How to Apply Machine Safety Rules: From Selection to Installation
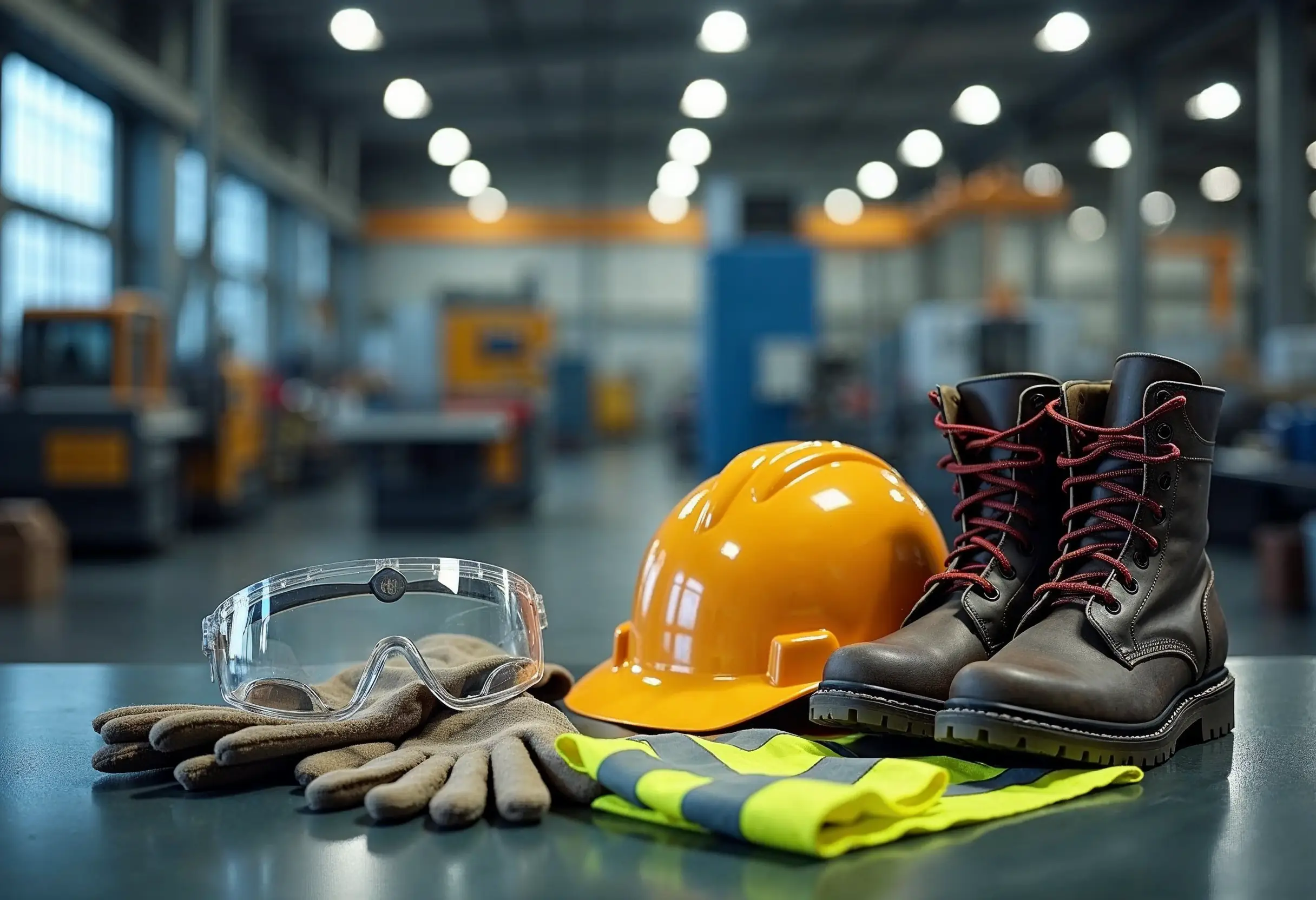
Crushing, entanglement, and cutting injuries from moving machinery parts are among the most severe workplace accidents. Machine safety rules aren’t just paperwork—they’re the first line of defense.
The OSHA machine guarding standard (OSHA 1910.212) mandates proper guarding to protect operators from point of operation hazards, ingoing nip points, and rotating parts. But installing guards isn’t enough. Machinery needs comprehensive safety measures, including proper anchoring, regular inspections, and employee training.
Understanding OSHA PPE standards (OSHA 1910.132) ensures correct personal protective equipment (PPE) use. Whether setting up new equipment or upgrading safety protocols, implementing machine safeguarding requirements is crucial for workforce protection and regulatory compliance.
Understanding Machine Safety Basics
Machine safety begins with a thorough understanding of potential hazards and essential protective equipment. OSHA standards mandate that any machine part, function, or process capable of causing injury must be properly safeguarded, as outlined in the OSHA machine guarding standard (OSHA 1910.212).
Key machine hazards to address
Moving machinery components present several critical hazards that demand immediate attention. These include crushing between moving parts, entanglement in rotating components, and severe cuts from sharp edges. Additionally, mechanical hazards arise from point of operation, ingoing nip points, and flying chips or sparks.
Electrical hazards pose equally serious risks, particularly during maintenance operations. Furthermore, hydraulic and pneumatic systems store significant force that, when released unexpectedly, can lead to catastrophic outcomes. Recognizing these danger zones is essential for effective hazard recognition and assessment.
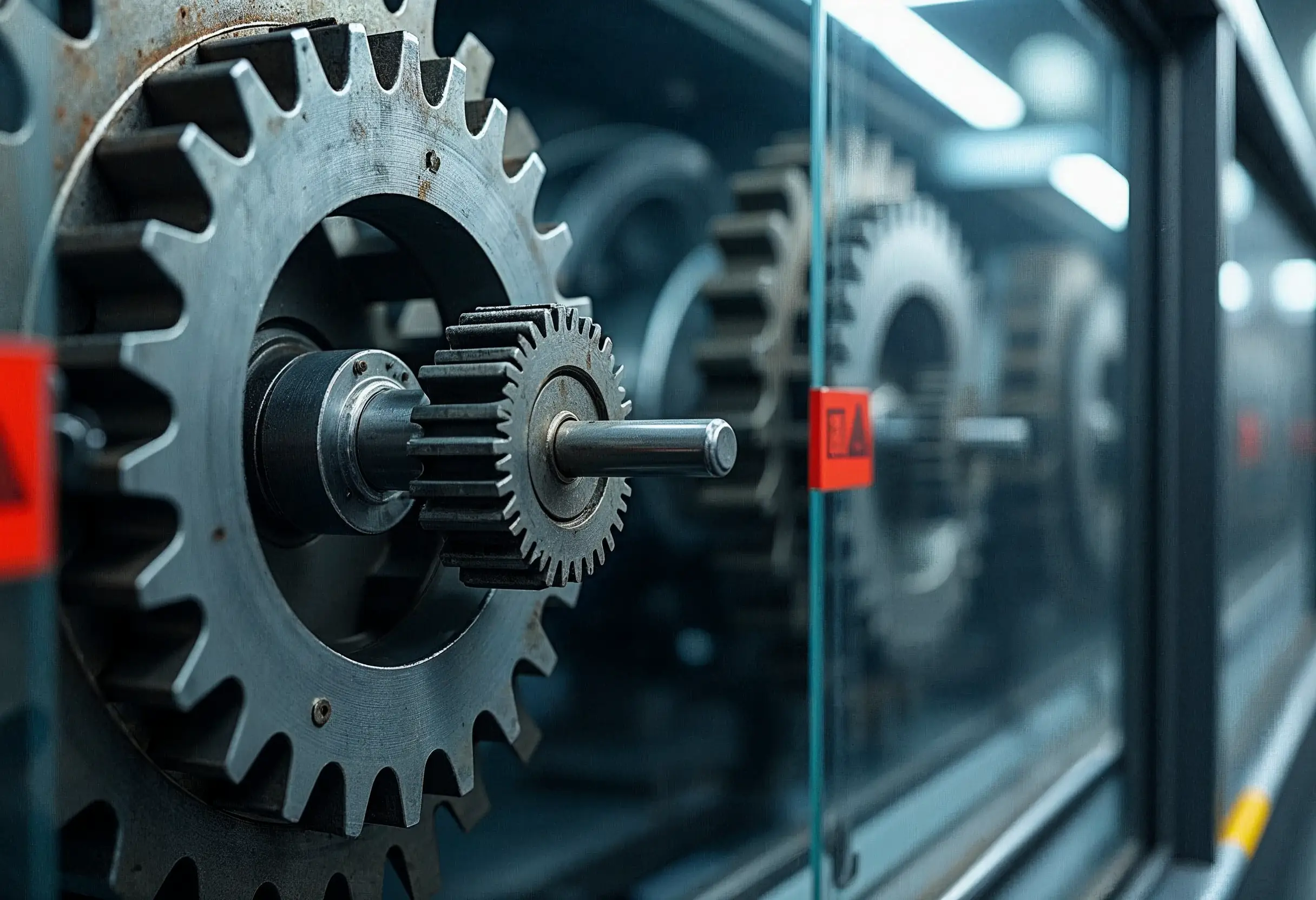
Essential safety components
To mitigate these risks effectively, specific safety devices must be incorporated into machinery systems. According to the Machinery Directive, essential safety components include:
- Protective devices for operator detection
- Power interlock guards
- Logic units ensuring safety functions
- Emergency stop devices
- Two-hand control devices
Safety interlocks play a vital role, featuring direct opening action and forcibly guided mechanisms as required by standards. These switches prevent workers from entering hazardous areas by detecting whether fences or doors remain closed.
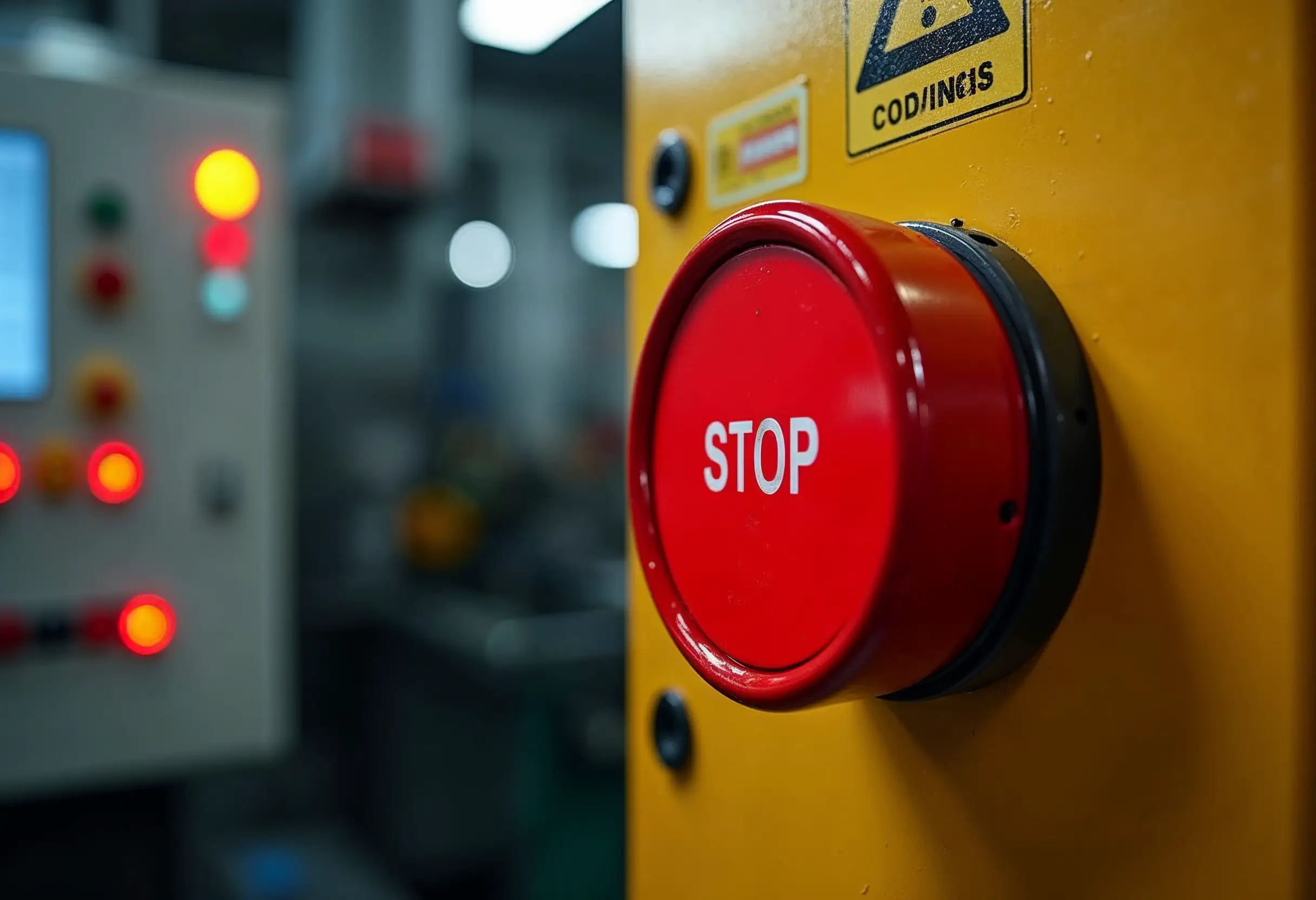
Current safety standards overview
The ANSI B11 standards serve as the cornerstone of machine safety standards, comprising nearly three dozen documents addressing machine tool safety requirements for both manufacturers and users. These standards specify requirements for:
- Risk assessment processes
- General machinery requirements
- Specific machine types (including mechanical power presses and abrasive wheel machinery)
- Safeguarding design and construction
OSHA's machine guarding regulations span multiple industries, including general industry (29 CFR 1910), maritime (29 CFR 1915, 1917, 1918), construction (29 CFR 1926), and agriculture (29 CFR 1928). Notably, OSHA standard 1910.212 outlines general requirements for all machines, ensuring comprehensive protection against mechanical hazards.
Minimize workplace risks and stay compliant with OSHA standards by equipping your facility with high-quality safety components. From machine guards to emergency stop devices, MCH Parts provides the essential solutions to protect your workforce. Get a custom quote today.
Selecting the Right Safety Equipment
Proper selection of safety equipment stands as the cornerstone of an effective machine guarding program. Before implementing any safeguards, a systematic approach ensures optimal protection for operators and machinery alike.
Risk assessment process
The first step involves conducting a thorough machine hazard assessment that aligns with ANSI/ISO 12100:2012 standards. This assessment encompasses:
- Determining machinery limits across all lifecycle phases
- Identifying potential hazards and hazardous situations
- Estimating risks based on severity of harm and probability of occurrence
A diverse team of experts, specifically operators, mechanics, and safety professionals, must collaborate to recognize all possible hazards. Moreover, the assessment should incorporate every task involving machinery operations, maintenance, and sanitation.
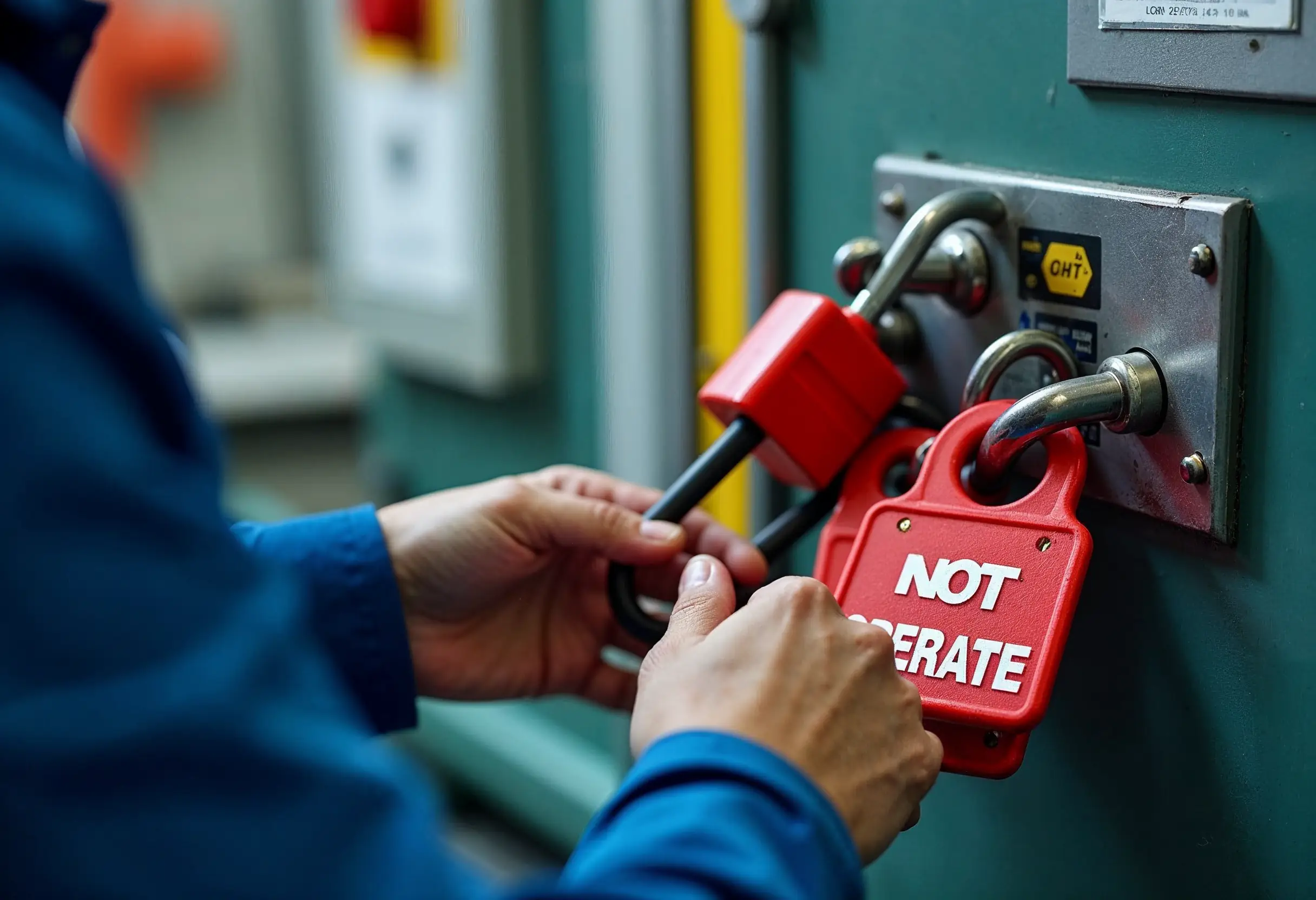
Matching guards to machine types
Once risks are identified, selecting appropriate types of machine guards becomes crucial. Fixed guards serve as permanent machine components, offering maximum protection while requiring minimal maintenance. Alternatively, interlocked guards automatically shut off power upon opening or removal, making them ideal for machines requiring frequent access.
For operations involving varying stock sizes, adjustable guards provide necessary flexibility. Meanwhile, self-adjusting guards automatically adapt their openings based on stock movement, offering continuous protection without compromising operational efficiency.
Consider these essential criteria for machine guards while selecting:
- Prevention of contact with hazardous areas
- Secure attachment to prevent tampering
- Protection against falling objects
- Accessibility for safe lubrication
- Non-interference with machine operation
The selection process must also account for environmental factors such as dust exposure, washdown requirements, and temperature variations. Furthermore, special consideration should be given to machines requiring frequent changeovers, as traditional hard guarding might not be the optimal solution in such cases.
Is your machinery meeting the latest safety regulations? Our team at MCH Parts helps you identify risks, select the right safety equipment, and implement industry-best practices. Request a free consultation and keep your operations safe.
Installing Machine Guards Correctly
Successful machine guard installation requires meticulous attention to detail and adherence to safety protocols. A systematic approach ensures optimal protection for operators while maintaining operational efficiency.
Pre-installation checklist
Prior to mounting any safeguards, verify these essential requirements:
- Compatibility assessment of guards with machine specifications
- Clear, stable work surface suitable for securing the system
- Availability of qualified personnel for installation
- Proper tools and mounting hardware
- Disconnection of power sources
Step-by-step mounting guide
The mounting process demands precision and careful execution. First, secure the guard's base plate to the machine using appropriate fasteners. Subsequently, align mounting holes precisely with the machine's bolt pattern to ensure stability.
For fixed guards, use fasteners that require tools for removal, making them tamper-resistant. Position interlocked guards strategically, ensuring automatic shutdown mechanisms function properly upon guard removal.
Throughout installation, maintain these critical parameters:
- Proper clearance between guards and hazard points
- Secure attachment points that prevent guard movement
- Unobstructed access to machine controls
- Clear visibility of work areas
Testing and verification
After installation, thorough testing validates guard effectiveness. Begin by examining all mounting points and connections. Next, verify that:
- Guards prevent contact with dangerous moving parts
- No objects can fall into machinery
- Lubrication points remain accessible
- Emergency stops function correctly
- Interlocking mechanisms operate as designed
Document all verification procedures, maintaining detailed records of installations, modifications, and initial testing results. Conduct operational tests under normal working conditions to ensure guards don't interfere with machine functionality.
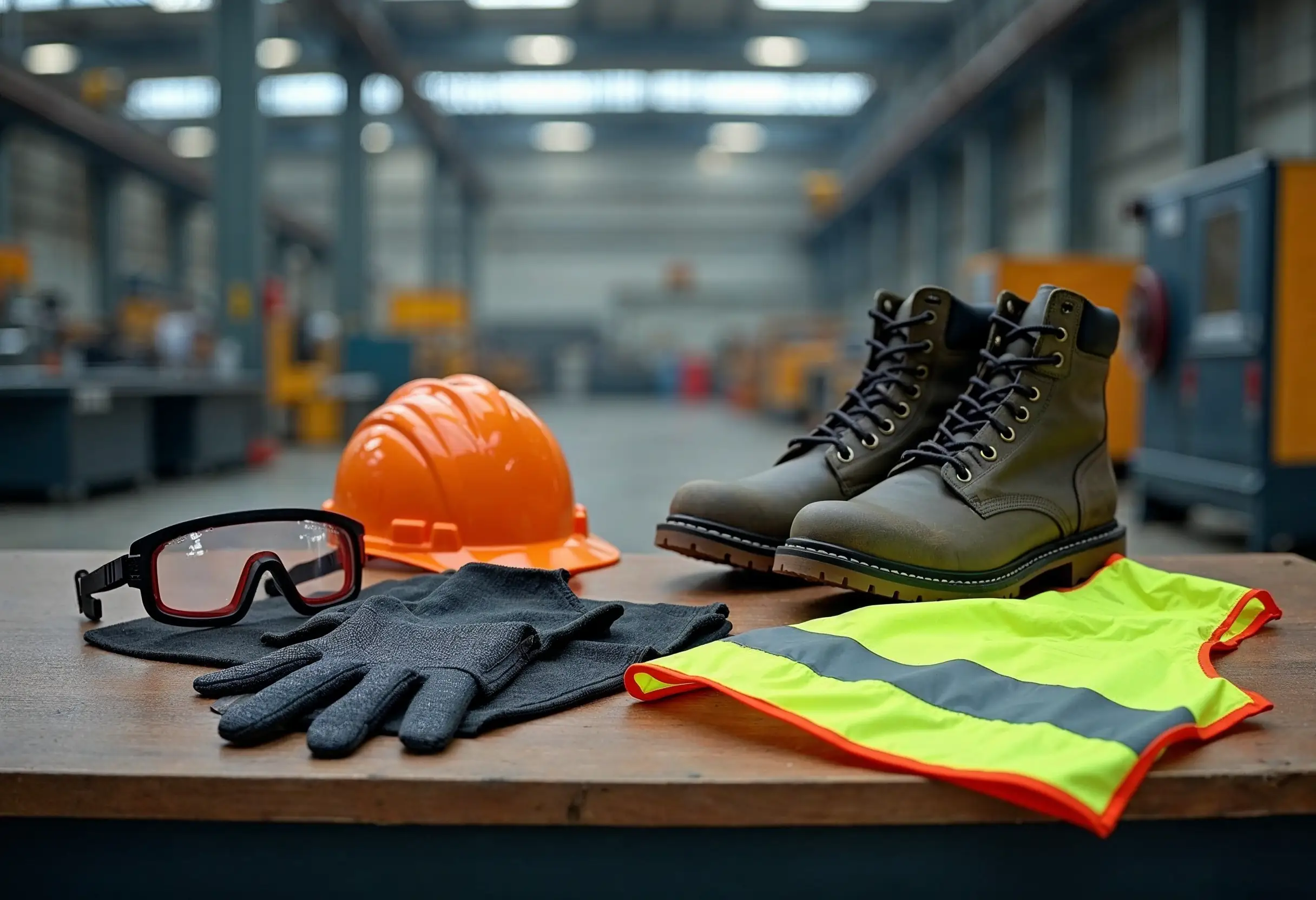
Maintaining Safety Systems
Regular maintenance forms the backbone of effective machine safety systems. A well-structured maintenance program ensures equipment operates safely while extending its operational lifespan.
Regular inspection schedule
Establishing a systematic inspection routine proves vital for maintaining machine safety standards. OSHA mandates periodic inspections of each energy control procedure at least annually. These inspections must verify that:
- Energy control procedures remain properly implemented
- Employees understand their responsibilities
- Protection measures stay effective throughout operations
For critical equipment operating in harsh conditions, daily or weekly monitoring becomes essential. Nonetheless, inspection frequencies should adapt based on:
- Equipment criticality and operational impact
- Current machine condition
- Operating environment characteristics
- Known or diagnosed problems
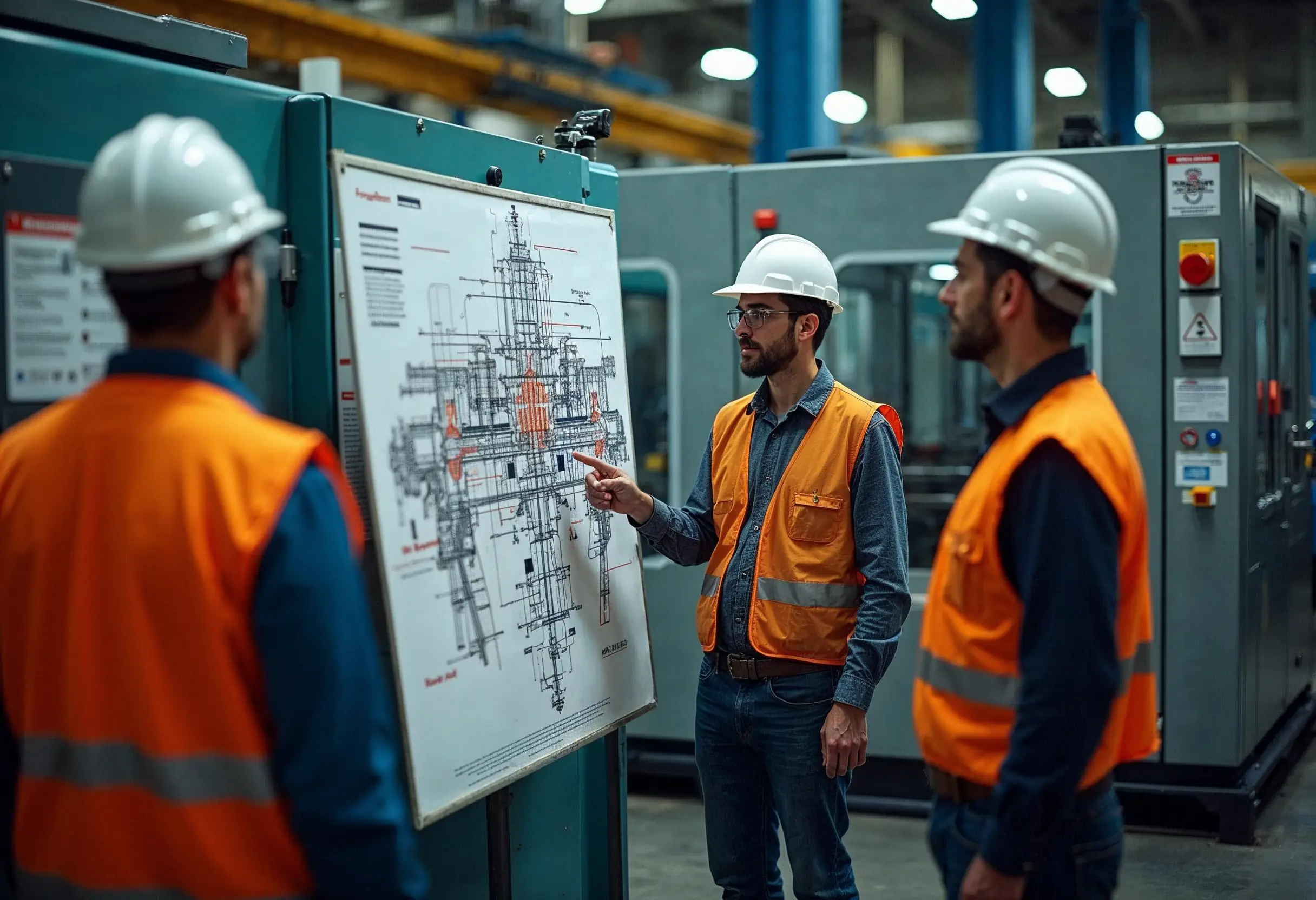
Common maintenance tasks
Maintenance procedures significantly contribute to both operator and maintenance crew safety. Essential maintenance tasks encompass:
- Examining guards for secure attachment and proper functioning
- Verifying emergency stop mechanisms
- Checking interlocking devices
- Inspecting power transmission apparatus
- Testing safety switches and controls
Before performing maintenance, follow these crucial steps:
- Notify affected employees about equipment shutdown
- Stop the machine completely
- Isolate equipment from energy sources
- Apply lockout/tagout devices
- Release stored energy
- Verify complete isolation
Upon maintenance completion, conduct thorough equipment inspection, ensuring all guards return to their proper positions. Furthermore, maintenance personnel must receive comprehensive training on specific machines, understanding which equipment requires shutdown versus those permitting service while running.
Proper documentation remains crucial throughout the maintenance process. Maintain detailed records of:
- Inspection findings
- Completed maintenance tasks
- Equipment modifications
- Testing results
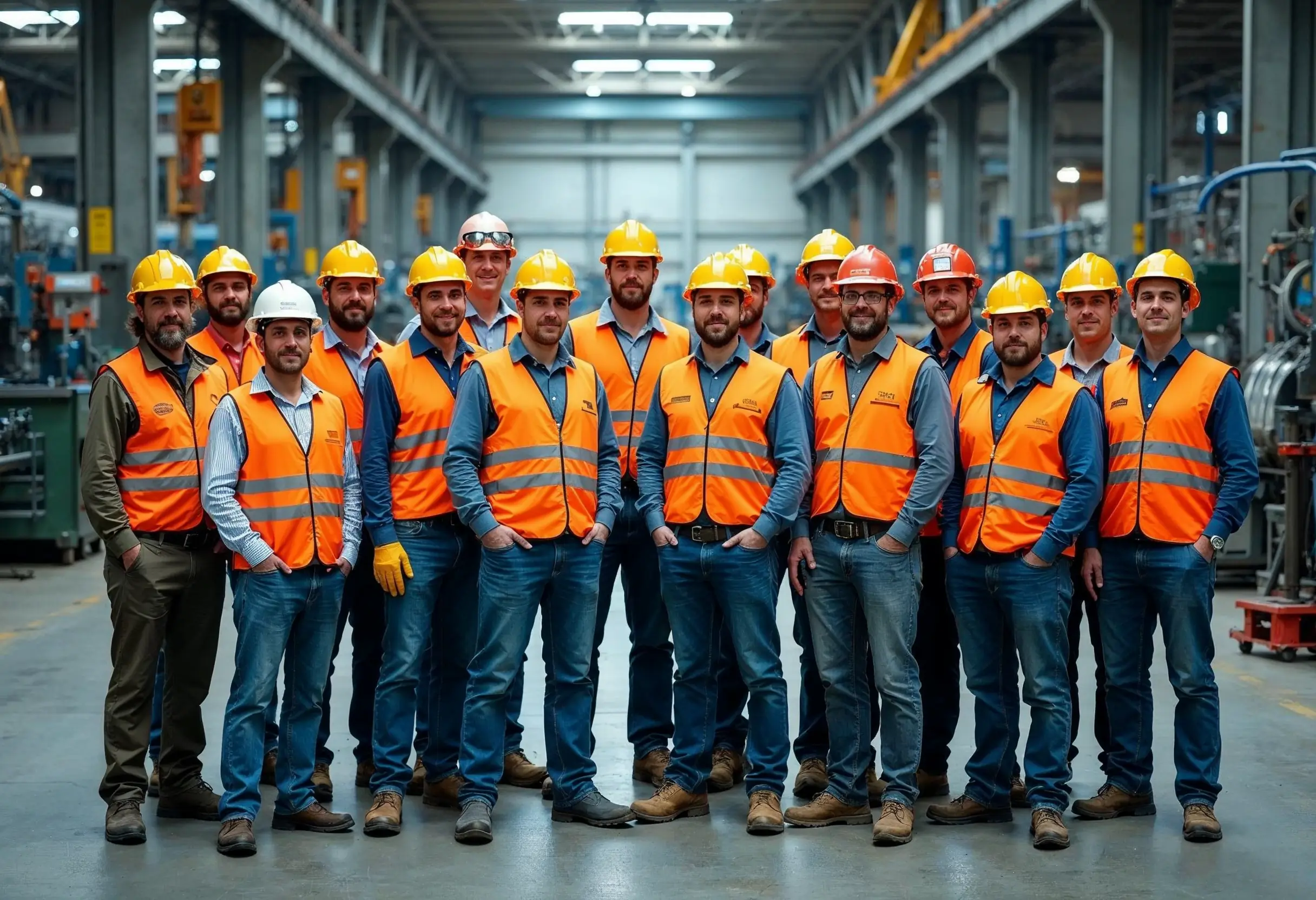
Conclusion
Machine safety rules serve as essential safeguards against workplace accidents, protecting both workers and equipment from serious harm. Following proper safety protocols - from initial risk assessment through regular maintenance - creates a secure working environment that meets regulatory requirements.
Success depends on selecting appropriate safety components, installing them correctly, and maintaining them diligently. Each step builds upon the previous one, creating layers of protection that shield operators from crushing, entanglement, and other mechanical hazards.
Remember that safety measures must evolve with your machinery and operational needs. Workplace safety isn’t just about compliance—it’s about efficiency. Prevent costly accidents, extend equipment lifespan, and maintain peak performance with our premium safety solutions. Explore our products and find the right fit for your facility.
Ultimately, effective machine safety comes down to thorough planning, proper implementation, and consistent oversight. Make safety your top priority, and you'll create a workplace where both productivity and worker protection thrive together. Continuous improvement through regular safety audits and worker training for PPE use is essential for maintaining a safe work environment.
FAQs
Q1. What are the essential components of machine safety? Essential safety components include protective devices for operator detection, power interlock guards, logic units for safety functions, emergency stop devices, and two-hand control devices. Safety switches with direct opening action and forcibly guided mechanisms are also crucial for preventing access to hazardous areas. Point of operation guards and barrier guards are vital for protecting workers from the area of material processing on machines.
Q2. How often should machine safety inspections be conducted? OSHA mandates that each energy control procedure should be inspected at least annually. However, for critical equipment operating in harsh conditions, daily or weekly monitoring may be necessary. The frequency of inspections should be adjusted based on equipment criticality, current condition, operating environment, and known issues. Regular safety audits contribute to continuous improvement in workplace safety.
Q3. What steps should be taken before performing machine maintenance? Before maintenance, it's crucial to notify affected employees, stop the machine completely, isolate it from energy sources, apply lockout/tagout devices, release stored energy, and verify complete isolation. This ensures the safety of both operators and maintenance personnel. Following the OSHA guarding distance chart is essential when re-installing guards after maintenance.
Q4. Why is a risk assessment important when selecting safety equipment? A risk assessment is crucial because it helps identify potential hazards and hazardous situations, estimate risks based on severity and probability, and determine appropriate safety measures. This process ensures that the selected safety equipment effectively addresses the specific risks associated with each machine, including woodworking machinery and mechanical power presses.
Q5. What should be considered when installing machine guards? When installing machine guards, consider factors such as proper clearance between guards and hazard points, secure attachment to prevent movement, unobstructed access to machine controls, and clear visibility of work areas. It's also important to ensure that guards don't interfere with machine functionality and are tamper-resistant where necessary. Additional safety devices like safety mats and safety light curtains may be necessary depending on the specific machine and its operation.
Read More
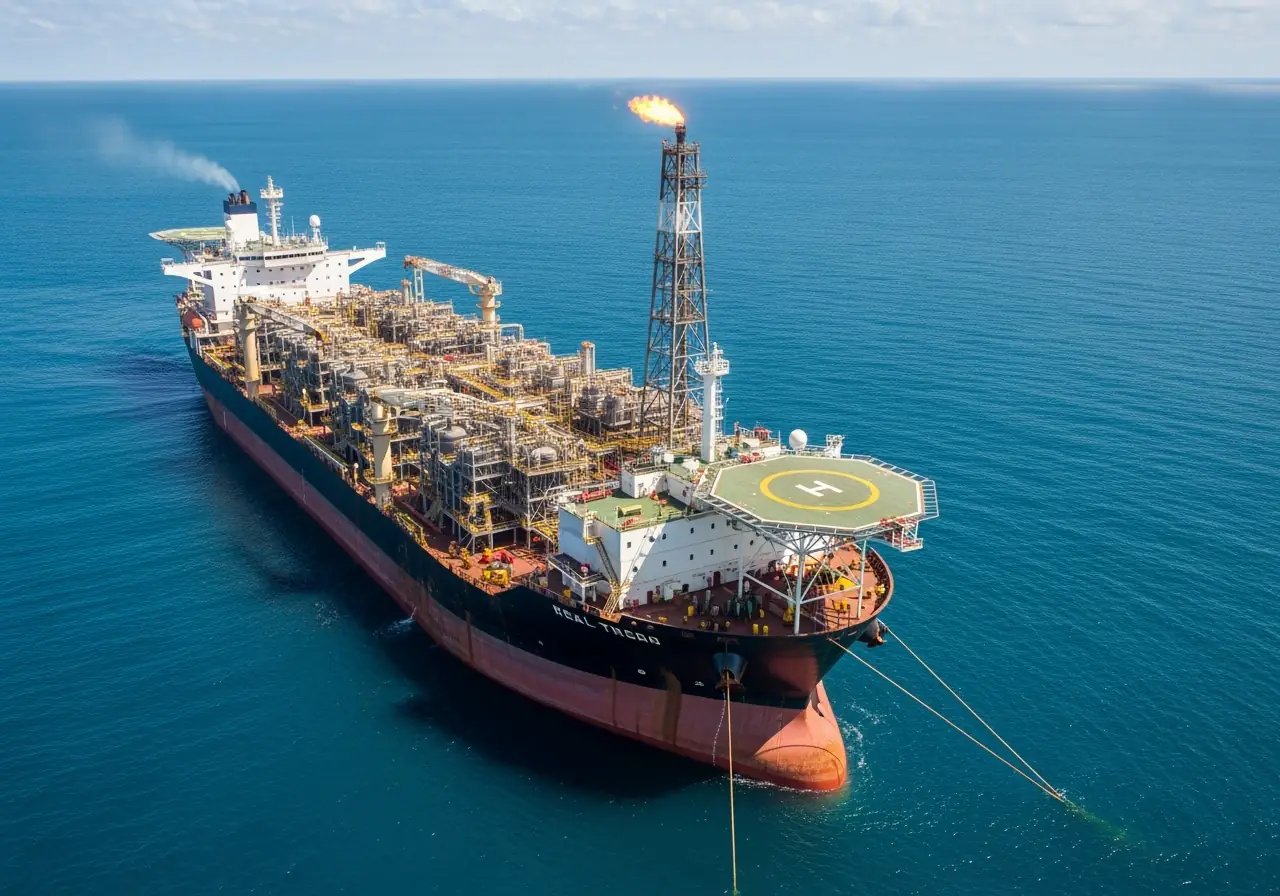
How FPSO Inspection Prevents Million-Dollar Shutdown Losses
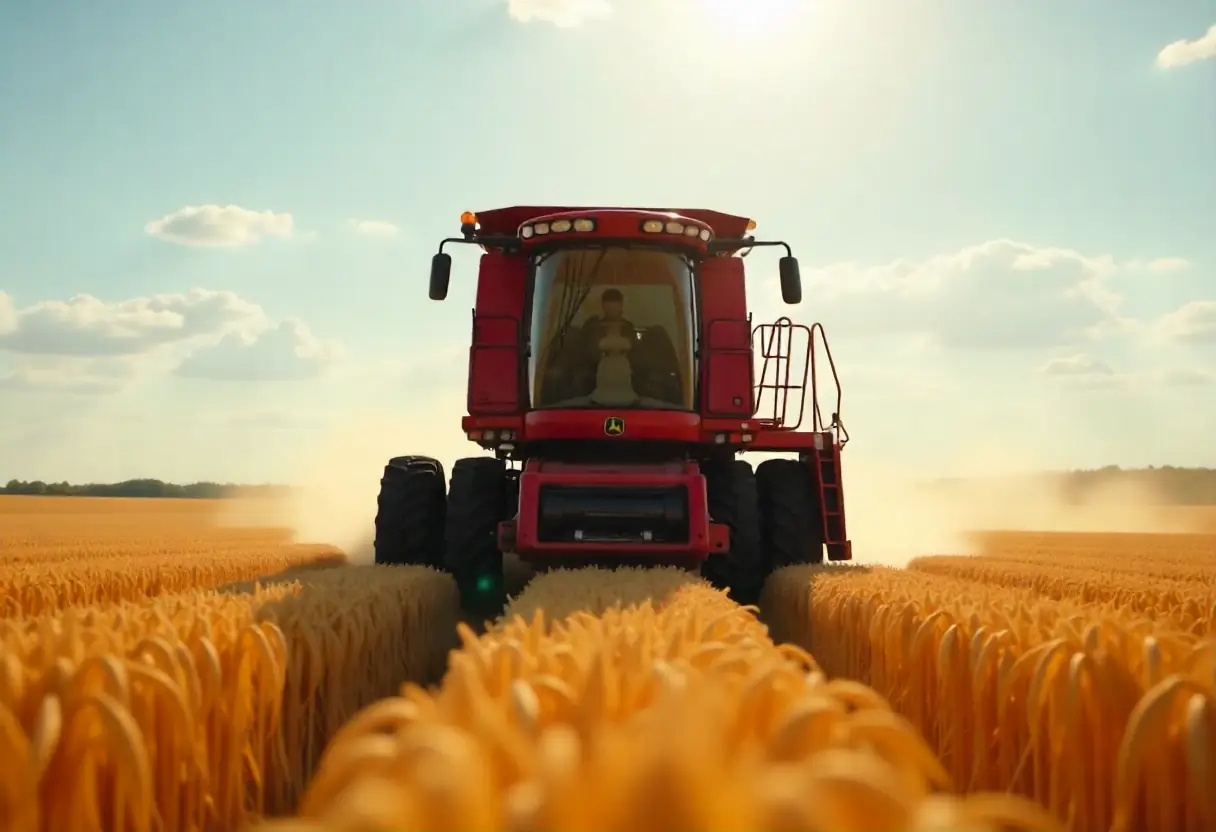
Fix It Before It Breaks: A Farmer's Guide to Combine and Harvester Maintenance
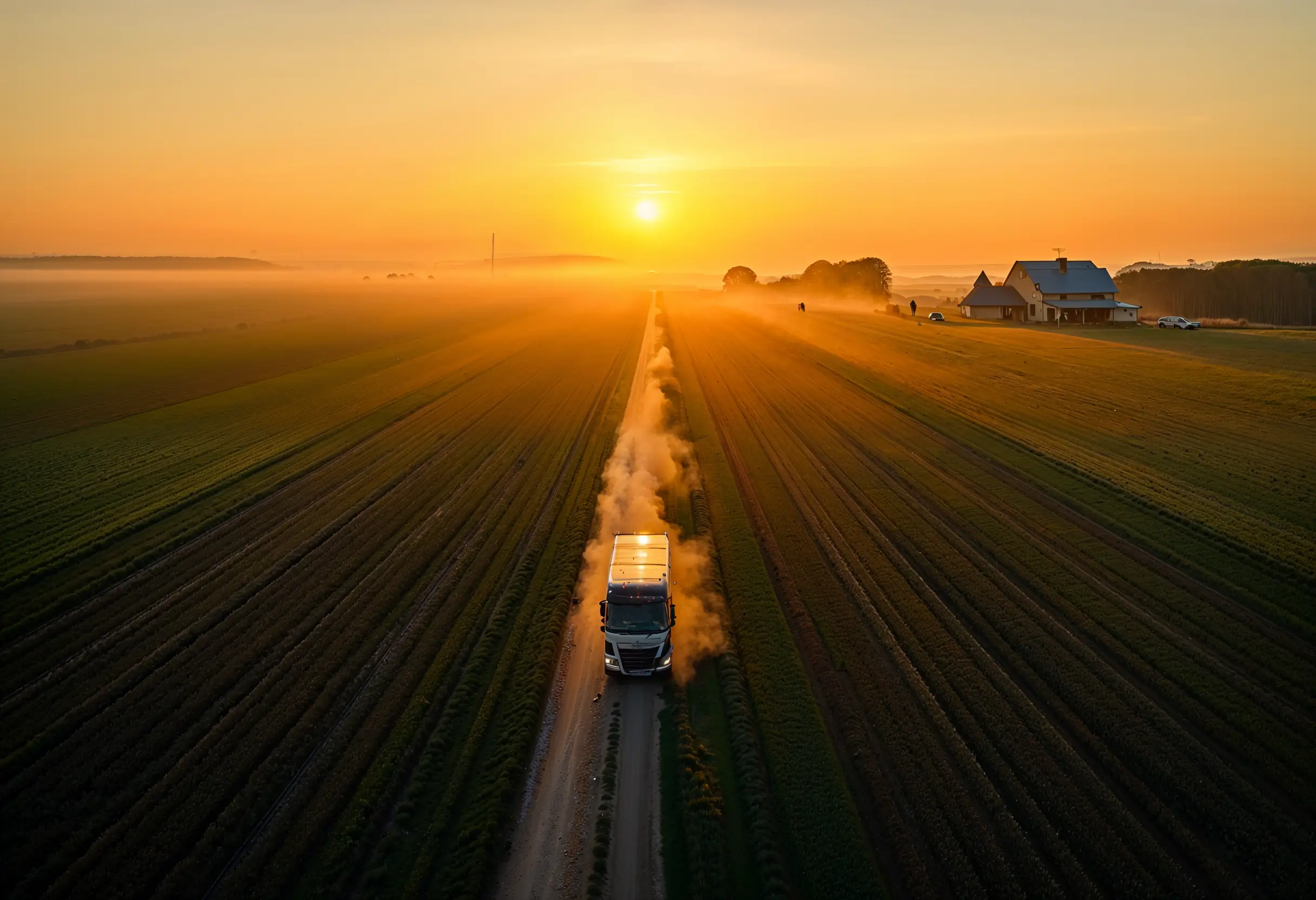
Why Fast Tractor Parts Delivery is Changing Modern Farming [2025 Guide]
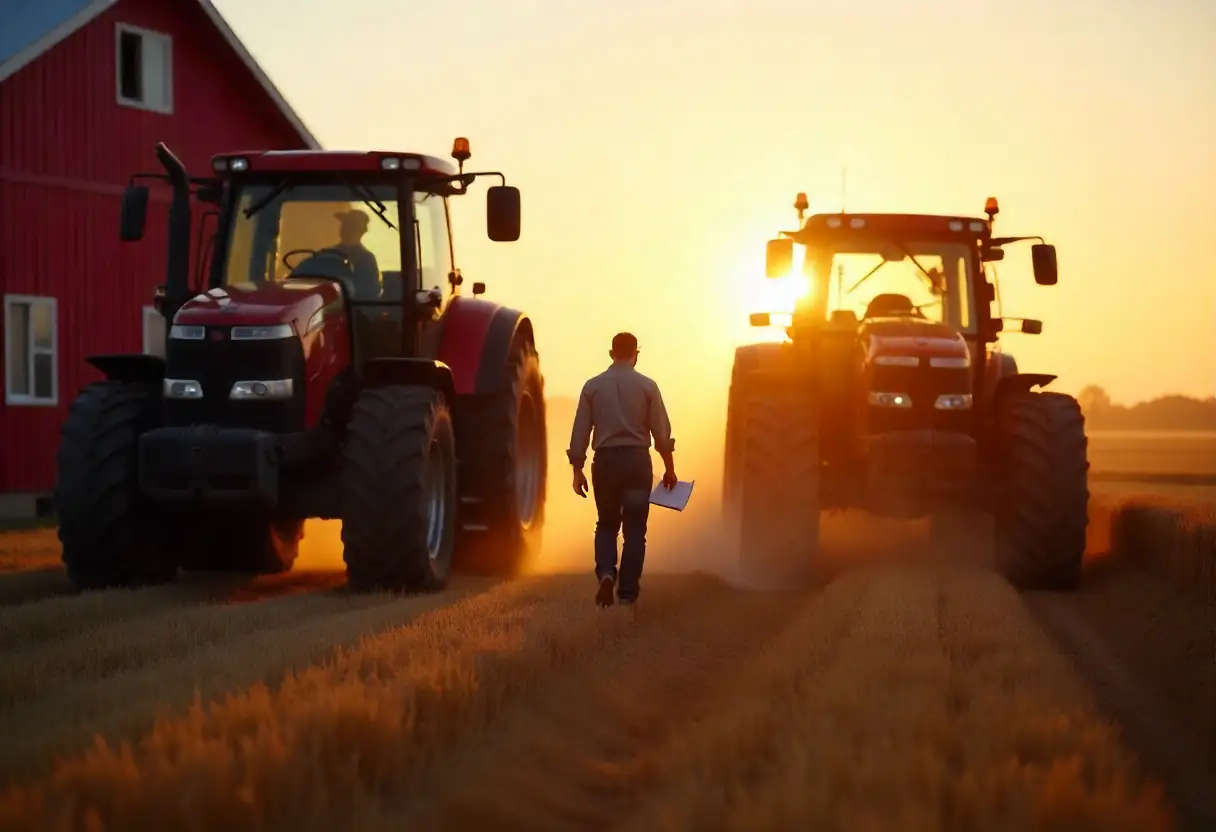
The Critical Farm Equipment Replacement Parts You Need Before Harvest 2025
.webp)
How to Double Your Farm Efficiency: Expert Guide to Smart Scaling
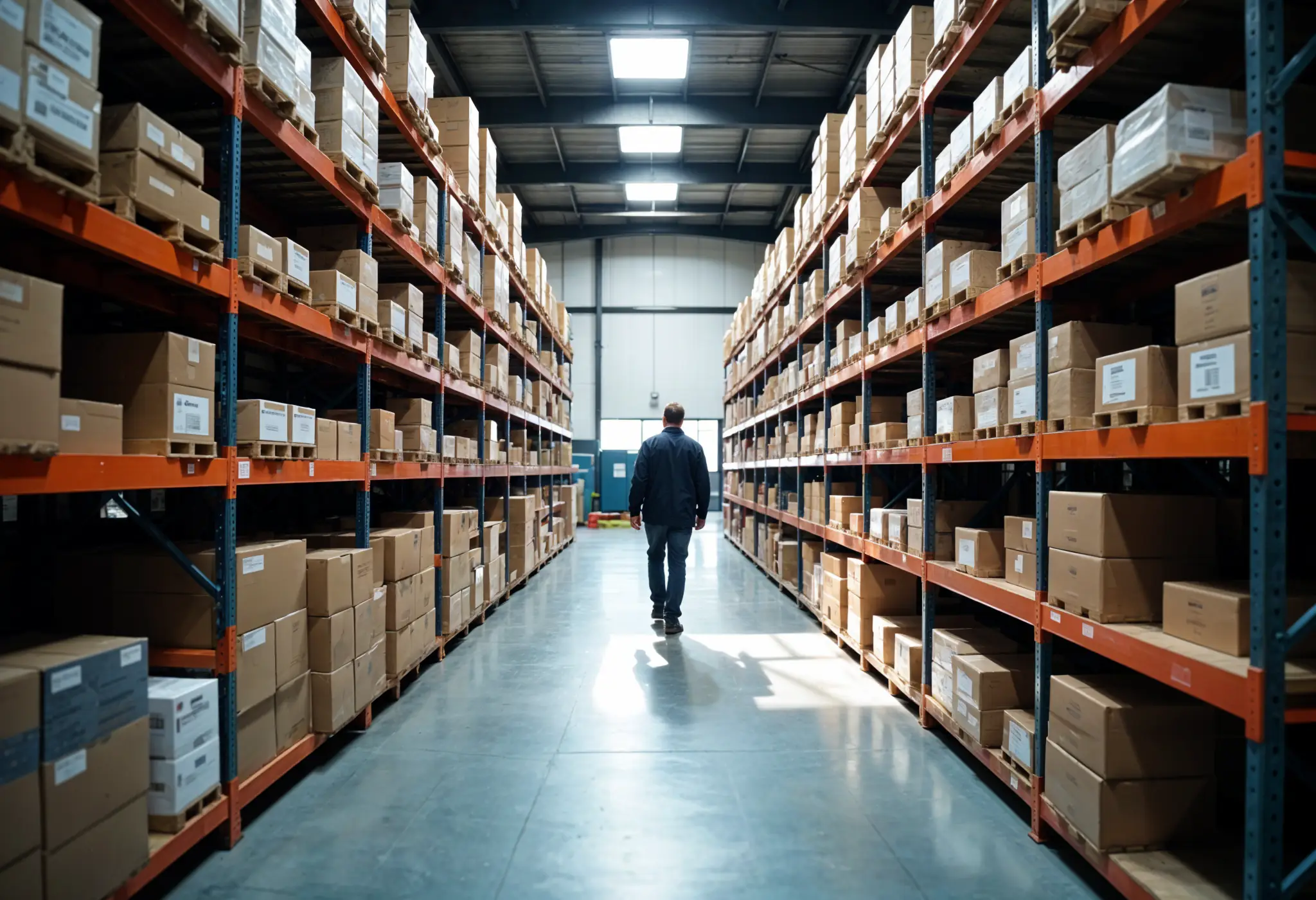
Cut Costs by 30%: Pre-Season Spare Parts Audit Checklist

Proven Success Factors for Agricultural Equipment Manufacturers in 2025
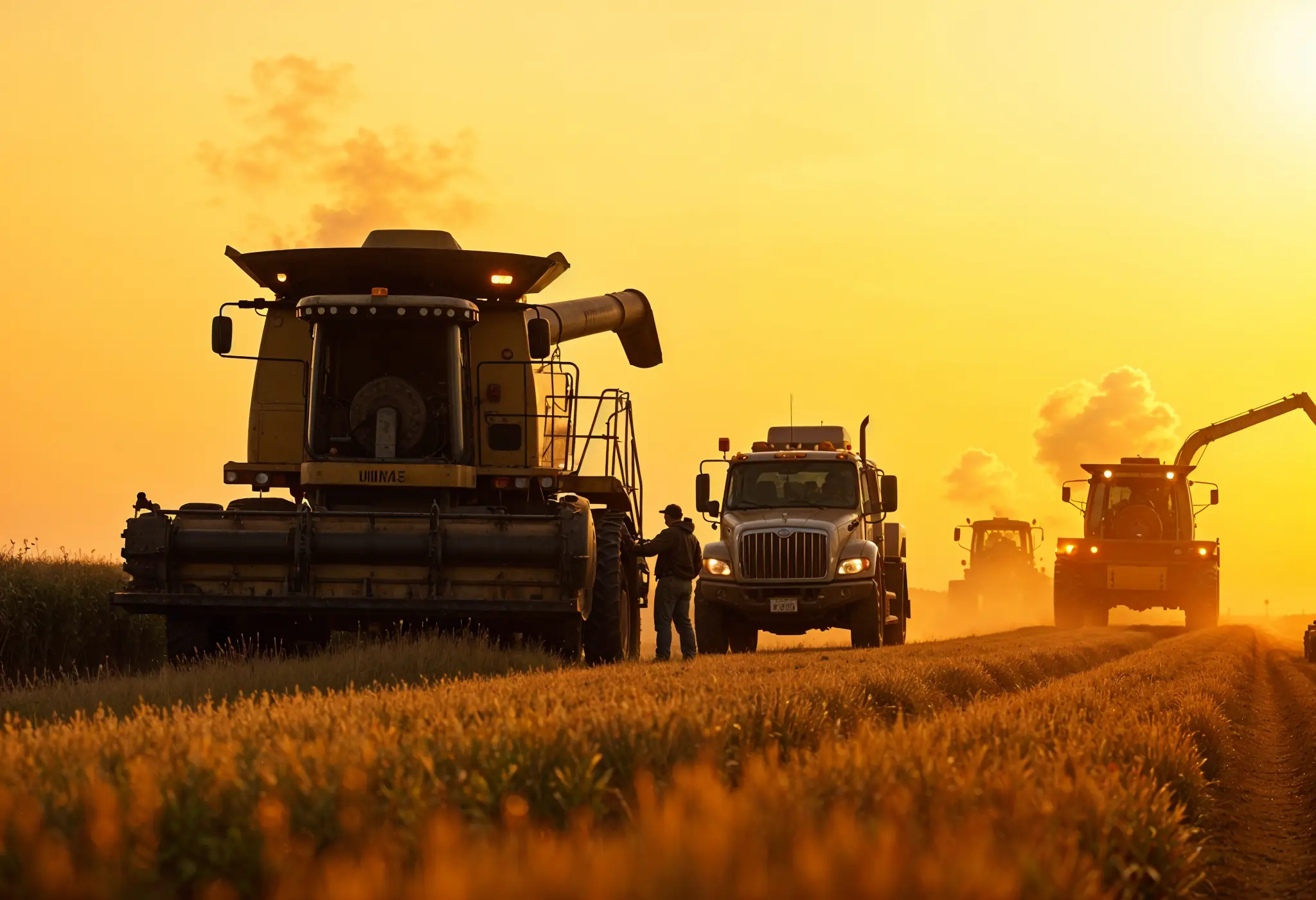
13 Overlooked Farm Spare Parts That Halt Operations — Pt. 2
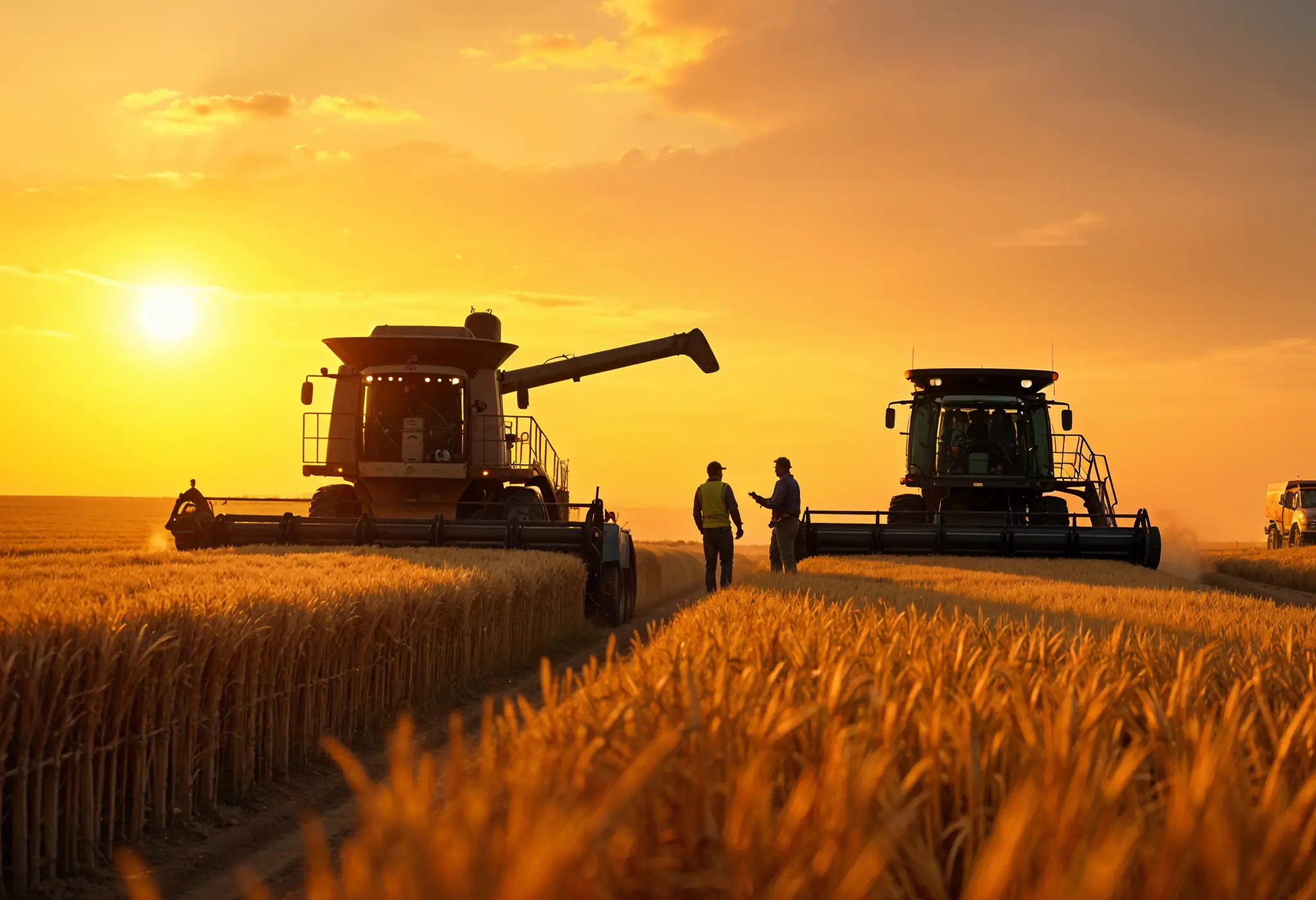
13 Overlooked Farm Spare Parts That Halt Operations — Pt. 1
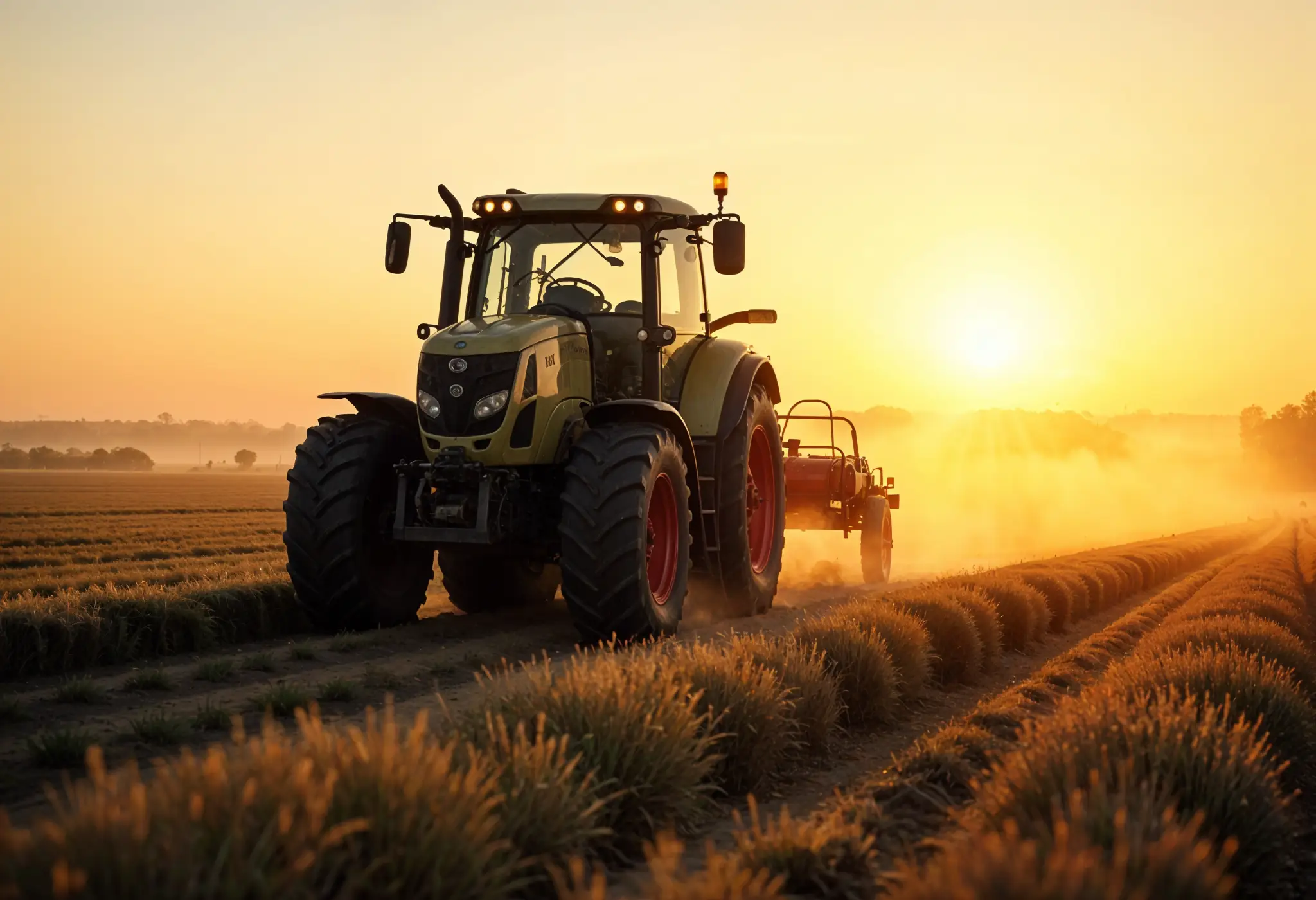
Top Hydraulic Components for Agricultural Equipment in 2025: Complete Guide
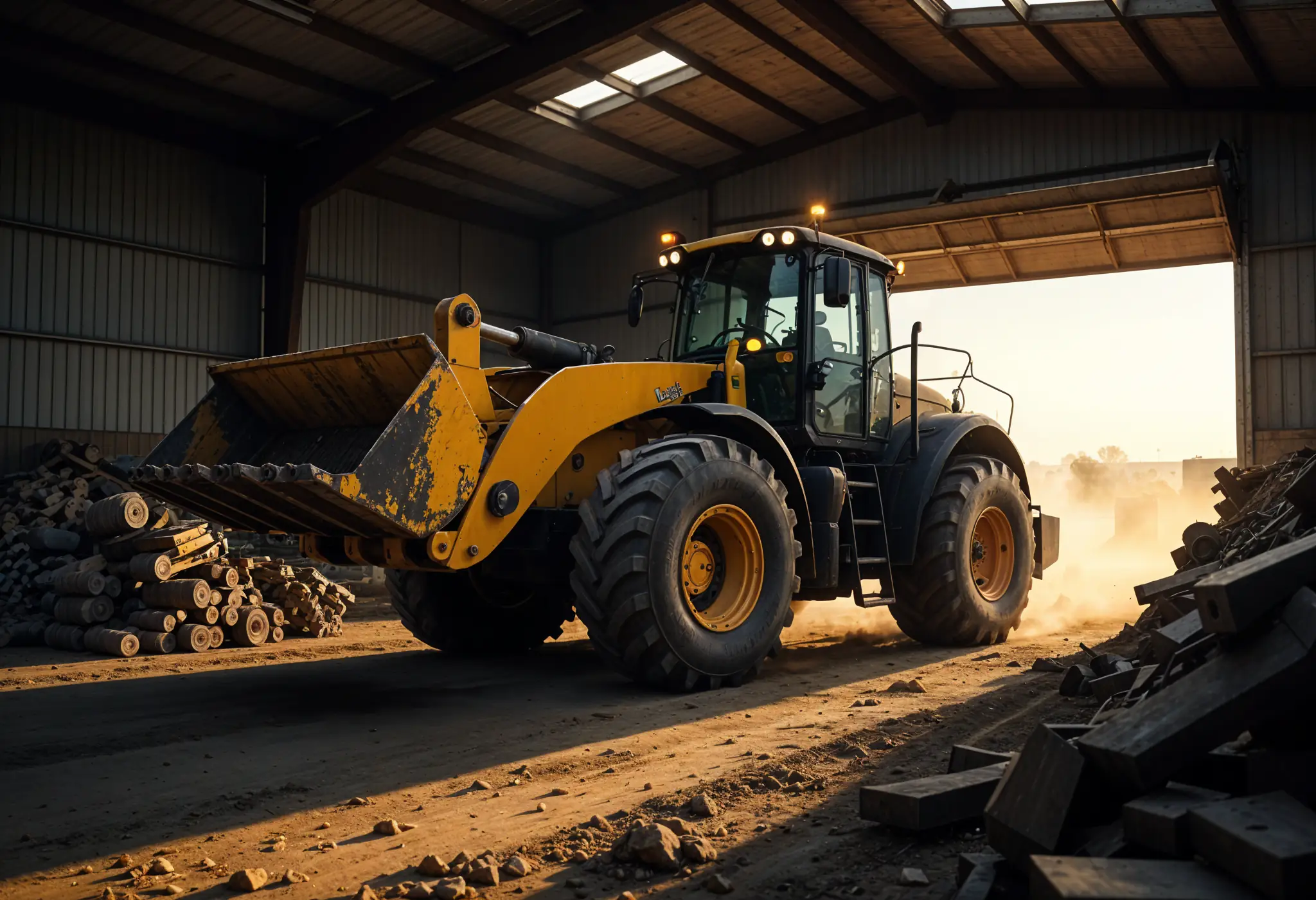
The Essential Farm Equipment Parts You Can't Afford to Run Out Of
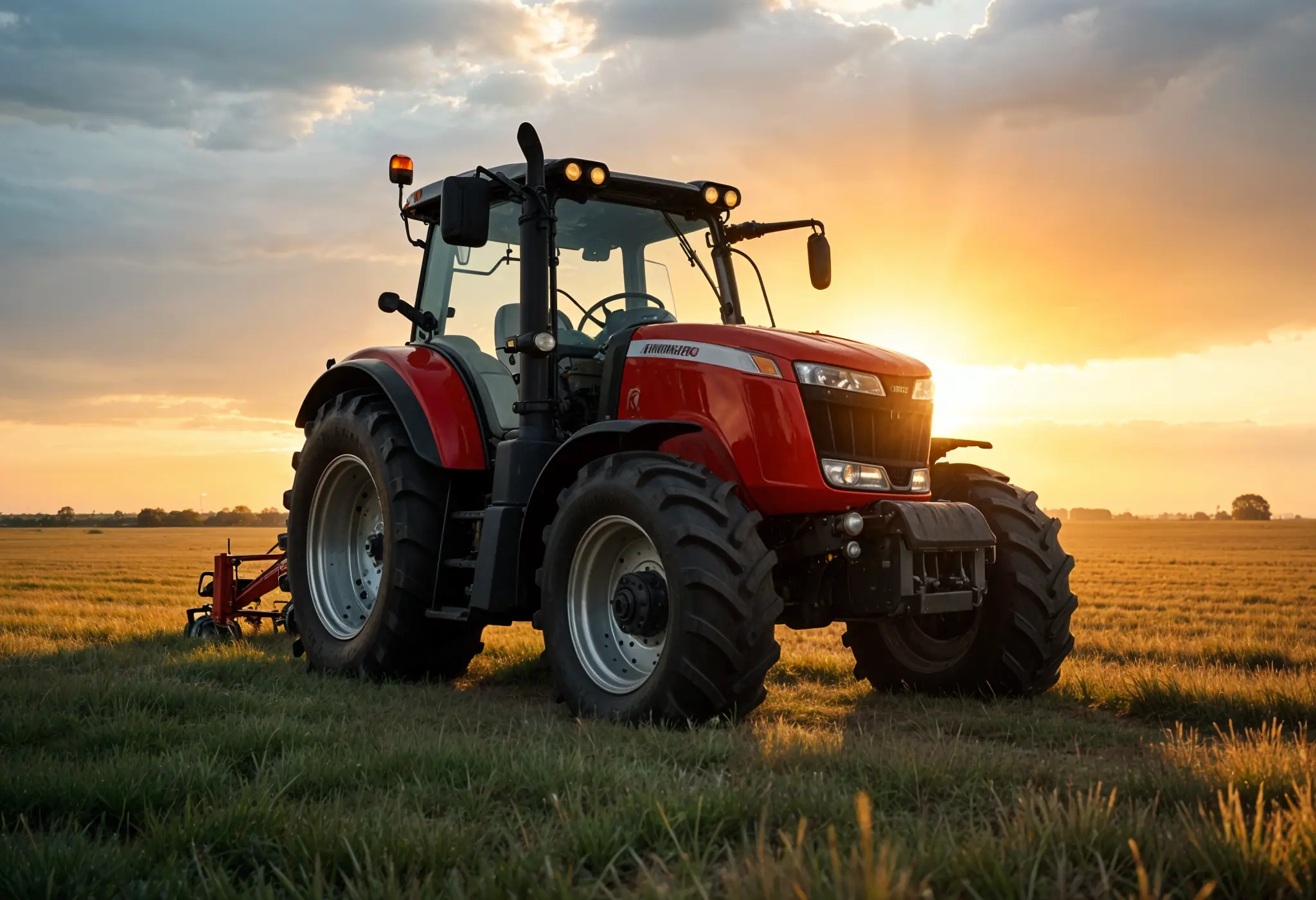
How to Service Farm Equipment: A Farmer's Guide to Zero Harvest Downtime
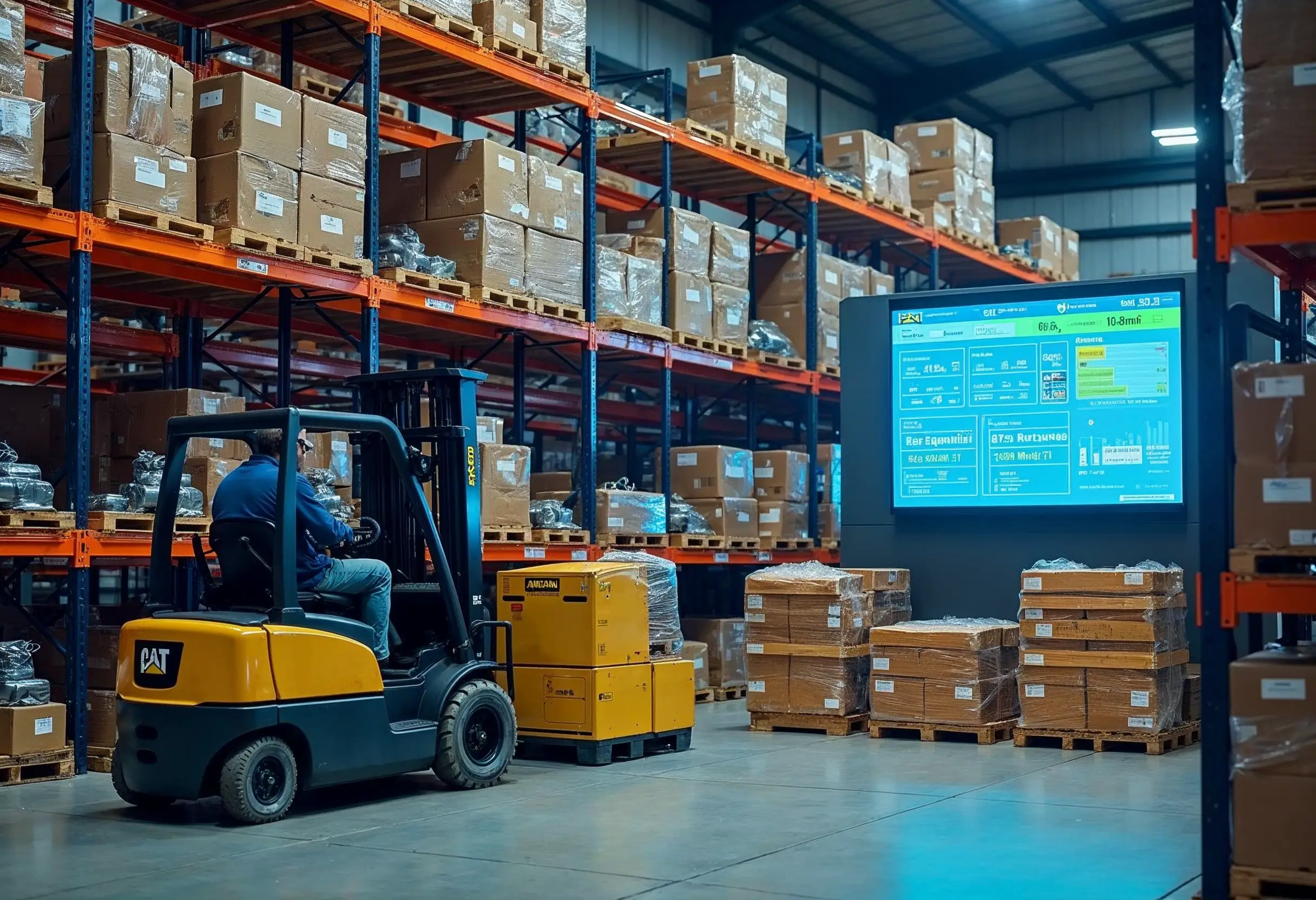
Construction Machinery Parts Suppliers: Expert Selection Guide
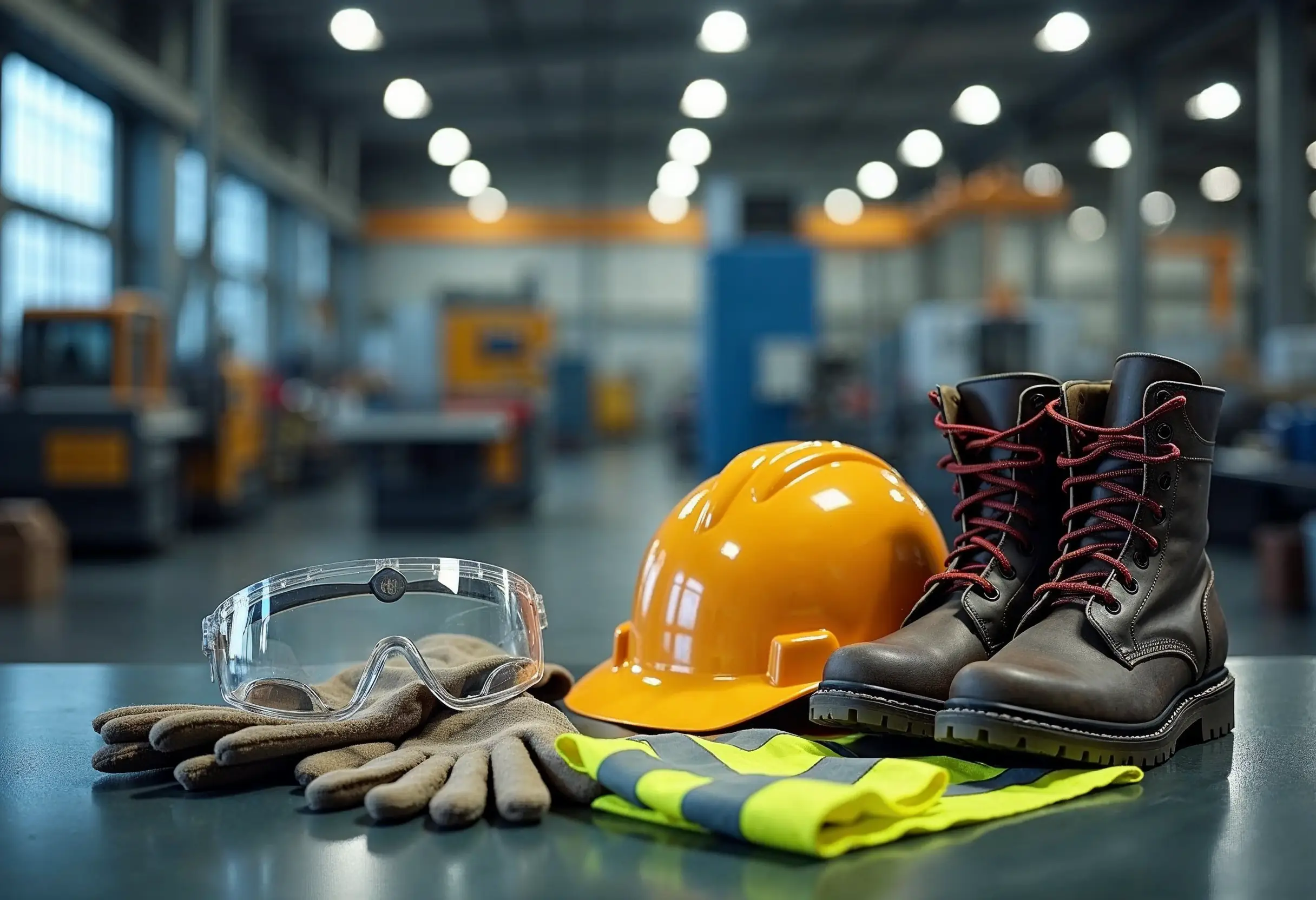
How to Apply Machine Safety Rules: From Selection to Installation
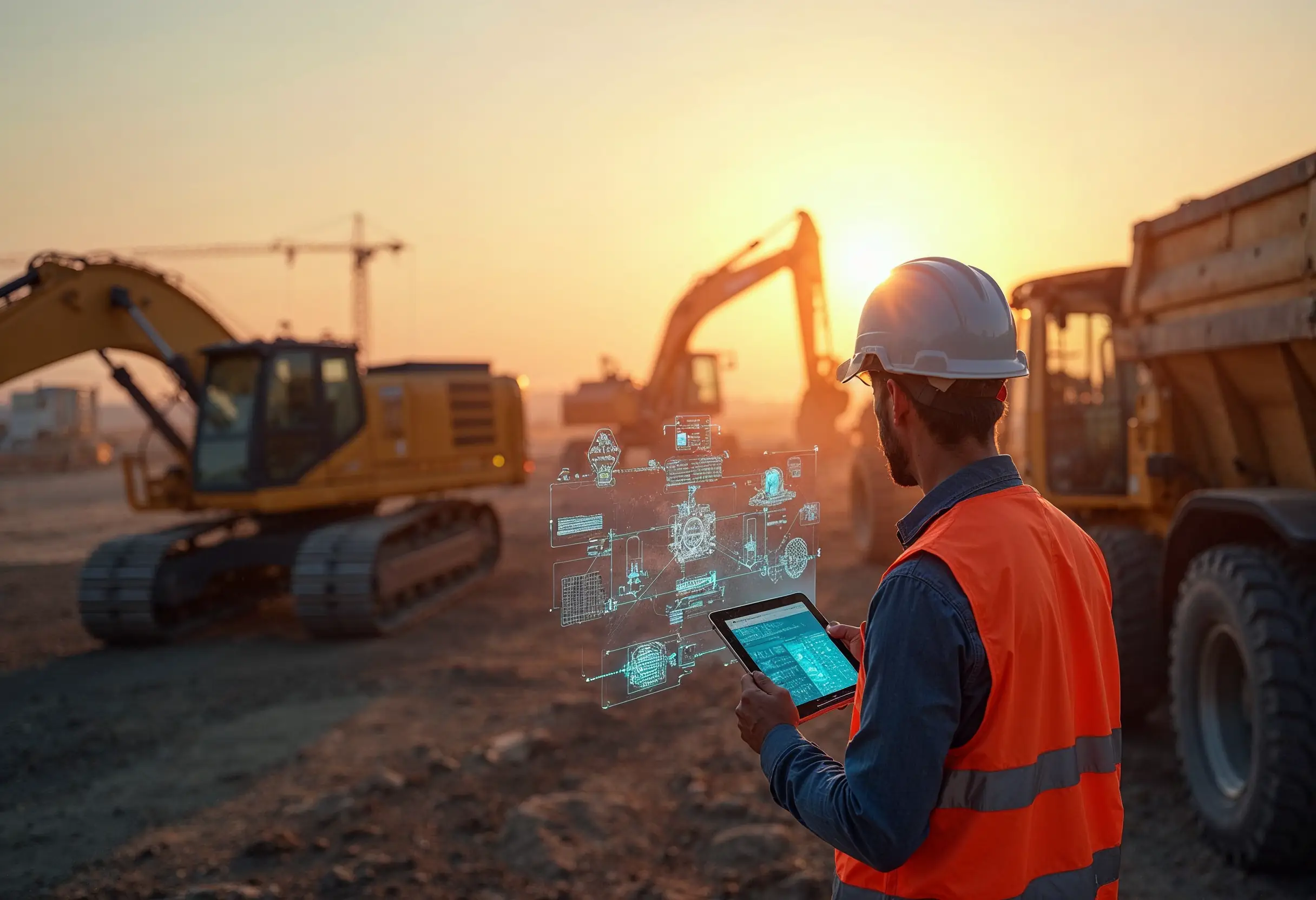
Smart Diagnostics Cut Heavy Equipment Failures by 73%
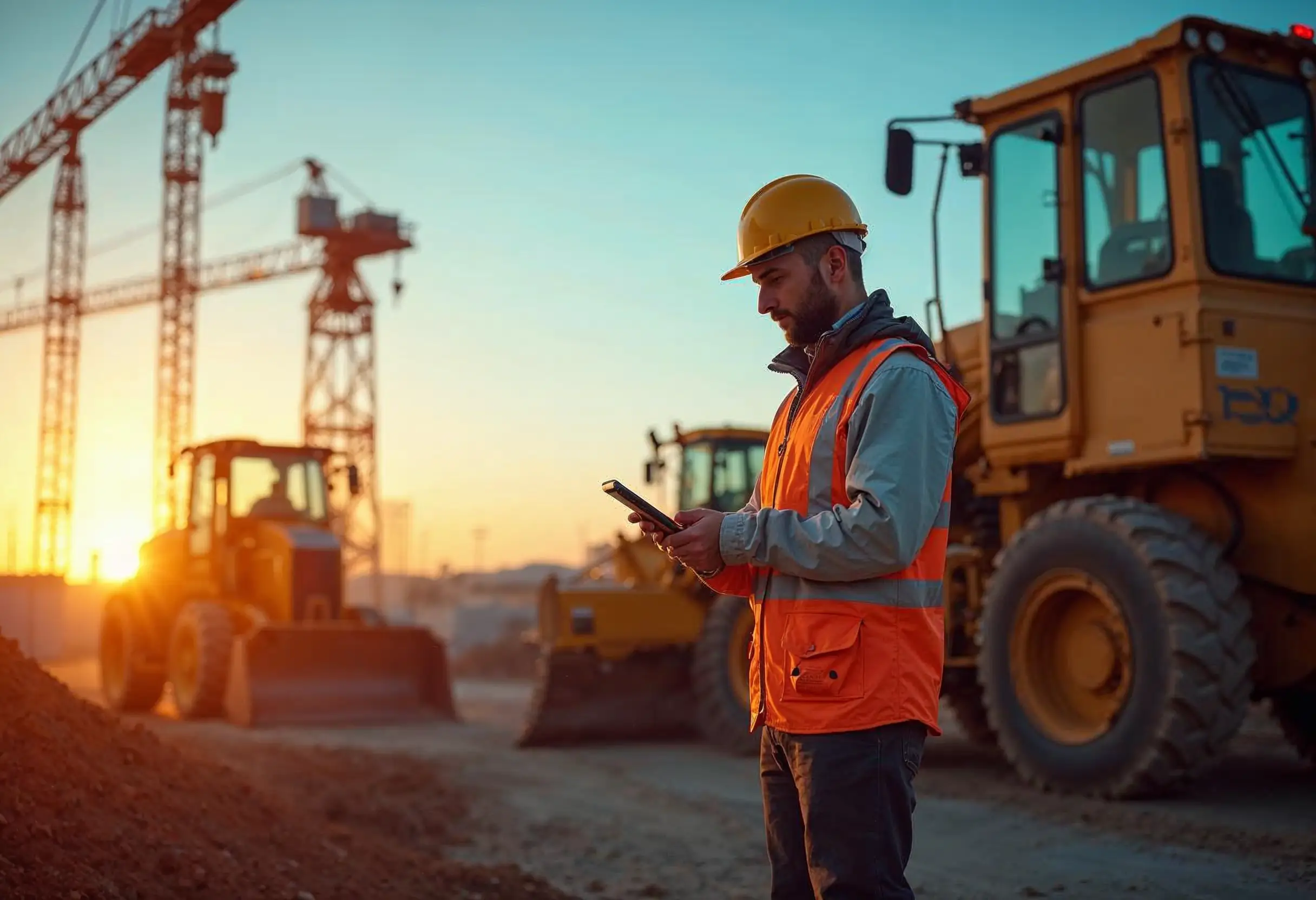
5 Ways to Assess the Environmental Impact of Heavy Construction Machinery
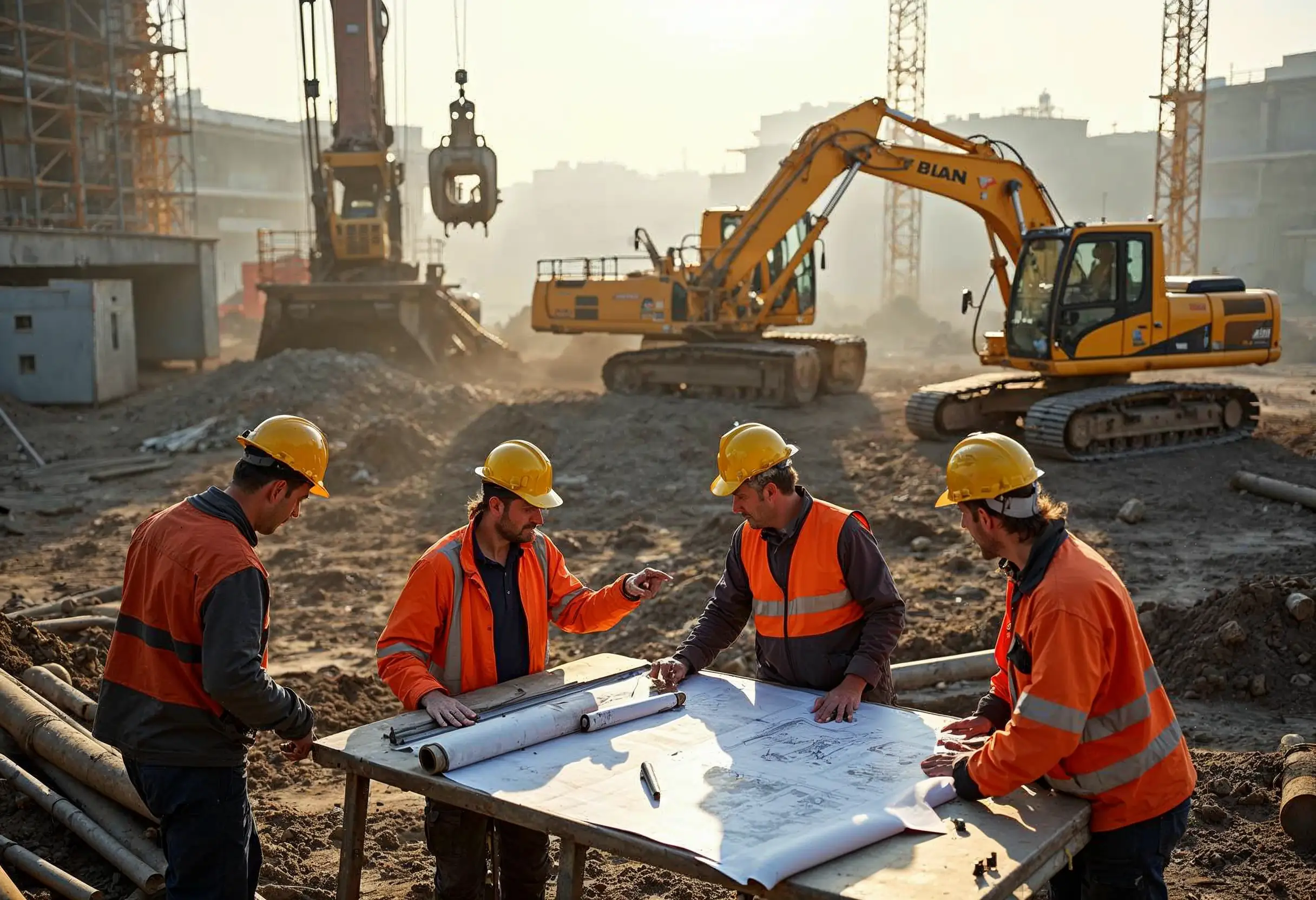
10 Smart Ways to Pick Construction Machinery for 2025 Projects
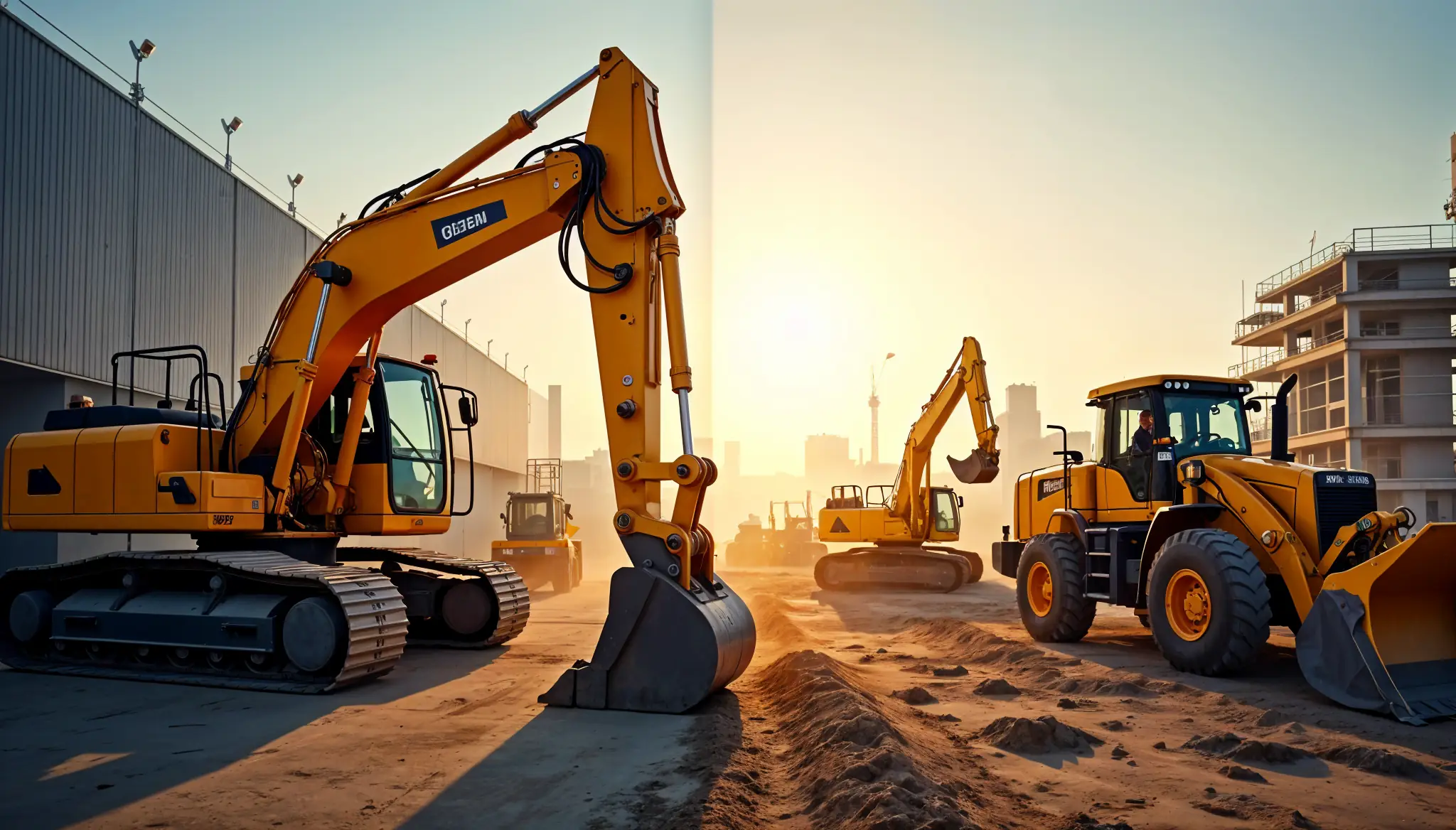
Rent vs Purchase Equipment: What Heavy Industry Experts Hide
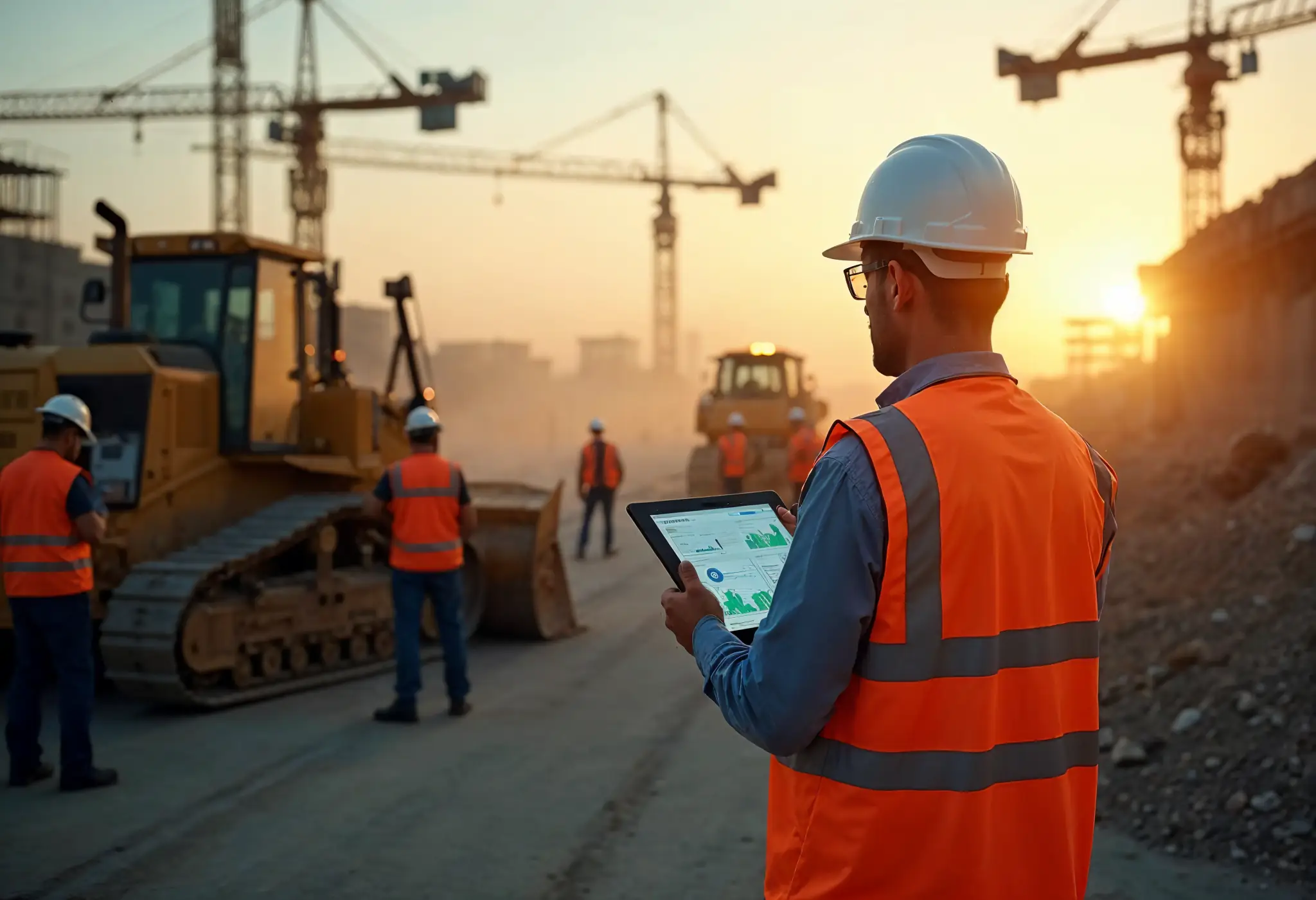
How to Implement a Construction Inventory Management System for Equipment Efficiency
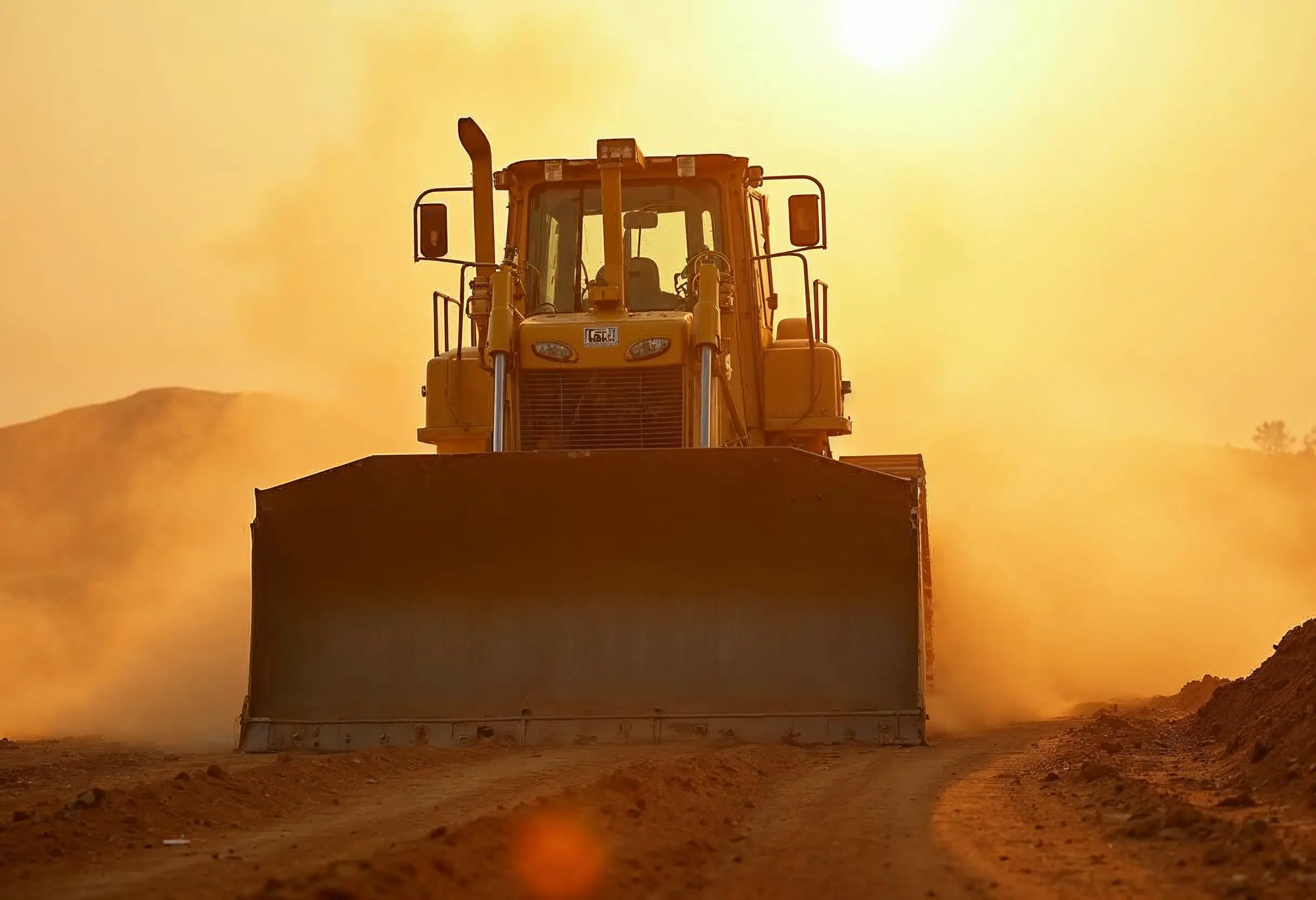
How to Extend Equipment Life Expectancy with Regular Maintenance
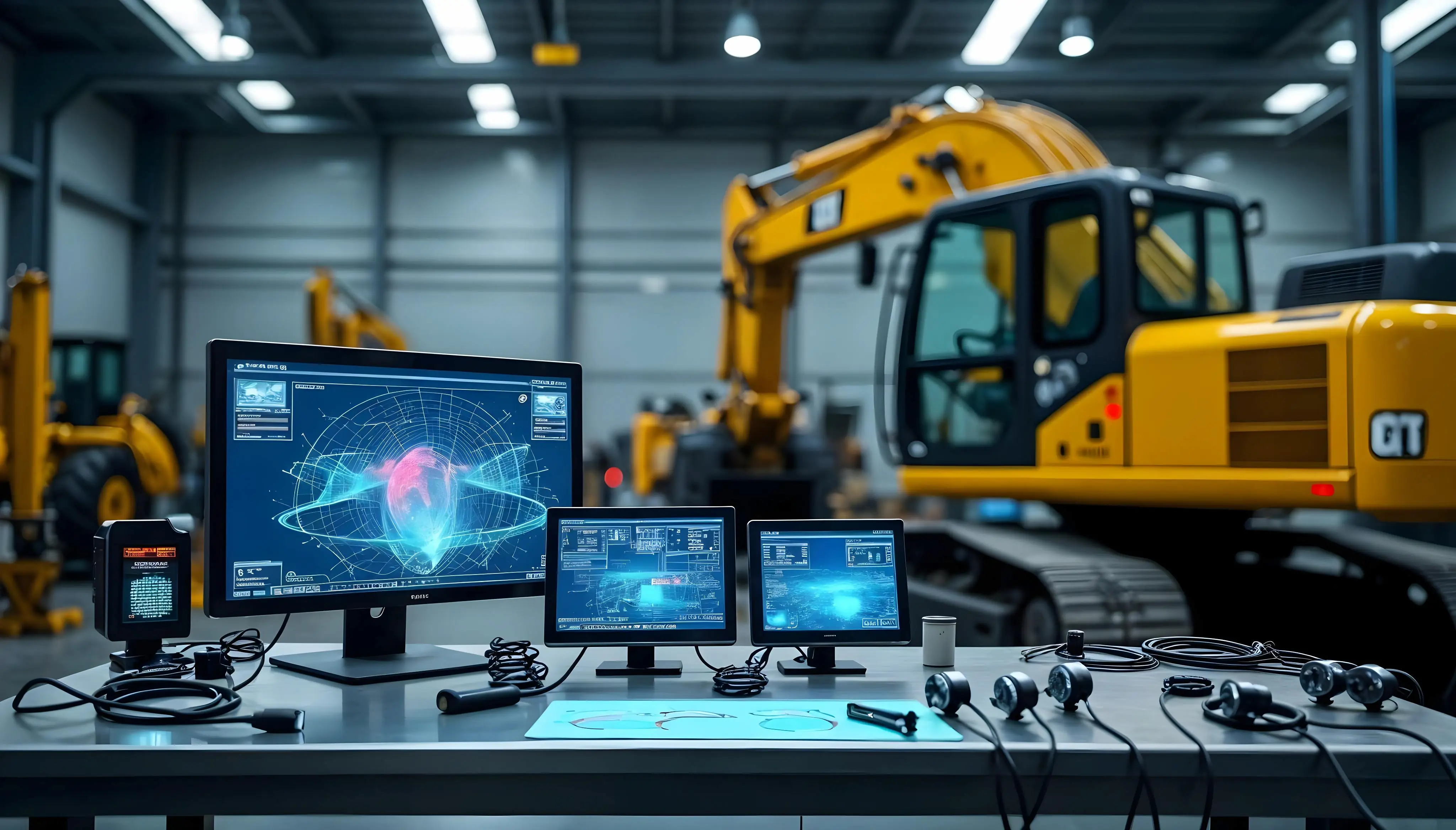
Advanced Heavy Equipment Diagnostic Tools: Ensuring Construction Machinery Quality
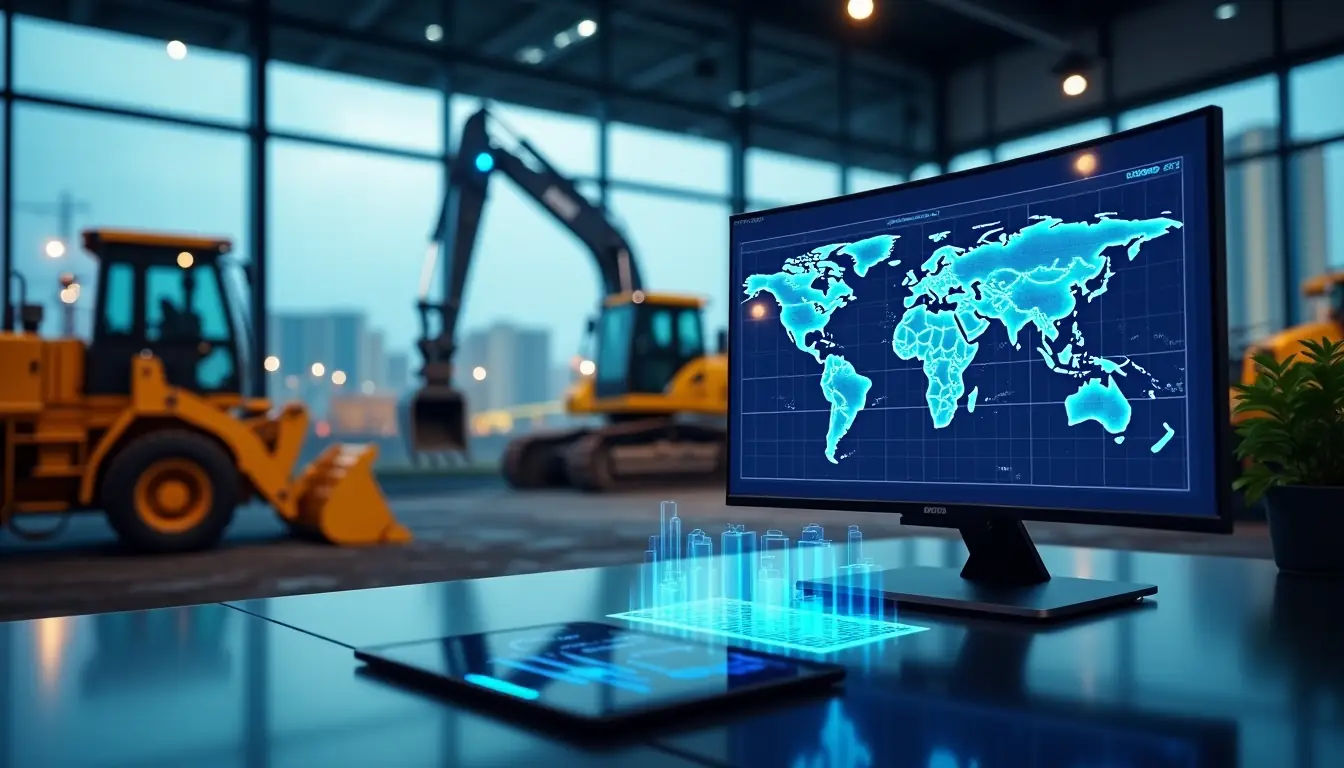
Essential Features Your Construction Equipment Inventory System Needs
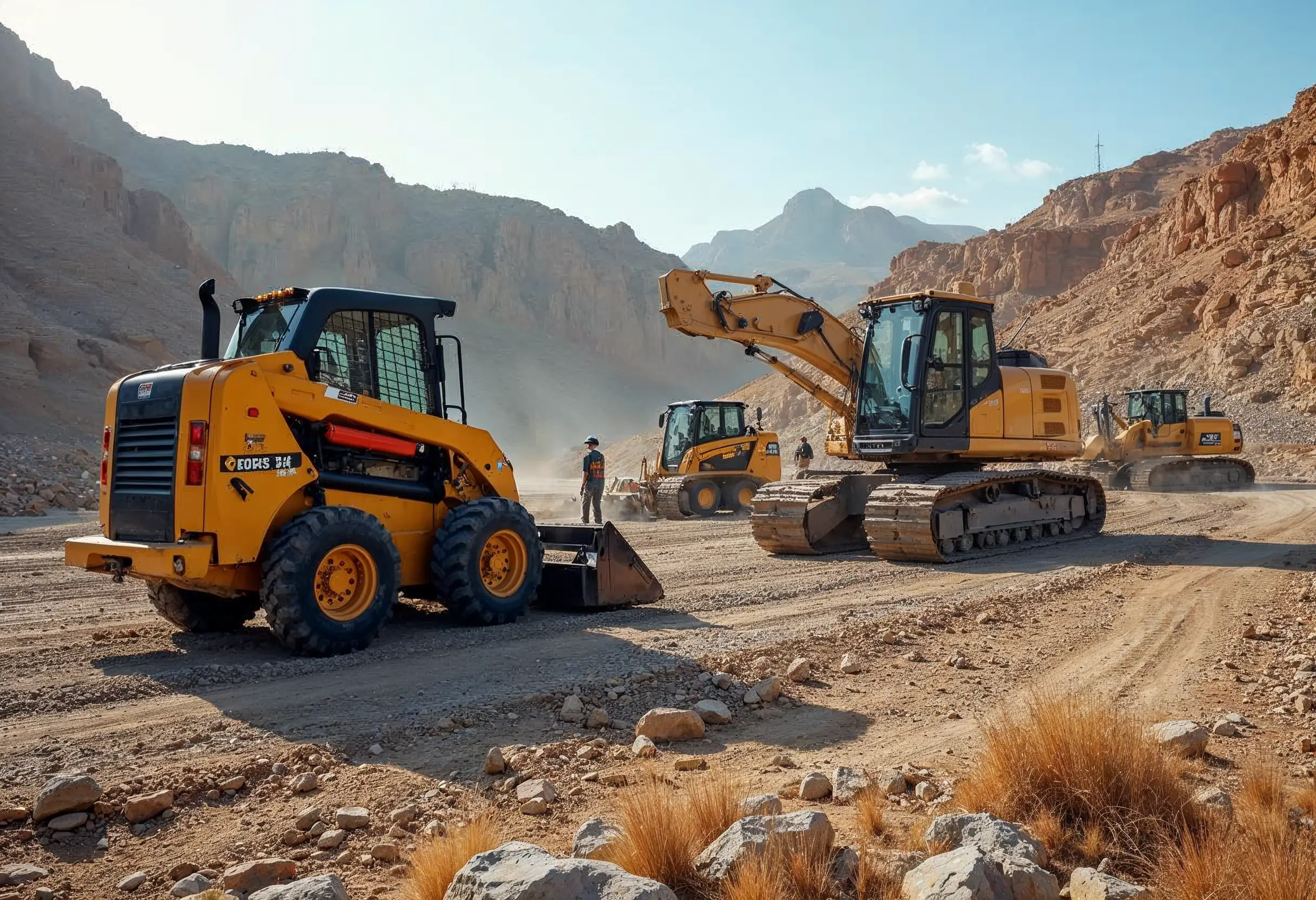
29 Quick Tips for Choosing Construction Equipment for Remote Locations
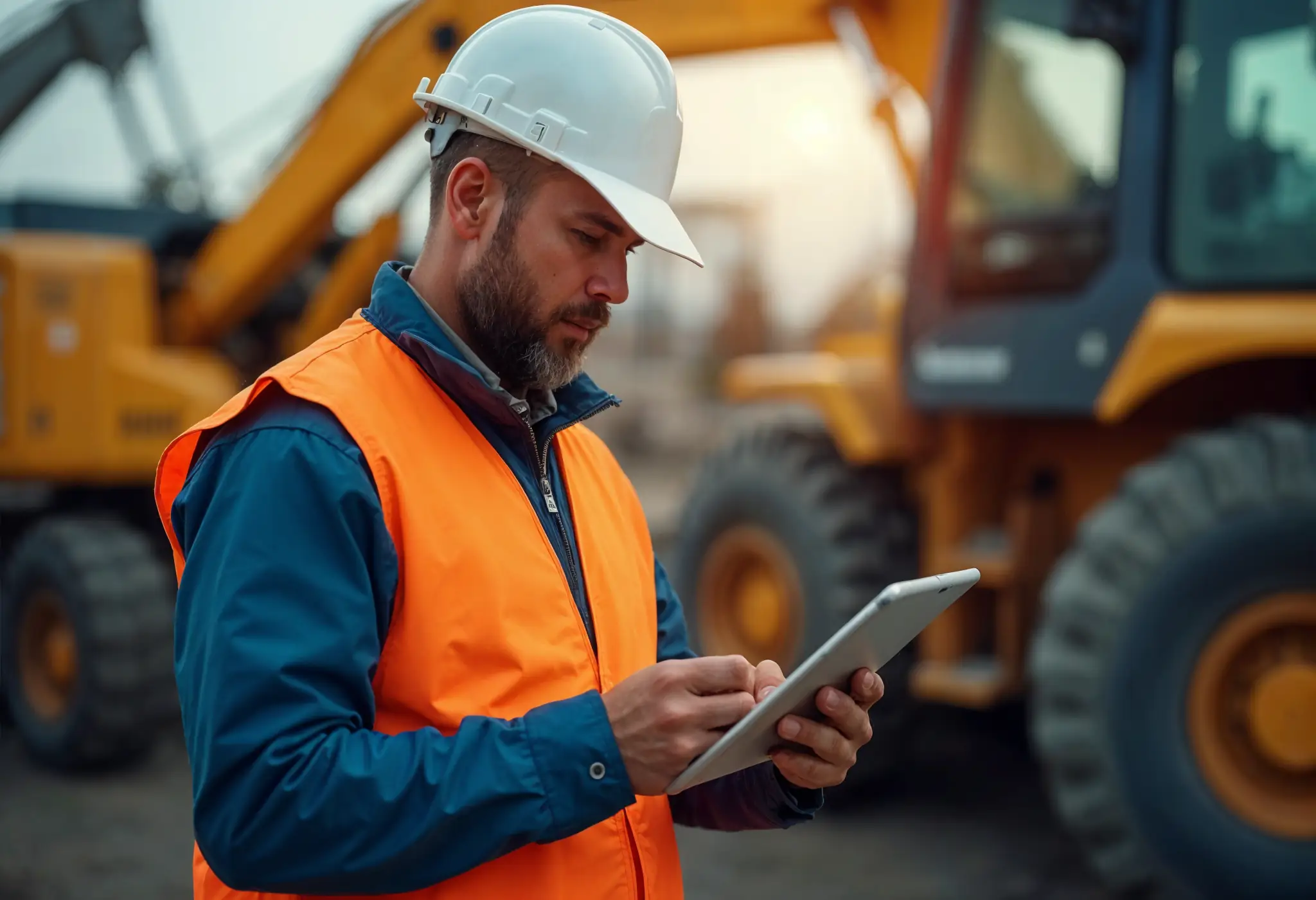
How to Select Construction Machinery with Optimal Equipment Maintenance in Mind
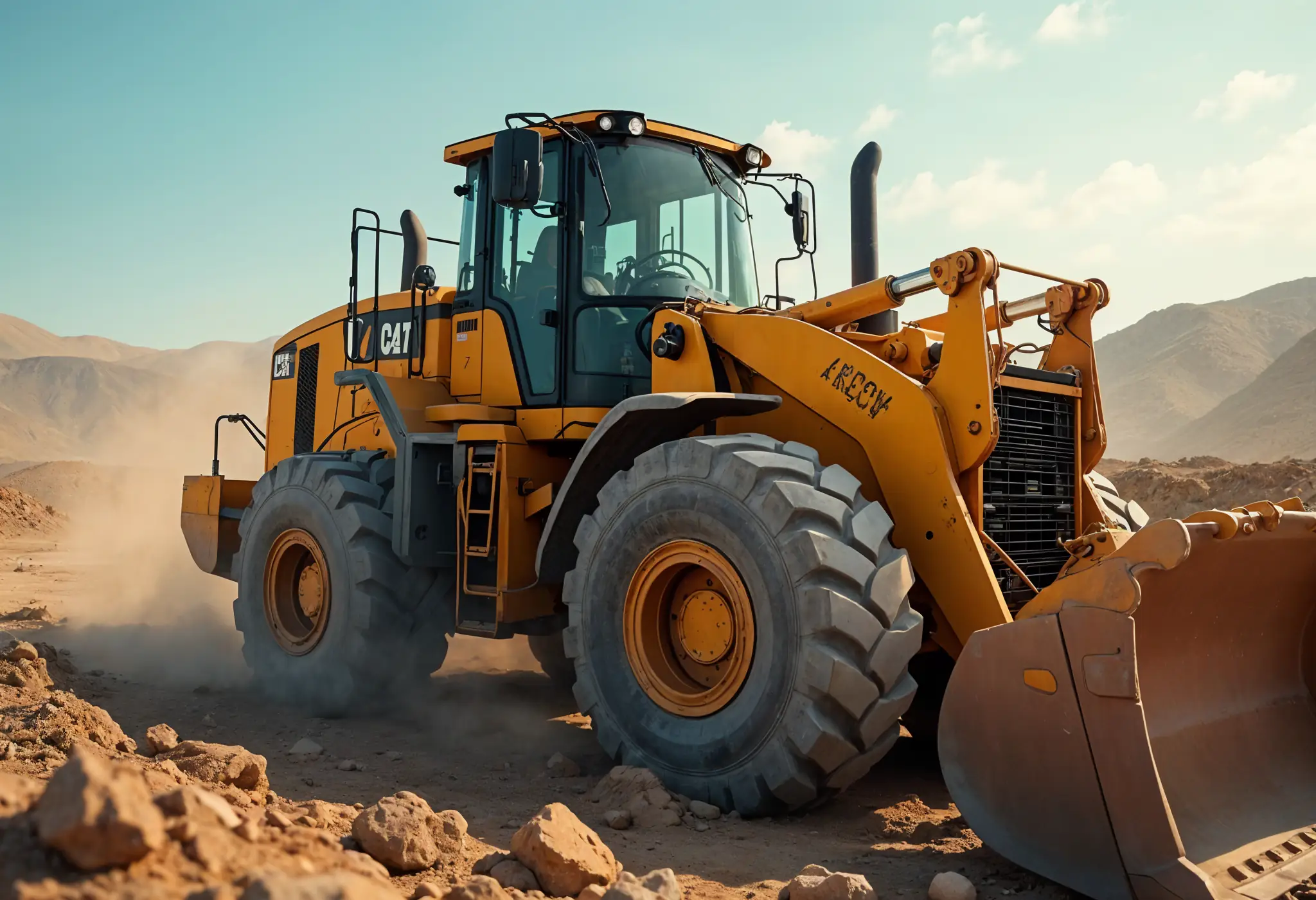
Top 25 Tips for Selecting Bulldozers for Construction Sites
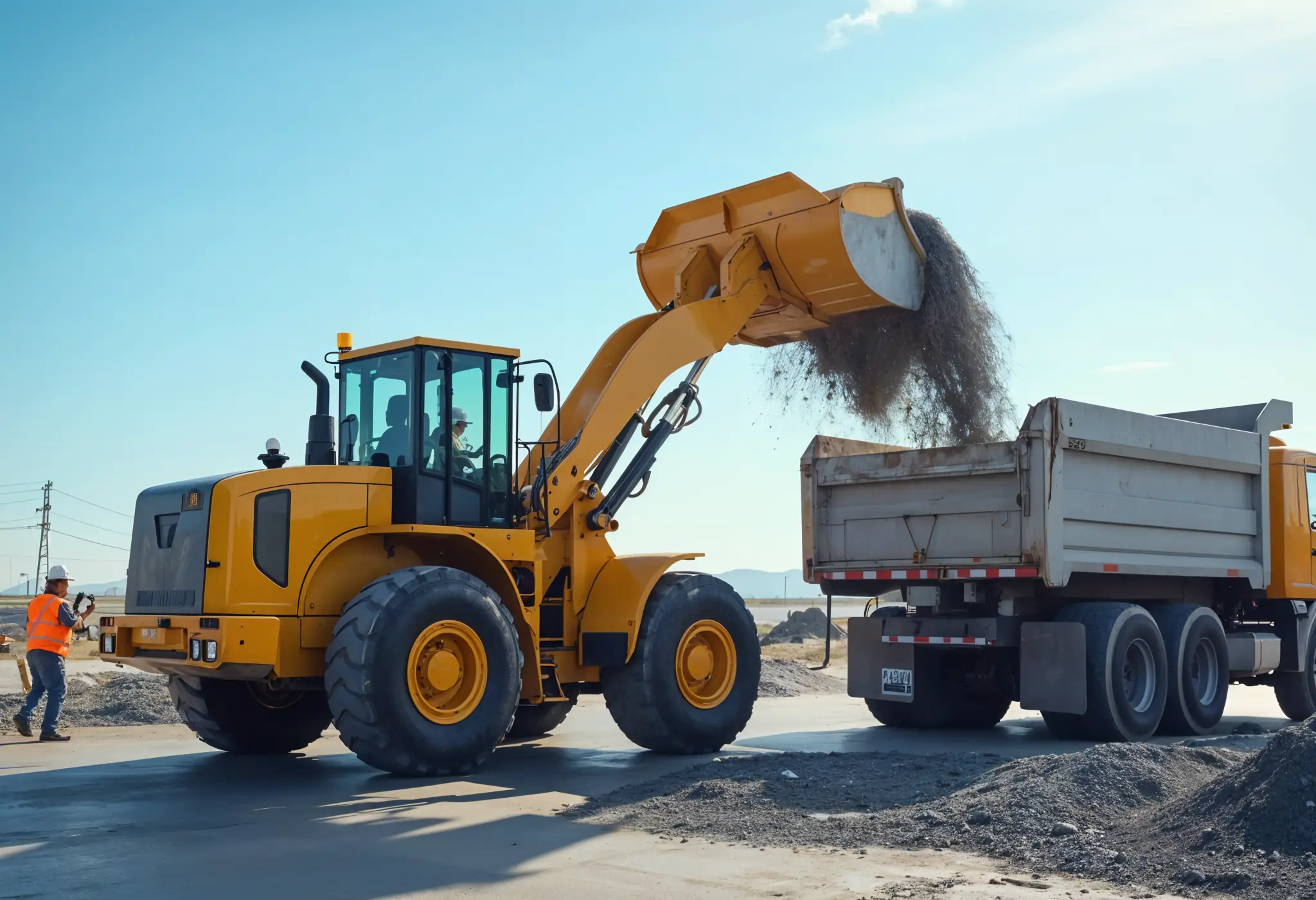
Which Construction Loader is Best for Your Project Needs?
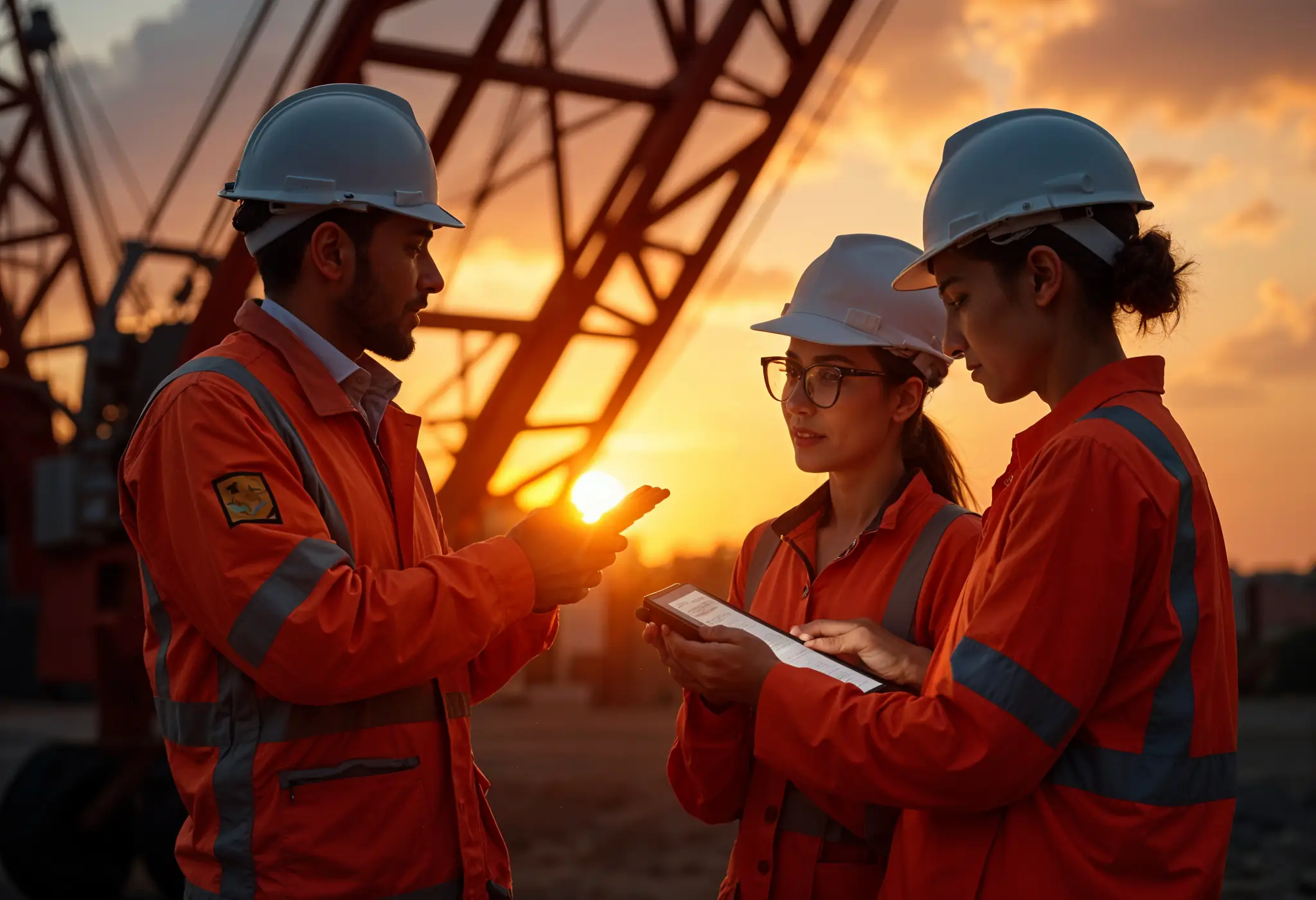
4 Key Steps to Form a Construction Machinery QC Team
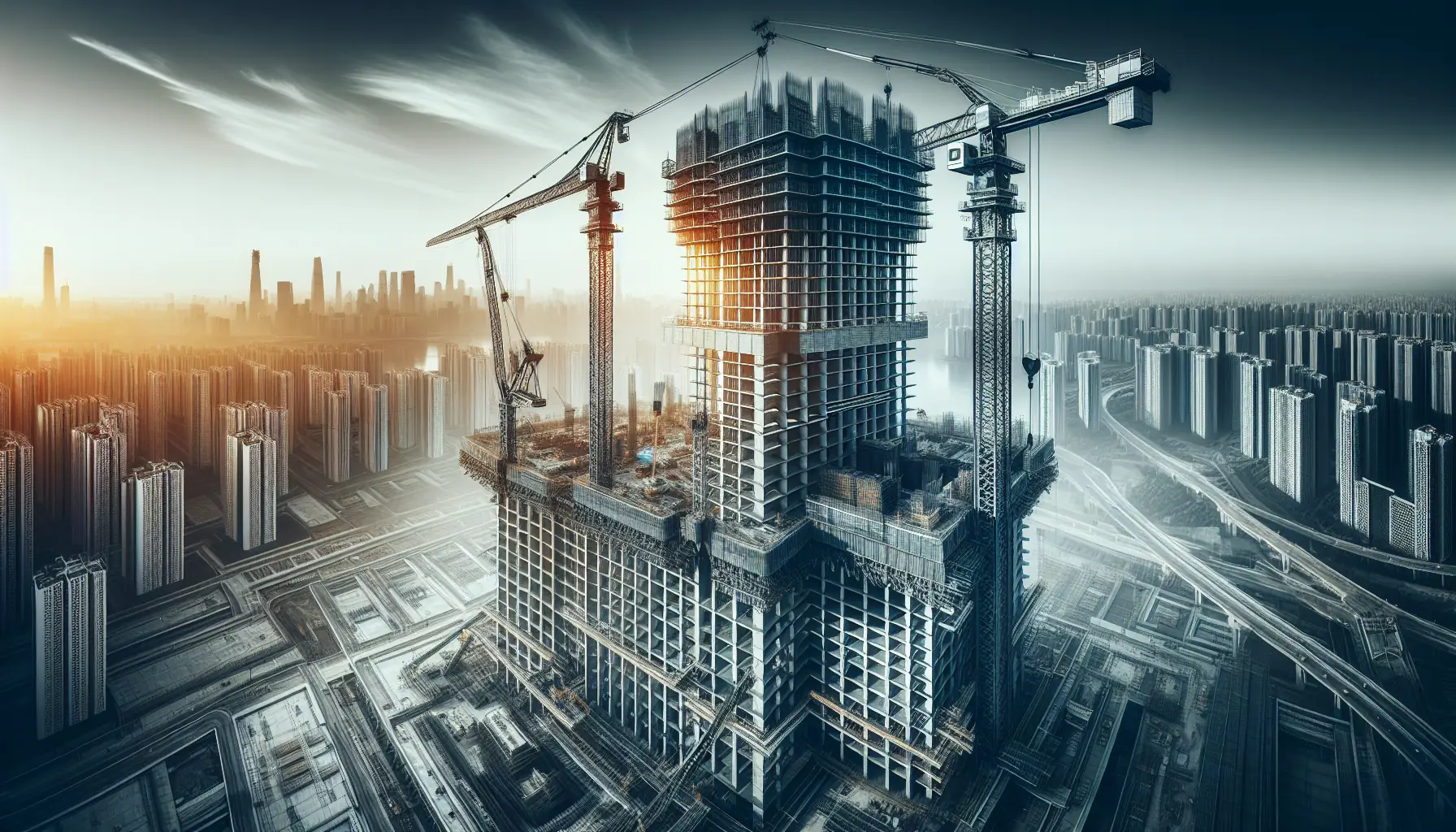
15 Essential Tips for Selecting the Perfect Crane for Construction
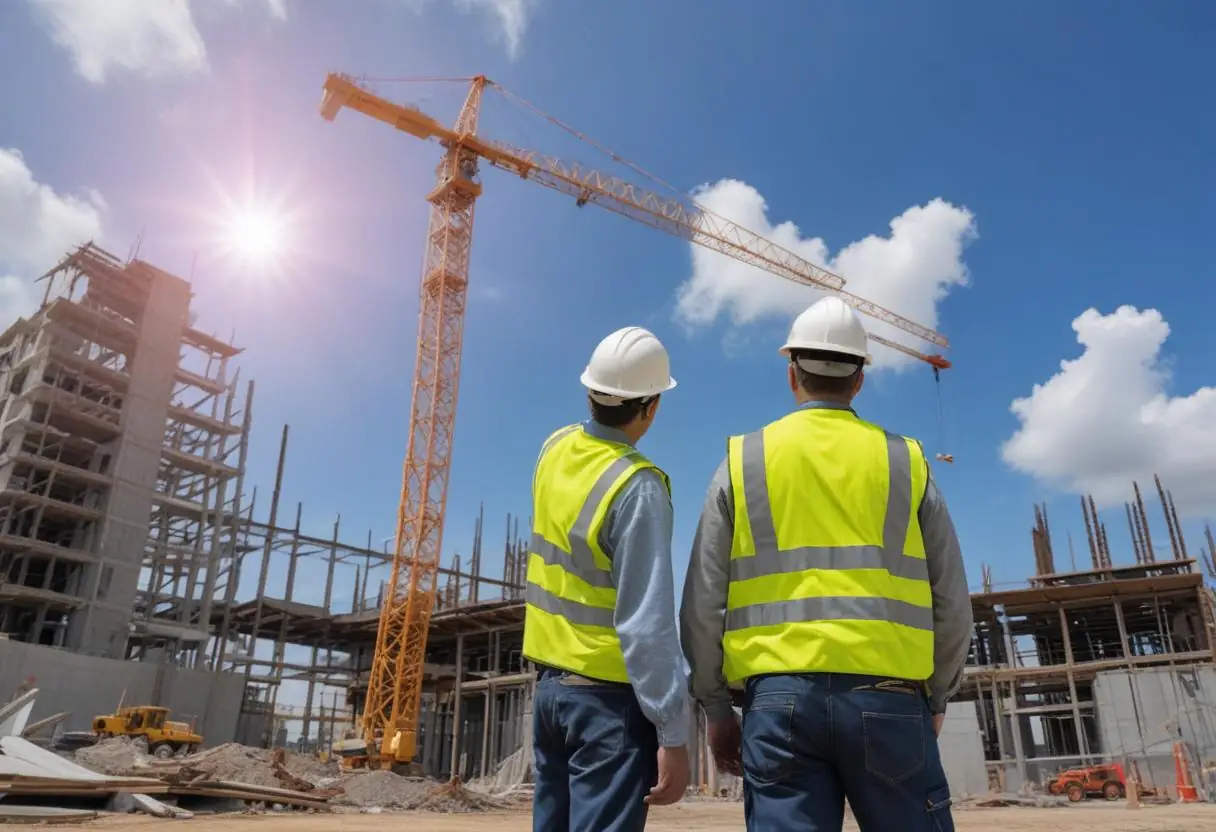
Maximize Savings: Multi-Purpose Construction Machinery for Lower Costs
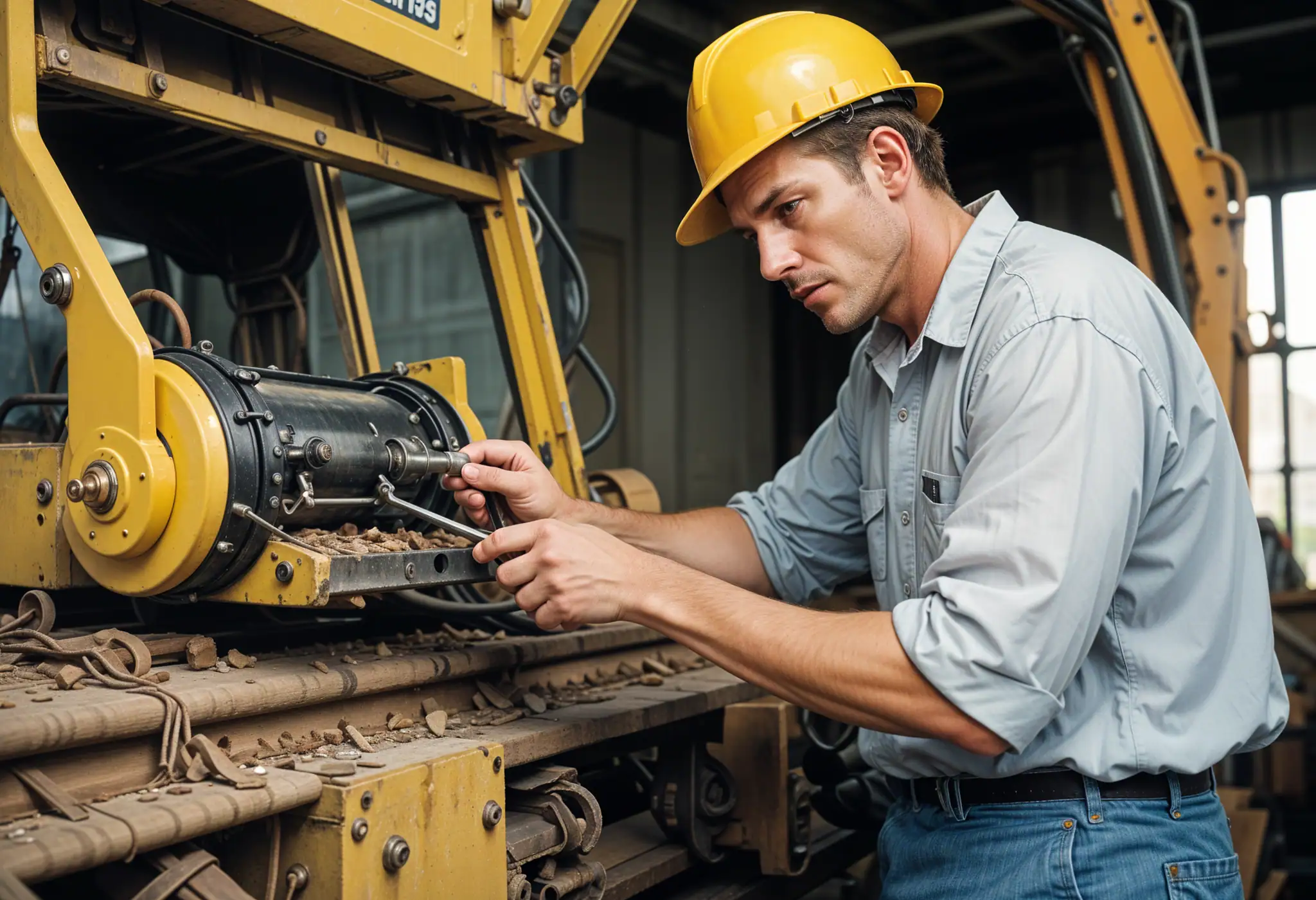
Affordable Heavy Equipment Parts: A Sourcing Guide
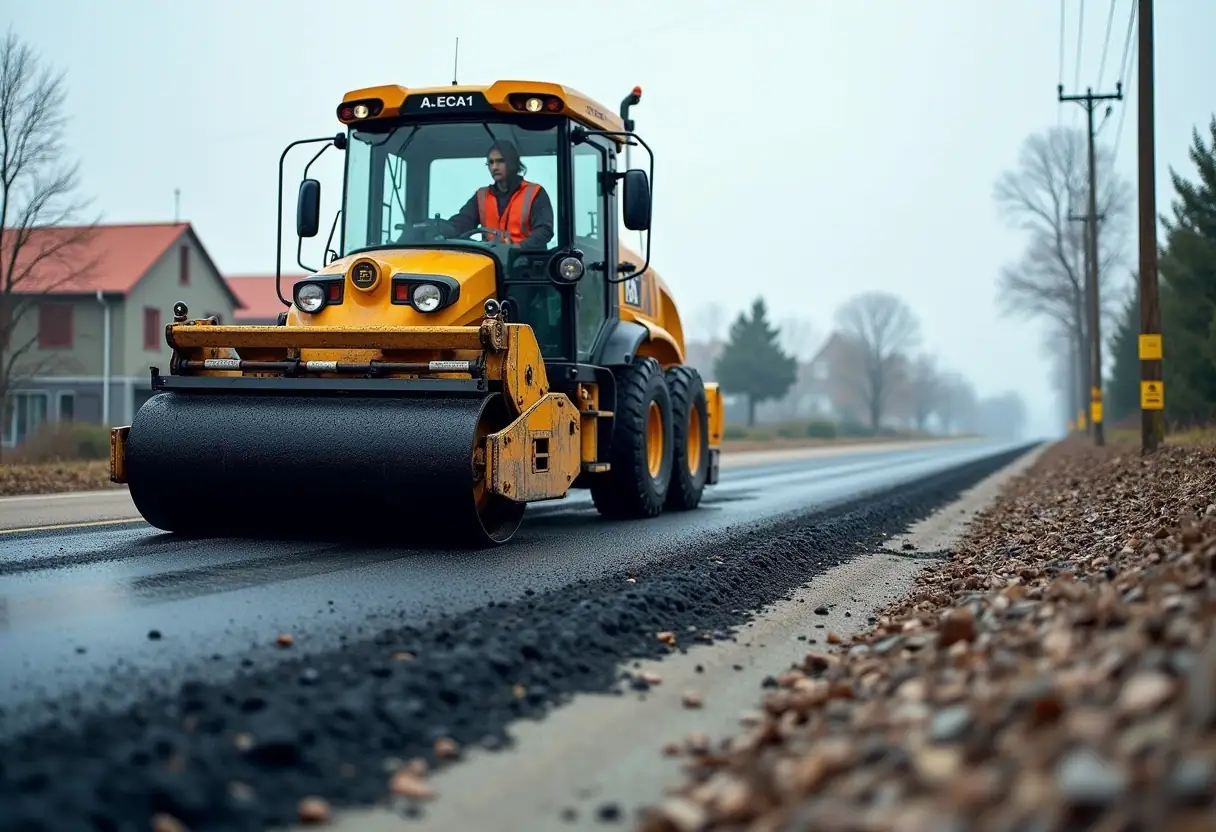
Choosing the Right Road Construction Equipment: A Complete Guide
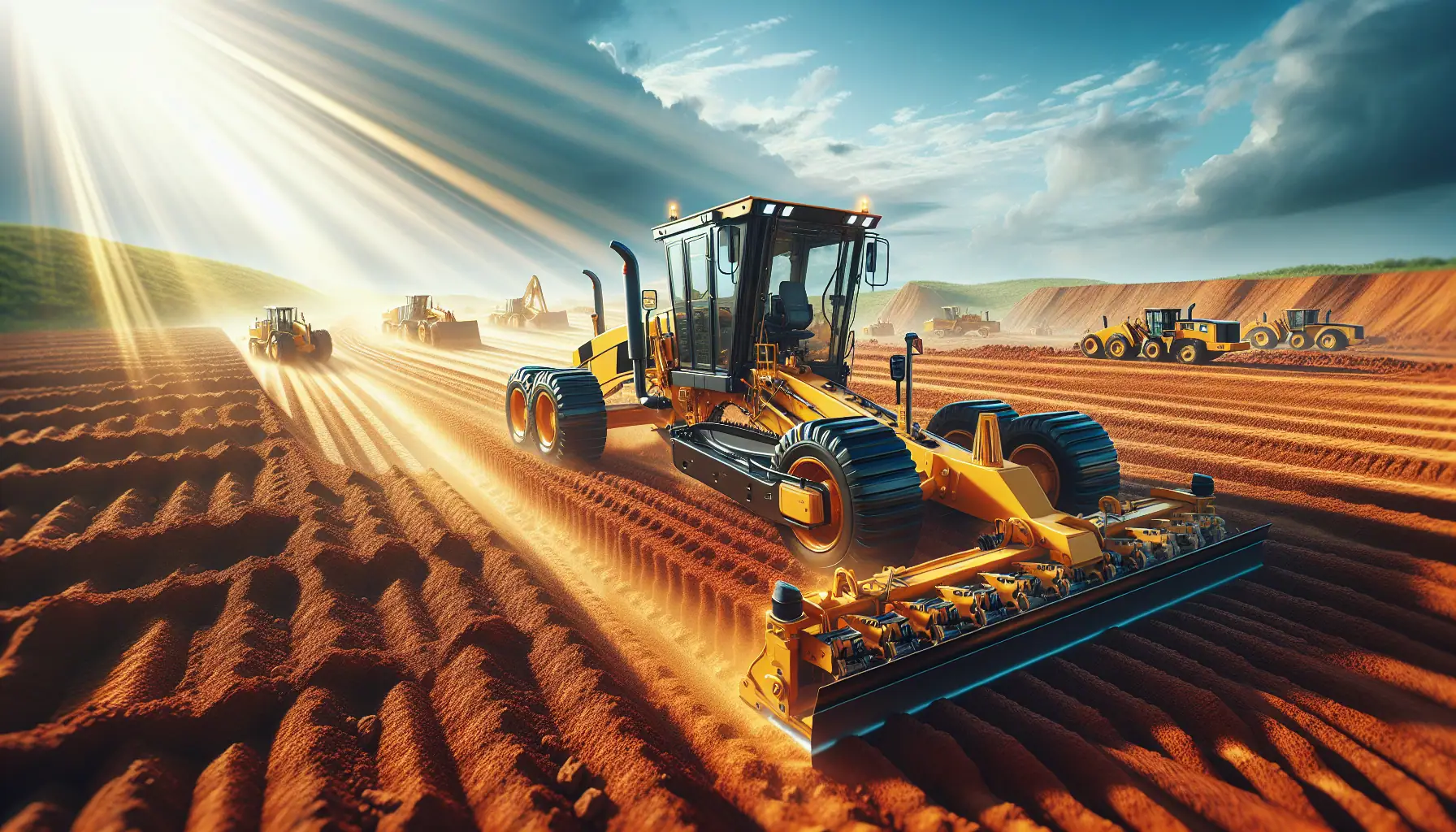
Motor Graders: Key Elements to Consider for Optimal Selection
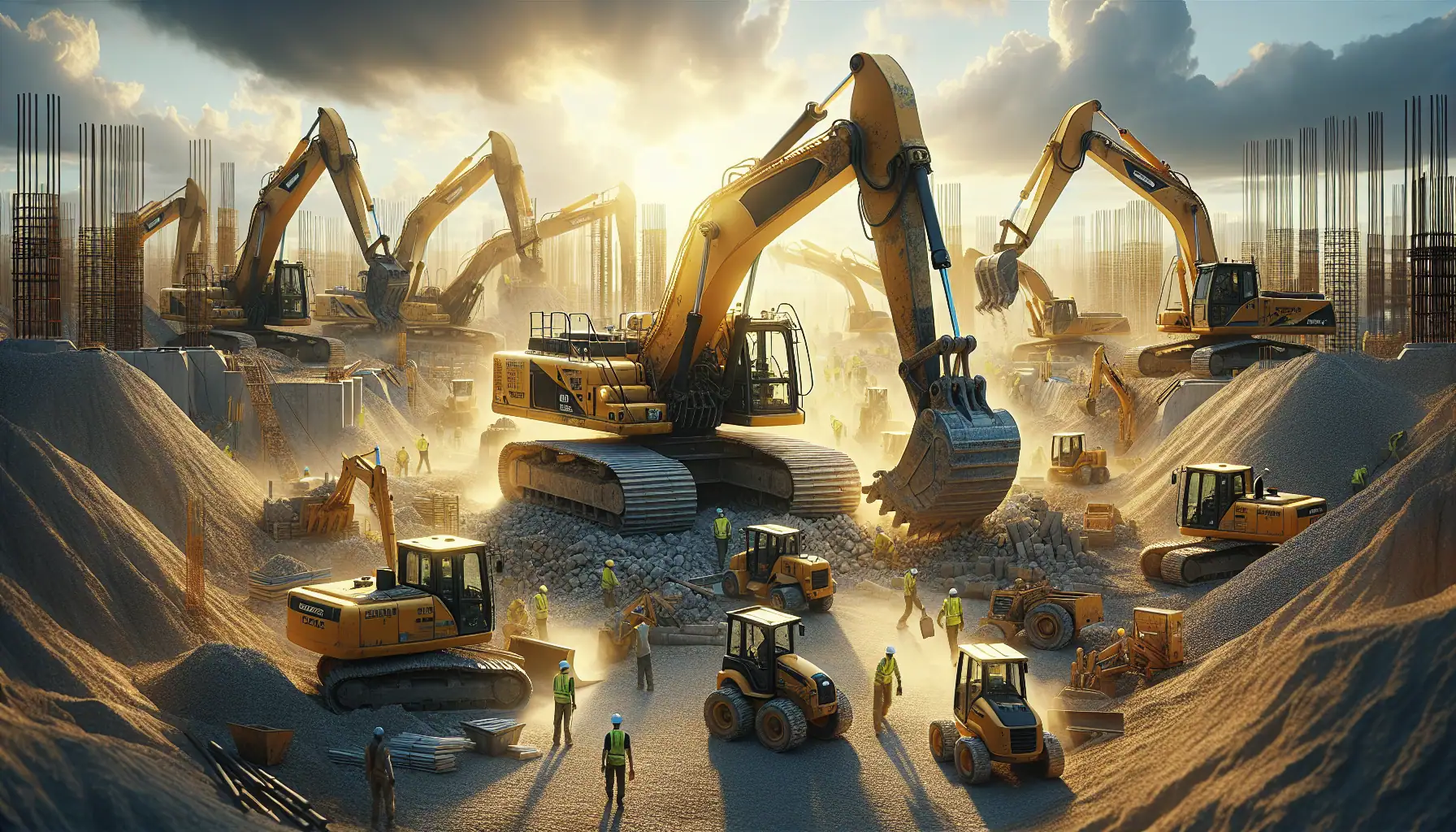
A Detailed Guide to Choosing Excavators for Construction Work
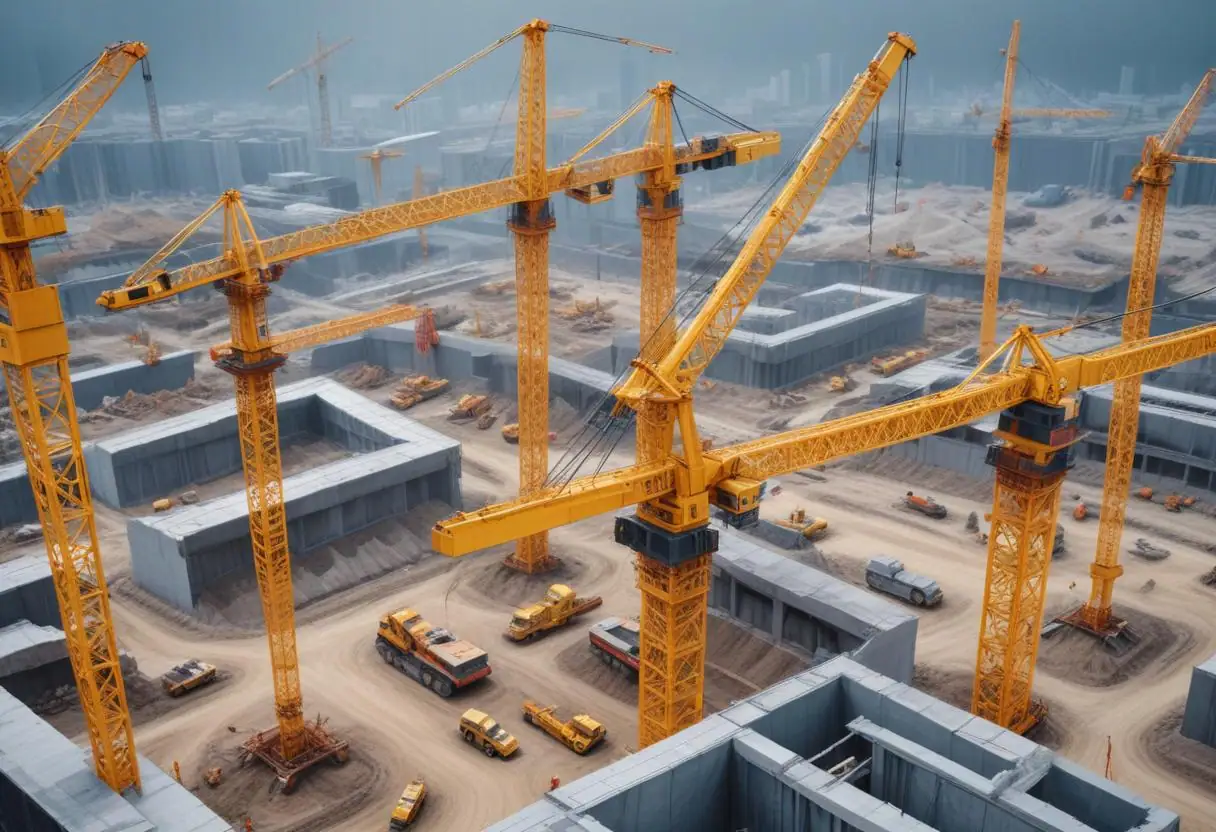
Top Tips for Choosing Cranes for Construction Projects
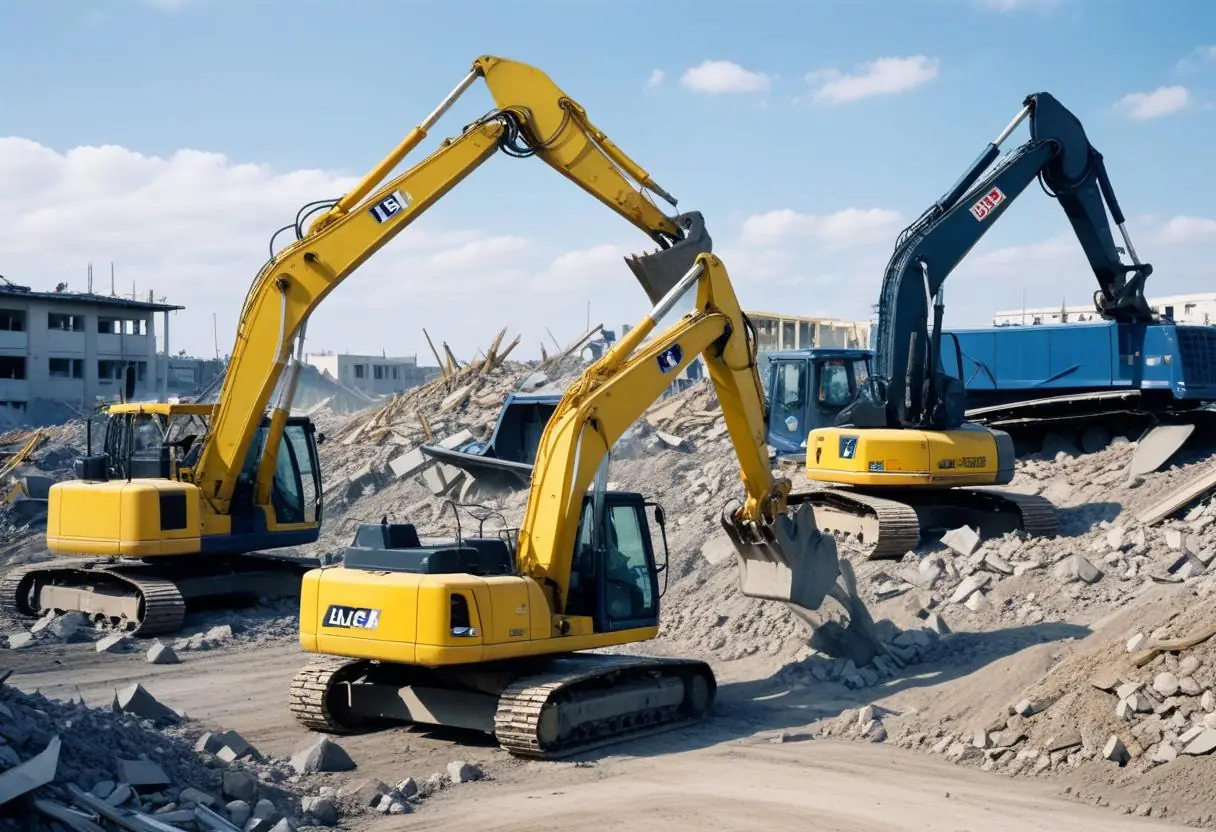
5 Top-Rated Demolition Machines for Construction Professionals
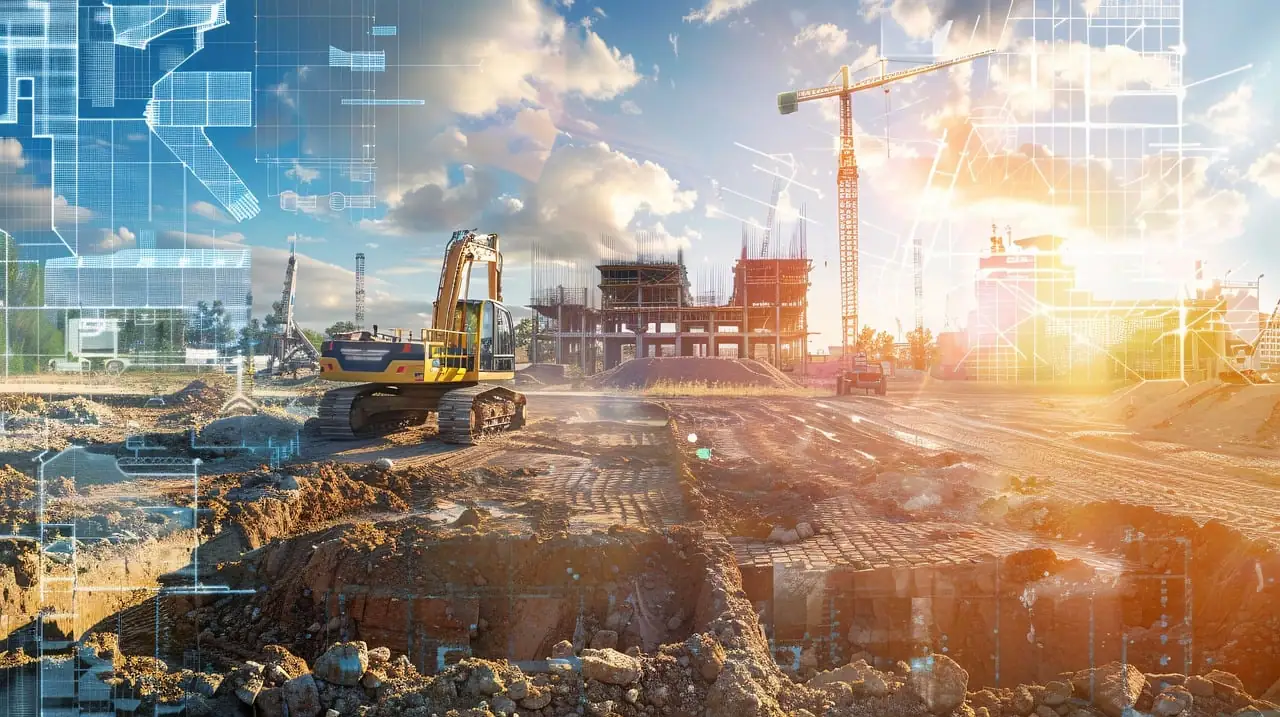
Expert Tips on Choosing Earthmoving Equipment for Large Projects
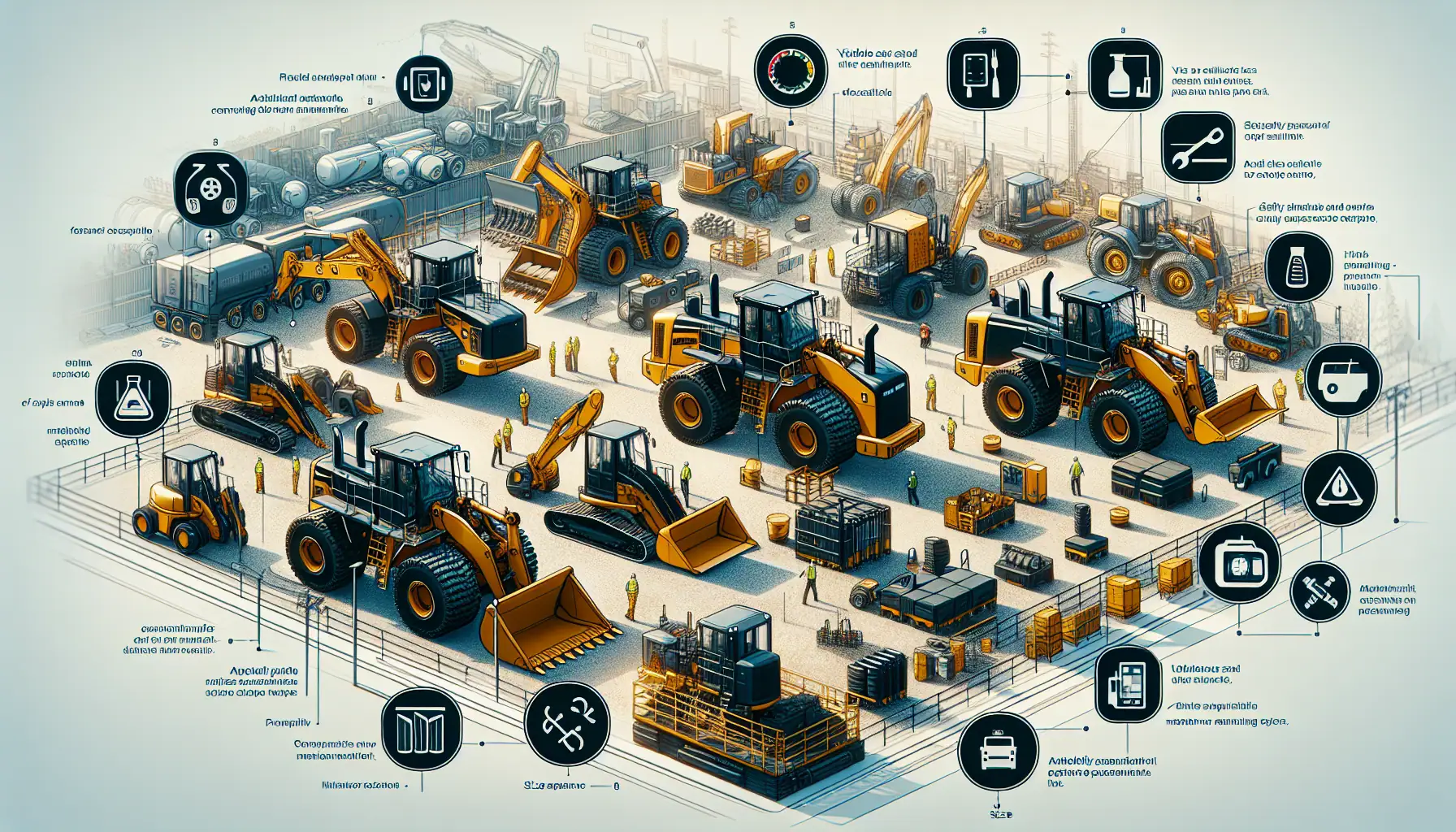
Top Functional Criteria for Selecting Heavy Construction Equipment
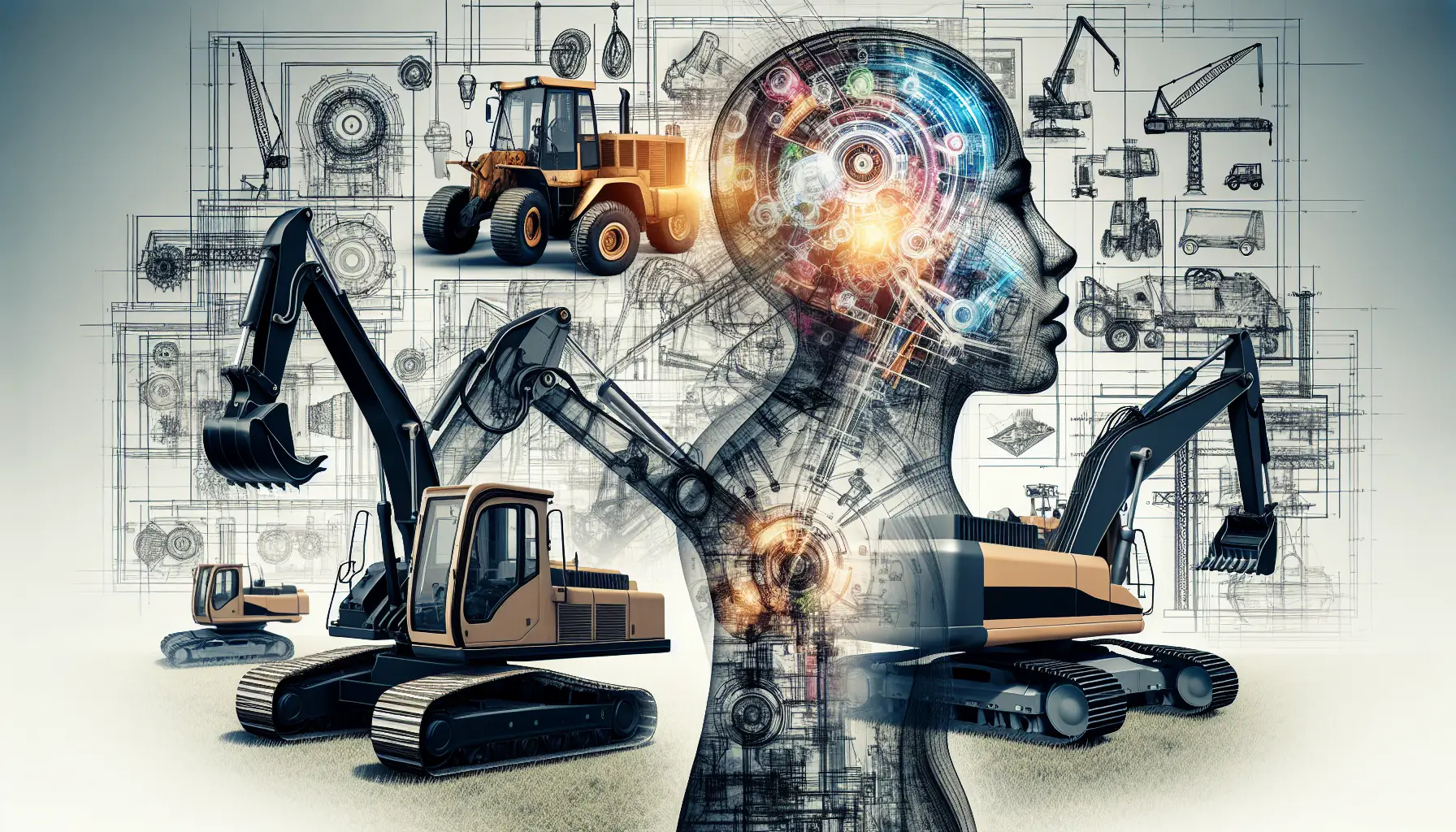
Construction Machinery: Detailed Guide to Equipment Specifications
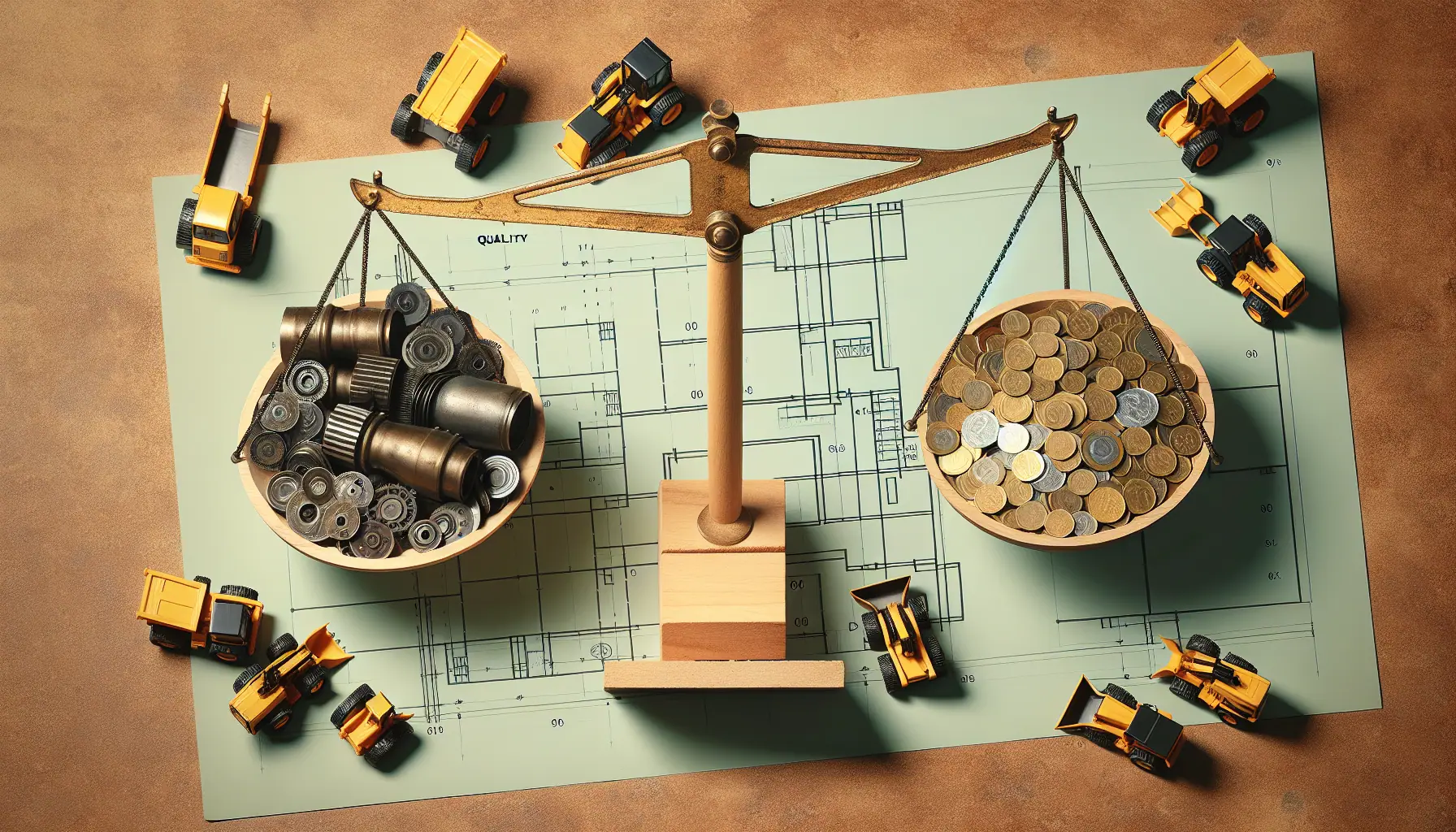
Heavy Machinery Prices: Key Factors in Cost and Quality Balance
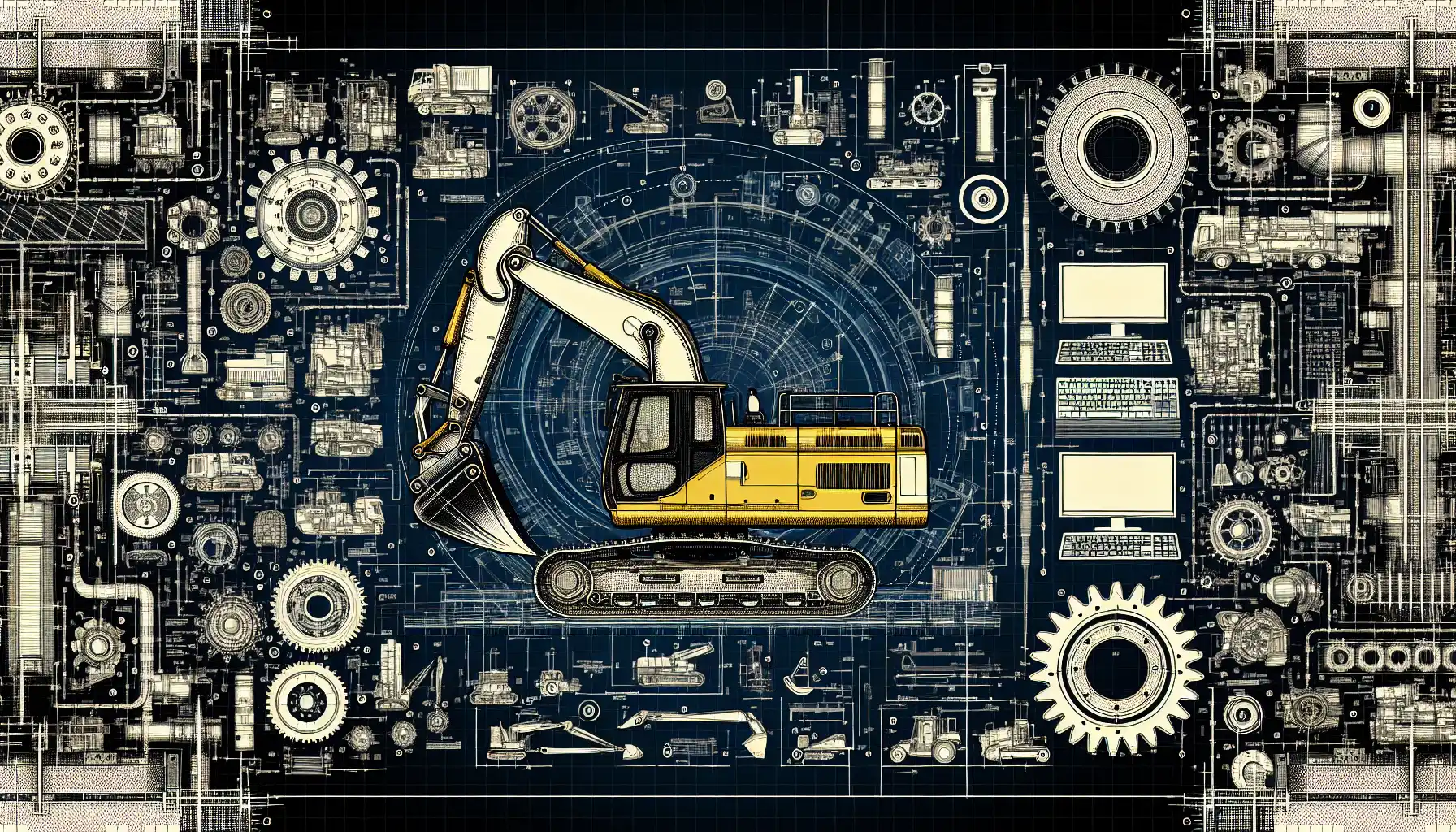
Best Construction Heavy Equipment Brands: Pros and Cons
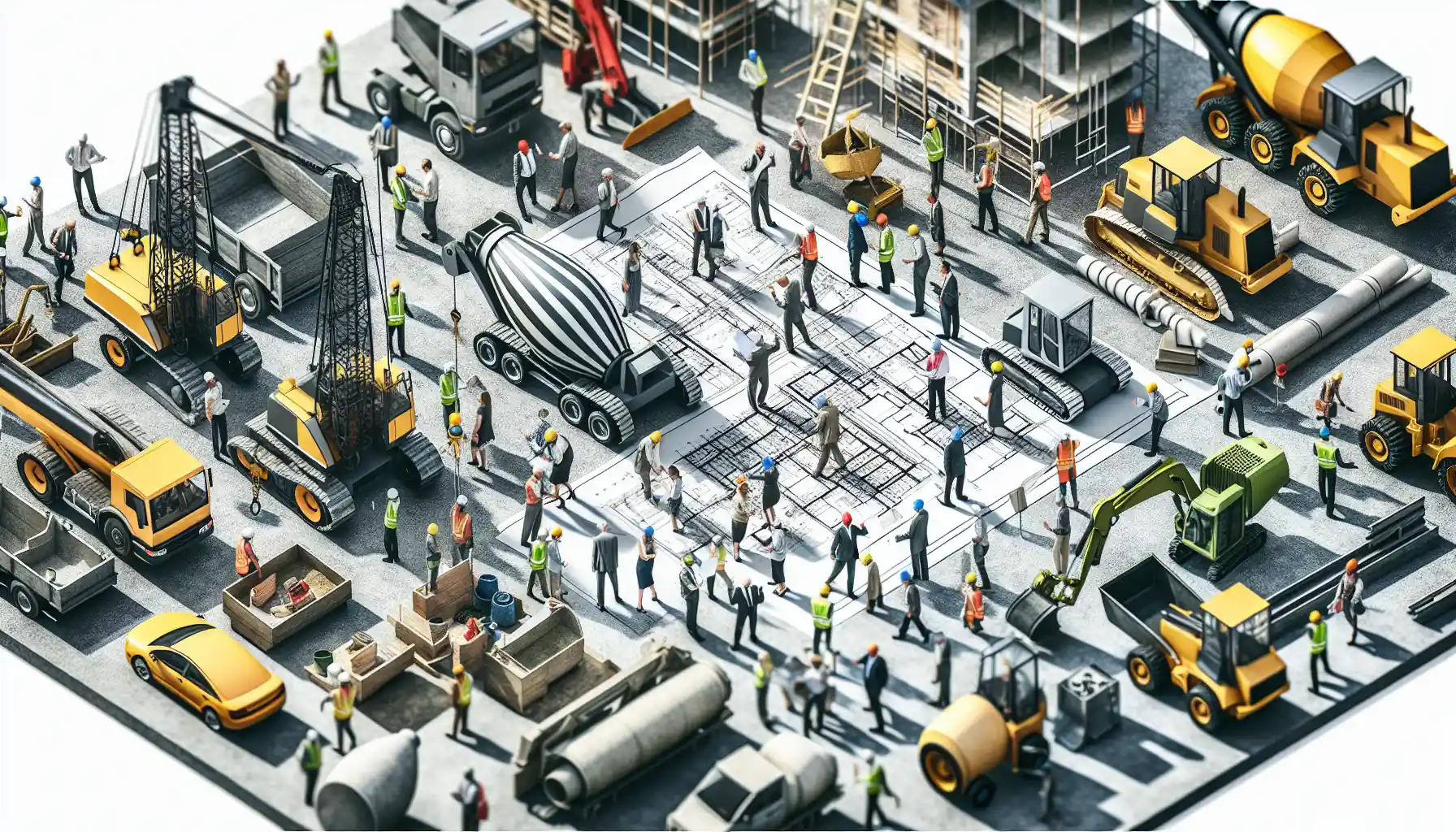
Construction Site Equipment: How to Determine Your Requirements
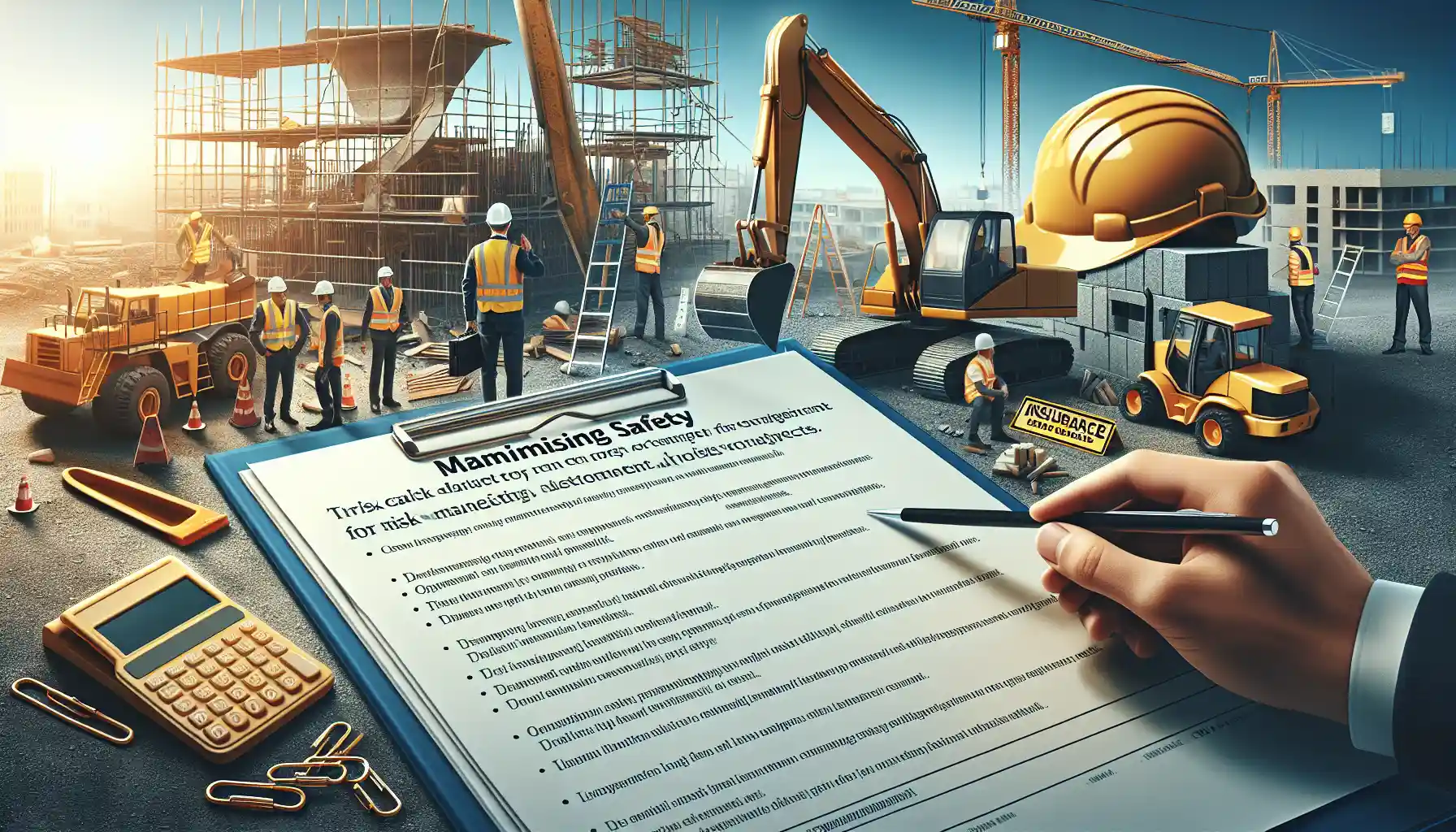
Maximizing Safety: Risk Management for Construction Projects
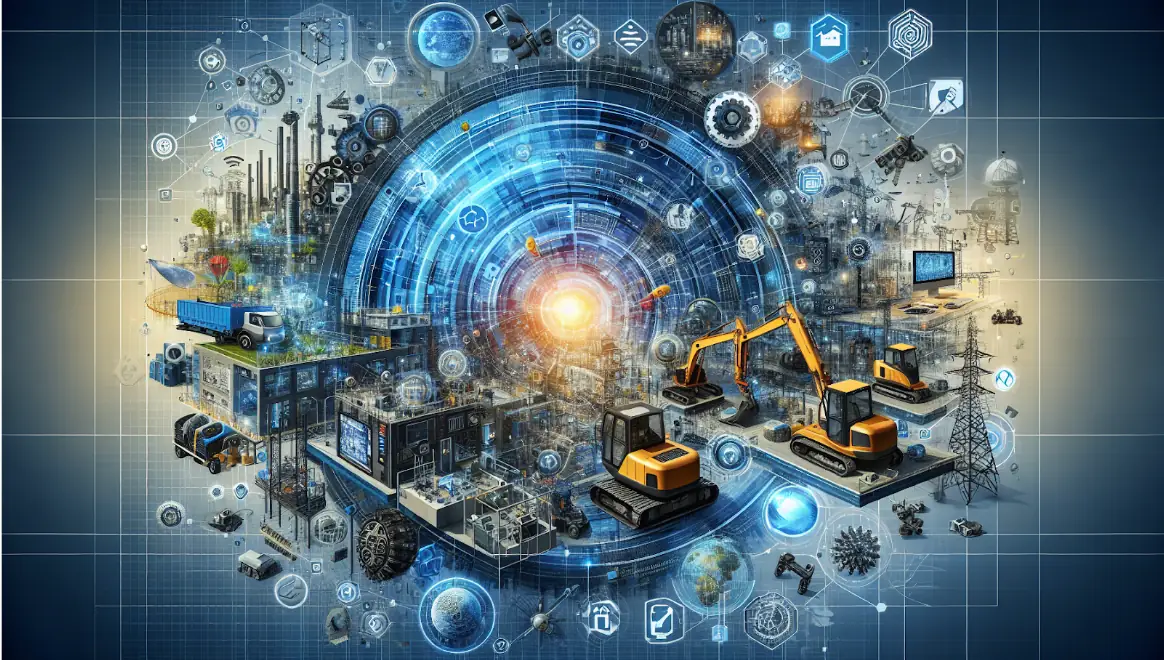
Innovations in Construction: Transforming Machinery and Equipment
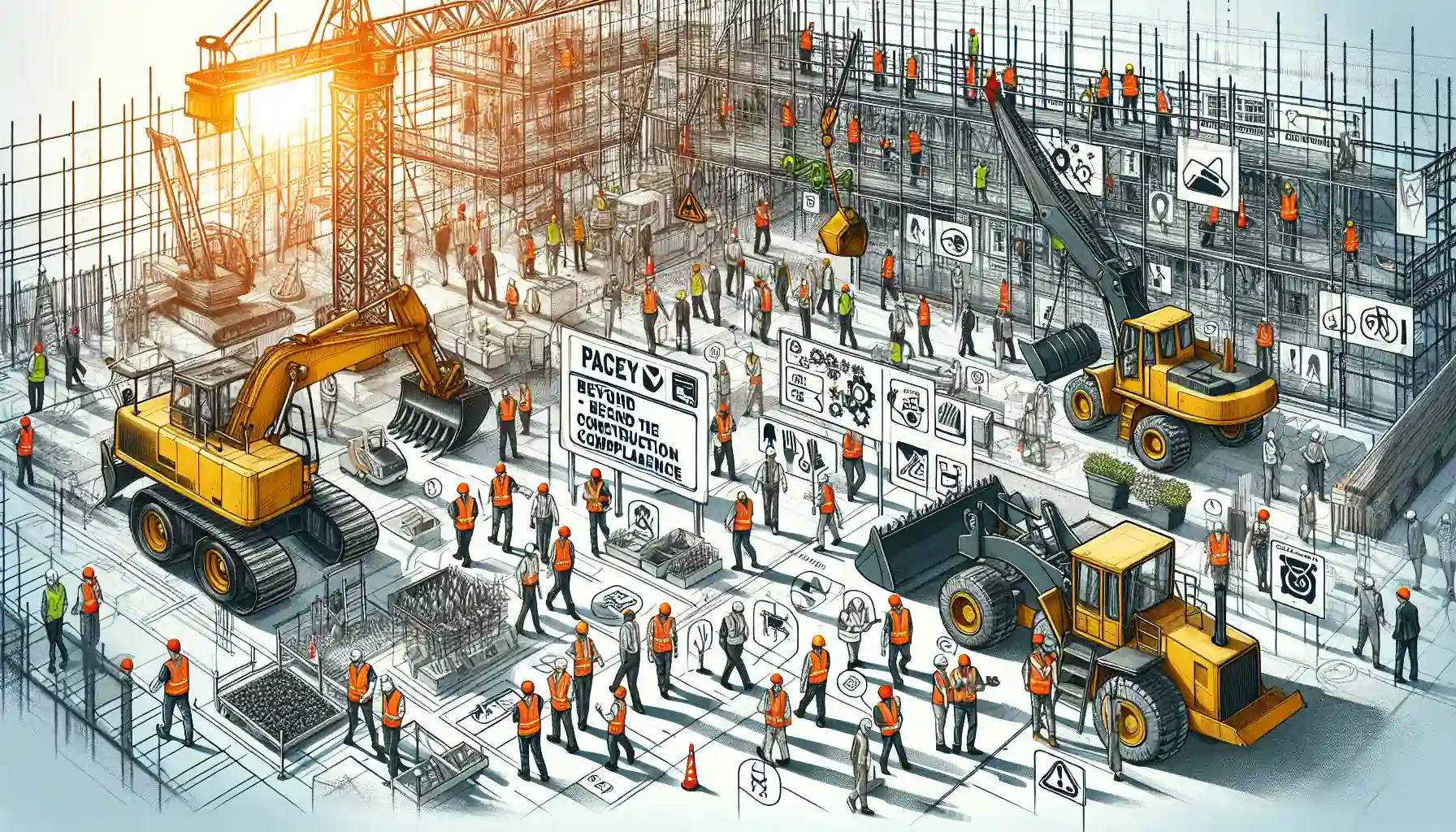
Heavy Equipment Safety: Beyond the Basics in Construction Compliance
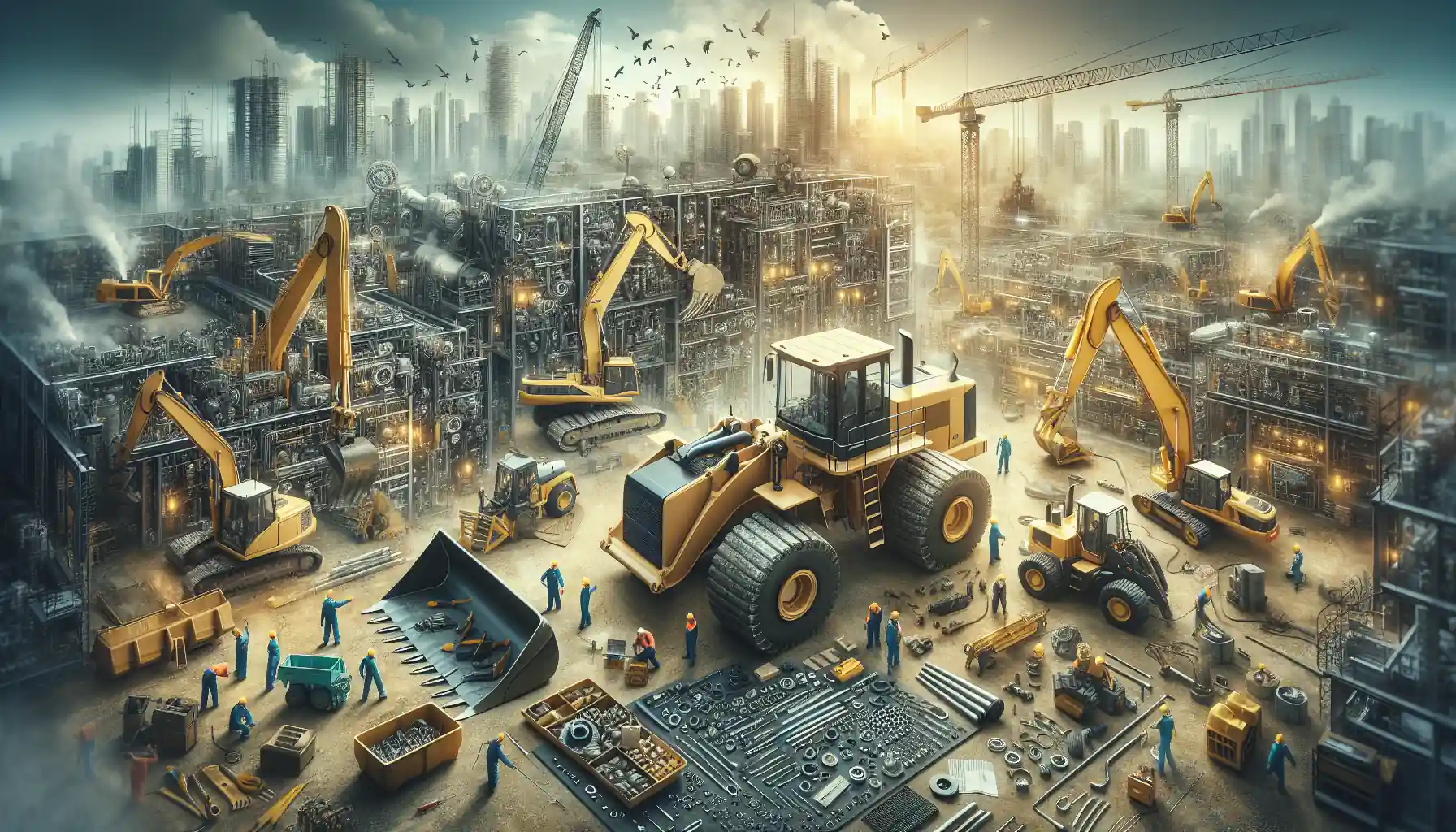
The Essential Handbook for Construction Equipment Repair and Maintenance
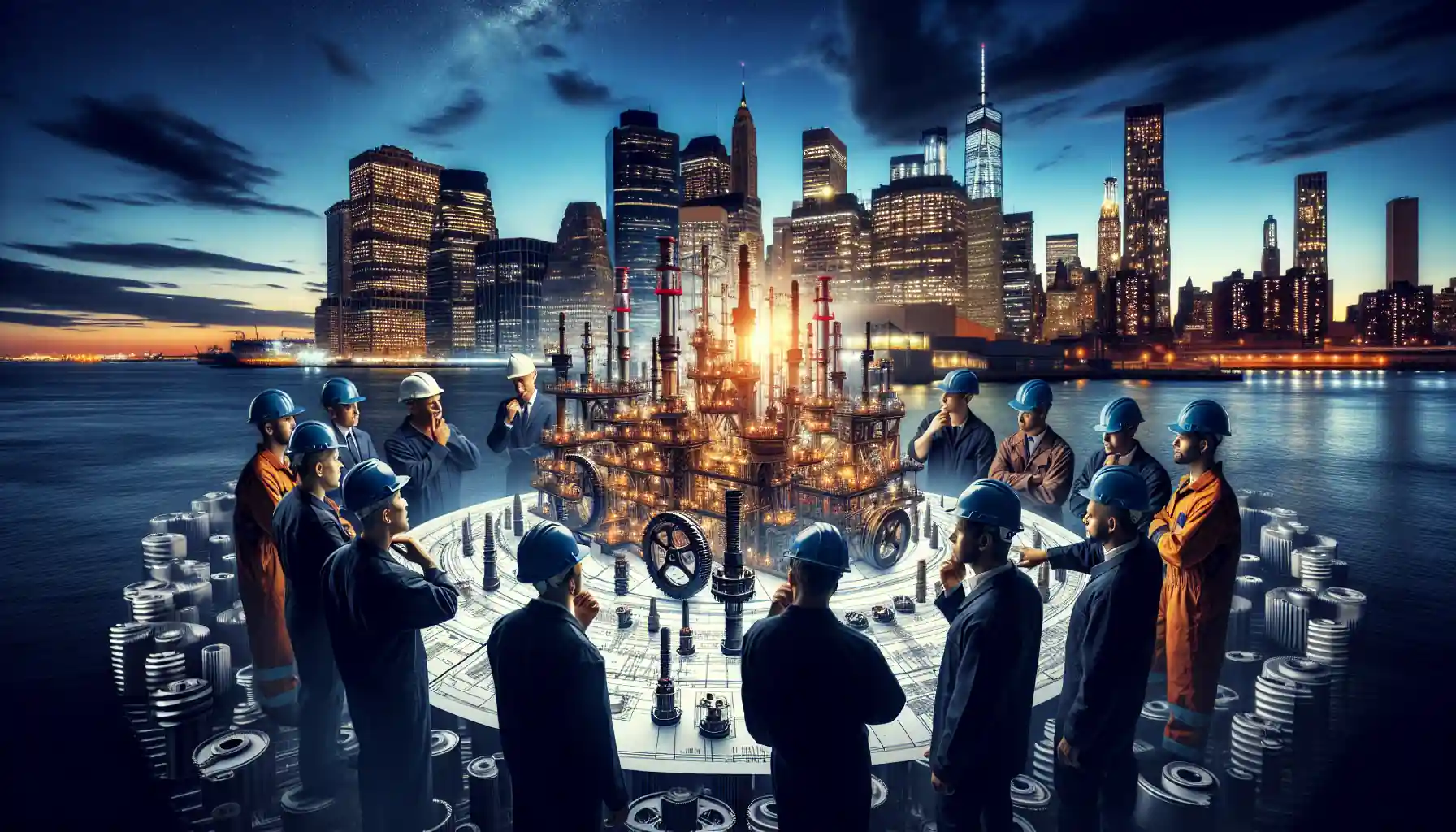
How to Efficiently Source Oil and Gas Machinery Parts in NYC
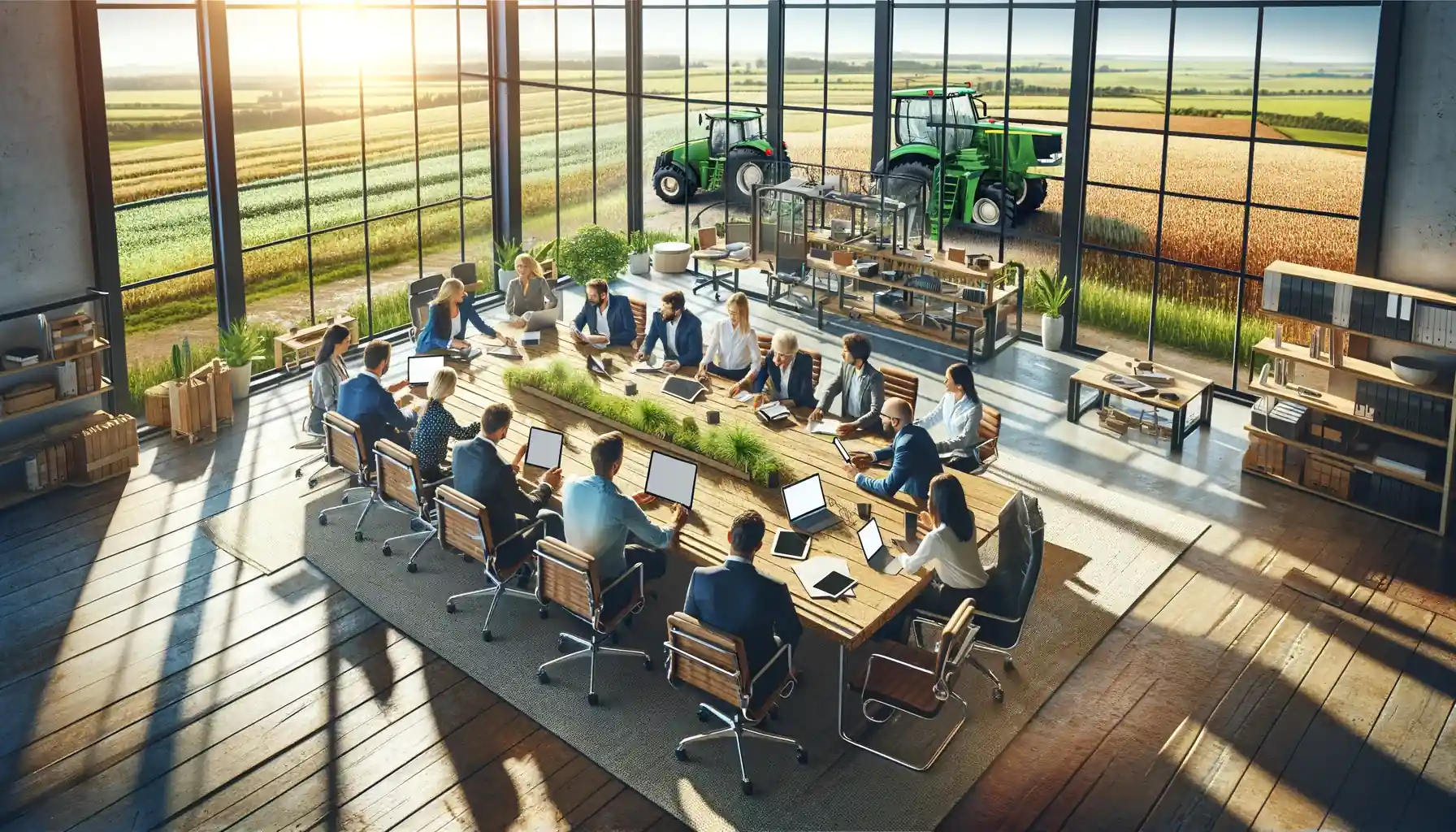
Essential Guide to Sourcing Agriculture Equipment Parts
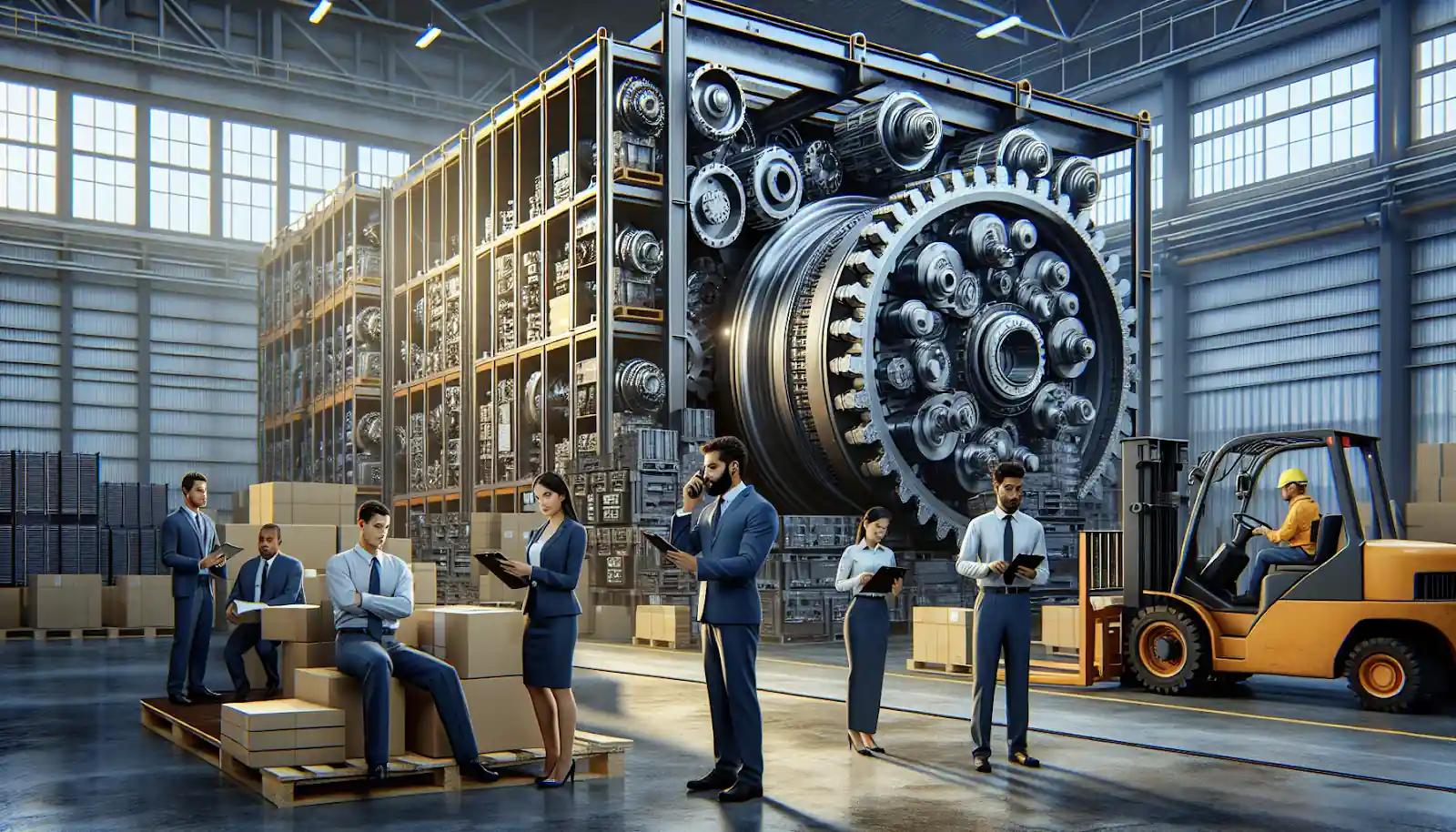
How to Source Mining Machinery Parts: Tips and Strategies
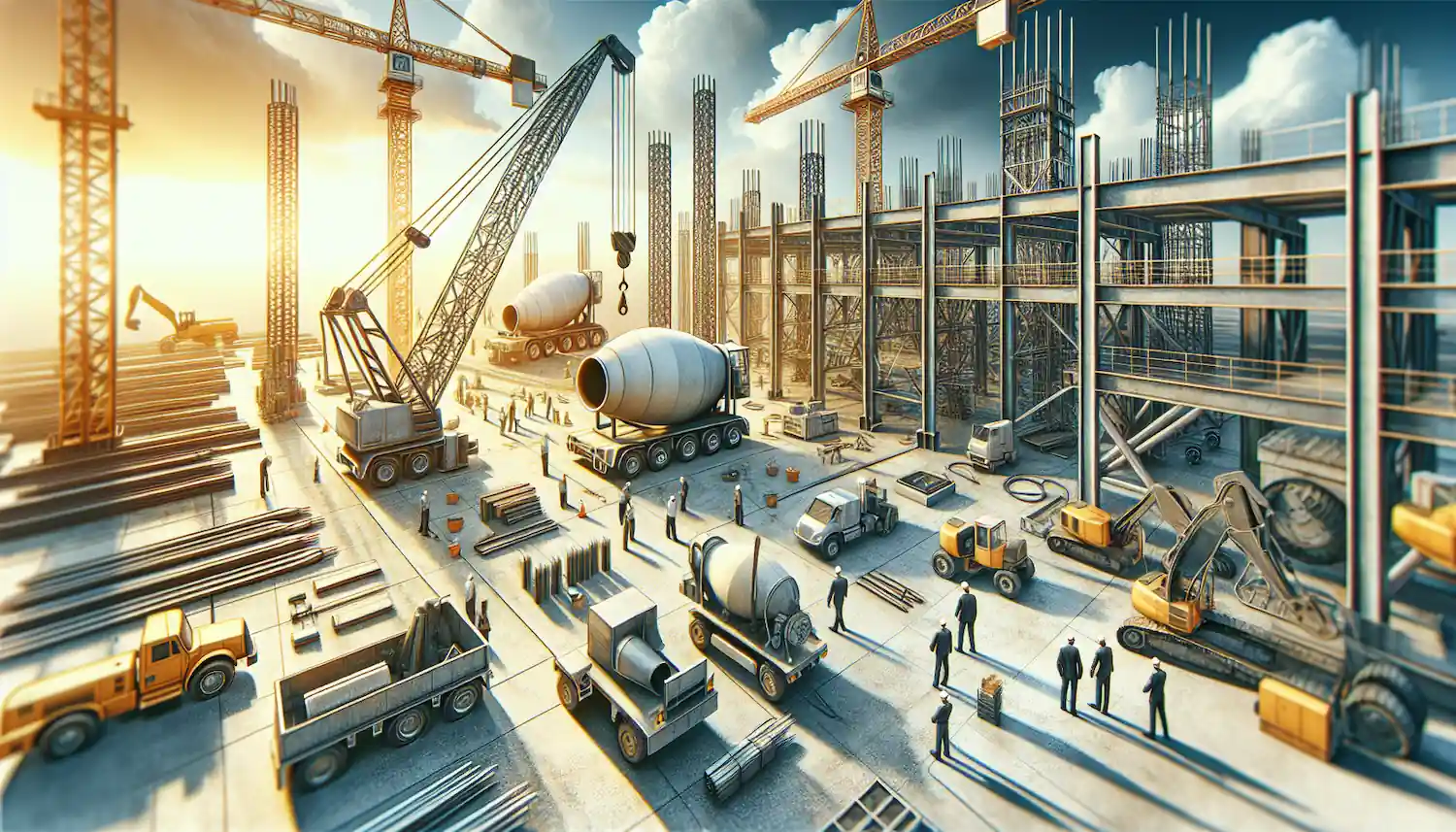