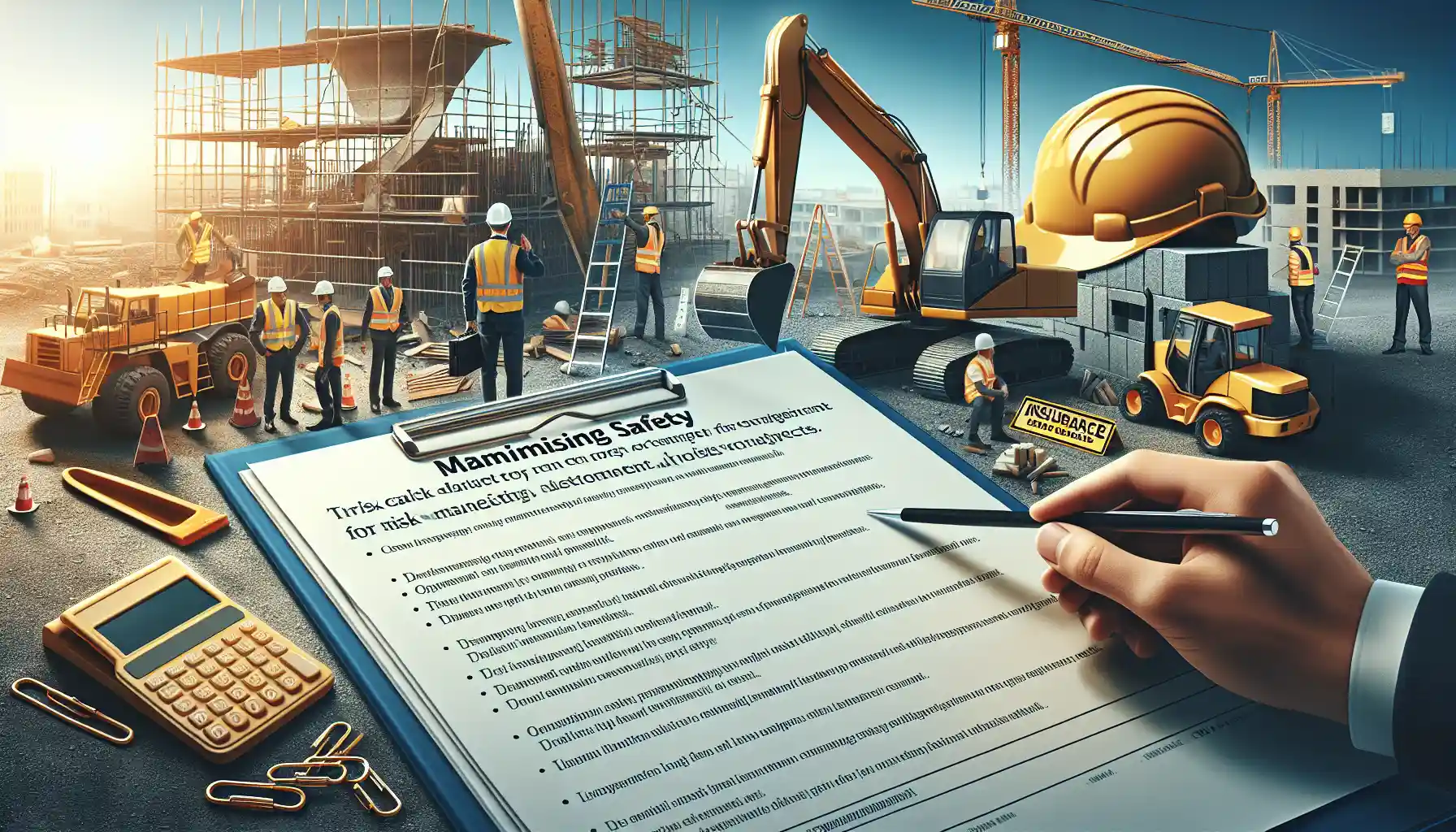
Maximizing Safety: Risk Management for Construction Projects
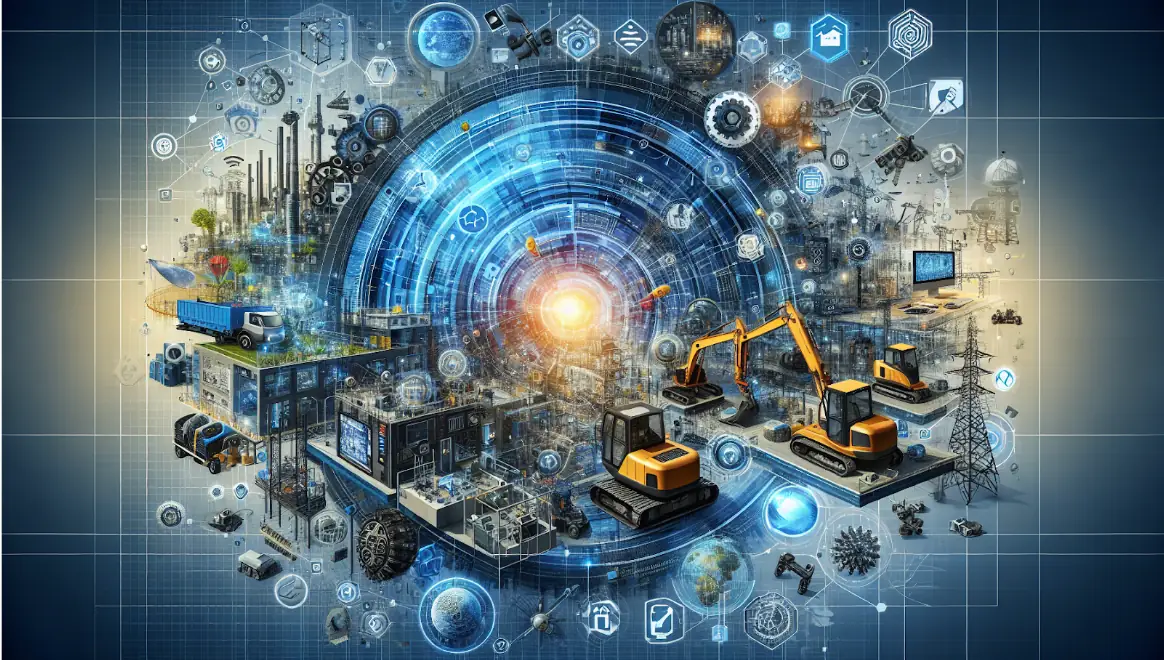
Innovations in Construction: Transforming Machinery and Equipment
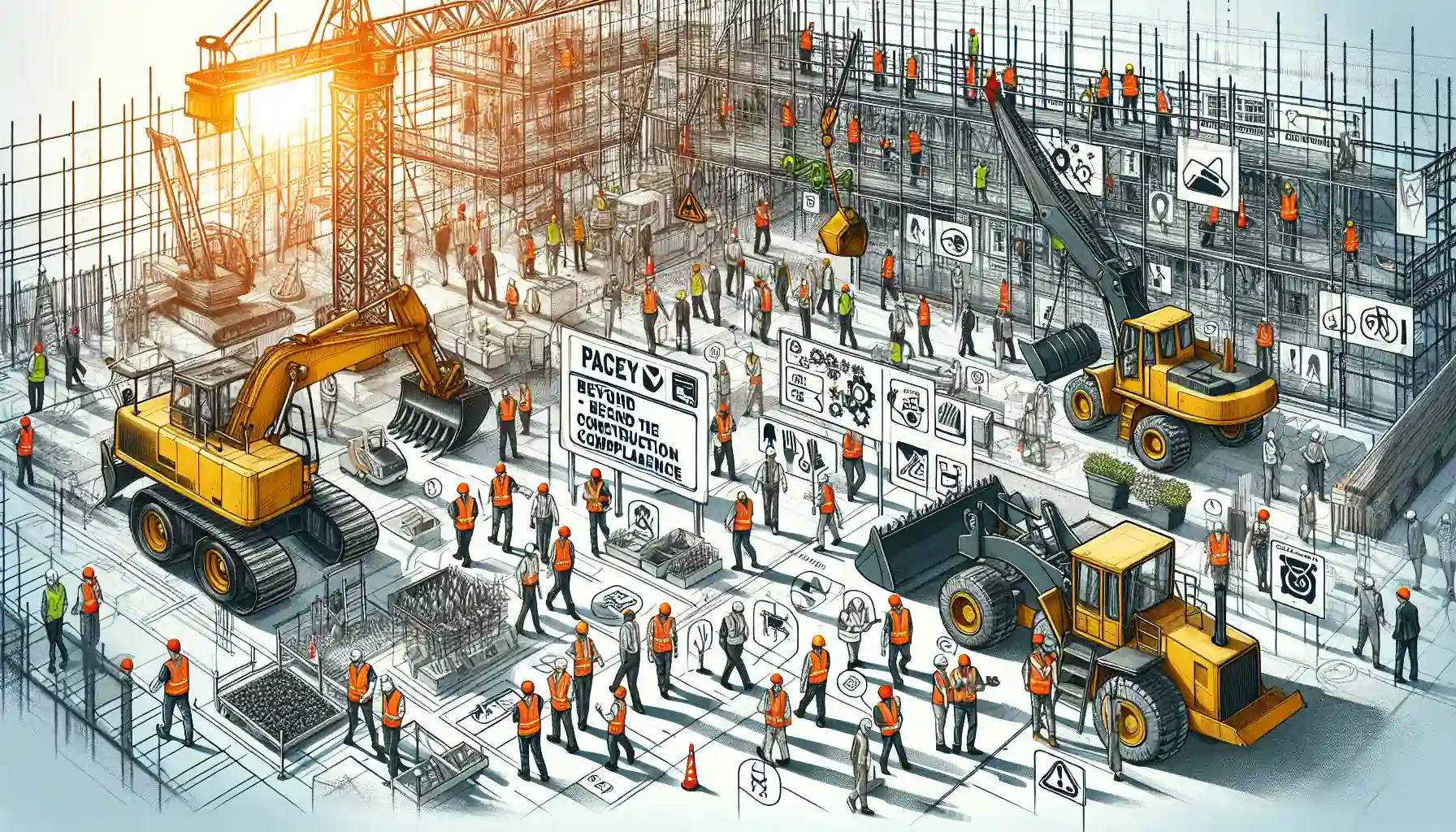
Heavy Equipment Safety: Beyond the Basics in Construction Compliance
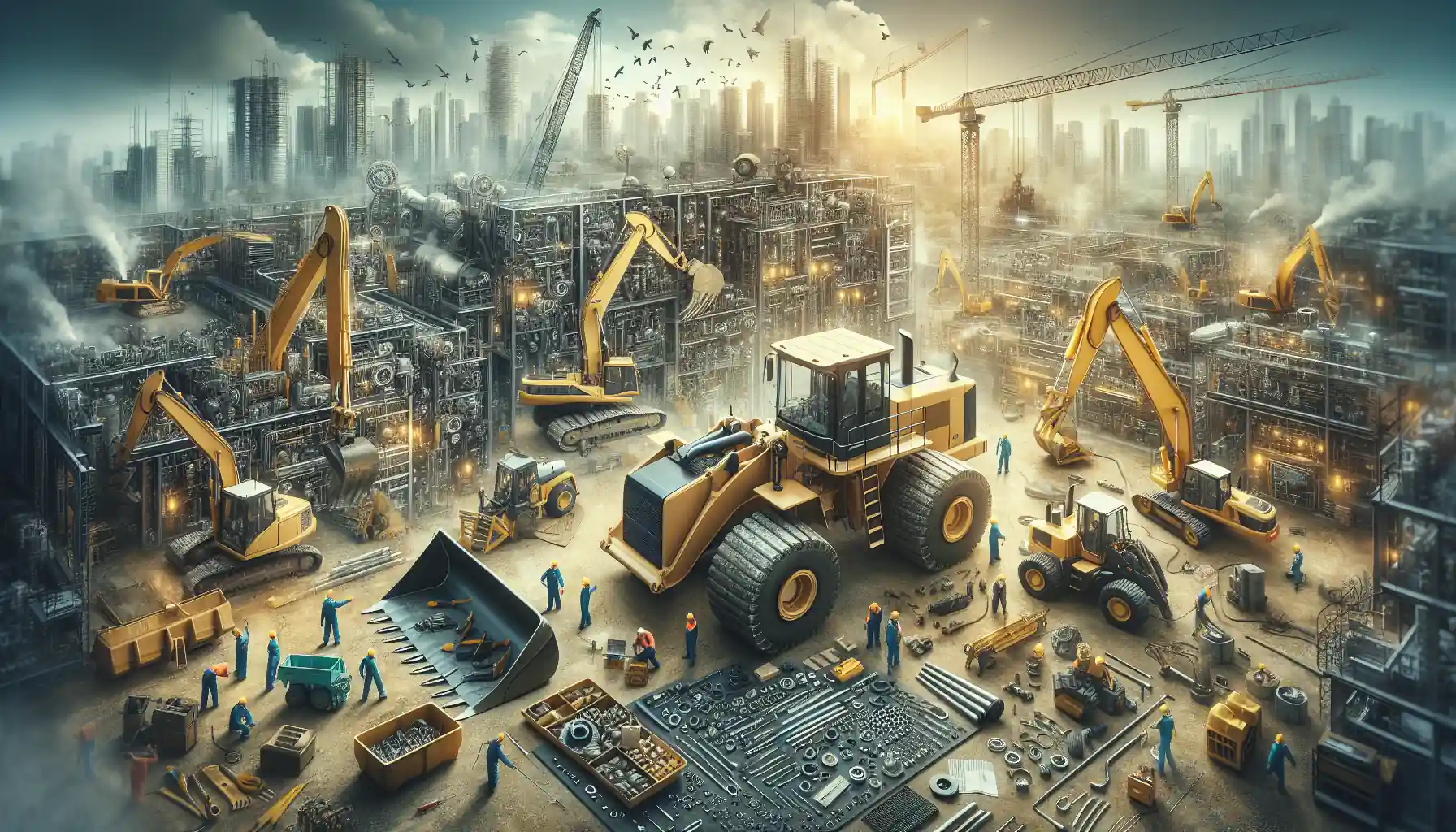
The Essential Handbook for Construction Equipment Repair and Maintenance
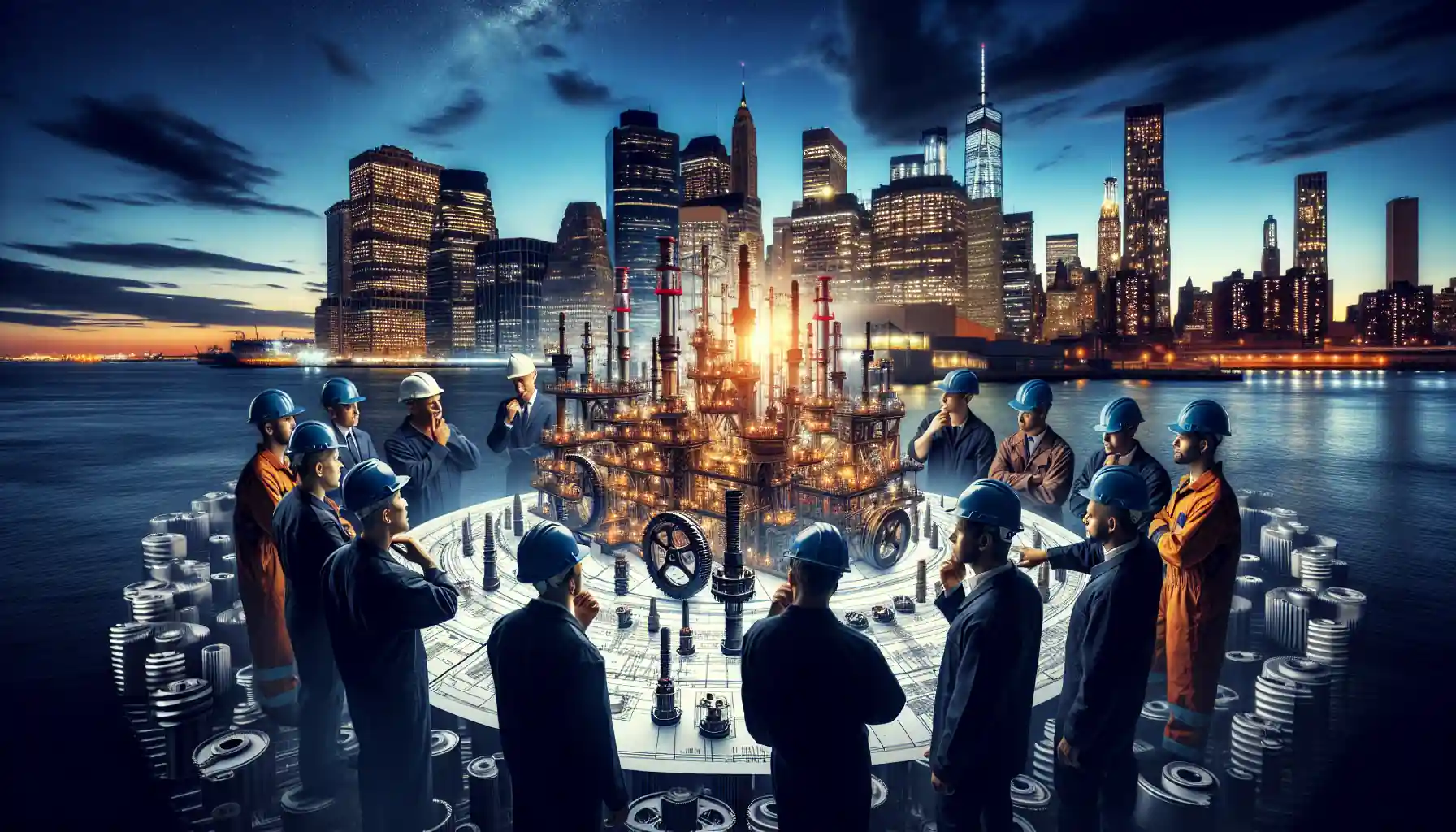
How to Efficiently Source Oil and Gas Machinery Parts in NYC
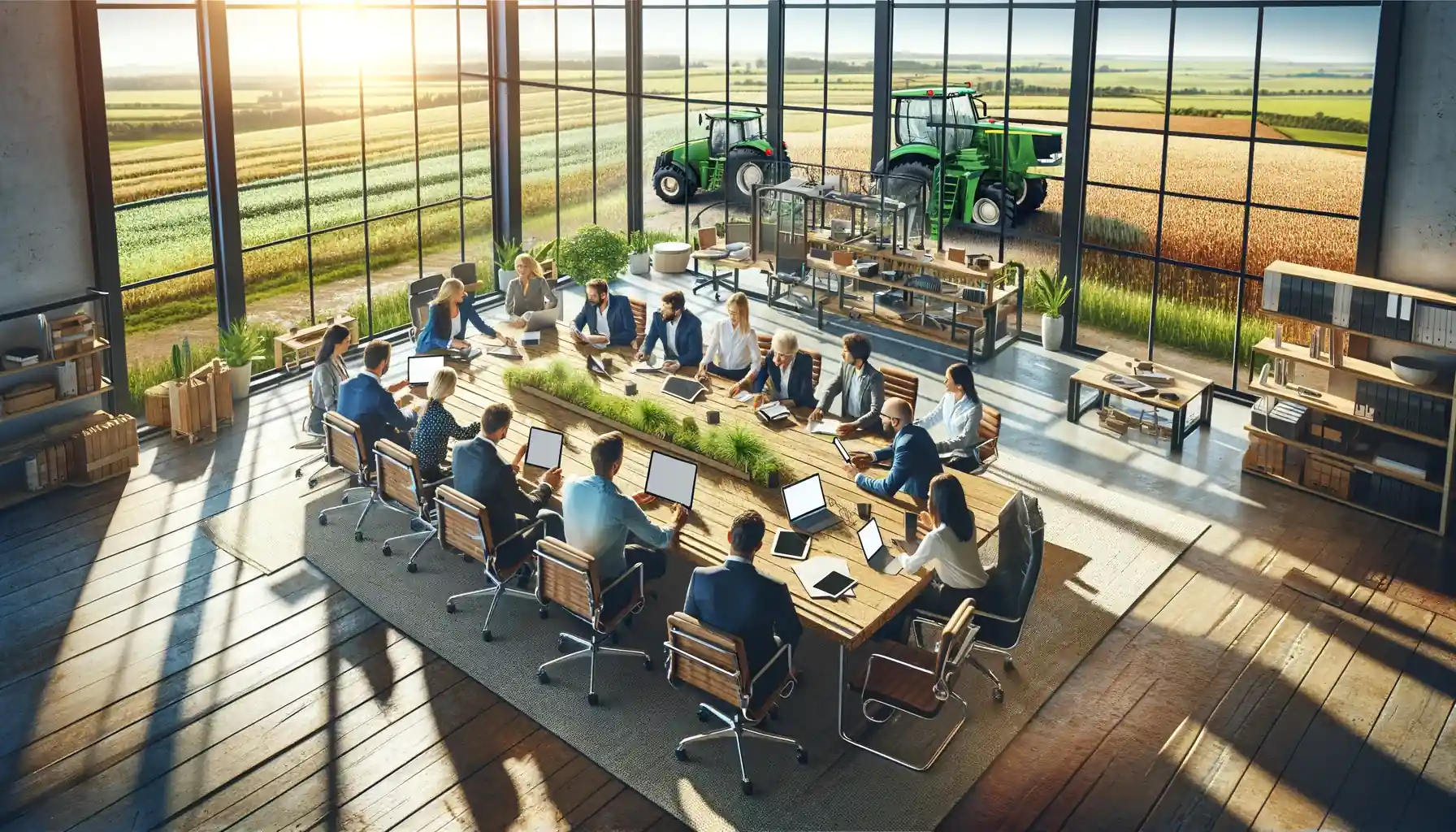
Essential Guide to Sourcing Agriculture Equipment Parts
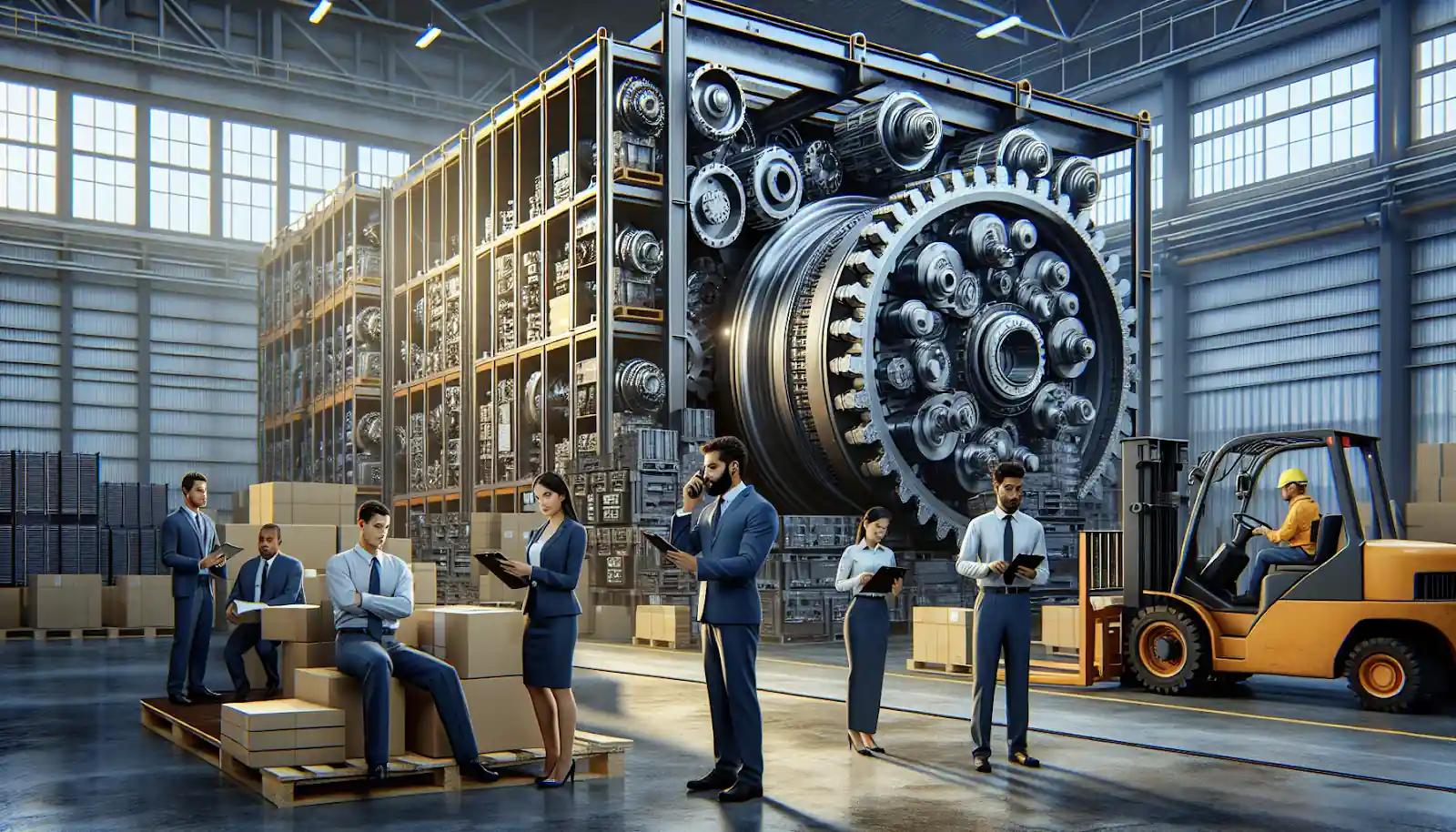
How to Source Mining Machinery Parts: Tips and Strategies
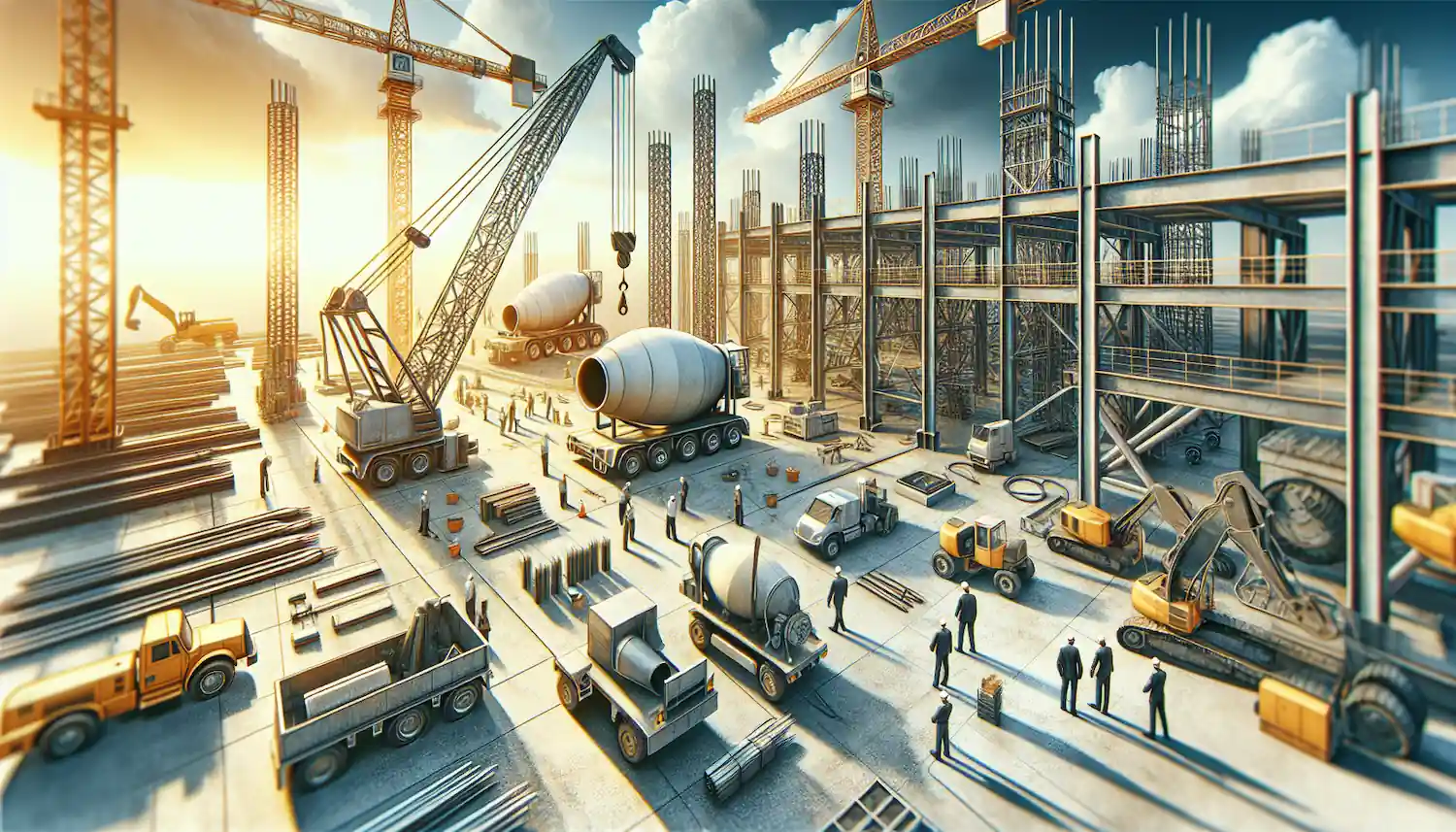