13 Overlooked Farm Spare Parts That Halt Operations — Pt. 2
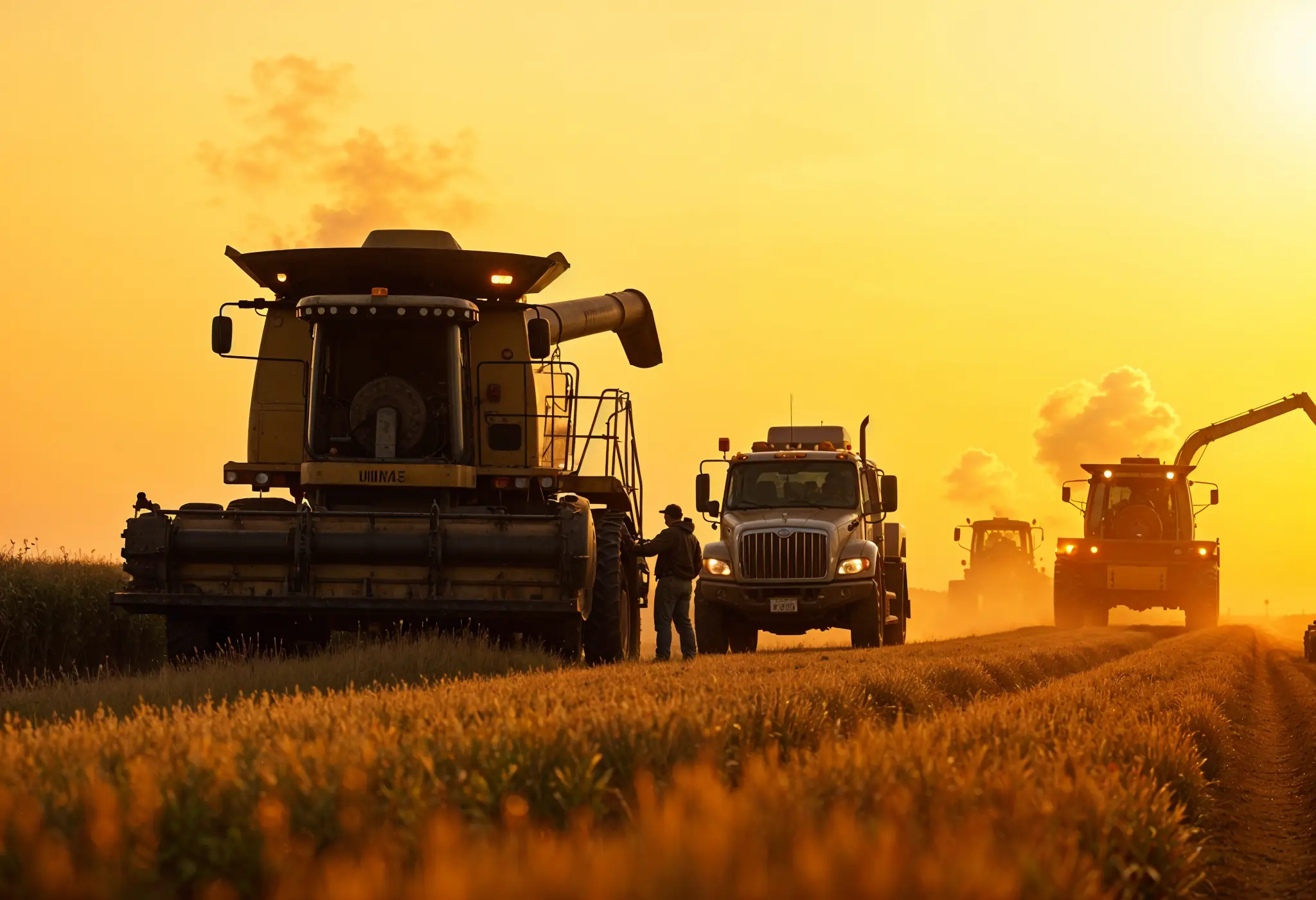
Unexpected downtime during peak fieldwork often comes down to one thing—neglected critical spare parts. From fan belts and ignition switches to radiator caps, wheel bearings, control cables, and glow plugs, these essential components are often overlooked until they fail—and when they do, your entire farm operation stops cold. With the farm equipment spare parts market growing rapidly and supply chains still unstable, having the right spares on hand is no longer optional. This is Part 2 of our essential guide to the 13 most-overlooked critical farm equipment spare parts. If you missed Part 1, be sure to review the first 7 components that keep your machinery running when it matters most.
Fan Belts
Fan belts seem deceptively simple, yet they rank among the most critical components on your farm equipment. These humble rubber loops serve as vital power transfer mechanisms between your engine and cooling systems. When they fail, your busiest work periods transform into costly downtime.
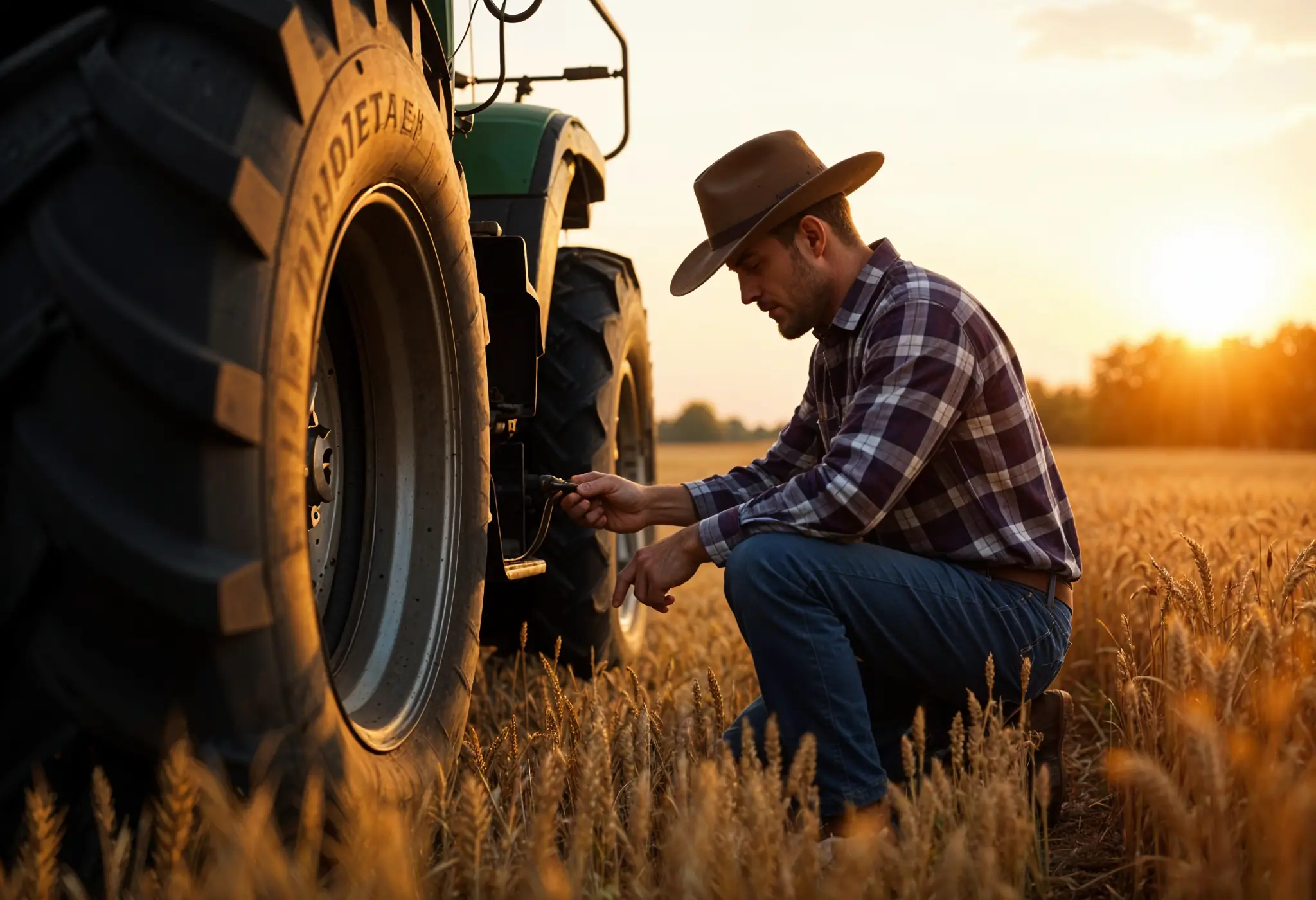
Fan Belts in Engine Cooling
Fan belts transfer power from your engine to both the cooling system and water pump. A properly functioning belt ensures your radiator receives adequate airflow while simultaneously powering the water pump that circulates coolant throughout the system. Nearly all agricultural engines rely on these belt-driven cooling components to prevent overheating during extended field operations.
A correctly tensioned belt maintains optimal engine temperature even under the heaviest loads. To check tension properly, apply about 10 pounds of pressure to the longest section between the alternator and crankshaft pulley—it should deflect approximately 10mm (1/2 inch). This simple check prevents major failures during critical work periods.
Consequences of Fan Belt Breakage
When a belt fails, the problems cascade immediately:
- Engine temperature spikes rapidly as the water pump stops circulating coolant
- Head gasket failure often follows, resulting in repairs that can cost thousands
- Electrical systems fail when alternators stop charging batteries
- Power steering and A/C systems become inoperable on equipment with serpentine belts
Modern tractors typically include electronic sensors that alert you to belt issues, but even a loose belt can lead to engine seizure in extreme cases. One maintenance supervisor noted significantly higher belt replacement rates during rainy seasons, suggesting weather conditions directly affect belt durability.
How to Stock and Replace Fan Belts
Proper belt inventory prevents devastating downtime. Start by documenting exact belt specifications for each piece of equipment—never substitute with incorrect sizes. Inspect belts regularly for warning signs like cracking, missing ribbing, or brittleness.
When replacing belts, loosen the alternator and adjusting link nuts before using a lever to achieve proper tension. Always recheck tension after tightening all mounting bolts. Never apply oil or grease when mounting belts—this practice causes premature failure rather than improving performance.
Implementing a spare parts management process that includes regular belt inspections and inventory tracking can help ensure you always have the right belts on hand when needed. This proactive approach to critical spares management can significantly reduce equipment downtime and improve overall operational efficiency.
Don't let a $20 part cost you a $20,000 harvest. Get expert help sourcing critical spare parts for your farm equipment. Visit MCHPartsNYC.com today for a free consultation and fast, reliable support.
Ignition Switches
The humble ignition switch serves as the gatekeeper to your equipment's entire electrical system. This small component carries outsized responsibility—either allowing your tractor to roar to life or leaving you stranded during critical harvest windows when every minute directly impacts your bottom line.
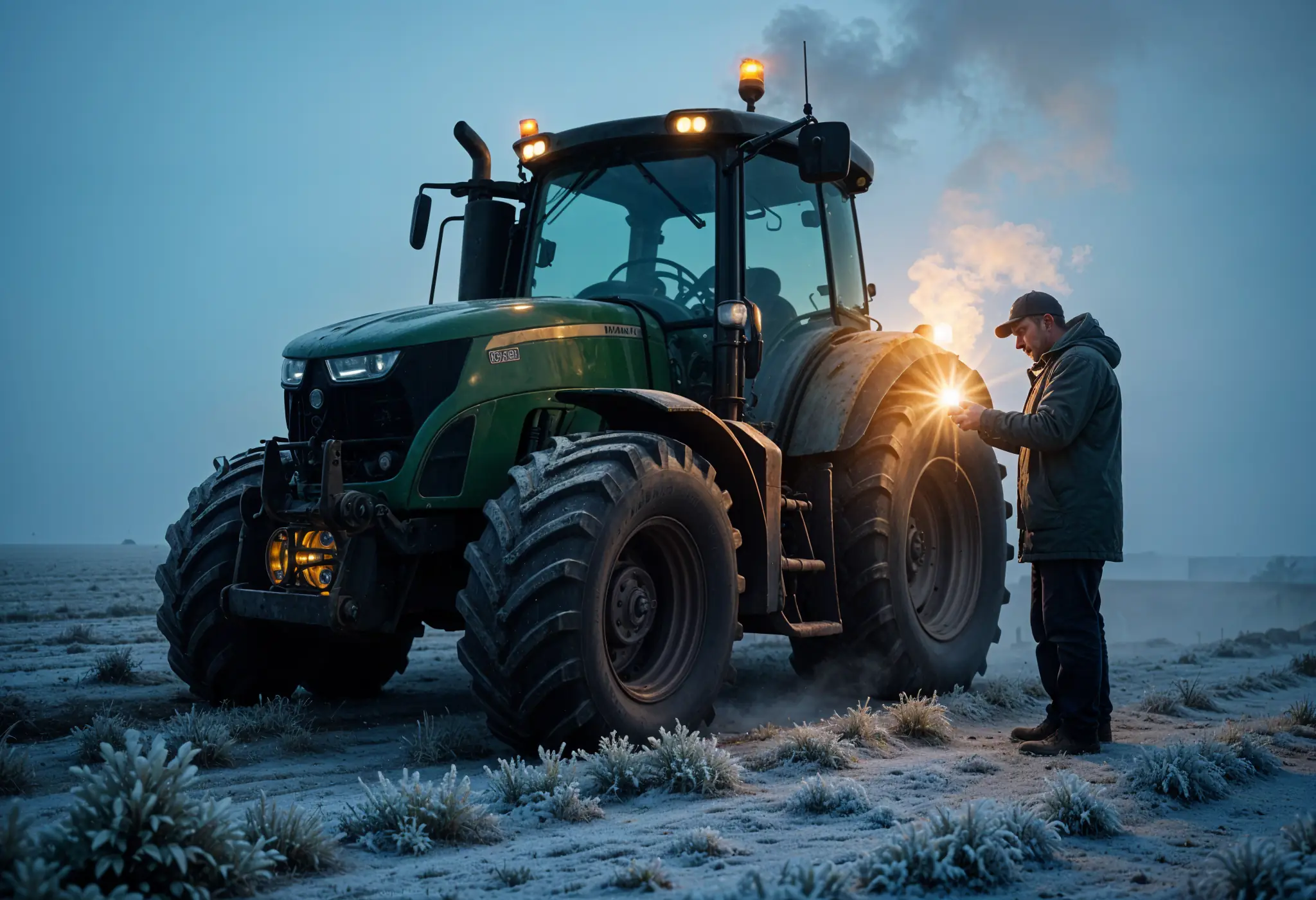
Ignition Switch Function
Turning your equipment key activates a precisely engineered electrical pathway. The ignition switch controls power flow through your tractor's systems, connecting battery power to the starting circuit while managing distribution to lights, accessories, and critical operating components.
When you first turn the key, the switch energizes the electrical system; with further rotation, it engages the starter motor. No matter how well-maintained your other components might be, equipment remains useless without a properly functioning ignition switch. These switches endure thousands of activation cycles while managing substantial electrical loads through multiple operating positions.
Warning Signs of Failing Switches
Your ignition switch will typically signal problems before complete failure occurs:
- Complete silence when turning the key
- Noticeable delay between key turn and starter engagement
- Key feeling unusually loose or sticky in the cylinder
- Accessories and lights receiving no power
- Key wobbling excessively in the switch housing
- Equipment refusing to power down completely
- Switch housing becoming hot to touch, especially during PTO operation
Most failures trace back to three primary causes: worn contact points, aging internal components, or corrosion damage. Farm equipment left exposed to weather elements faces accelerated deterioration as moisture infiltrates switch mechanisms. The resulting corrosion inside switch housings creates resistance points that disrupt electrical flow throughout starting and ignition systems.
Maintaining Ignition Switch Inventory
Smart farmers document exact switch specifications for each piece of equipment. Before attempting replacement, always disconnect the battery and photograph existing wire configurations for reference. Confirm that replacement switches match original specifications precisely—even minor variations can cause fitment problems or electrical incompatibility.
Implementing a comprehensive spare parts management process that includes regular inspections and inventory tracking can help ensure you always have the right ignition switches on hand when needed. This proactive approach to critical spares management can significantly reduce equipment downtime and improve overall operational efficiency.
Radiator Caps
That unassuming metal cap atop your tractor's radiator does far more than simply cover an opening. This precision-engineered component regulates your entire cooling system—its failure can transform a productive field day into costly downtime within minutes. Many farmers mistakenly view radiator caps as basic parts rather than the critical pressure regulators they truly are.
Radiator Cap Function
Radiator caps maintain precise pressure within your cooling system while providing controlled release of excess heat. Each cap raises coolant's boiling point by approximately 3°F for every psi of pressure added to the system. Under typical farm equipment conditions, a standard 15 psi cap elevates water's boiling point from 212°F to around 257°F—a significant difference that prevents vapor lock during heavy workloads.
The cap's spring-loaded valve opens at a predetermined pressure point, directing excess coolant into an overflow reservoir rather than onto your engine. As your tractor cools after shutdown, the vacuum valve within the cap pulls coolant back from the reservoir into the radiator, maintaining proper fluid levels without manual intervention. This continuous regulation occurs through countless pressure cycles throughout each working day.
Why Radiator Caps Matter
The importance of proper radiator cap function extends far beyond keeping coolant inside your system. Without adequate pressure, coolant boils prematurely, creating vapor pockets that slash cooling efficiency by 97%—essentially rendering your cooling system useless. Pressurized systems enable modern farm equipment to operate at the higher temperatures necessary for optimal fuel efficiency and power output.
Different equipment requires specific pressure ratings—most agricultural tractors use caps ranging from 13-16 psi, precisely calibrated to manufacturer specifications. Using incorrect pressure ratings leads to serious mechanical problems. Too low, and your coolant boils away; too high, and your hoses may burst under excessive pressure. Even a small variation of 2-3 psi can dramatically affect system performance during extended operations.
Signs of Radiator Cap Failure
Smart farmers watch for these telltale symptoms of radiator cap problems:
- Coolant repeatedly leaking from overflow tubes indicates worn seals or stuck pressure valves that can't maintain proper system pressure
- Burst or collapsed radiator hoses result from either excessive pressure buildup or improper vacuum release during cooling
- Coolant levels dropping gradually without visible leaks often points to caps releasing pressure prematurely
- Engine overheating during normal operations or even idling suggests pressure loss through the cap
In one documented case, a faulty radiator cap allowed coolant to escape so gradually that the farmer noticed no visible leaks. The slow evaporation eventually caused catastrophic overheating during soil preparation, resulting in three days of downtime during optimal planting conditions.
Implementing a comprehensive spare parts management process that includes regular inspections and inventory tracking can help ensure you always have the right radiator caps on hand when needed. This proactive approach to critical spares management can significantly reduce equipment downtime and improve overall operational efficiency.
Wheel Bearings
Tapered roller bearings form the silent backbone of your wheeled farm equipment. These small components shoulder tremendous loads while enabling smooth rotation—their failure instantly transforms your powerful tractor into an expensive, immobile obstacle in your field.
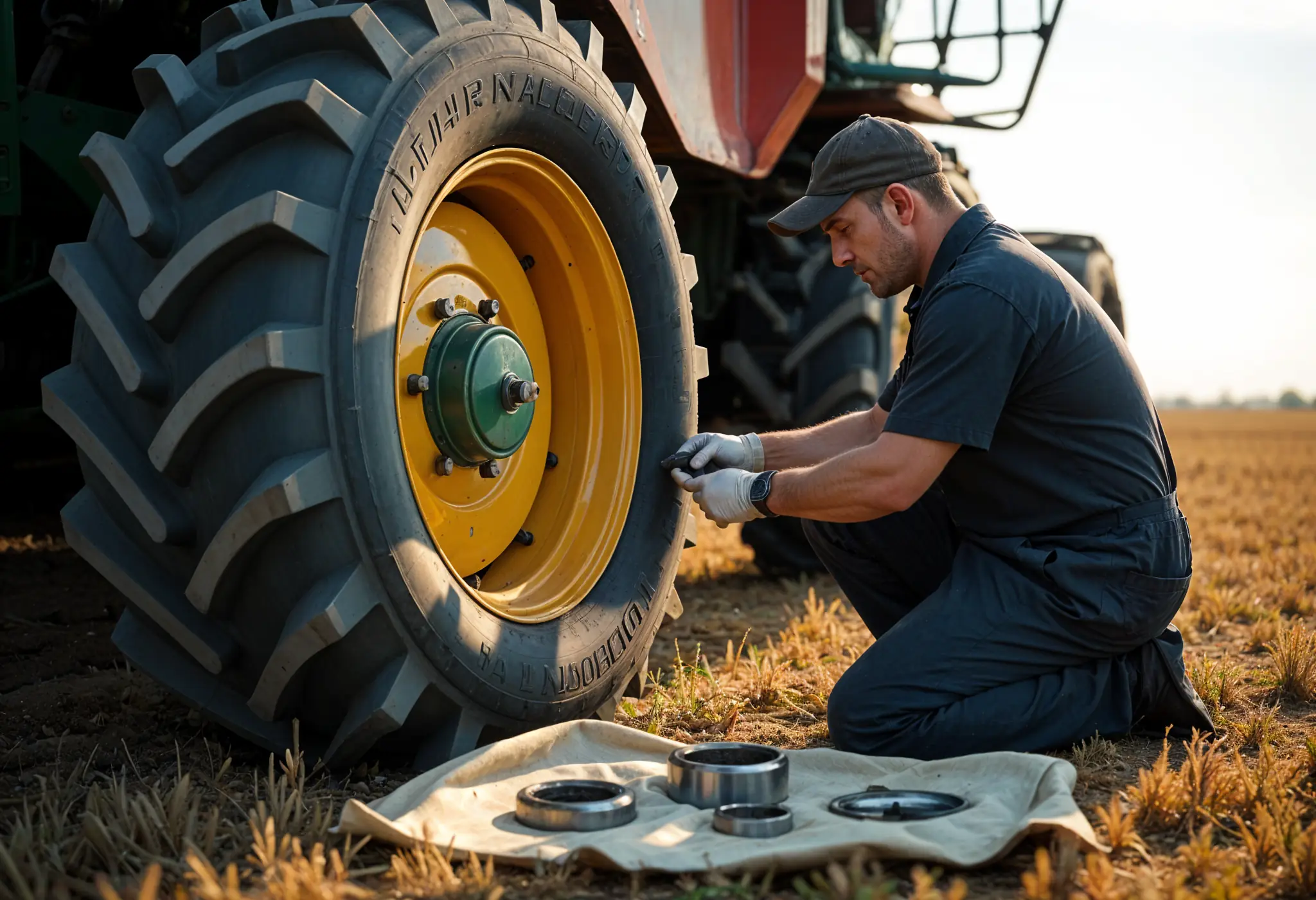
Wheel Bearings and Load Support
Wheel bearings handle both radial and thrust forces your equipment encounters daily. These precision-engineered components support your tractor's entire weight while allowing hub assemblies to rotate freely. During operation, they distribute load evenly across roller surfaces, maintaining optimal wheel movement under significant pressure. A properly functioning bearing withstands hundreds of thousands of miles of service. Yet many farmers overlook these critical parts until equipment suddenly fails at the worst possible moment.
Warning Signs That Demand Attention
Failing bearings rarely announce their deterioration with dramatic symptoms. At most, you'll notice a subtle grinding or grating noise that's easy to dismiss. This oversight proves costly. Damaged bearings increase your fuel costs, reduce stopping capability, and create dangerous loose steering response.
In severe cases, a completely failed bearing disintegrates and damages the entire final drive assembly, creating expensive repair bills and extended downtime. One farmer learned this lesson the hard way when parts shortages turned a simple bearing failure into a two-month equipment disability. The financial impact extends far beyond the bearing's modest price.
Three Keys to Maximum Bearing Life
Proper bearing maintenance hinges on three fundamental principles: cleanliness, correct lubrication, and proper preload adjustment.
Contamination ranks as the leading cause of bearing failure. Always leave new bearings in their original packaging until installation, and replace wheel seals at the first sign of failure. This simple precaution prevents most premature failures.
Use only manufacturer-recommended grease types. Different colored greases (black, red, honey-colored) should never be mixed, as incompatible formulations accelerate deterioration.
Setting correct preload proves critical—the difference between too loose and too tight measures merely 0.001 to 0.005 inch. Check for excessive play by lifting the wheel and testing for movement at the 12 and 6 o'clock positions. This quick inspection reveals problems before they become catastrophic.
Implementing a comprehensive spare parts management process that includes regular inspections and inventory tracking can help ensure you always have the right wheel bearings on hand when needed. This proactive approach to critical spares management can significantly reduce equipment downtime and improve overall operational efficiency.
Your equipment is only as reliable as your inventory. Ensure you have the right belts, bearings, glow plugs, and more—before they fail. Start building your custom spare parts plan at MCHPartsNYC.com.
Control Cables
Control cables represent the nervous system of your farm equipment. These critical components translate your commands into mechanical action—connecting your intentions directly to machine performance. When cables fail, even the most powerful tractors become useless hunks of metal sitting idle during your busiest seasons.
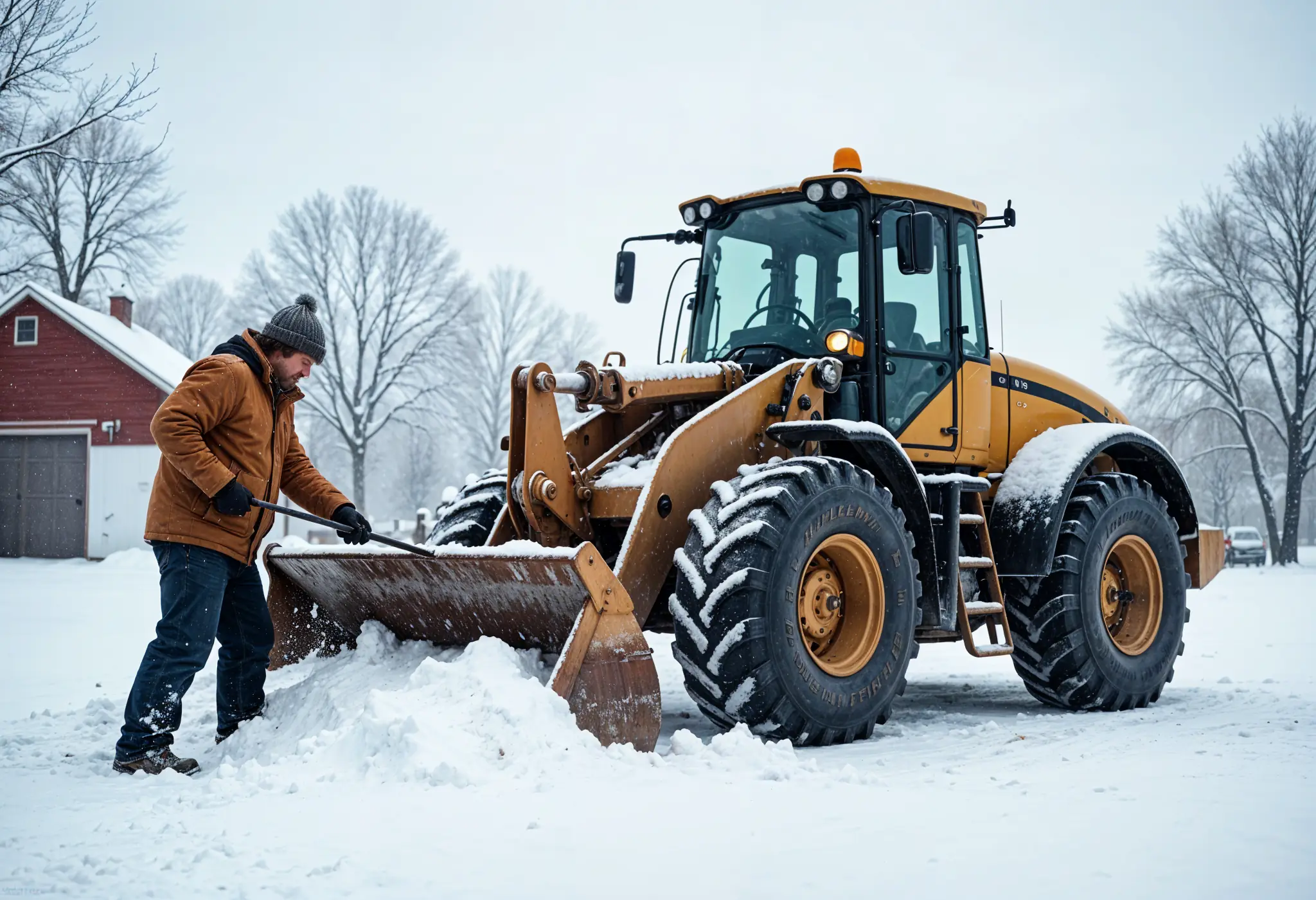
Control Cables in Equipment Operation
Control cables transmit mechanical force throughout your equipment, enabling precise management of various functions. At their core, these components consist of inner steel wires protected by durable sheaths, designed specifically to transfer movement in systems requiring accurate control.
For precision equipment like automated planters and harvesters, control cables determine the accuracy of seed placement and cutting height. Loader control cables connect joystick movements to hydraulic valves, providing the tactile feedback needed for bucket positioning. These modest components create the direct connection between your hands and your equipment's actions—from throttle adjustments to complex hydraulic operations.
Failure Risks and Symptoms
Watch for these warning signals that indicate deteriorating control cables:
- Roughness or sticking during operation suggests internal cable binding
- Slow or unresponsive functions often signal cables not traveling their full distance
- Complete function loss typically indicates core breakage from misalignment or wear
- Freezing cables in winter conditions can render loaders entirely unusable
Most cable failures stem from specific causes. Improper installation frequently results in cores working out of alignment with conduit terminals, creating unnecessary friction. When seals become damaged, dirt and moisture enter the cable housing, causing components to stick or break. One farmer discovered this the hard way when loader cables froze beneath his cab—requiring costly removal for replacement.
Replacement and Stocking Tips
For effective cable management, establish regular inspection intervals based on how frequently you use each piece of equipment. Keep spare cables for critical functions—clutch, throttle, and loader operations deserve priority in your inventory. When replacing cables, ensure proper routing with the largest possible bend radius to maximize service life.
Implementing a comprehensive spare parts management process that includes regular inspections and inventory tracking can help ensure you always have the right control cables on hand when needed. This proactive approach to critical spares management can significantly reduce equipment downtime and improve overall operational efficiency.
Glow Plugs (for Diesel Engines)
Miniature heating elements that make cold-weather operation possible, glow plugs rank among the most misunderstood yet vital components in diesel farm equipment. When winter temperatures plummet, these small parts determine whether your tractor starts promptly or sits uselessly in the barn while critical work waits.
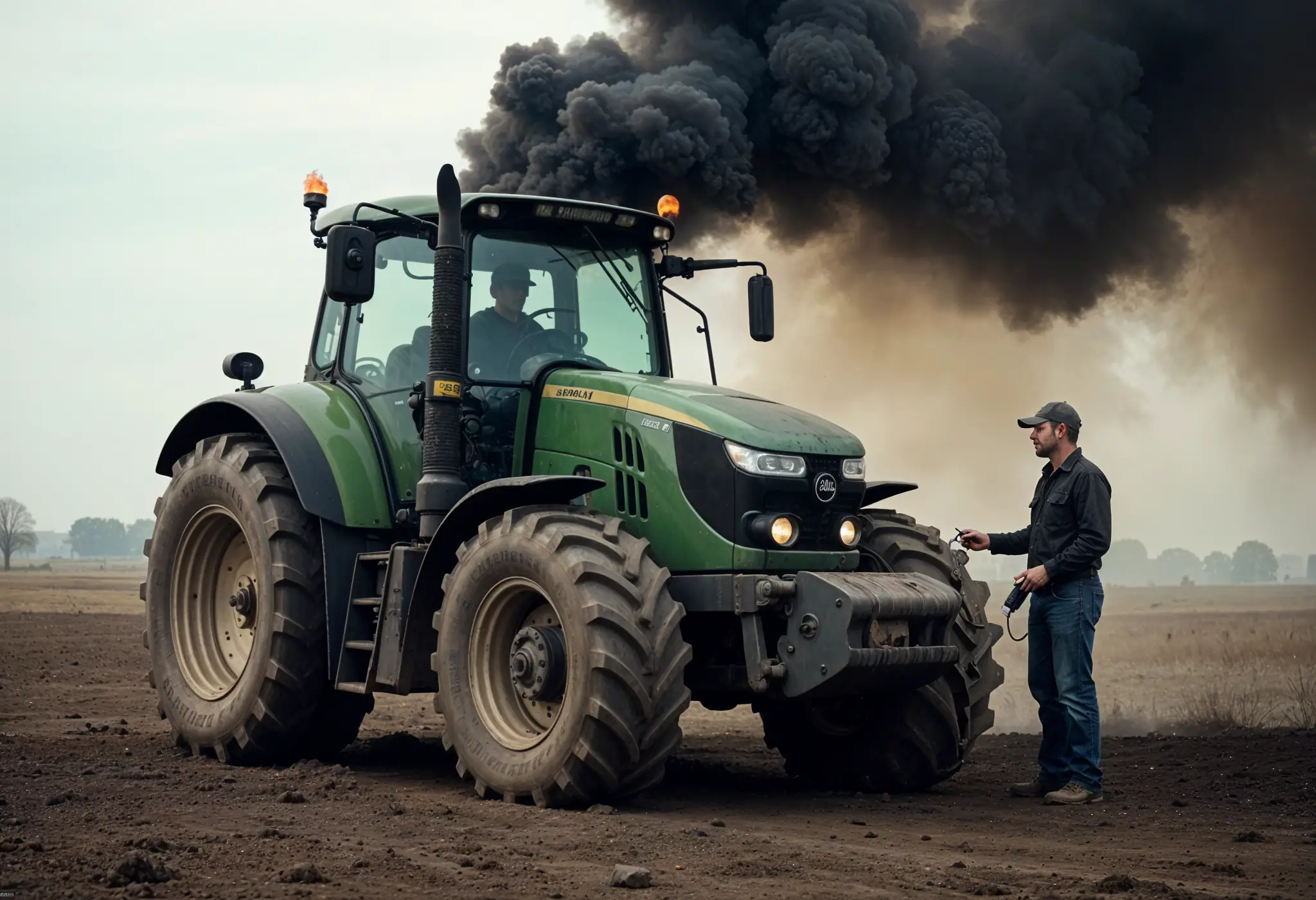
How Glow Plugs Enable Cold-Weather Starts
Unlike gasoline engines with their spark plugs, diesel engines rely entirely on compression heat for ignition. Glow plugs bridge the gap when ambient temperatures make normal compression ignition difficult. Each plug contains a heating element that reaches nearly 1,900°F in under two seconds, creating the conditions necessary for diesel fuel to ignite in cold cylinders.
The heating time varies with conditions—typically 5-10 seconds in mild weather but extending to 10-20 seconds during severe cold. This brief warm-up period determines whether your morning starts with productivity or frustration. Once activated, glow plugs create a high-temperature zone where atomized fuel contacts the hot tip, enabling combustion to begin when cold metal surfaces would otherwise absorb critical heat.
Warning Signs of Glow Plug Failure
Failed glow plugs create immediate operational problems that directly impact your productivity:
- Cold engines that crank but refuse to start during winter months
- Extended cranking periods that drain batteries and test your patience
- Rough idling immediately after cold starts
- Black smoke pouring from the exhaust during warm-up
- Increased fuel consumption during initial operation
- Intermittent starting issues that worsen as temperatures drop
The cost of replacing these small components pales compared to the operational losses from equipment that won't start during critical winter work periods. A single morning of downtime during livestock feeding or snow clearing operations quickly exceeds the price of maintaining proper spare parts inventory.
Proper Maintenance and Replacement
Checking glow plug functionality before cold weather arrives prevents costly surprises. Test suspected plugs using a multimeter—most function properly when resistance measures between 0.1 and 6 Ohms. When replacement becomes necessary, always disconnect the battery first to prevent electrical system damage.
Before installing new plugs, apply a small amount of anti-seize compound to the threads. This simple step prevents seizing and facilitates future replacements. Take care during removal, as glow plugs can break off in the cylinder head—creating an exponentially larger repair job. When possible, remove plugs when the engine is warm after applying penetrating oil to stubborn units.
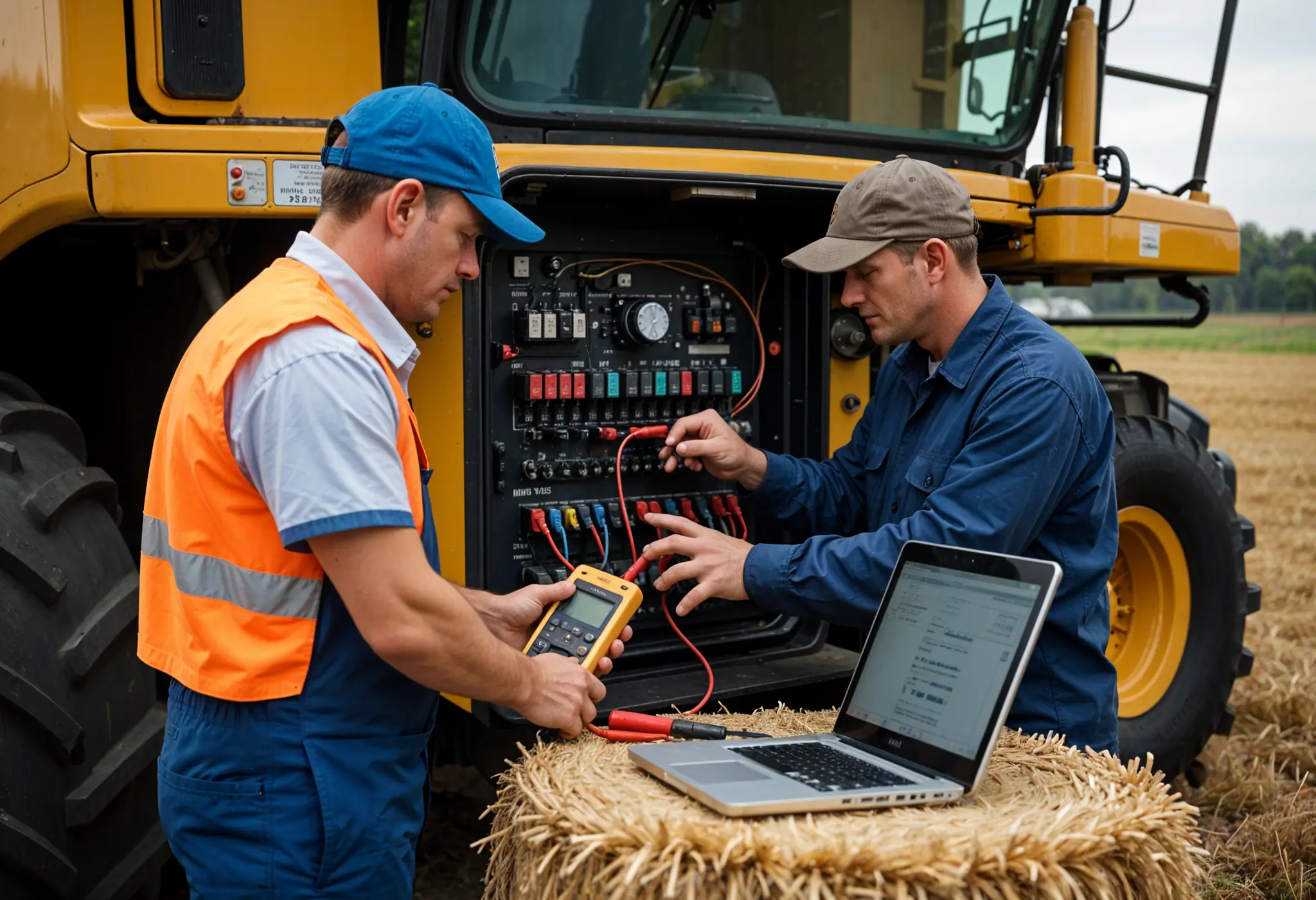
Avoid downtime during your busiest season. From ignition switches to hydraulic hoses, MCH Parts helps you stock what matters most. Request a no-obligation quote now at MCHPartsNYC.com.
Conclusion
Even the most powerful farm equipment is only as reliable as its smallest spare parts. Fan belts, ignition switches, radiator caps, wheel bearings, control cables, and glow plugs often fail without warning—bringing your operations to a sudden halt. With the farm equipment spare parts market expanding and supply chains strained, smart inventory management is critical. Don’t let overlooked components cause costly downtime during harvest, planting, or winter prep. A proactive approach to critical spares can protect your uptime, extend equipment life, and save thousands in emergency repairs.
Secure your essential farm equipment spare parts now at MCHPartsNYC.com. Request a free consultation and a quote—keep your machines moving when it matters most.
Read More
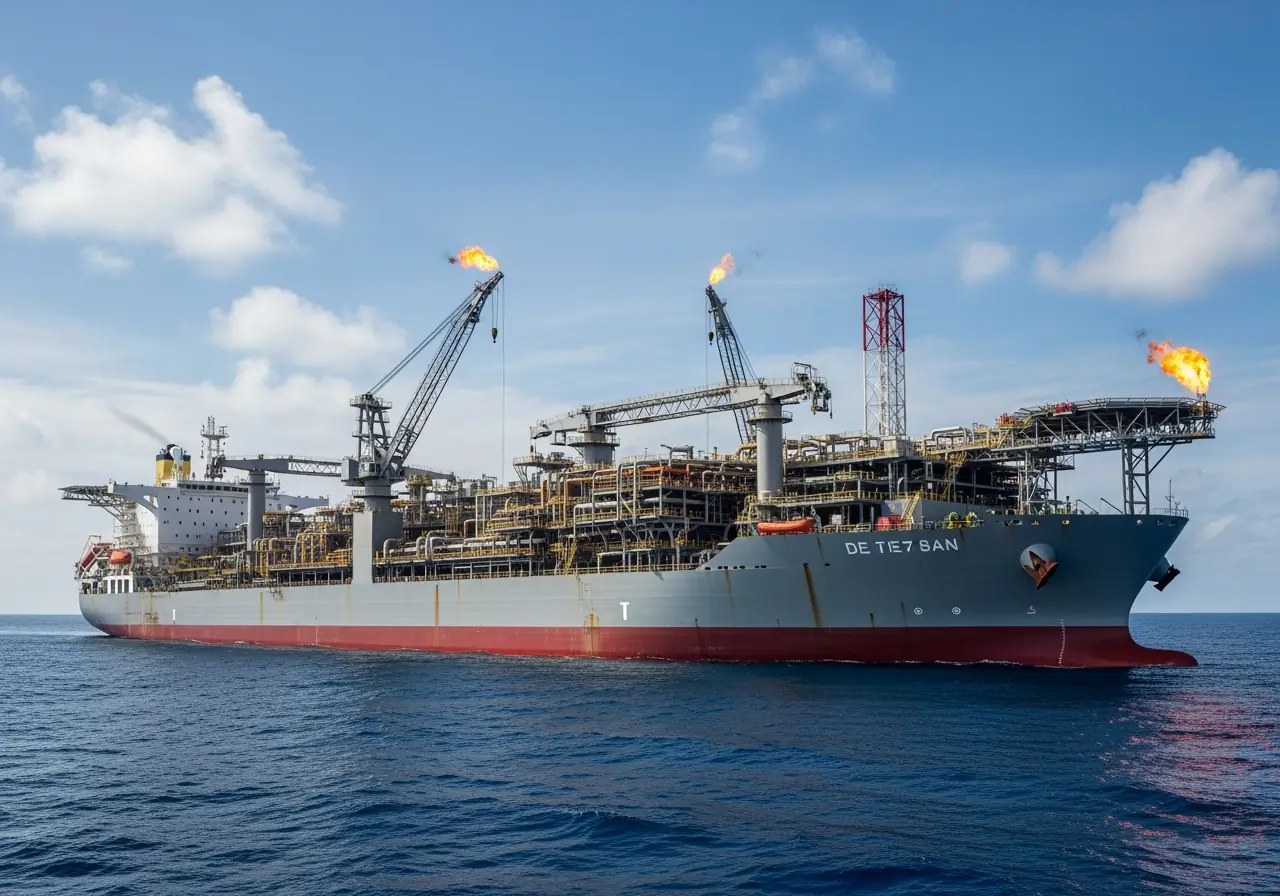
FPSO Smart Parts Planning: Proven Methods to Cut Downtime
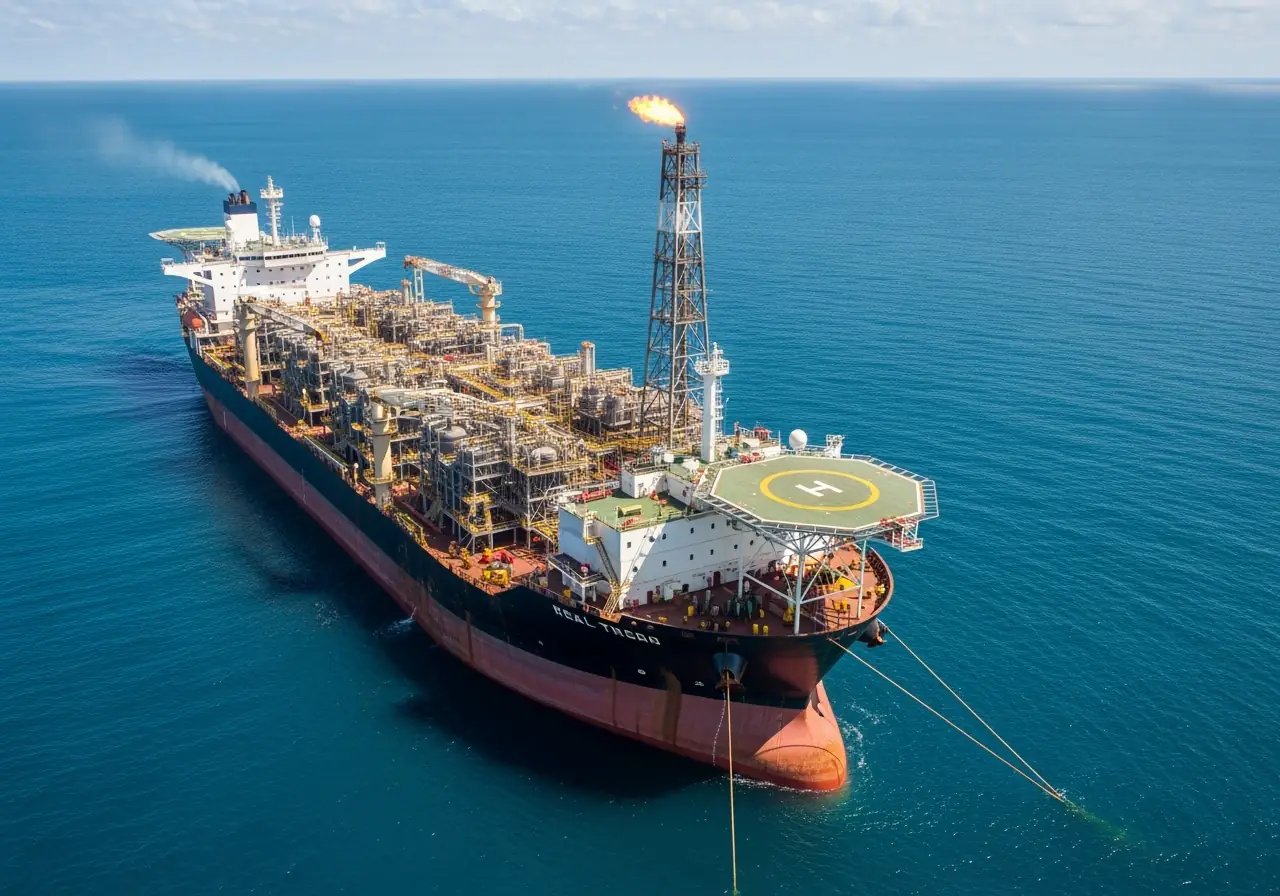
How FPSO Inspection Prevents Million-Dollar Shutdown Losses
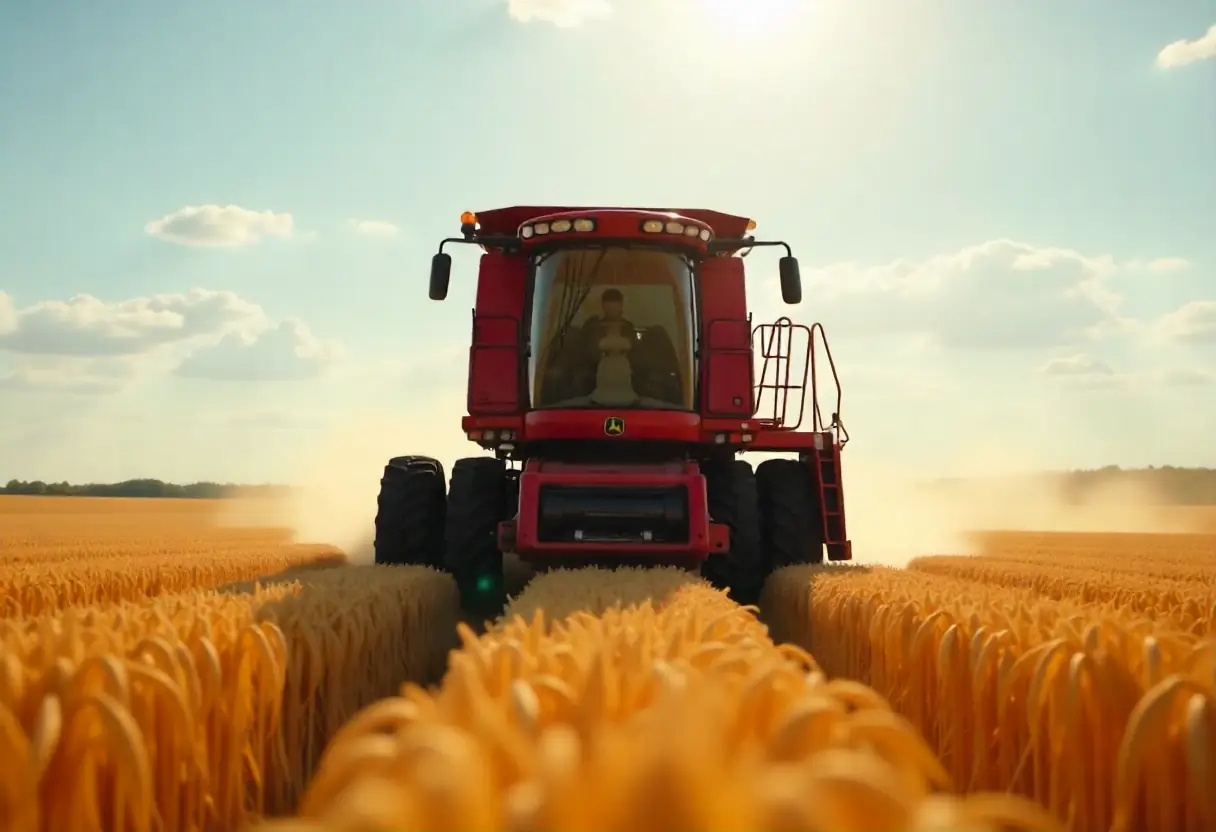
Fix It Before It Breaks: A Farmer's Guide to Combine and Harvester Maintenance
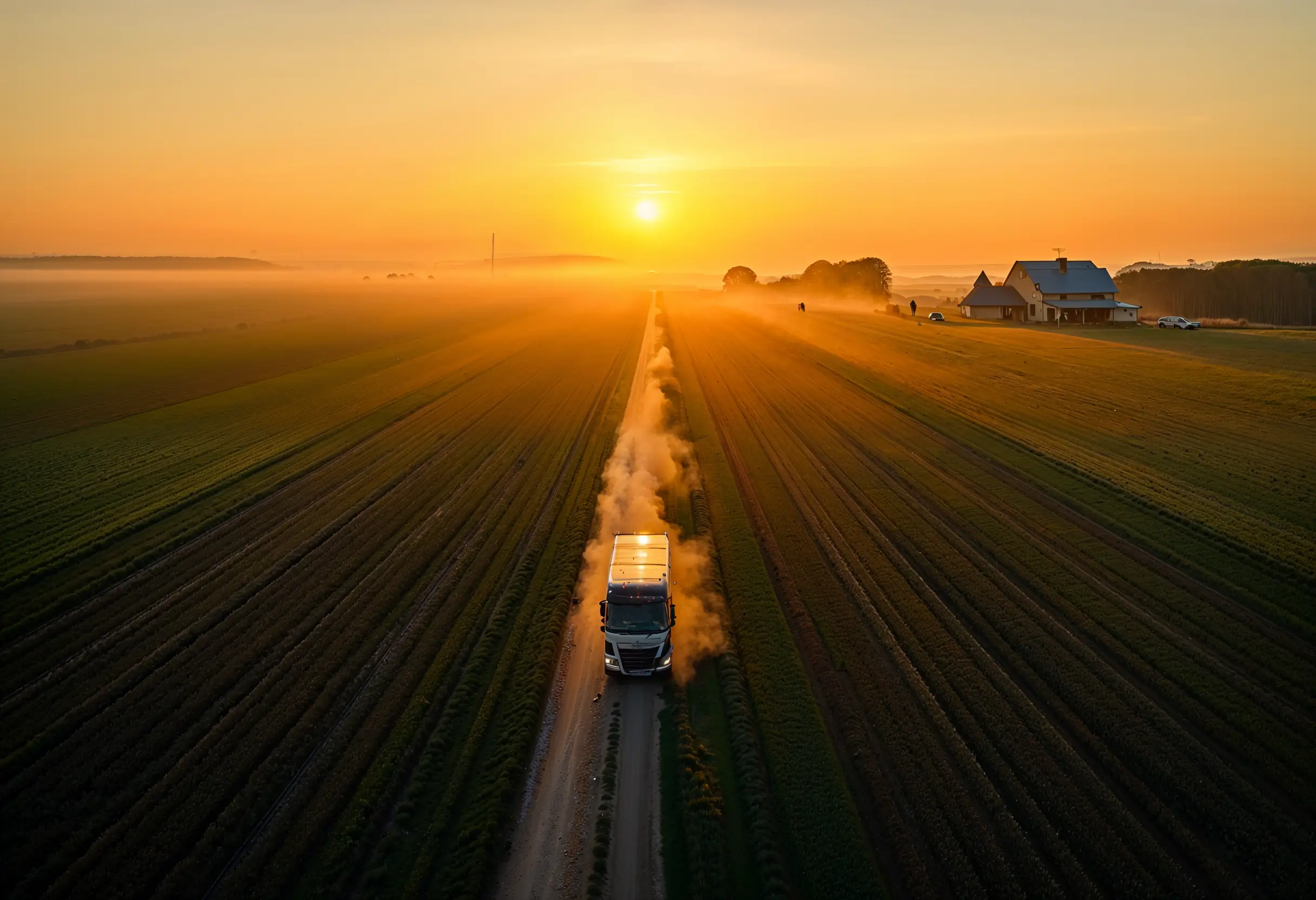
Why Fast Tractor Parts Delivery is Changing Modern Farming [2025 Guide]
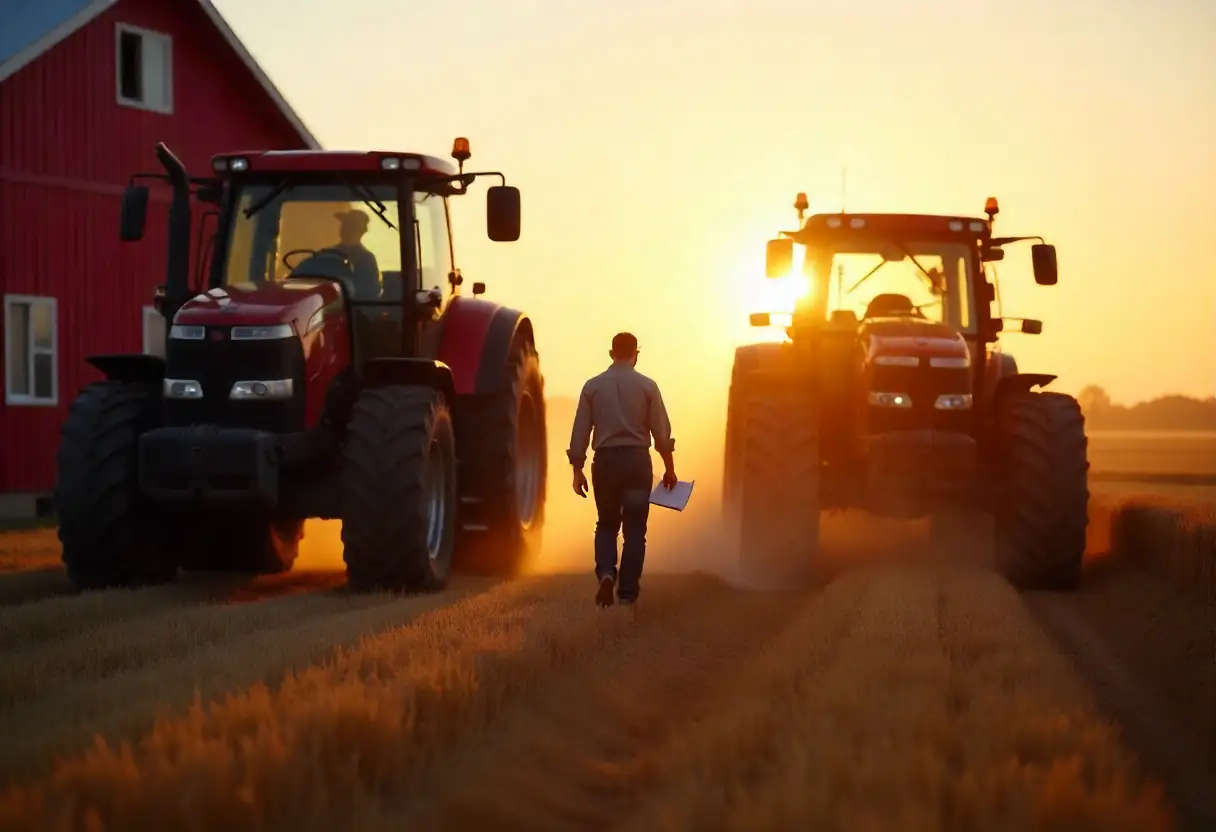
The Critical Farm Equipment Replacement Parts You Need Before Harvest 2025
.webp)
How to Double Your Farm Efficiency: Expert Guide to Smart Scaling
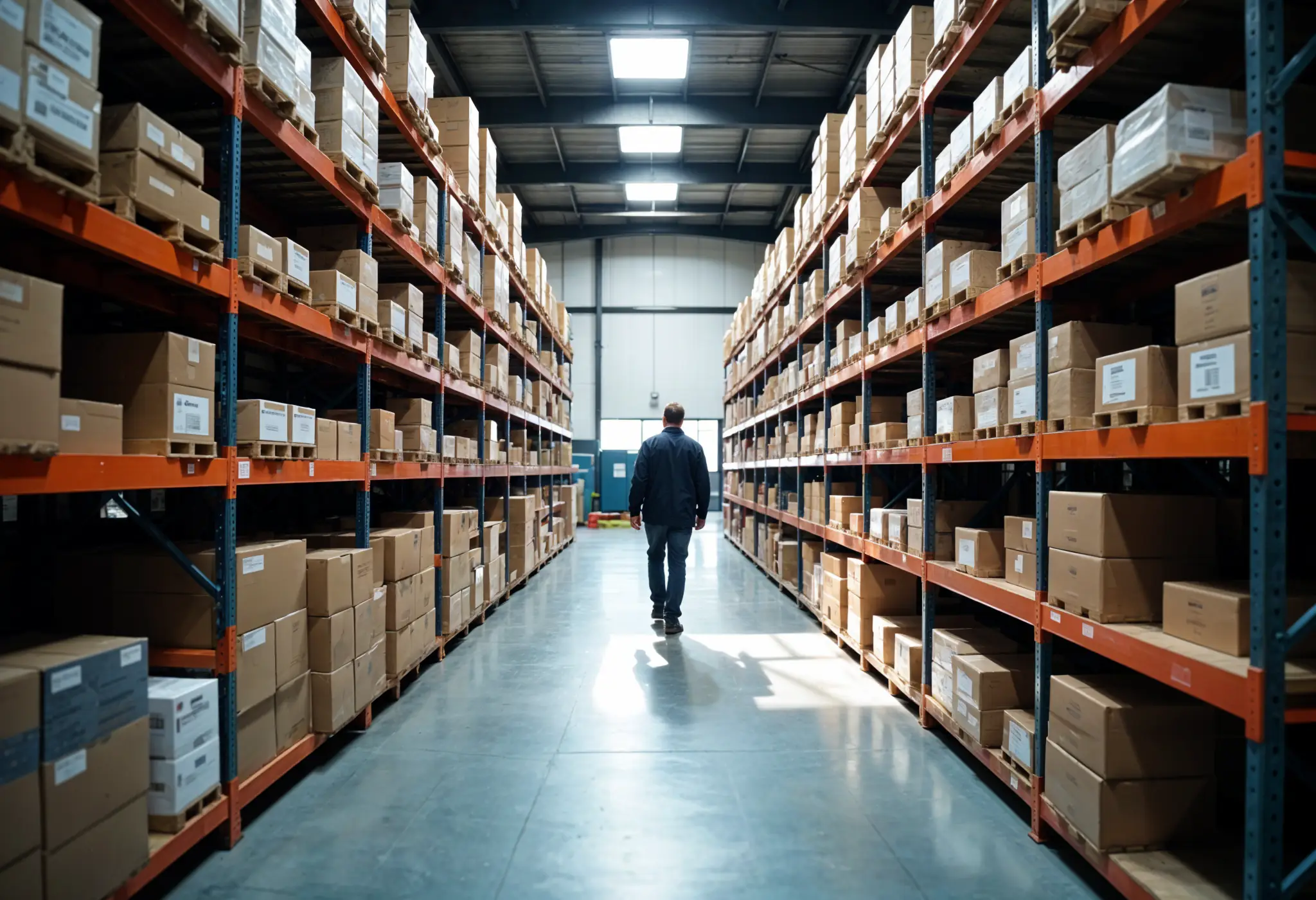
Cut Costs by 30%: Pre-Season Spare Parts Audit Checklist

Proven Success Factors for Agricultural Equipment Manufacturers in 2025
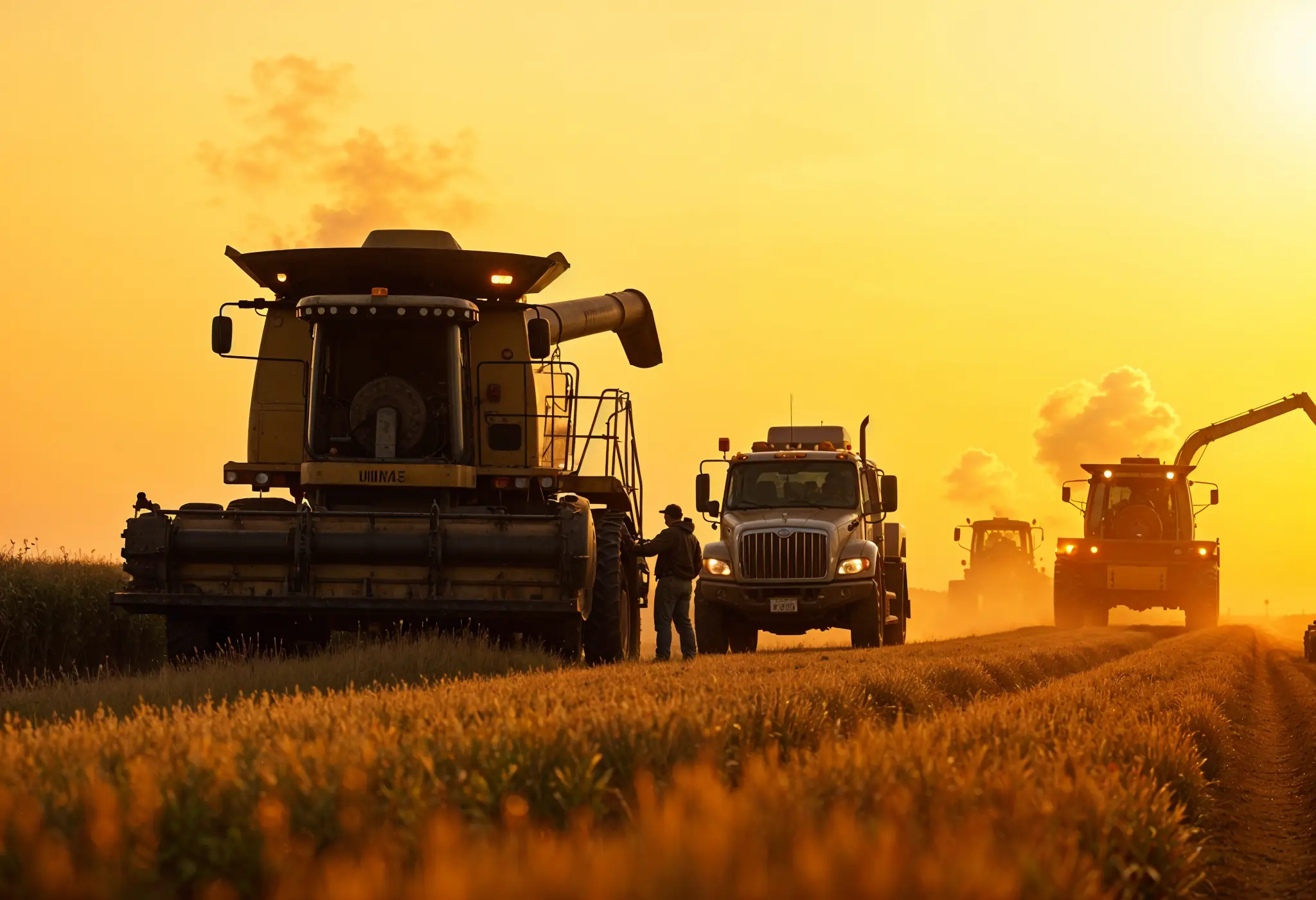
13 Overlooked Farm Spare Parts That Halt Operations — Pt. 2
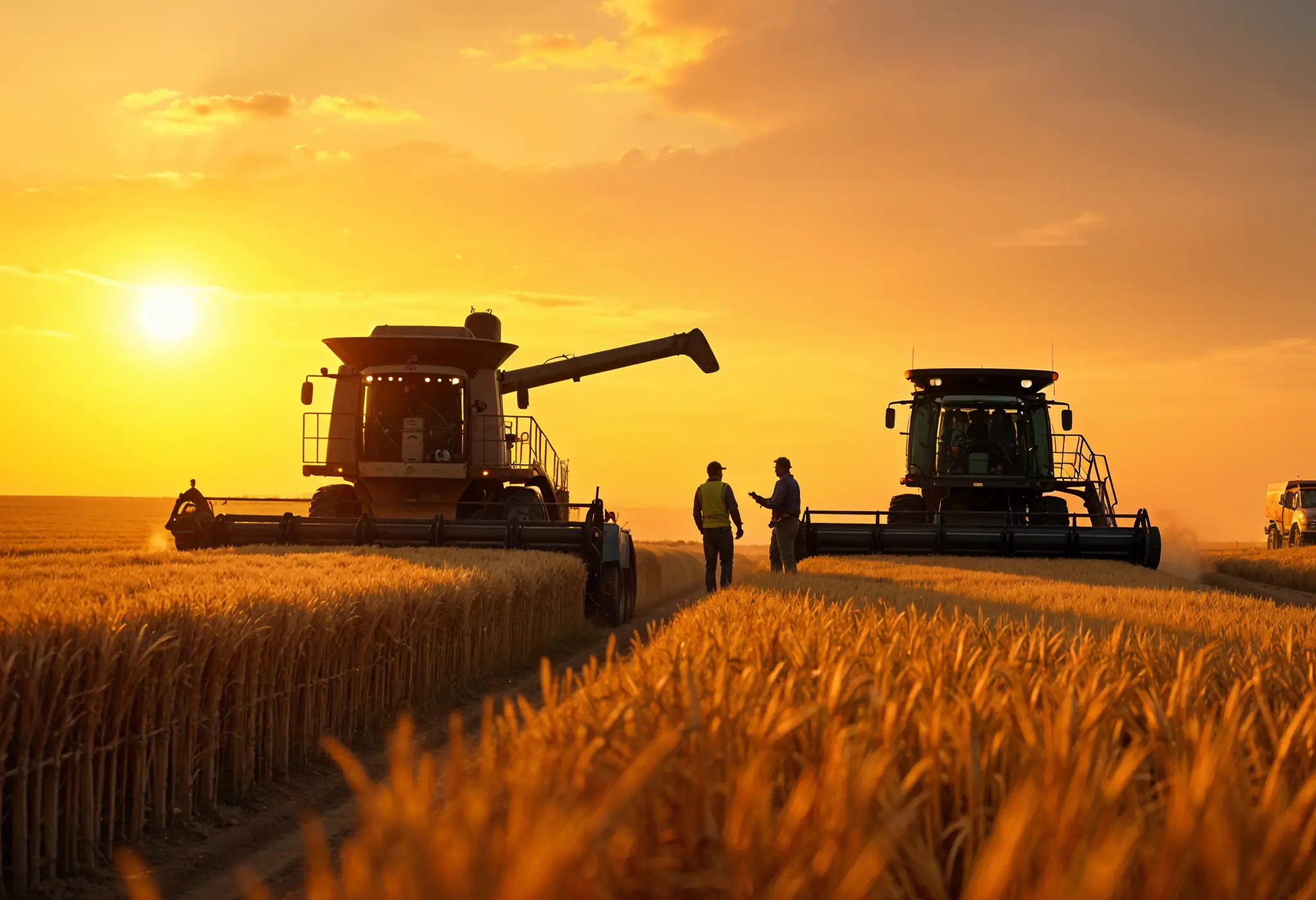
13 Overlooked Farm Spare Parts That Halt Operations — Pt. 1
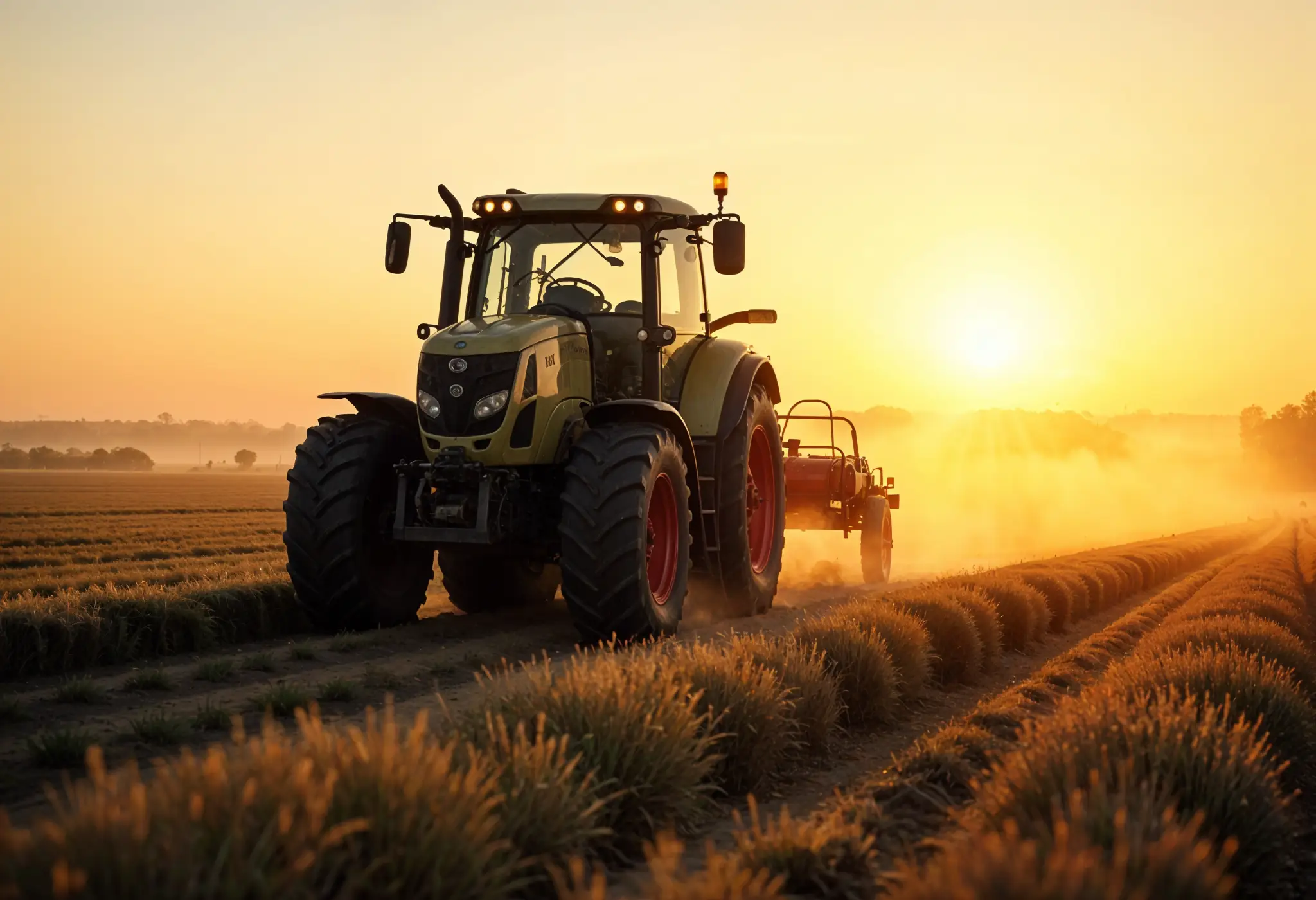
Top Hydraulic Components for Agricultural Equipment in 2025: Complete Guide
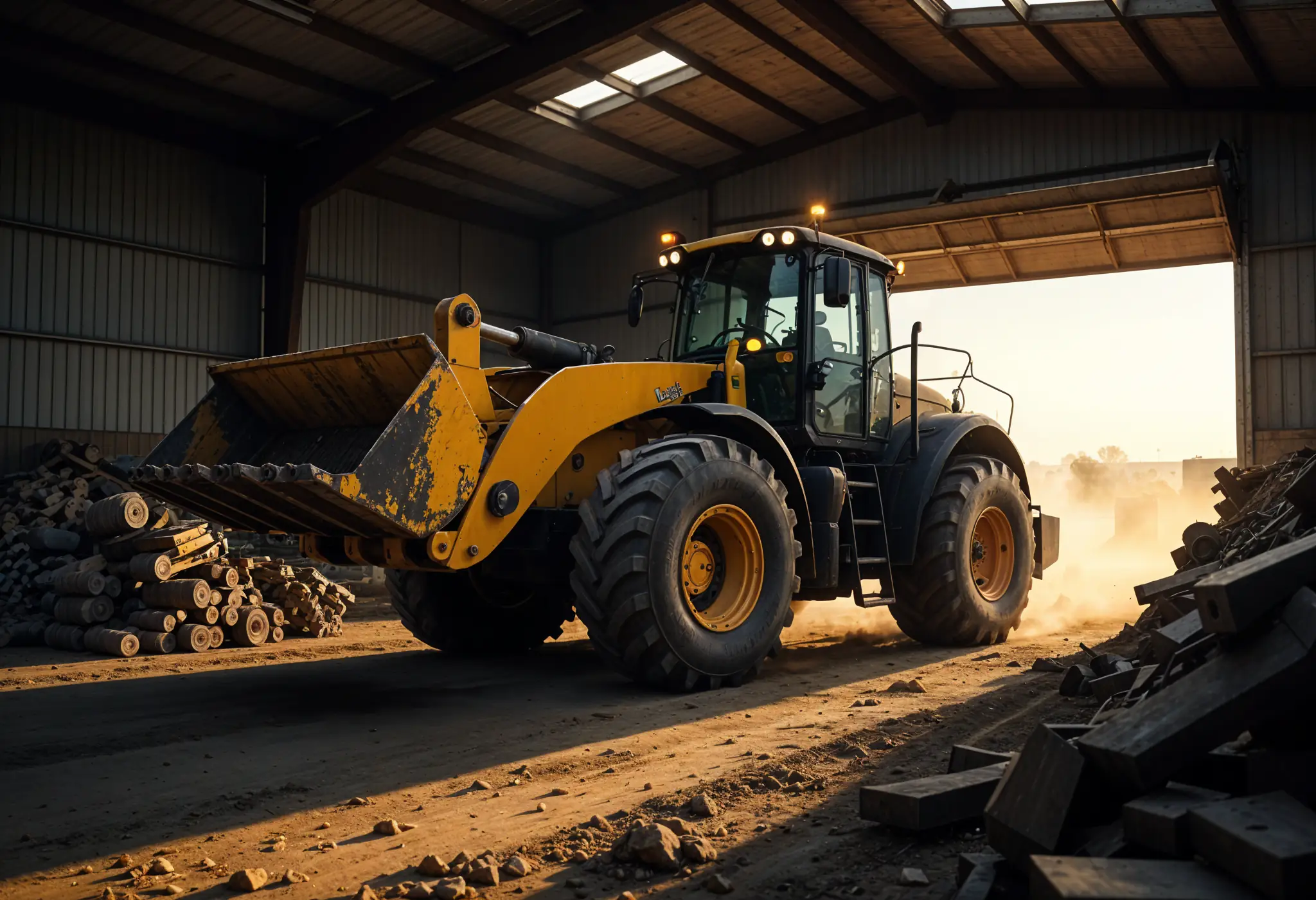
The Essential Farm Equipment Parts You Can't Afford to Run Out Of
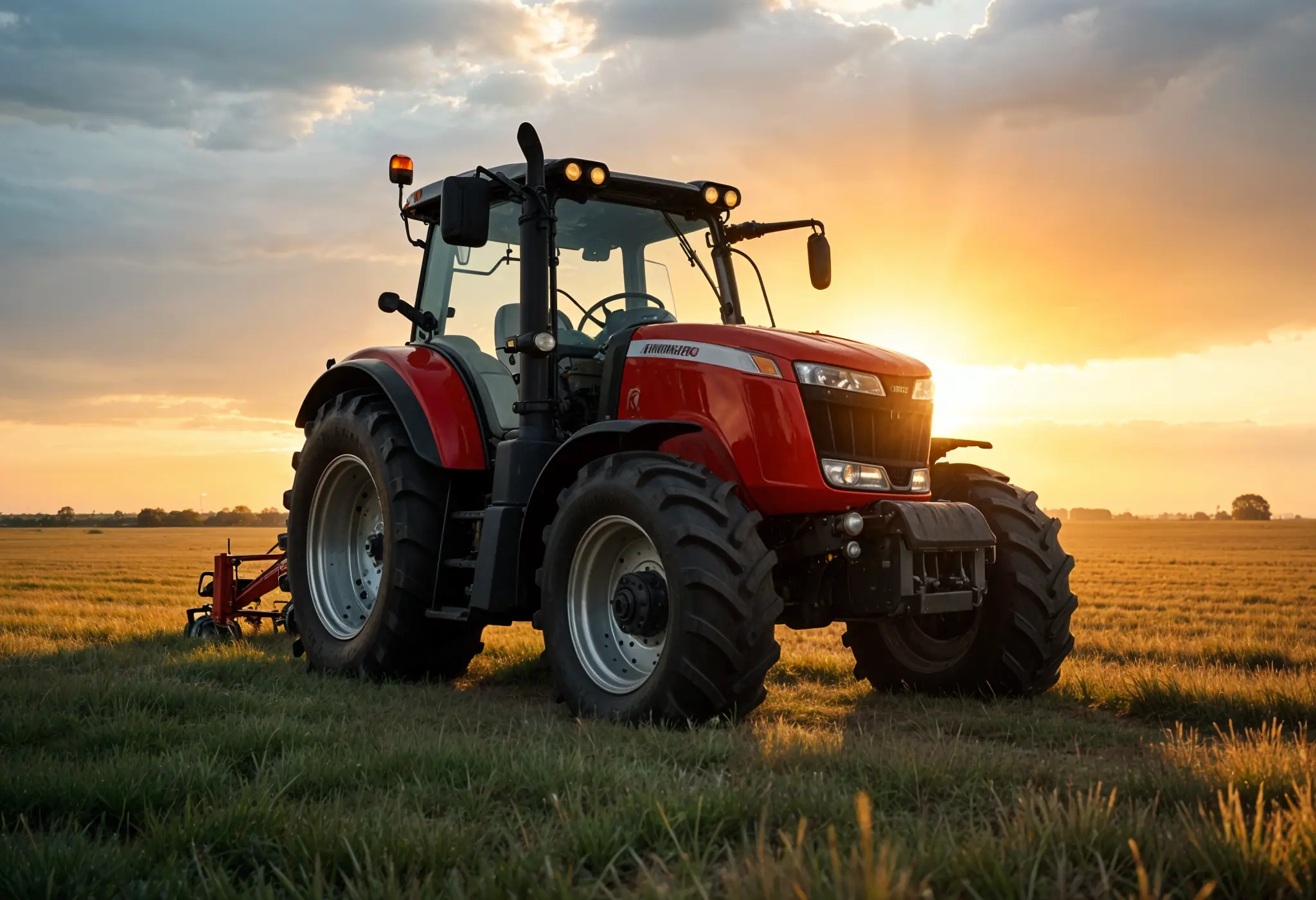
How to Service Farm Equipment: A Farmer's Guide to Zero Harvest Downtime
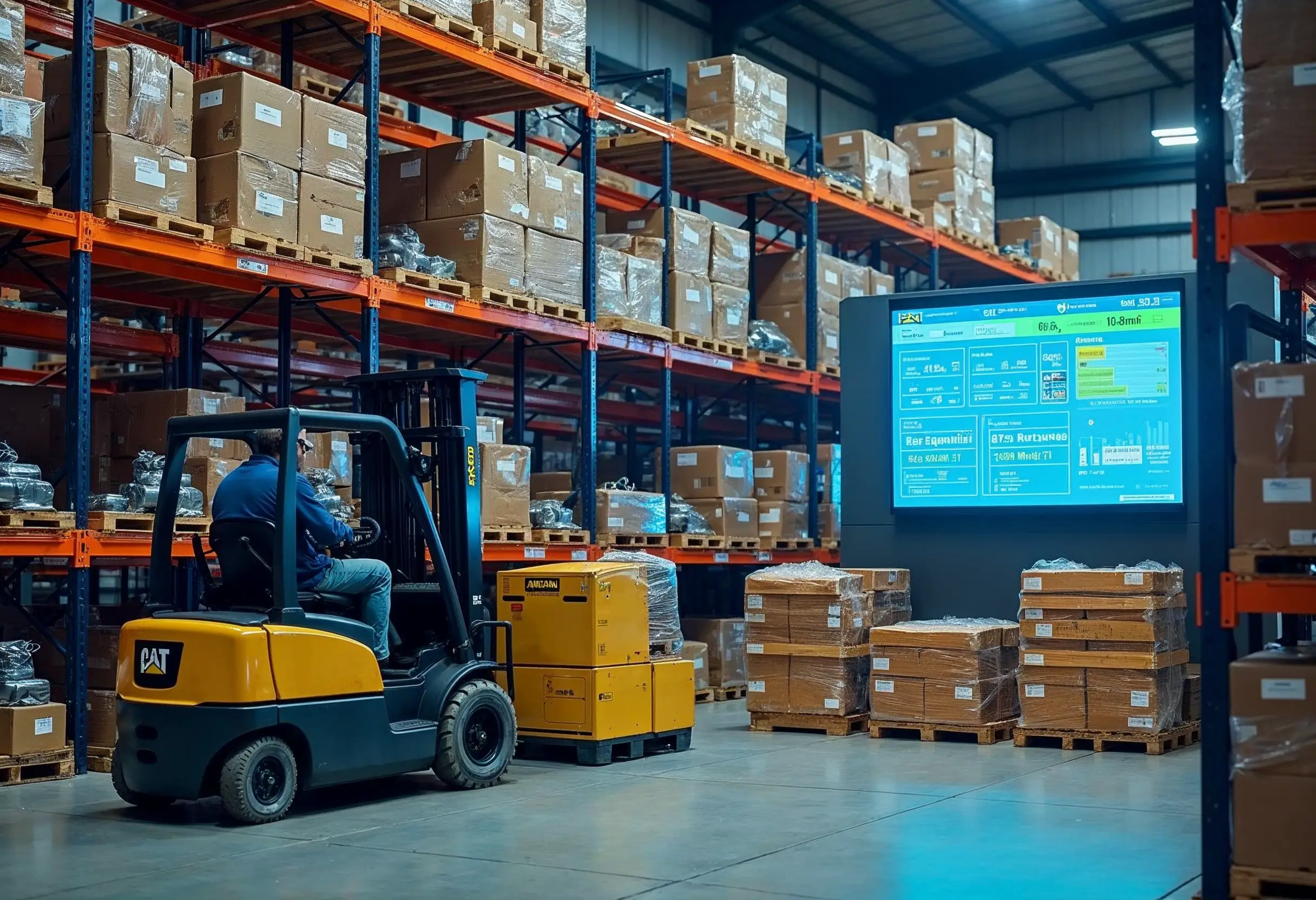
Construction Machinery Parts Suppliers: Expert Selection Guide
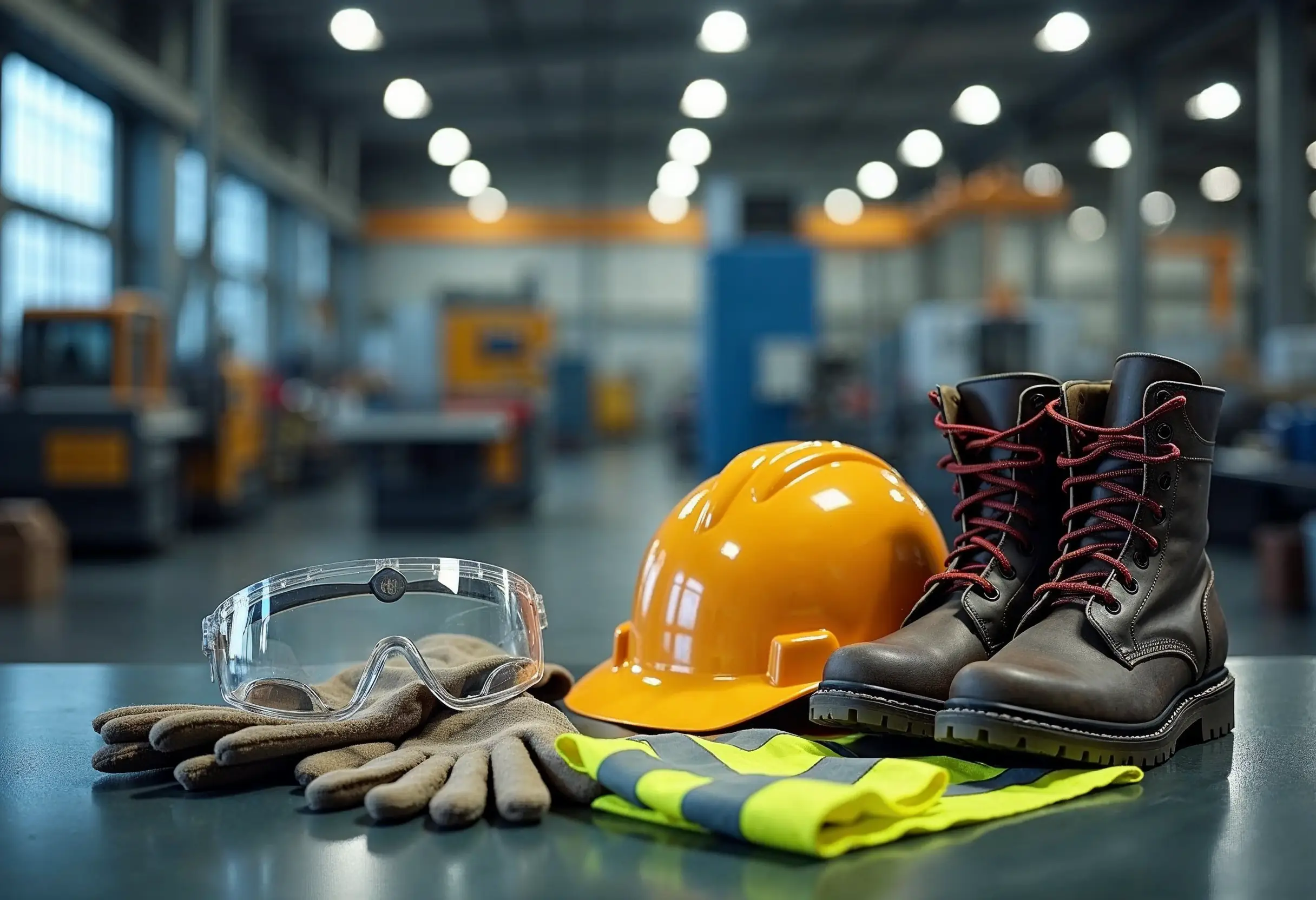
How to Apply Machine Safety Rules: From Selection to Installation
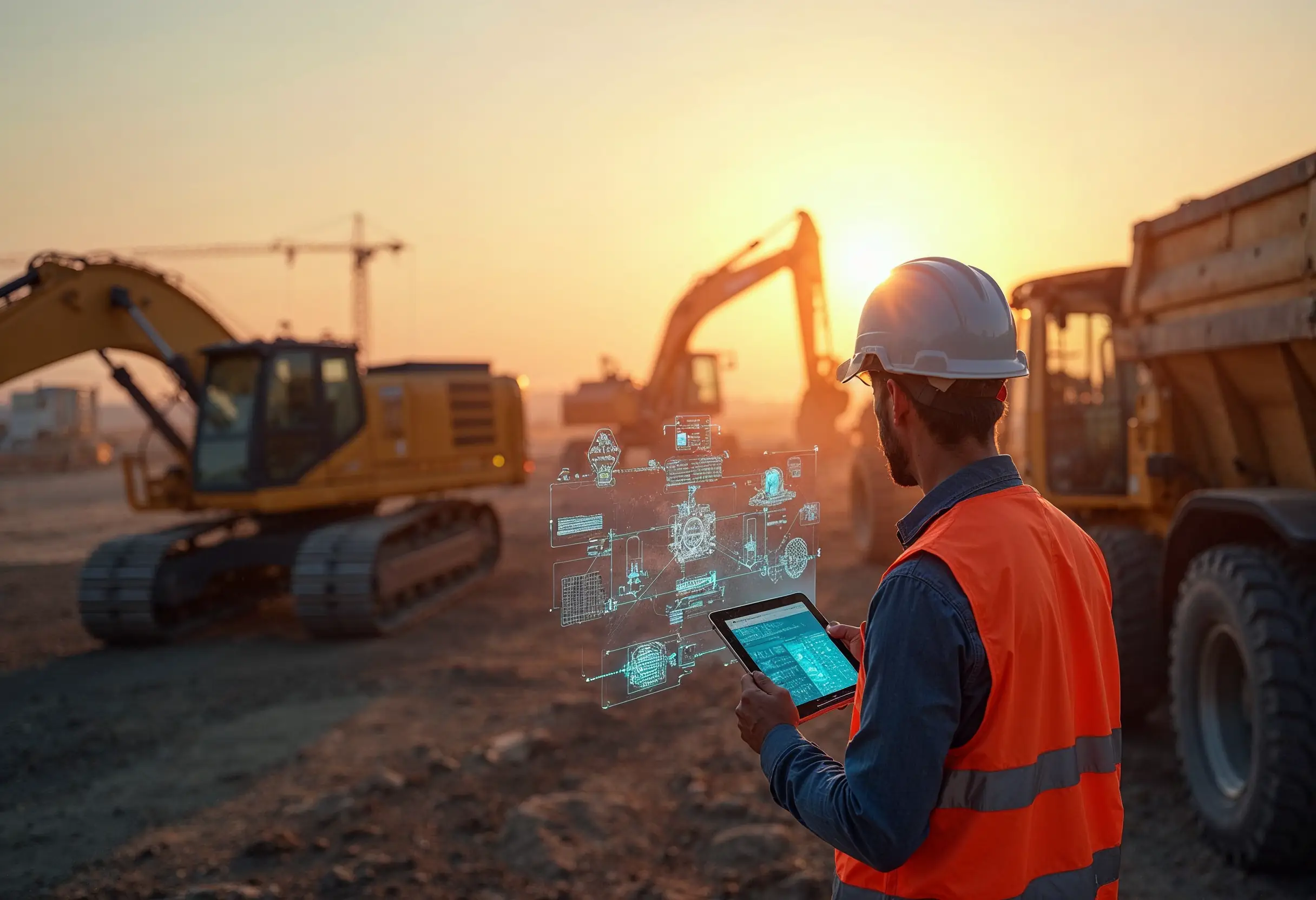
Smart Diagnostics Cut Heavy Equipment Failures by 73%
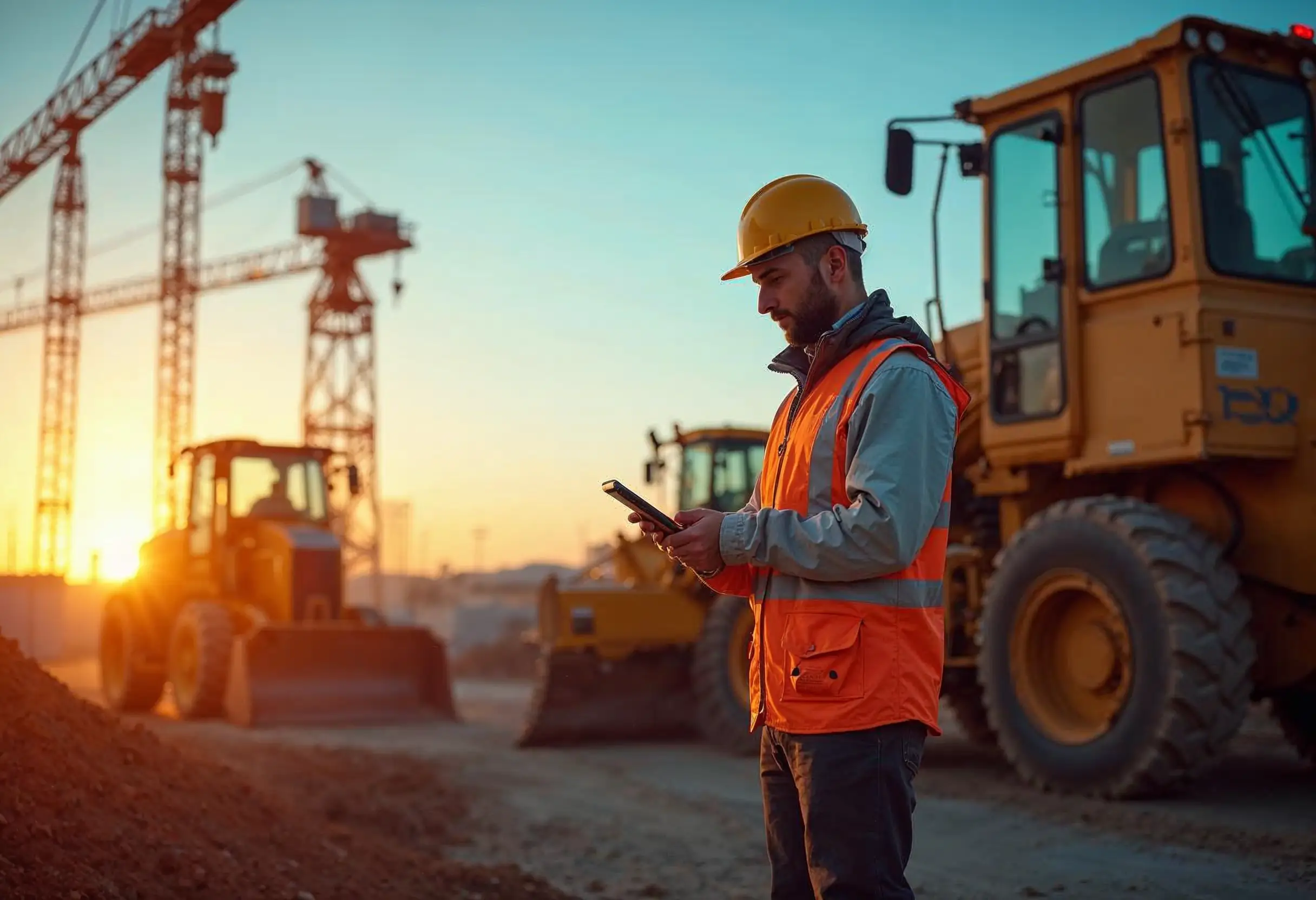
5 Ways to Assess the Environmental Impact of Heavy Construction Machinery
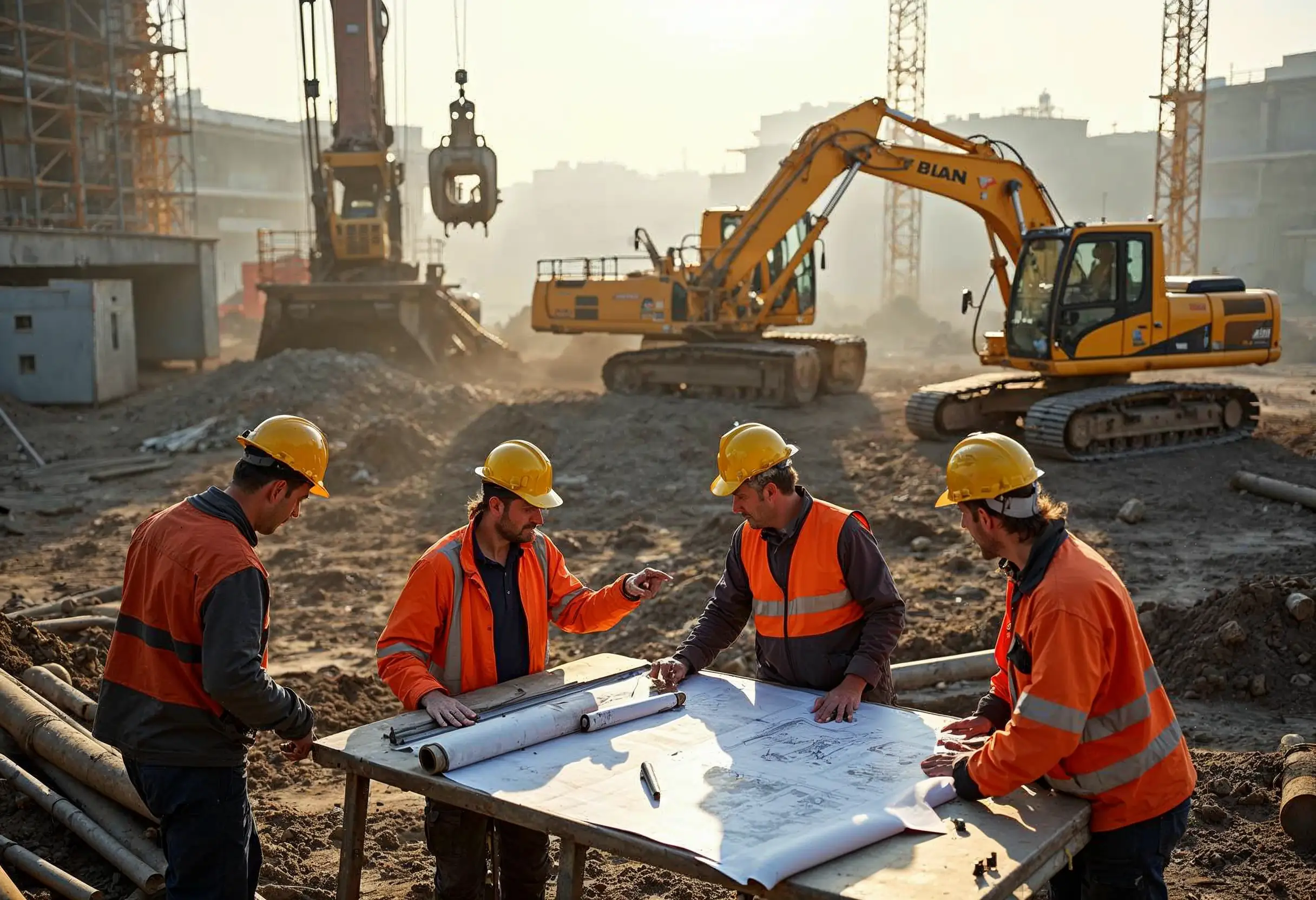
10 Smart Ways to Pick Construction Machinery for 2025 Projects
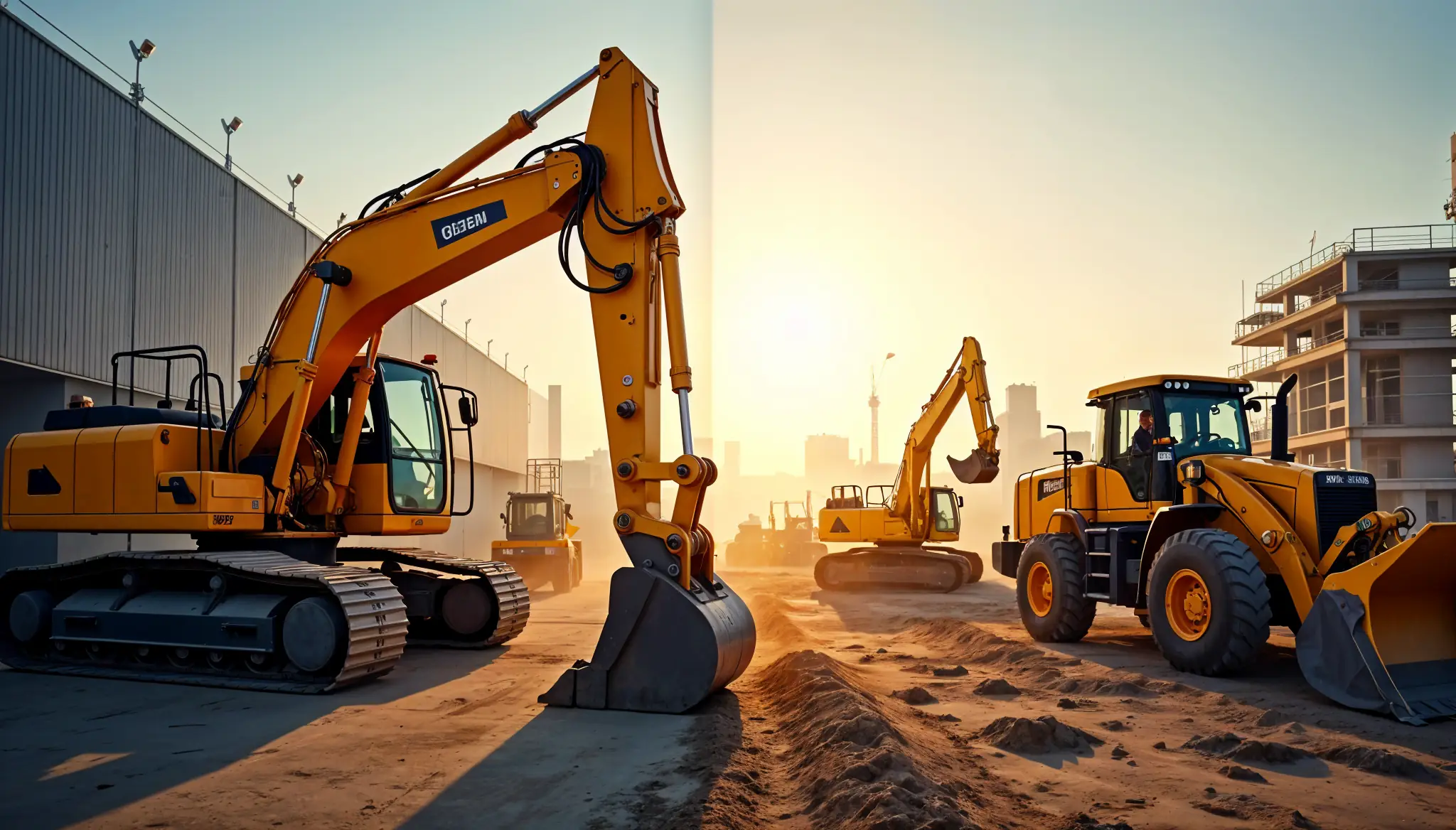
Rent vs Purchase Equipment: What Heavy Industry Experts Hide
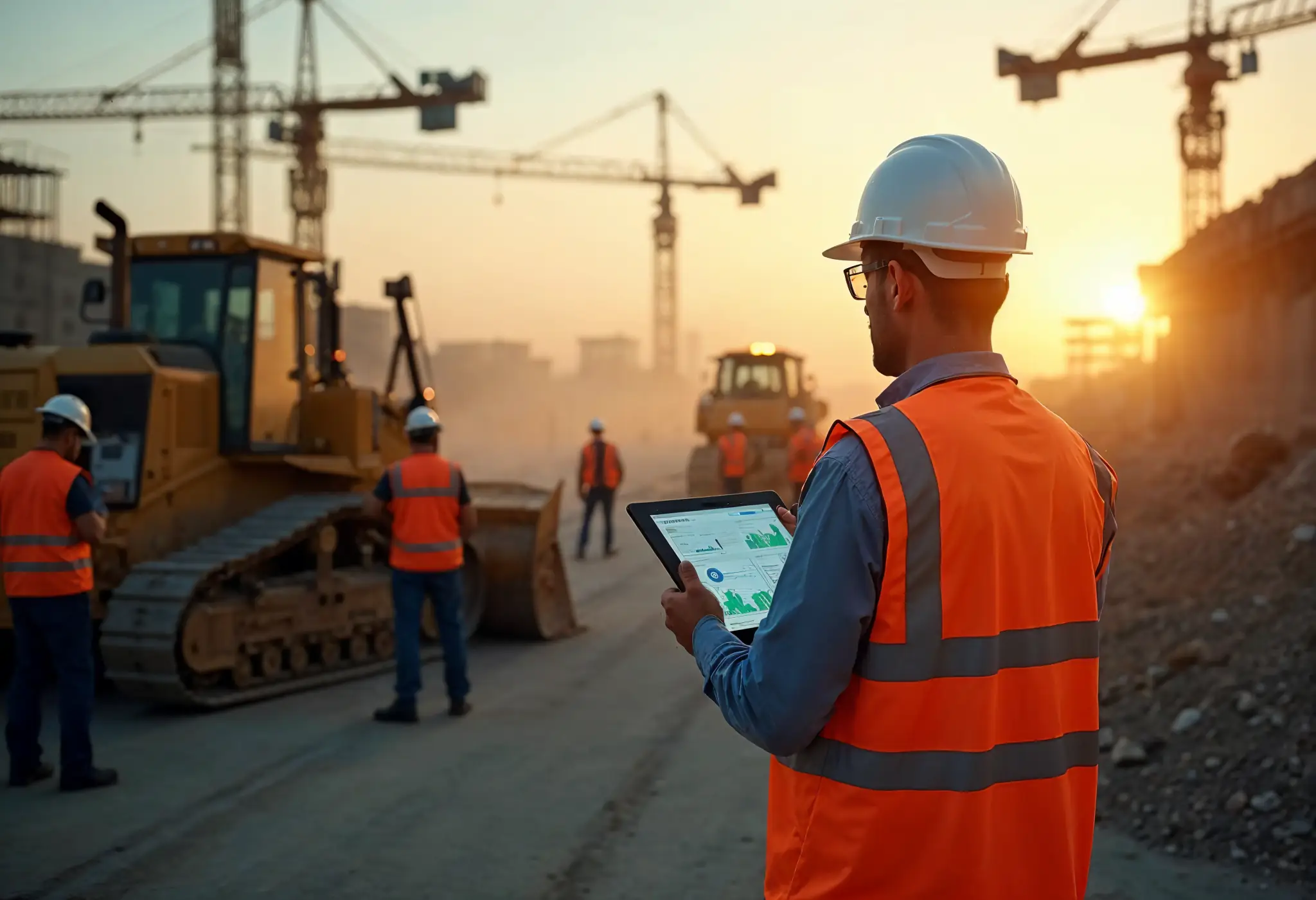
How to Implement a Construction Inventory Management System for Equipment Efficiency
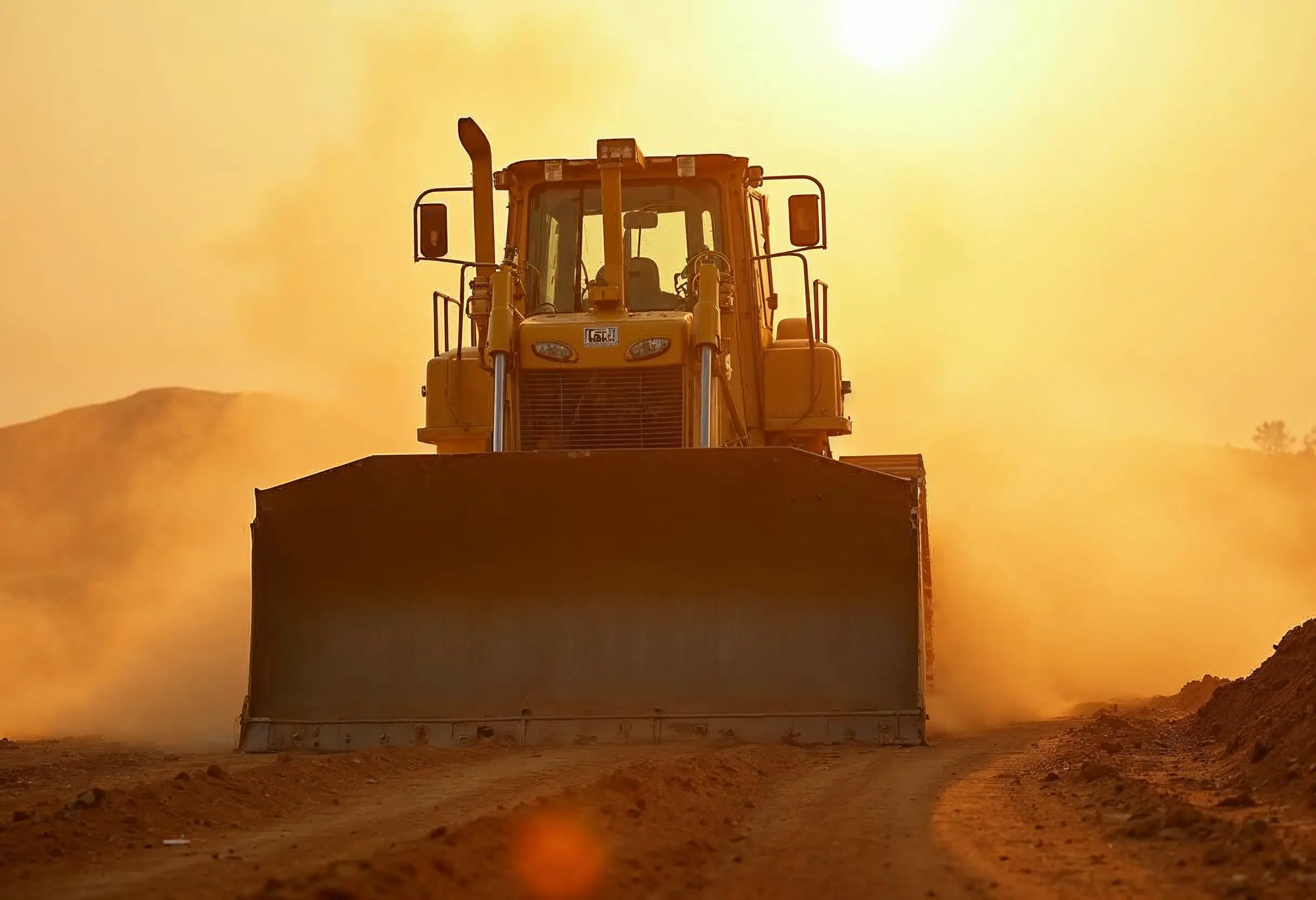
How to Extend Equipment Life Expectancy with Regular Maintenance
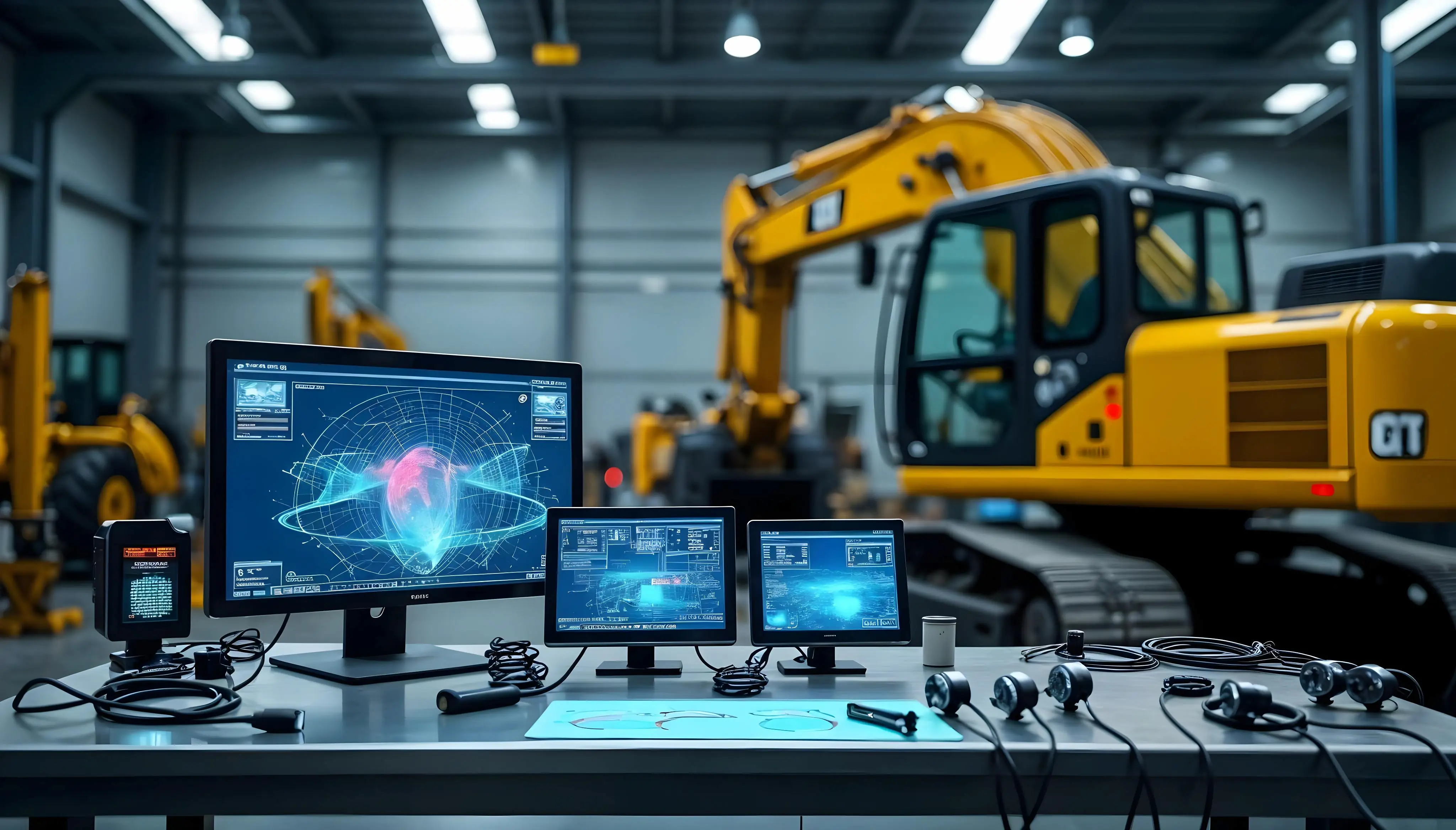
Advanced Heavy Equipment Diagnostic Tools: Ensuring Construction Machinery Quality
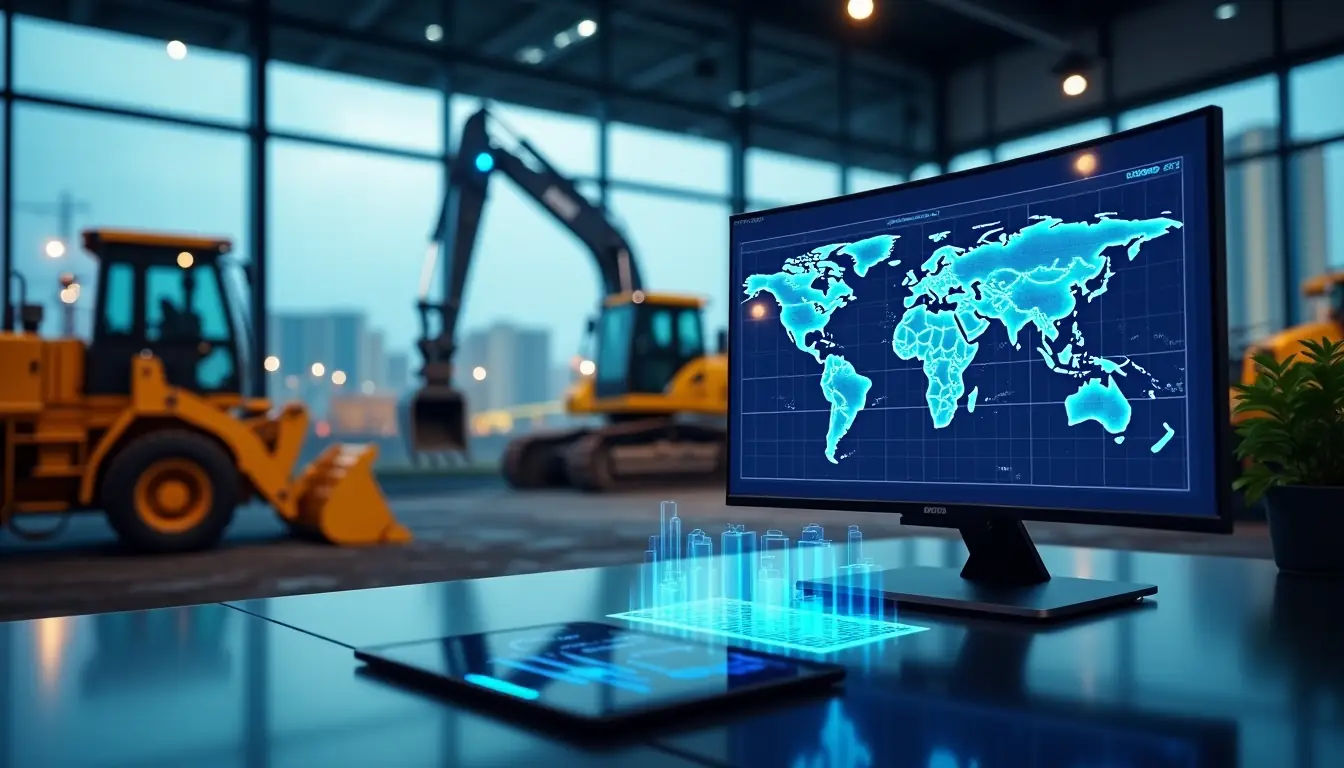
Essential Features Your Construction Equipment Inventory System Needs
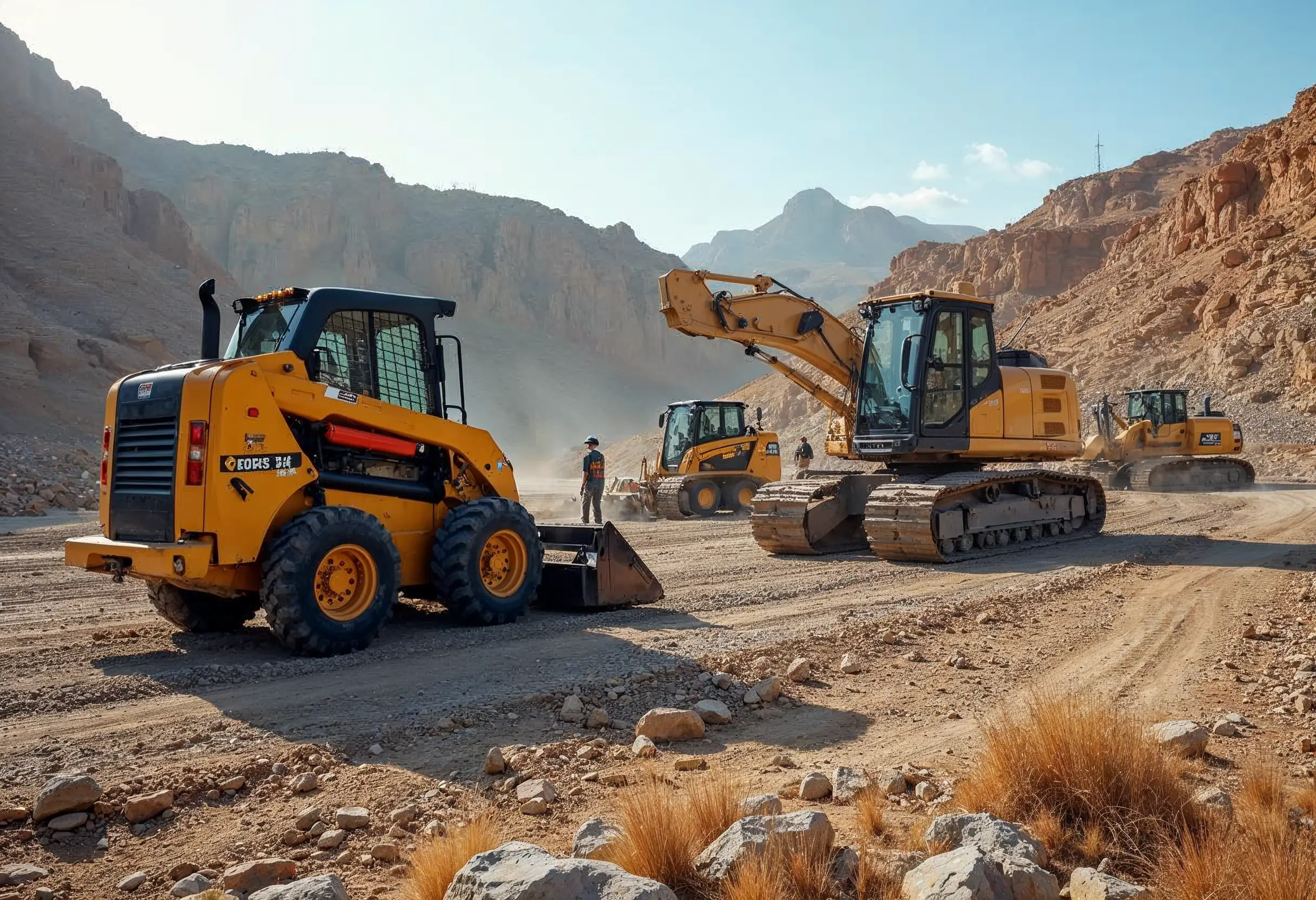
29 Quick Tips for Choosing Construction Equipment for Remote Locations
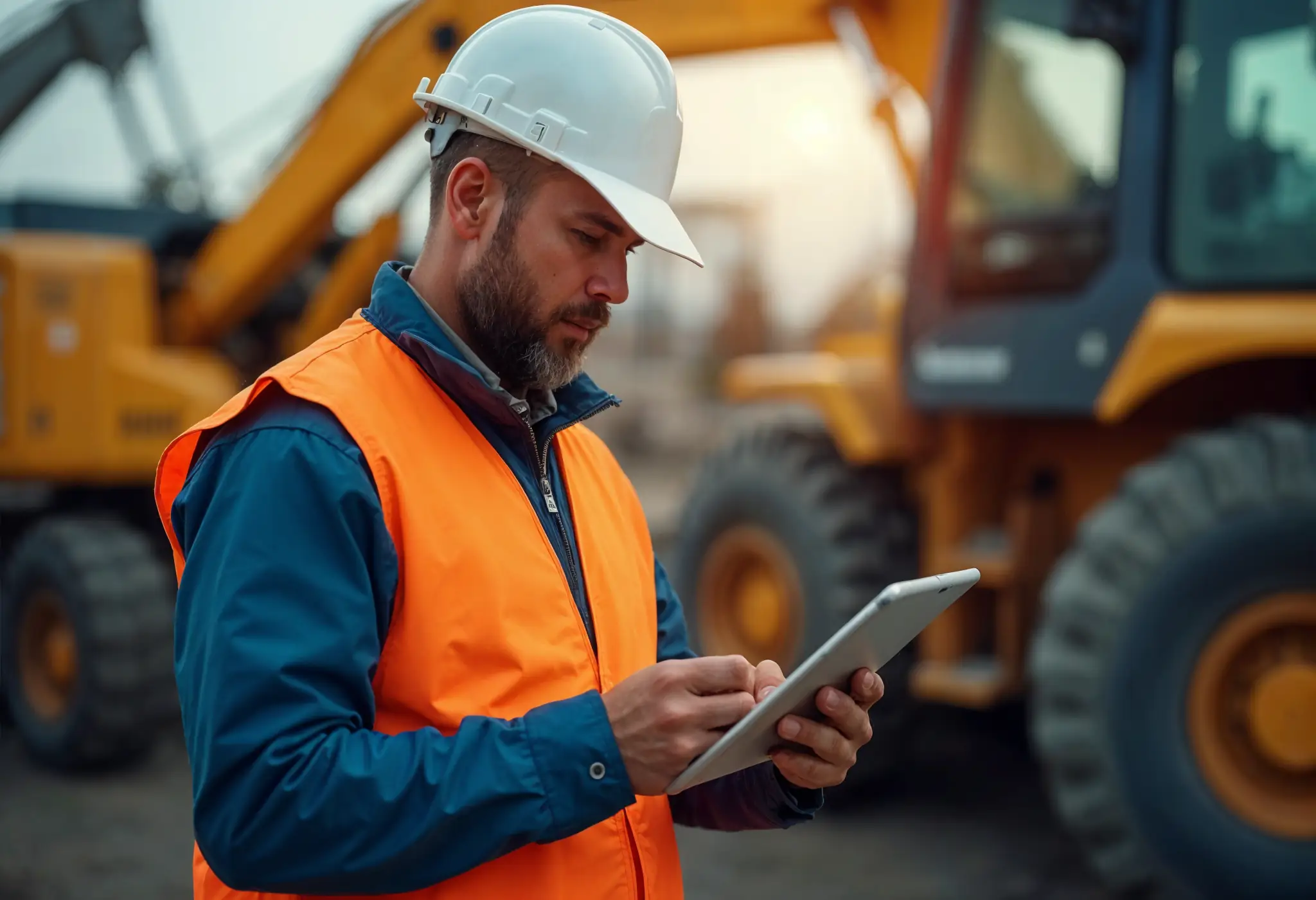
How to Select Construction Machinery with Optimal Equipment Maintenance in Mind
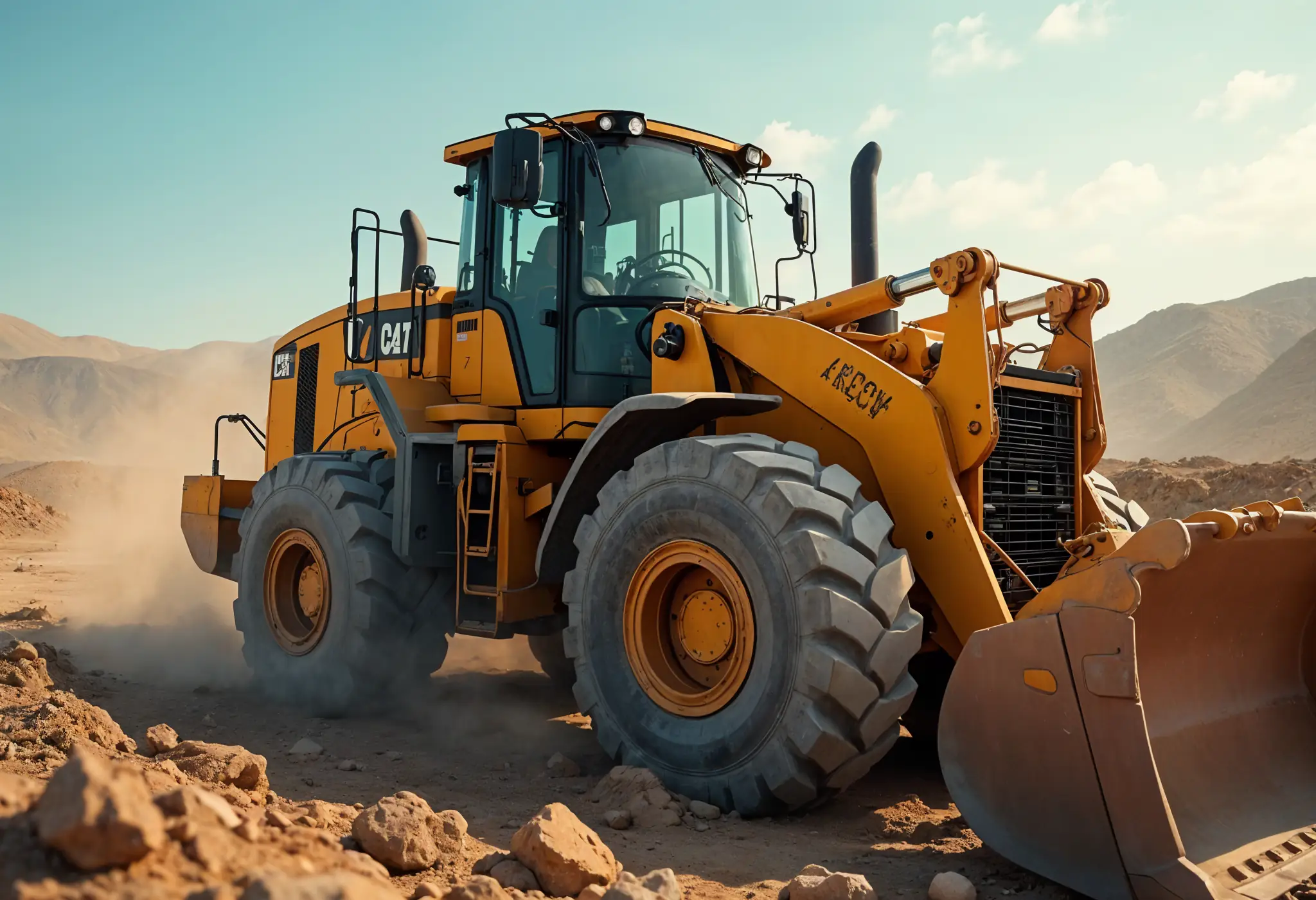
Top 25 Tips for Selecting Bulldozers for Construction Sites
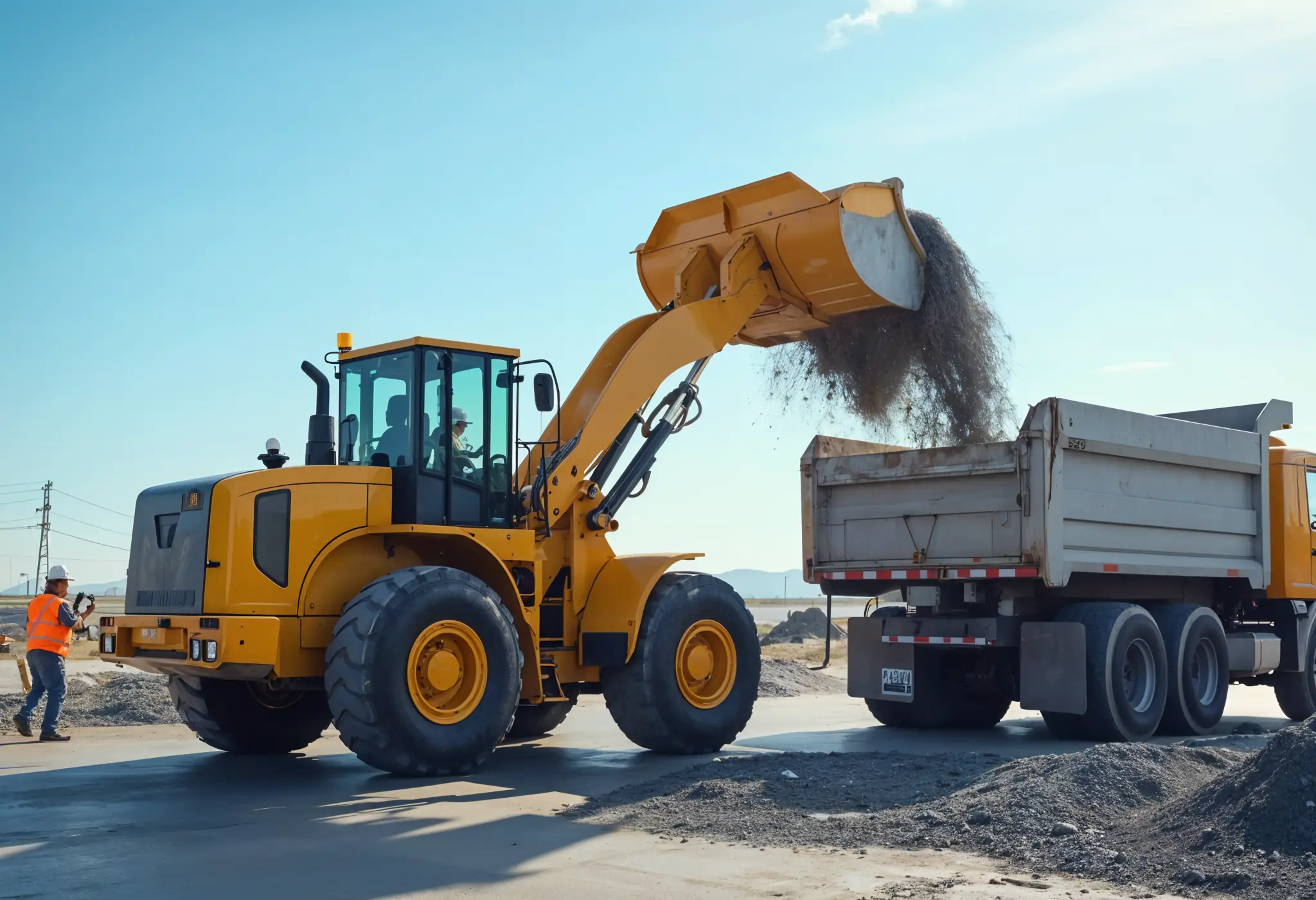
Which Construction Loader is Best for Your Project Needs?
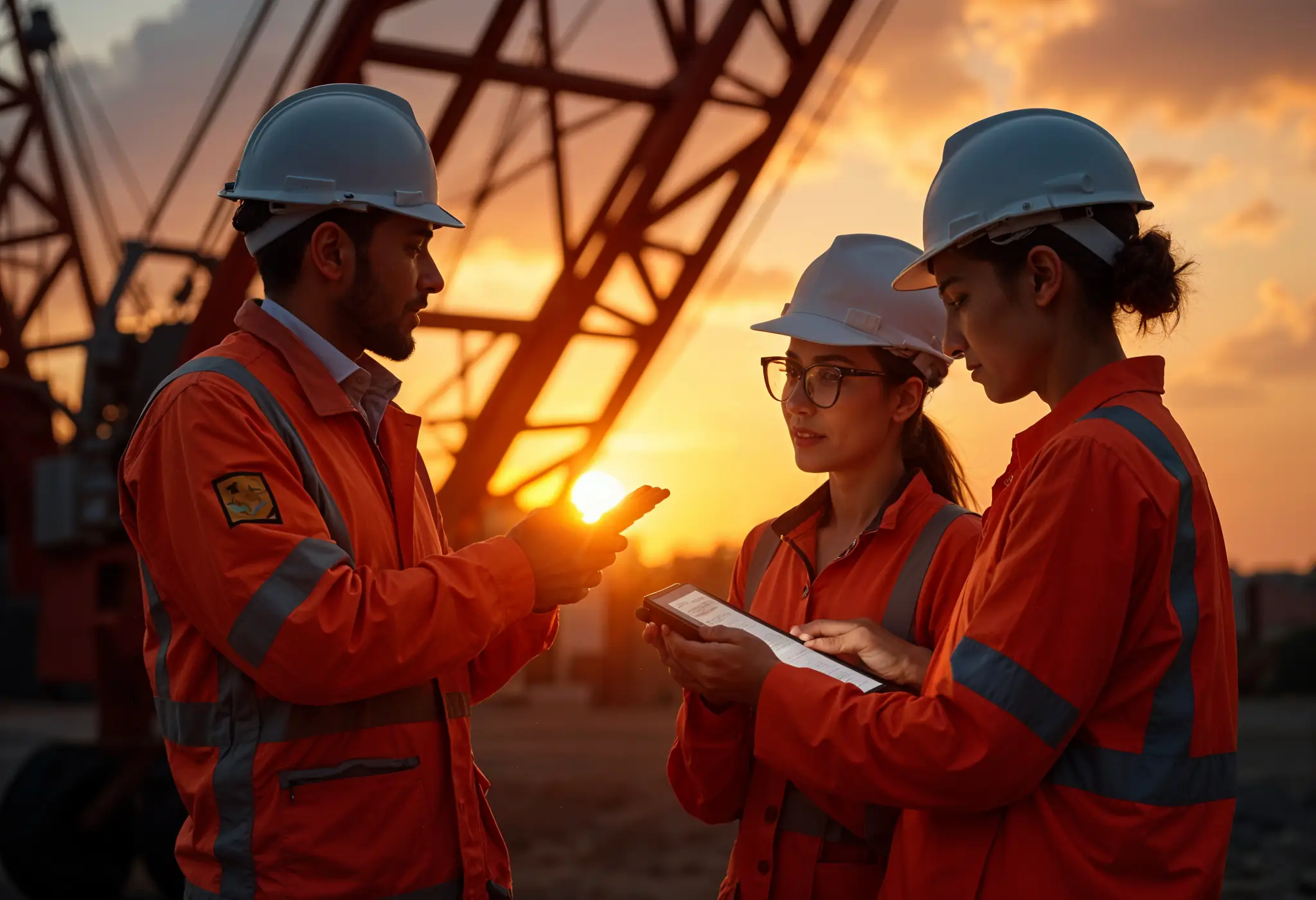
4 Key Steps to Form a Construction Machinery QC Team
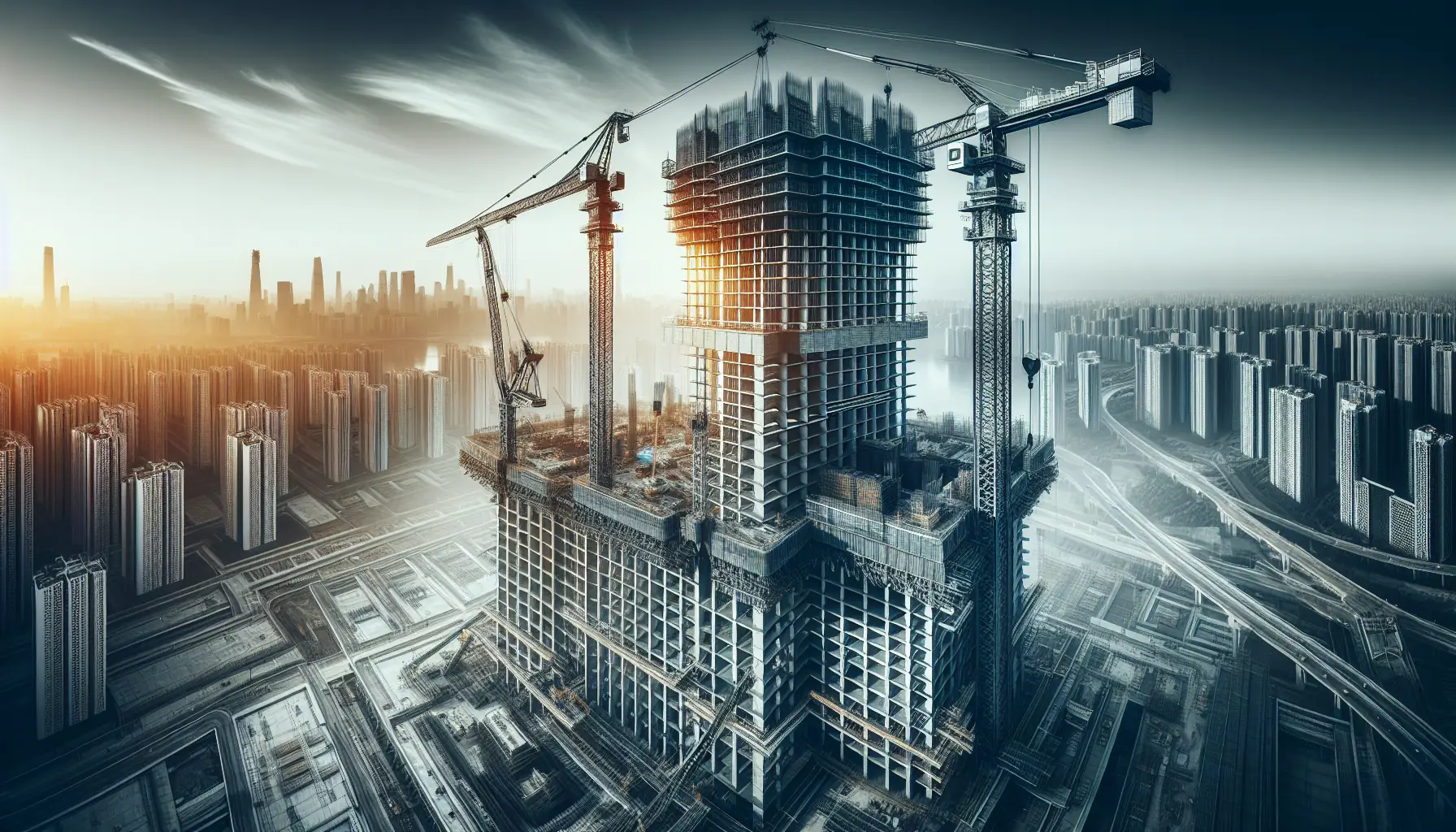
15 Essential Tips for Selecting the Perfect Crane for Construction
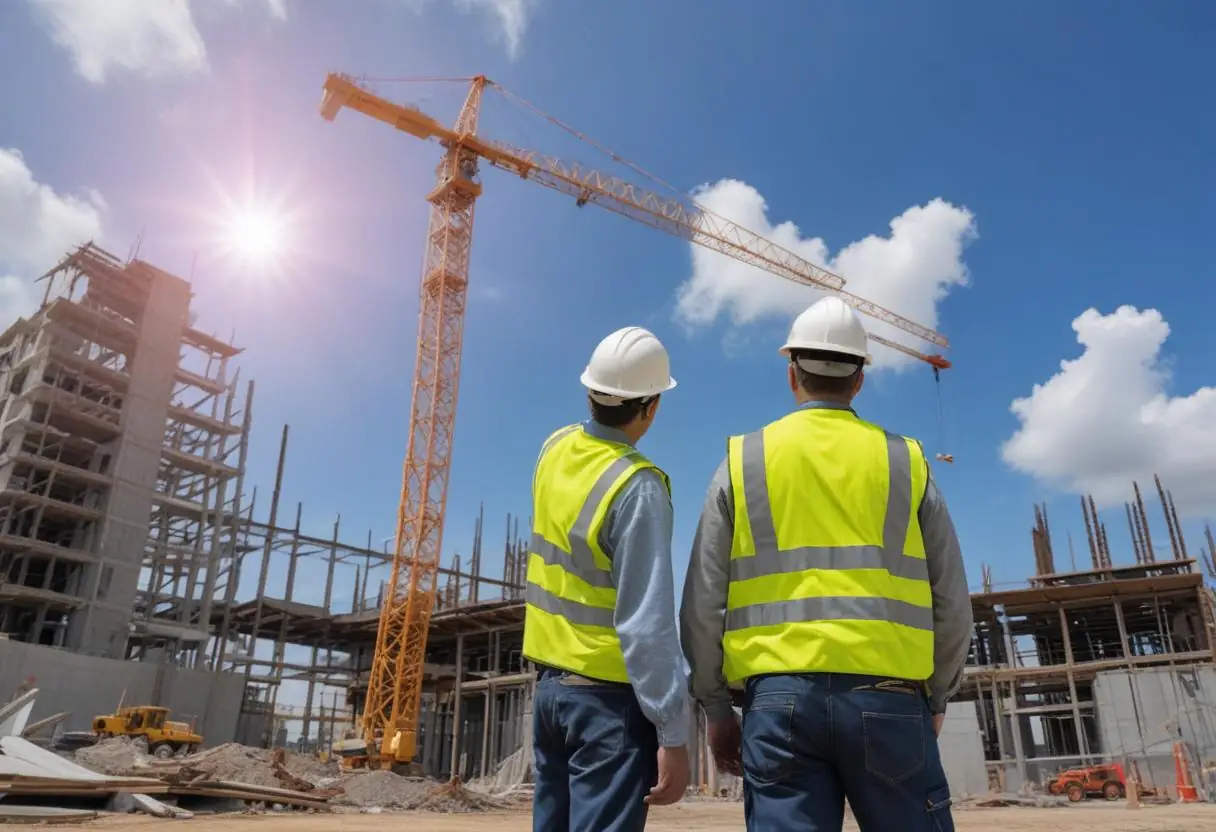
Maximize Savings: Multi-Purpose Construction Machinery for Lower Costs
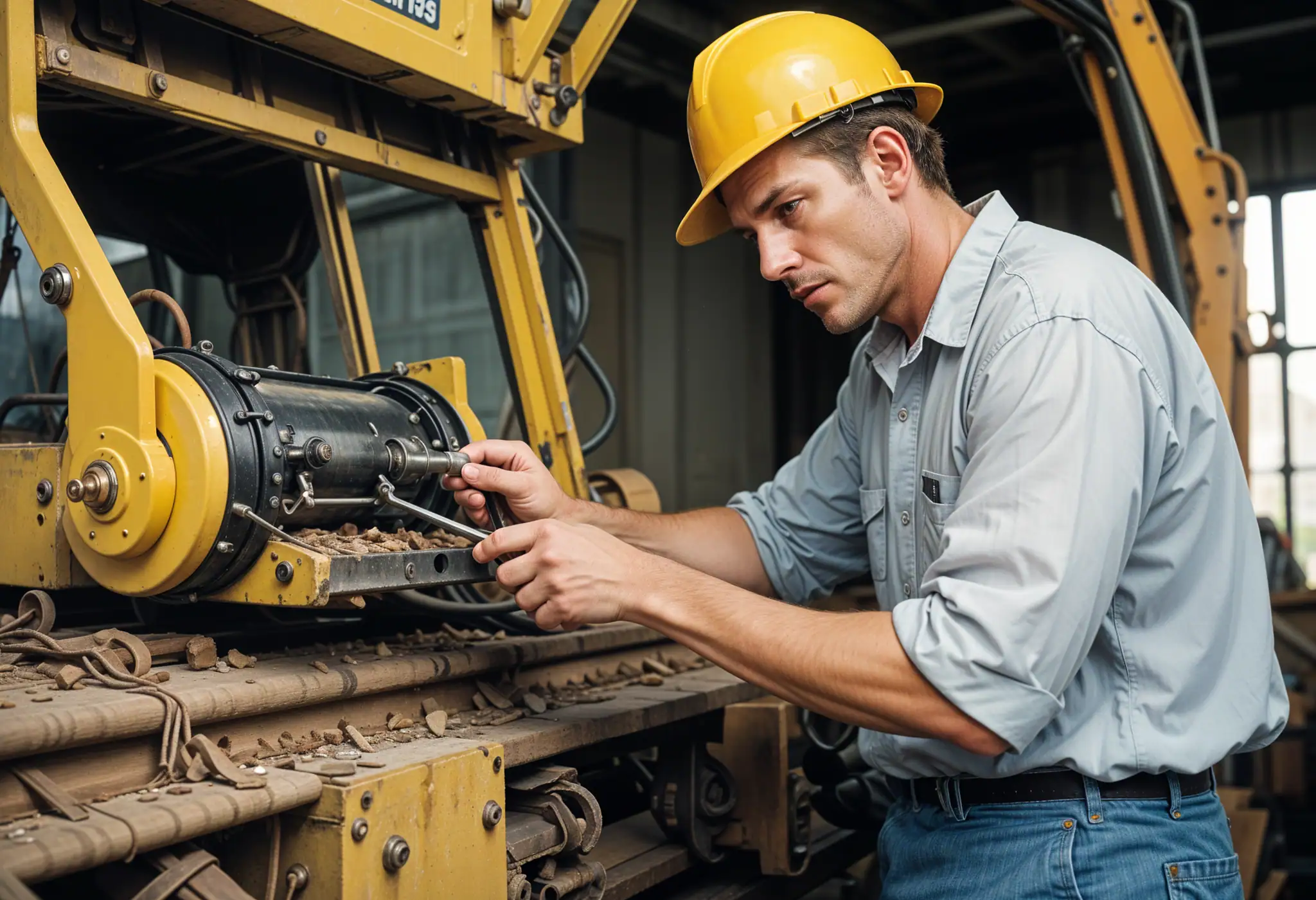
Affordable Heavy Equipment Parts: A Sourcing Guide
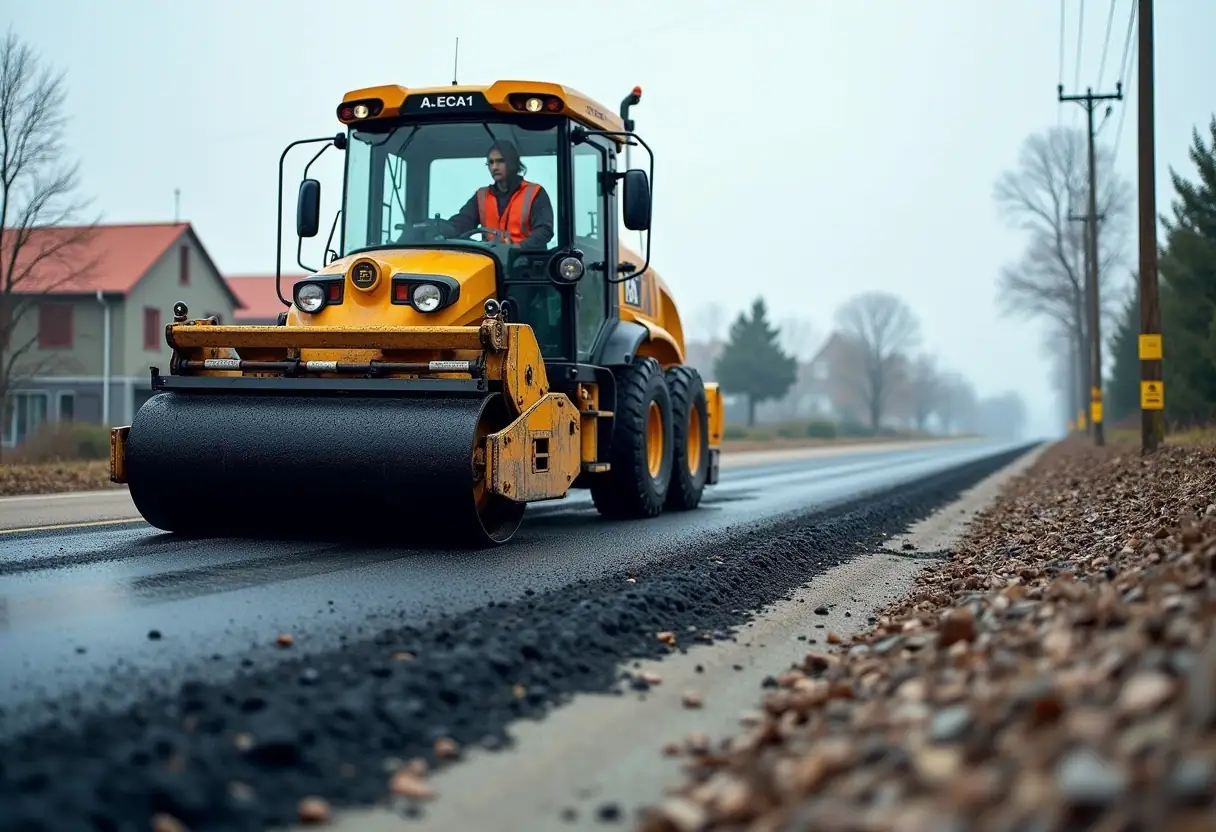
Choosing the Right Road Construction Equipment: A Complete Guide
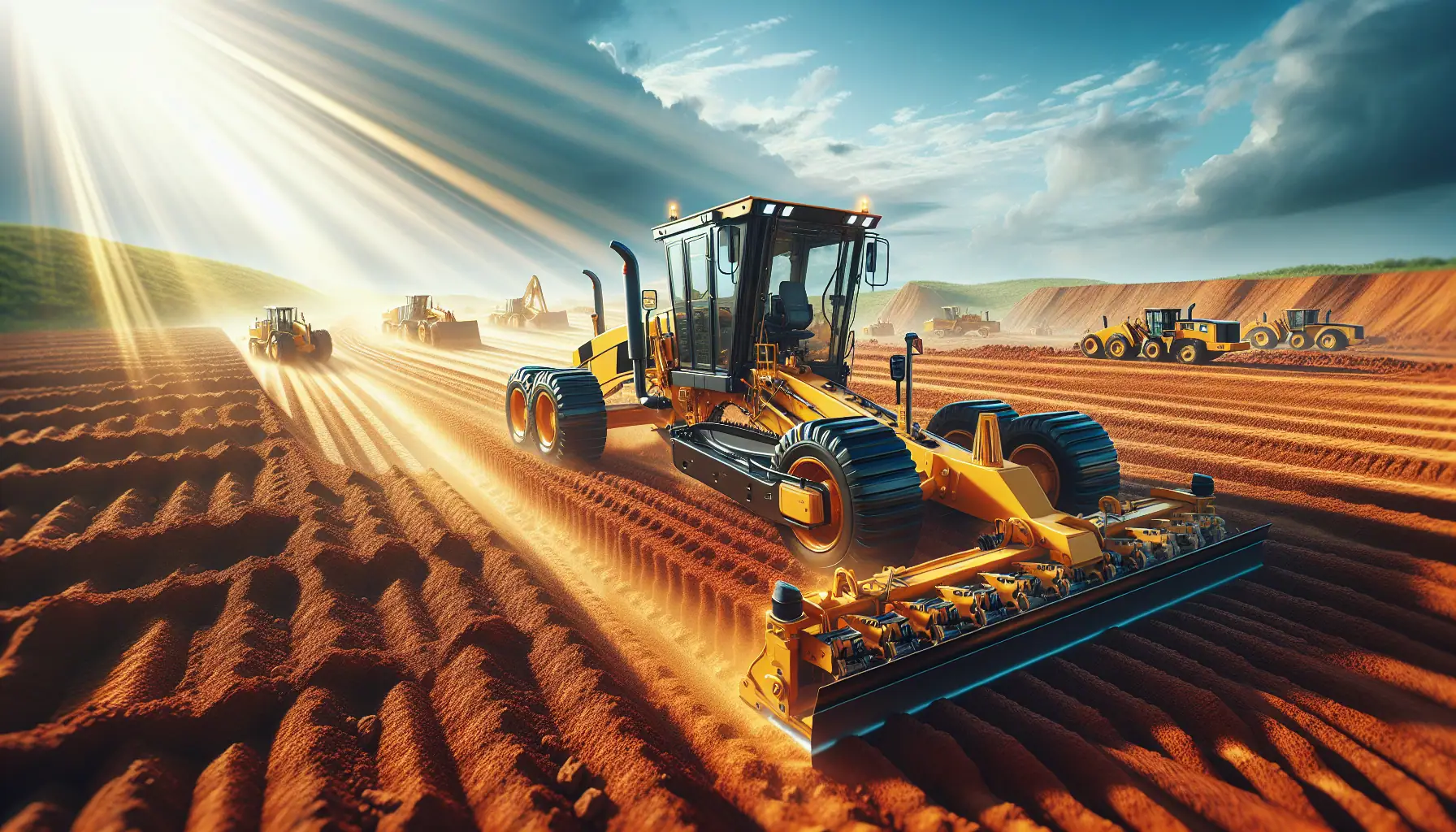
Motor Graders: Key Elements to Consider for Optimal Selection
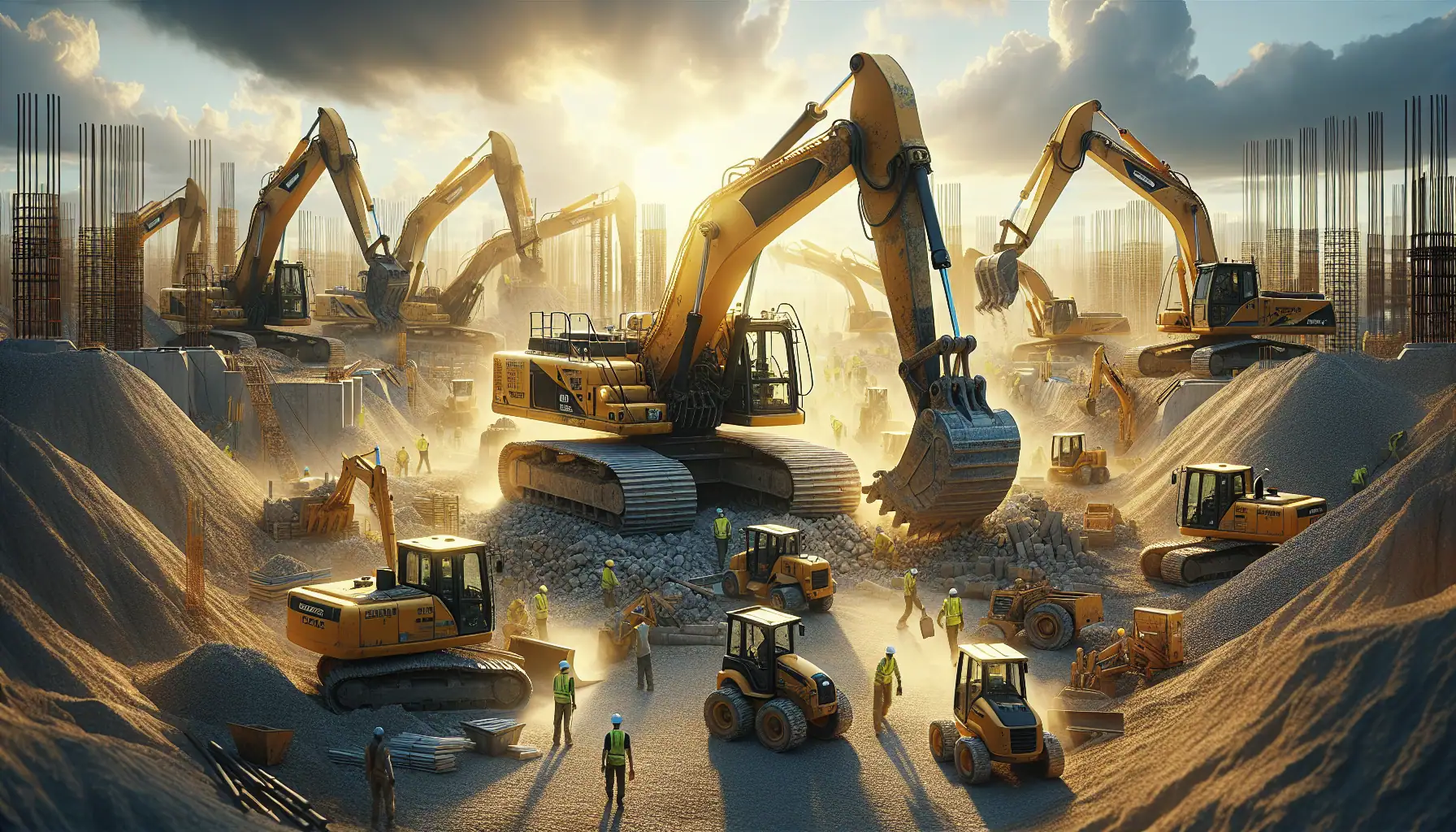
A Detailed Guide to Choosing Excavators for Construction Work
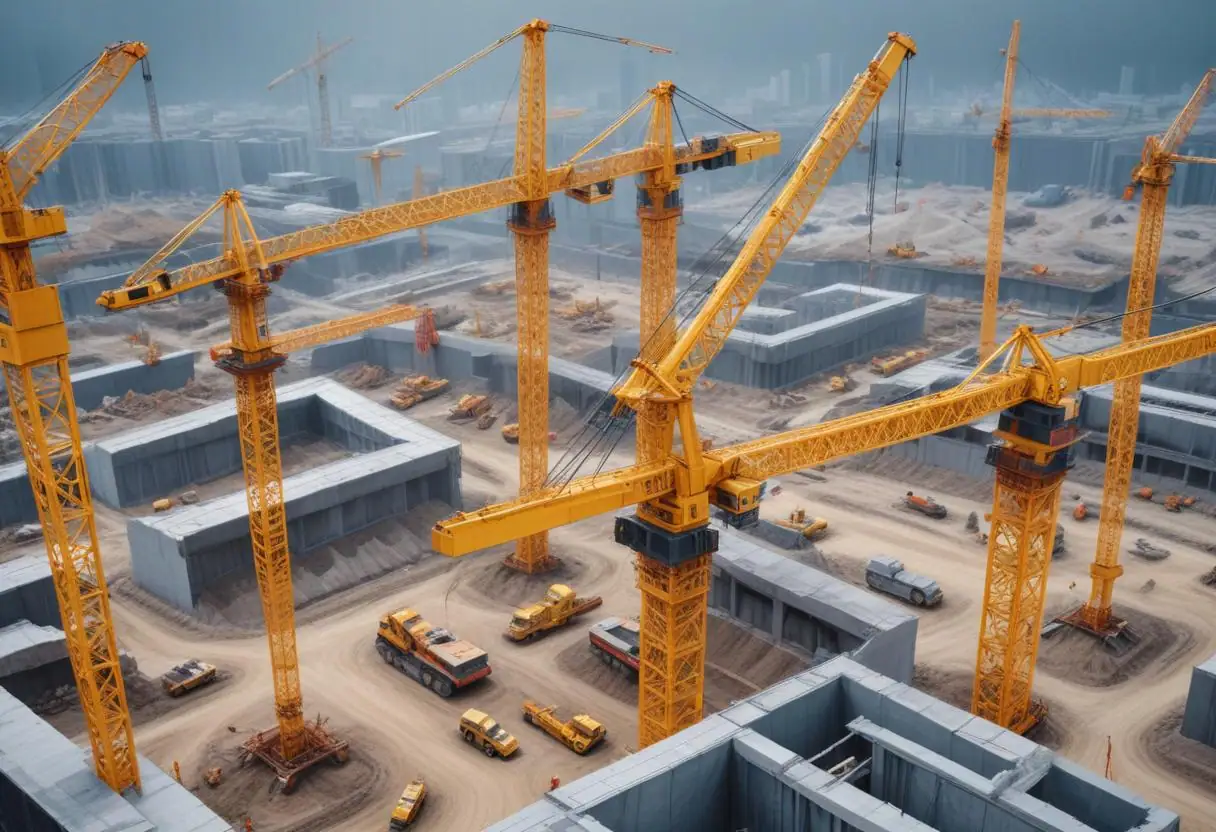
Top Tips for Choosing Cranes for Construction Projects
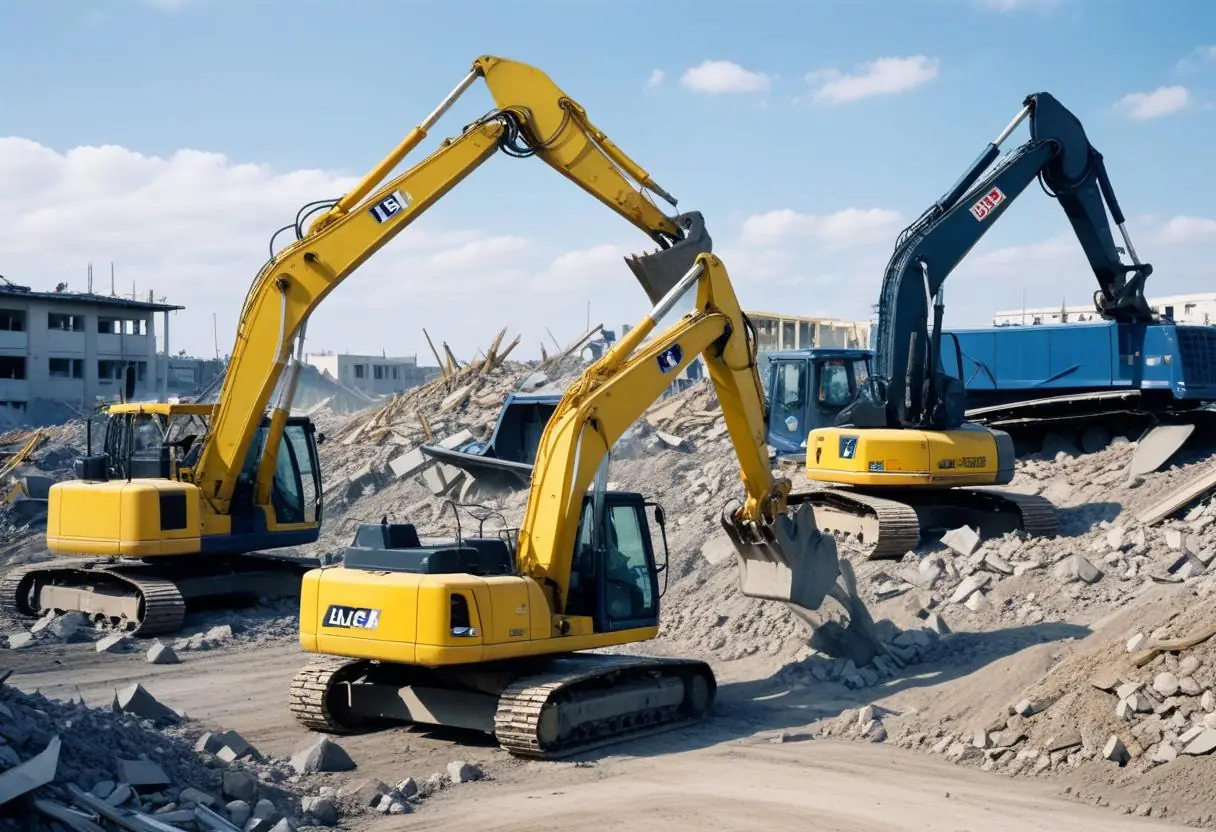
5 Top-Rated Demolition Machines for Construction Professionals
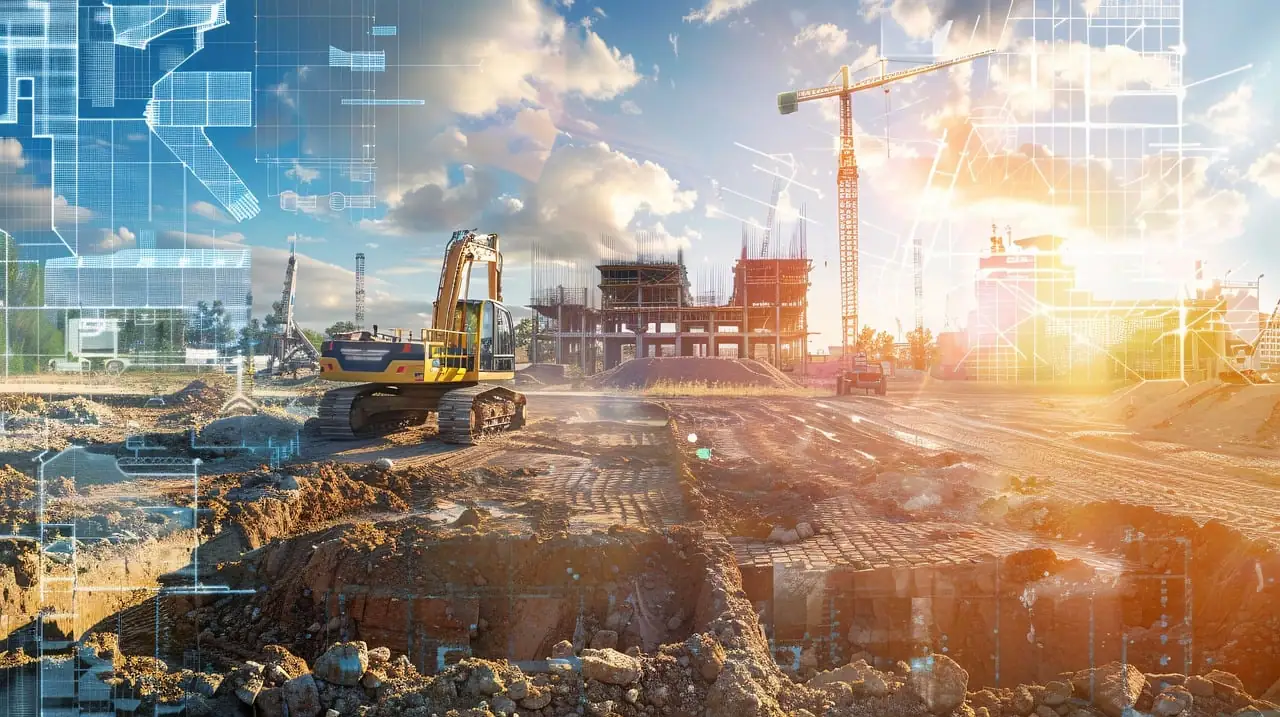
Expert Tips on Choosing Earthmoving Equipment for Large Projects
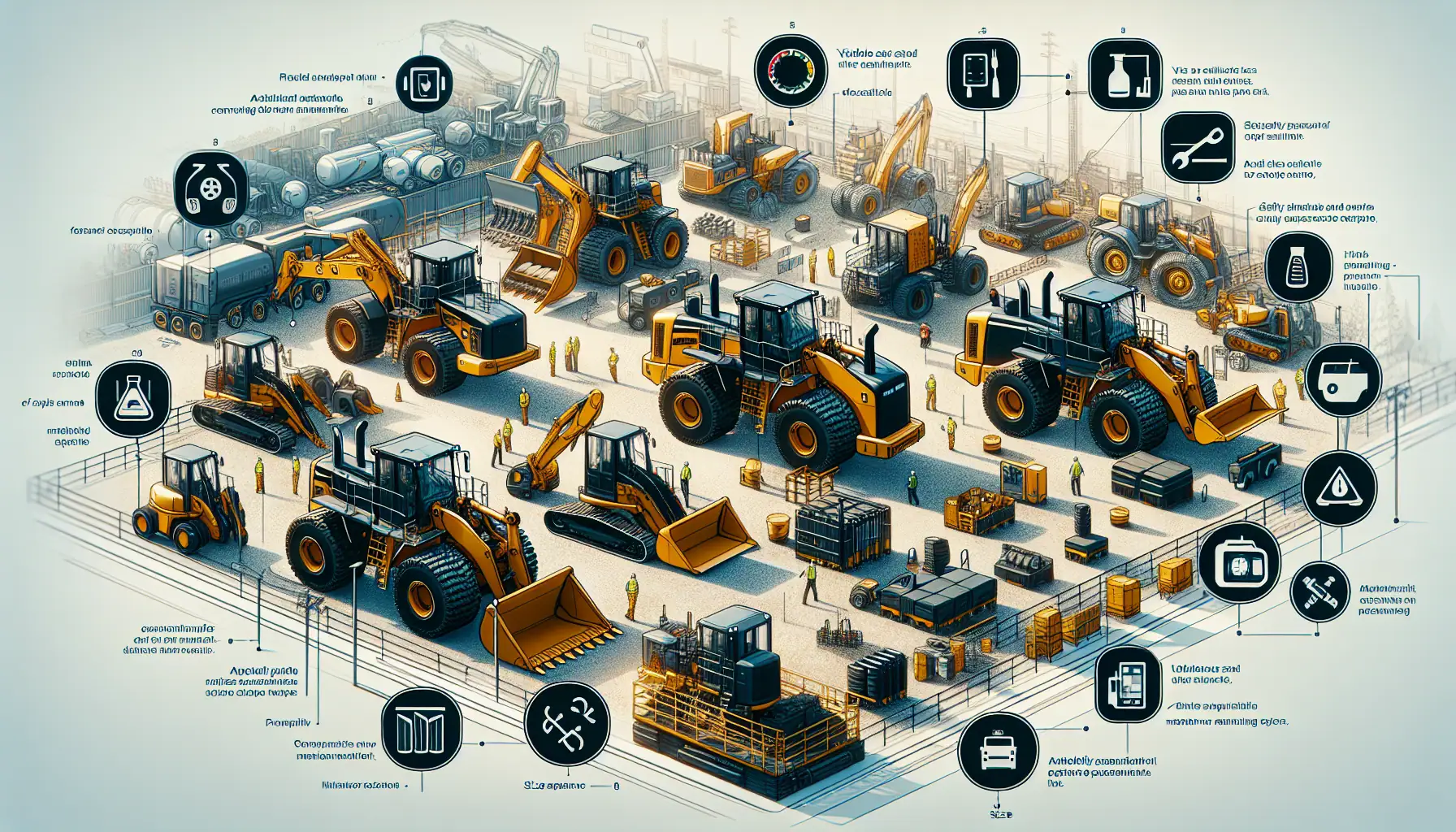
Top Functional Criteria for Selecting Heavy Construction Equipment
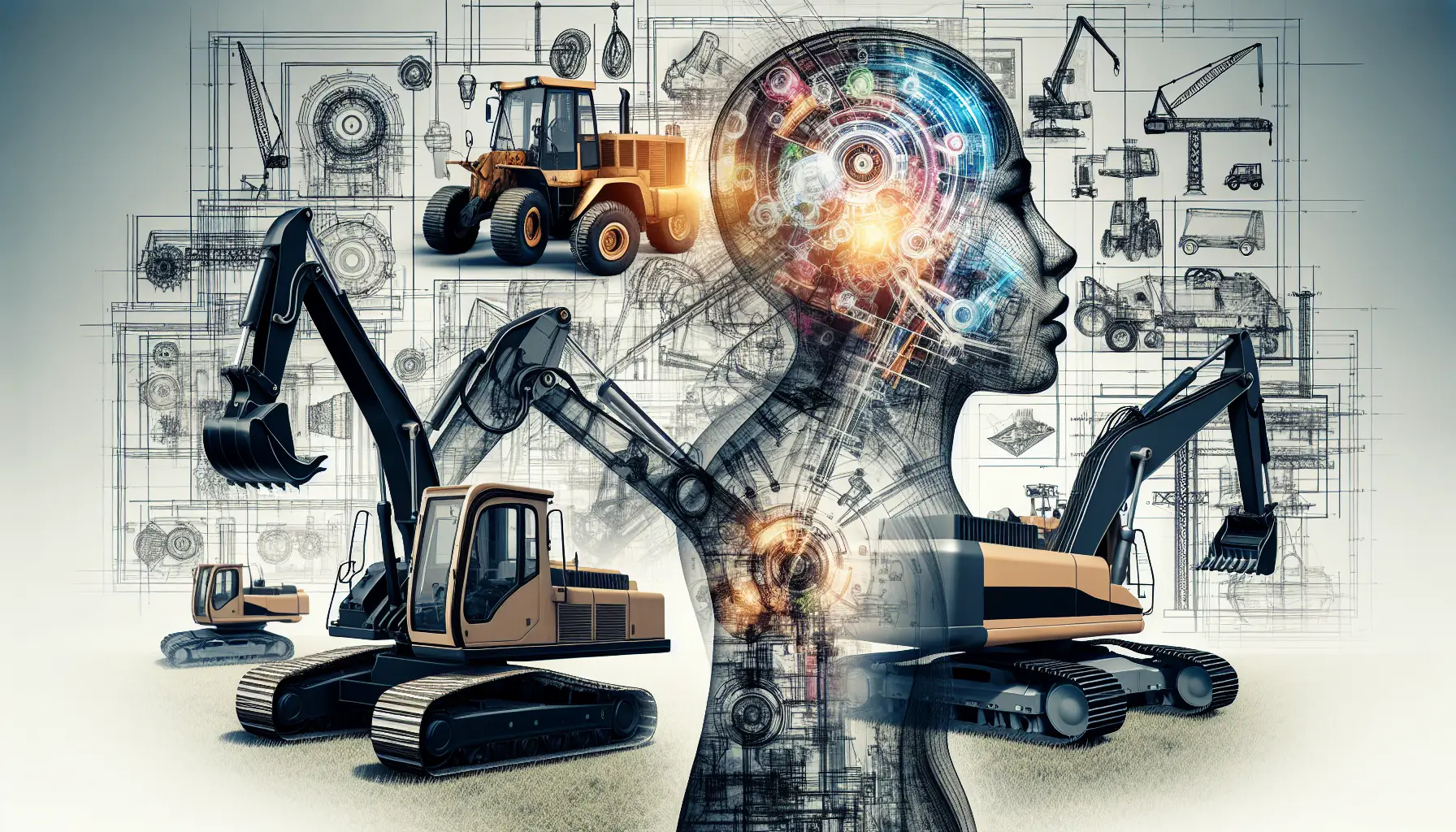
Construction Machinery: Detailed Guide to Equipment Specifications
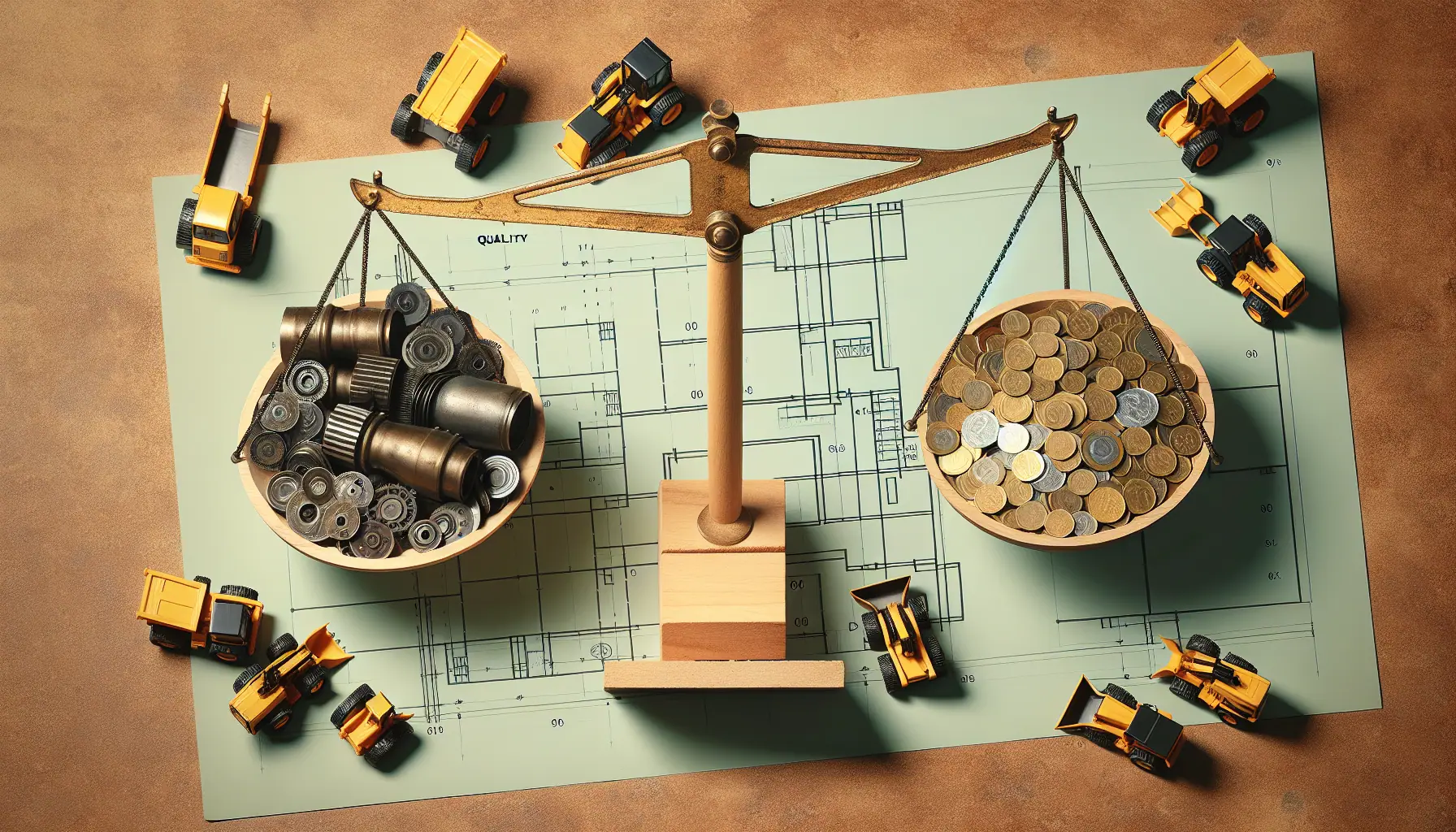
Heavy Machinery Prices: Key Factors in Cost and Quality Balance
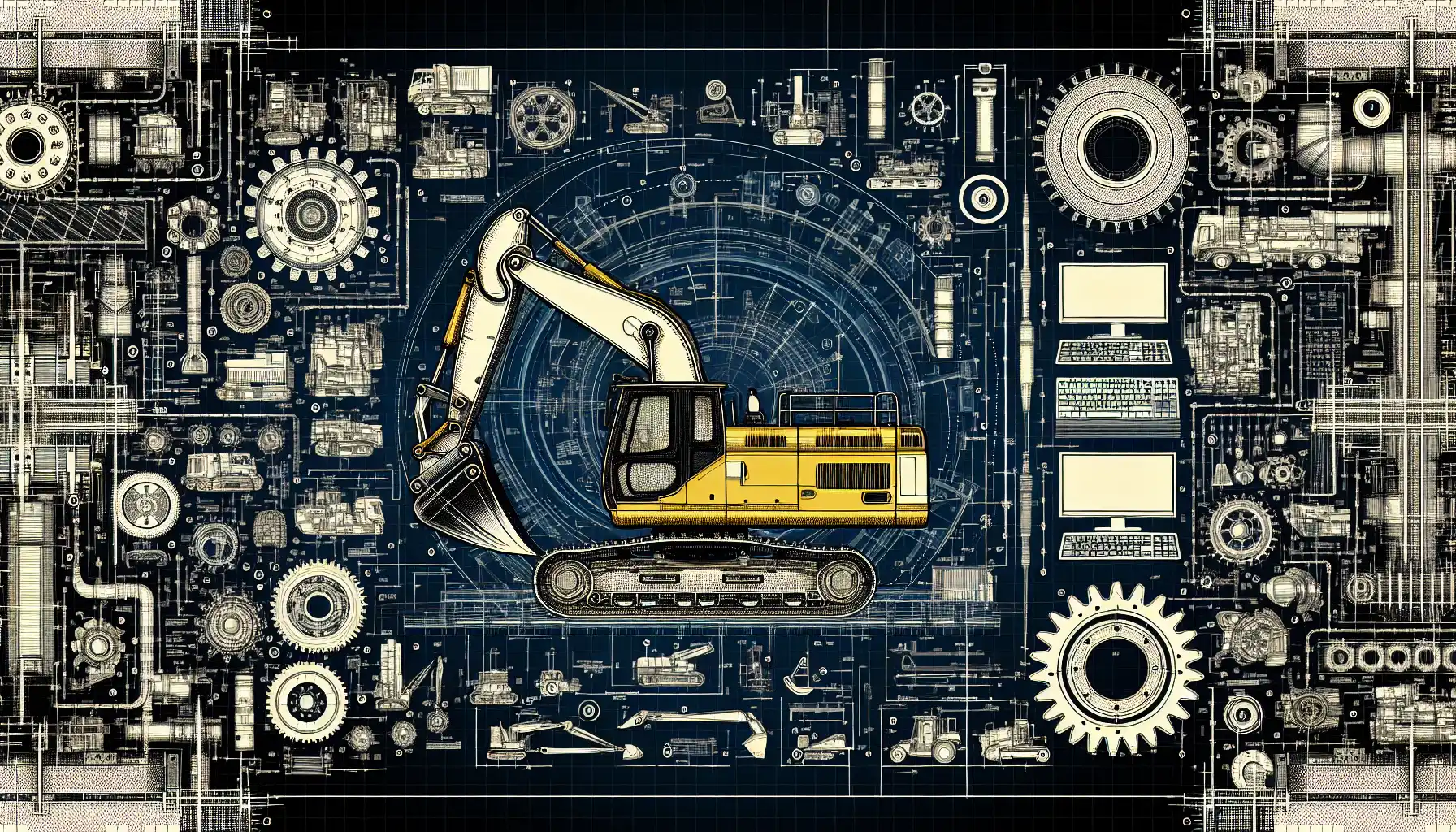
Best Construction Heavy Equipment Brands: Pros and Cons
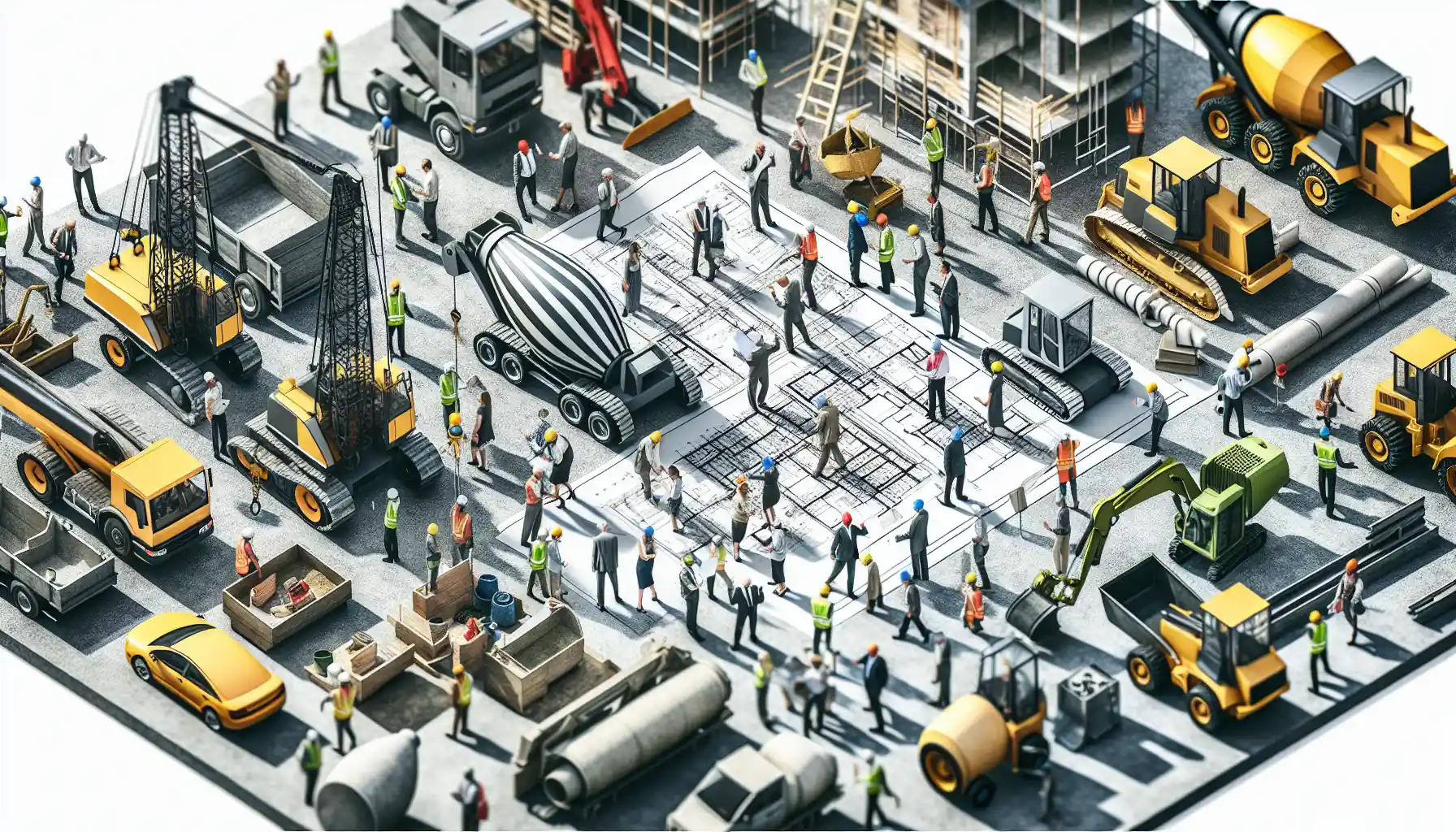
Construction Site Equipment: How to Determine Your Requirements
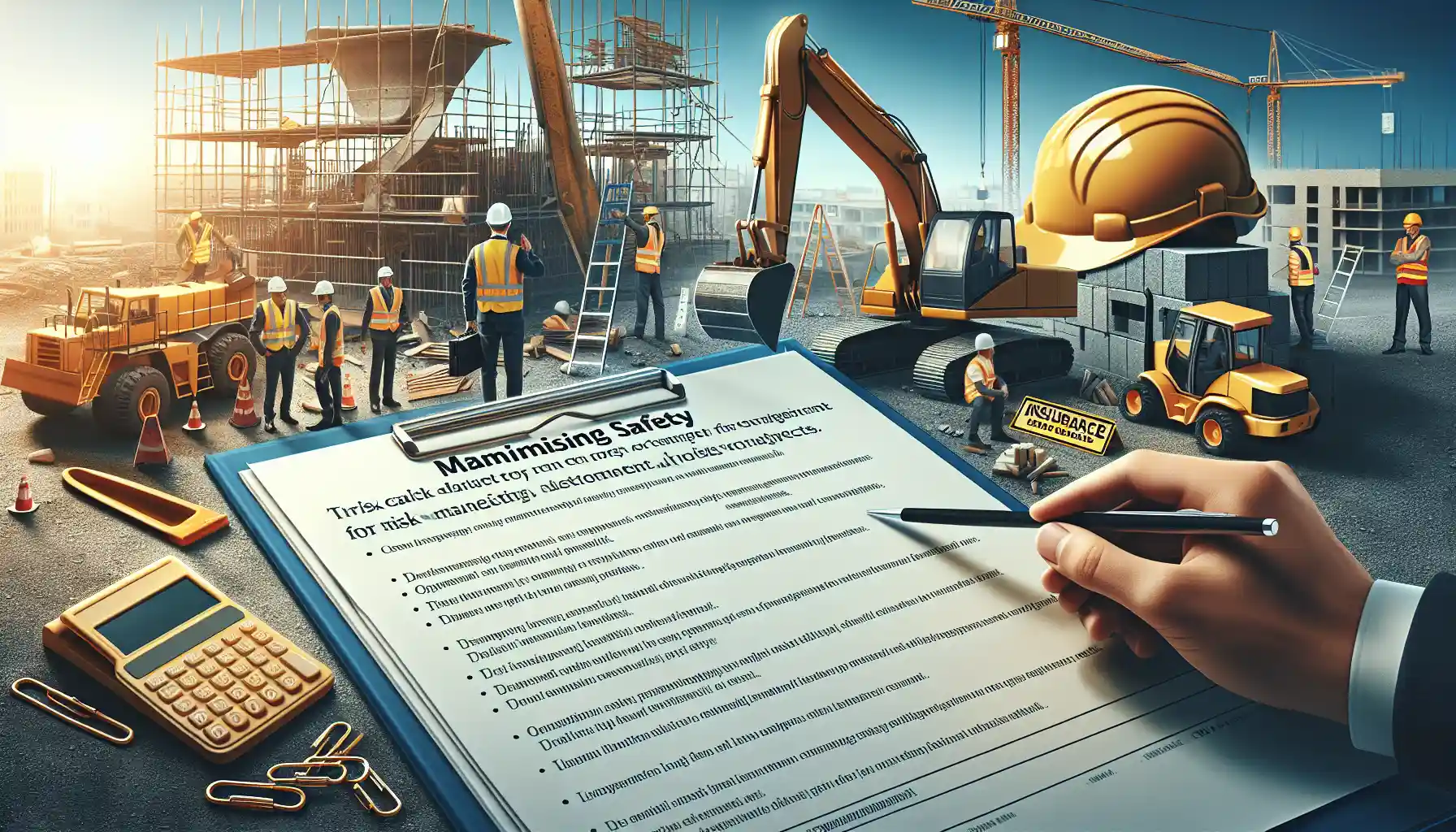
Maximizing Safety: Risk Management for Construction Projects
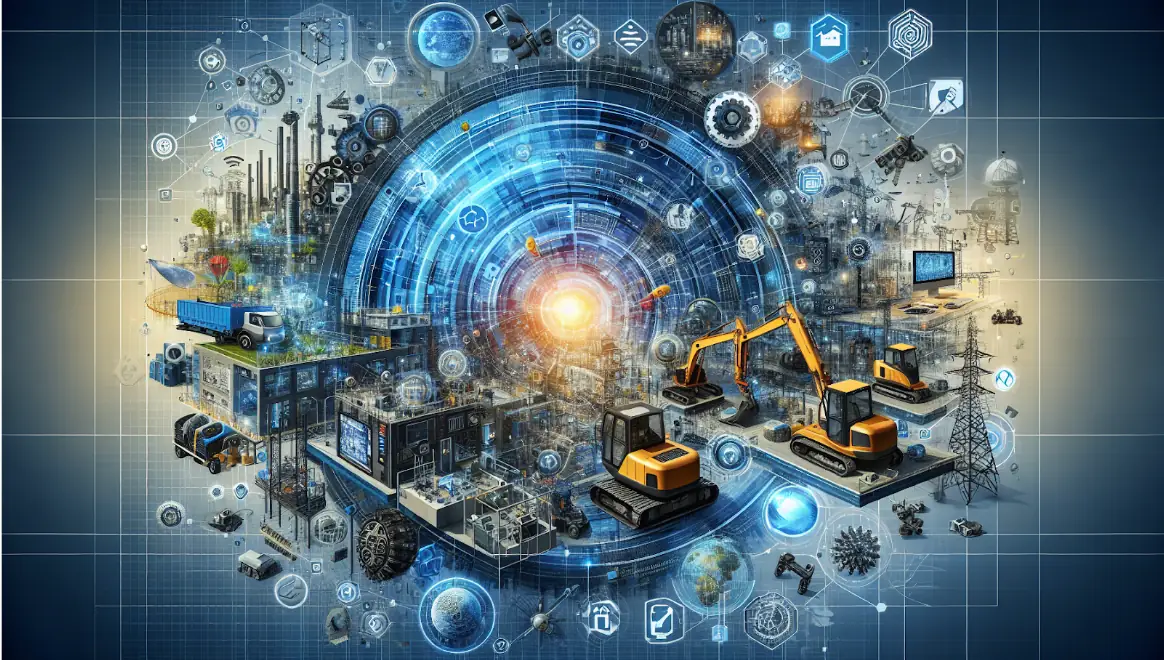
Innovations in Construction: Transforming Machinery and Equipment
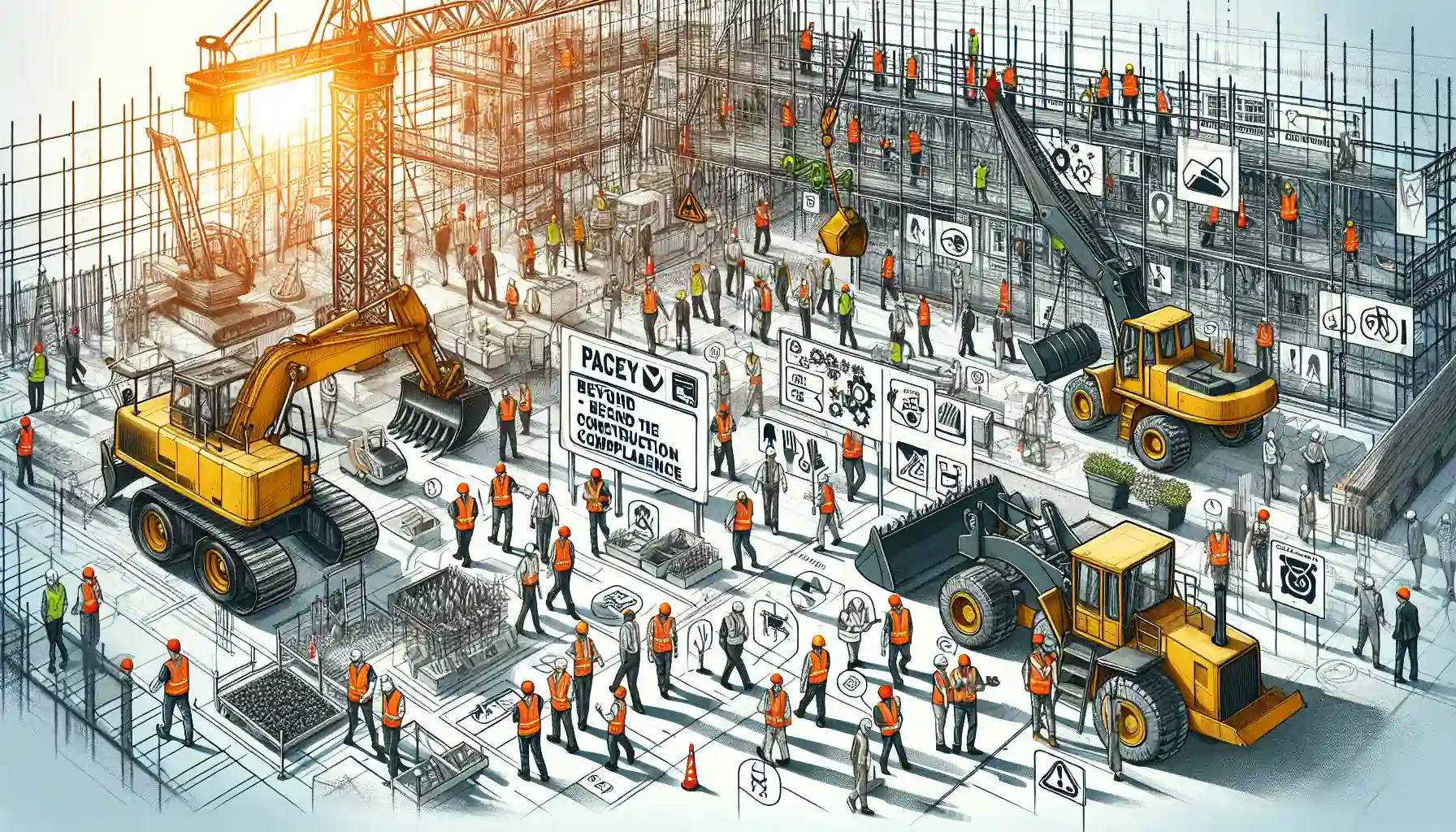
Heavy Equipment Safety: Beyond the Basics in Construction Compliance
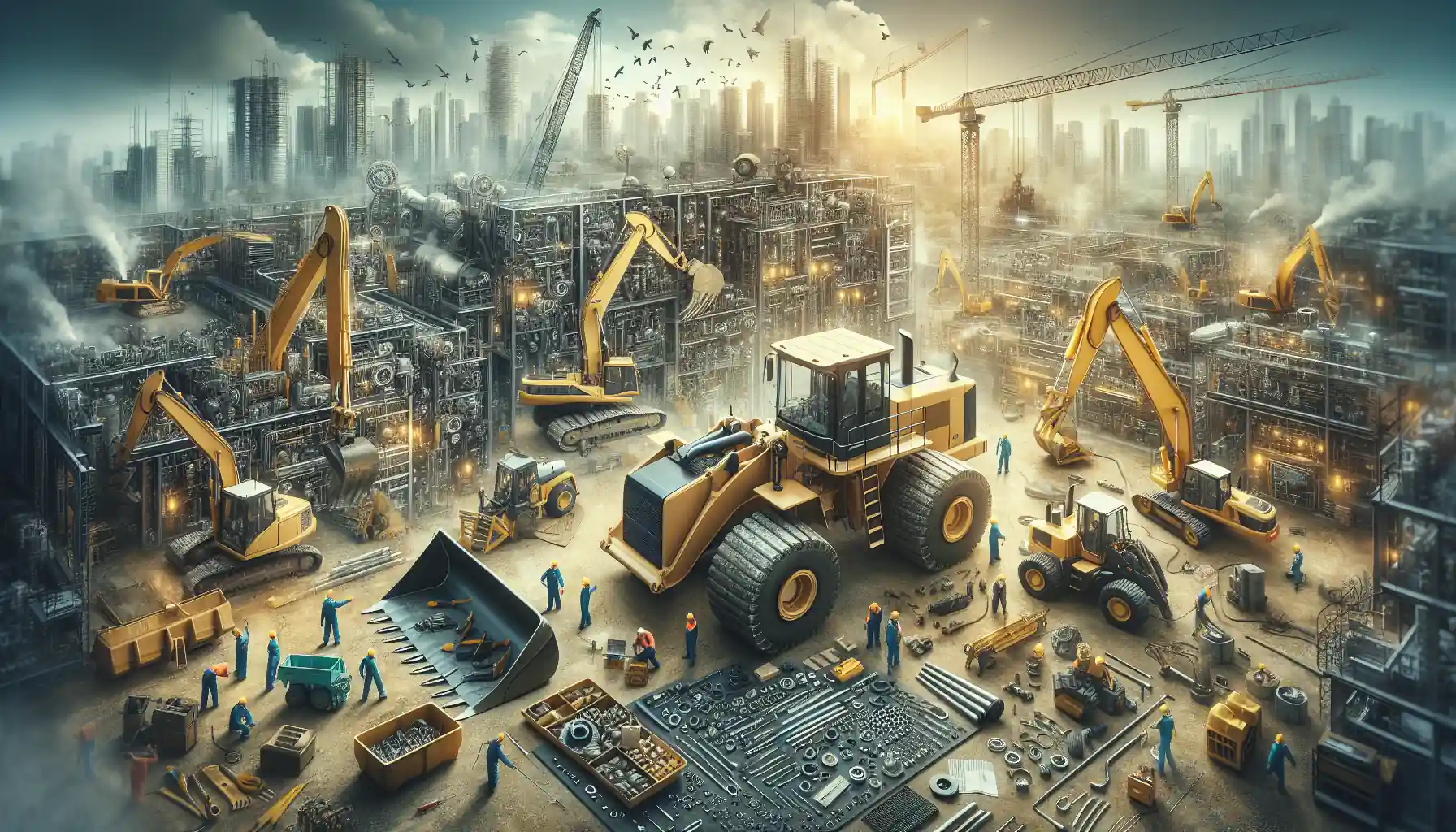
The Essential Handbook for Construction Equipment Repair and Maintenance
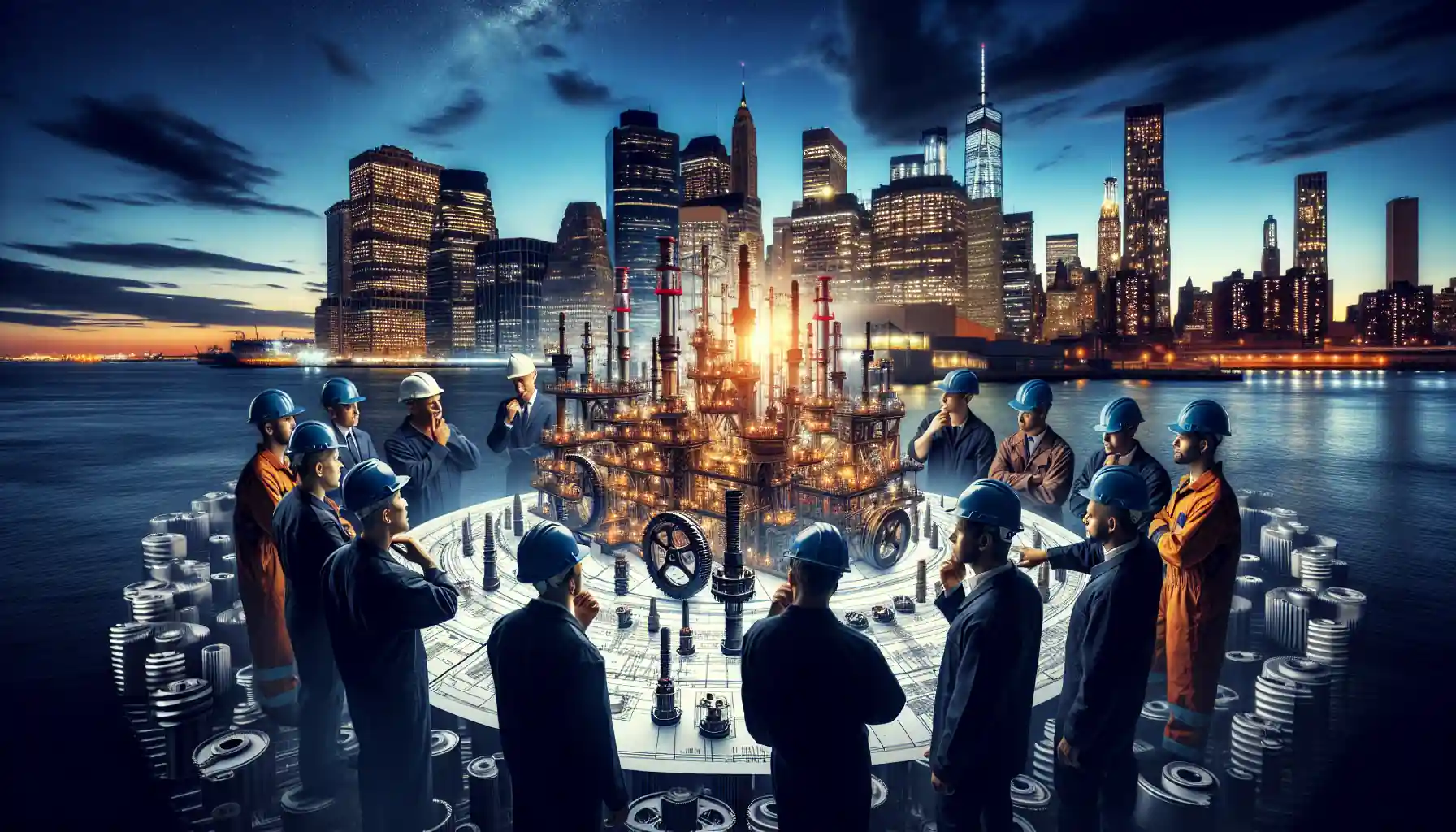
How to Efficiently Source Oil and Gas Machinery Parts in NYC
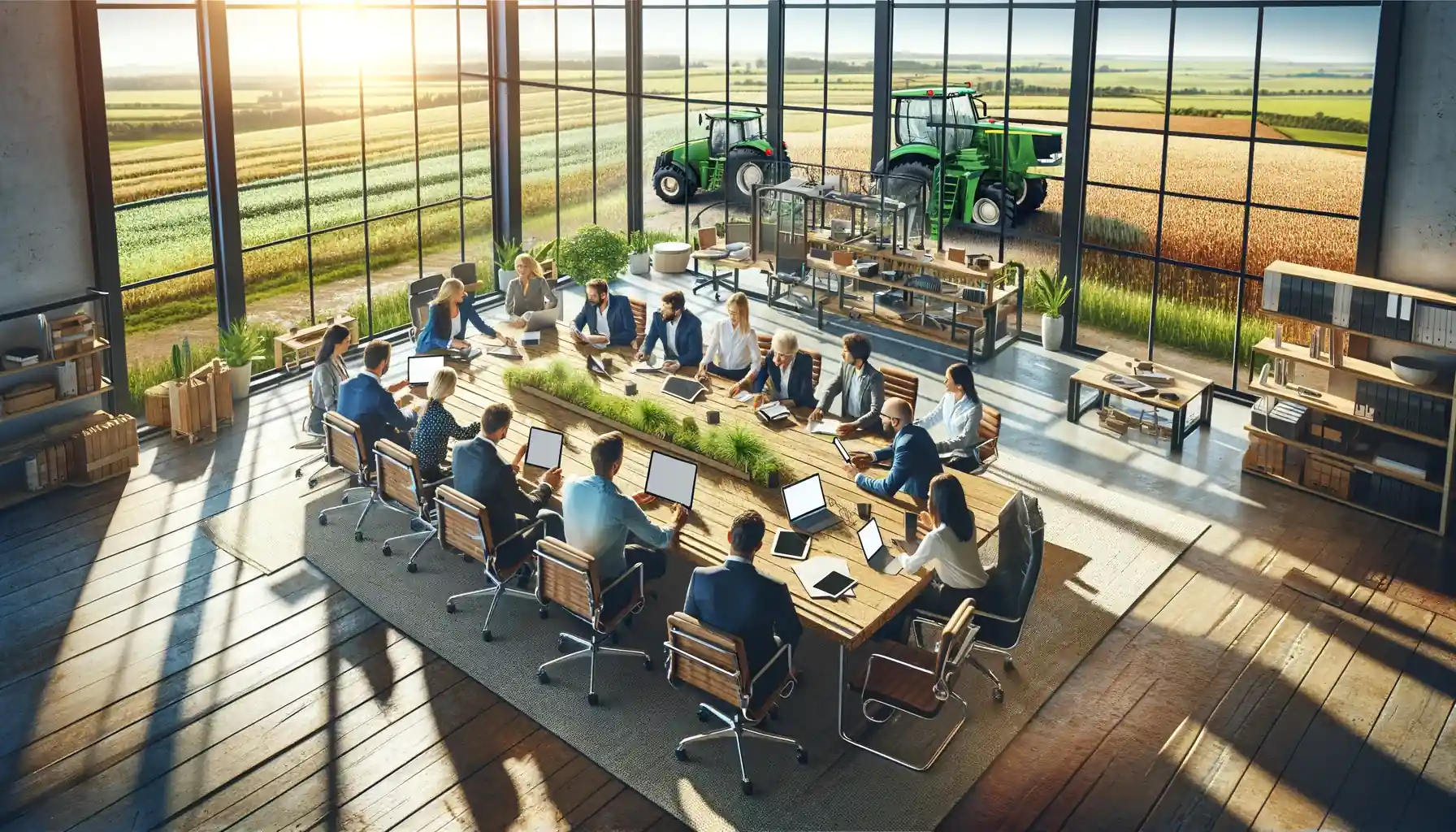
Essential Guide to Sourcing Agriculture Equipment Parts
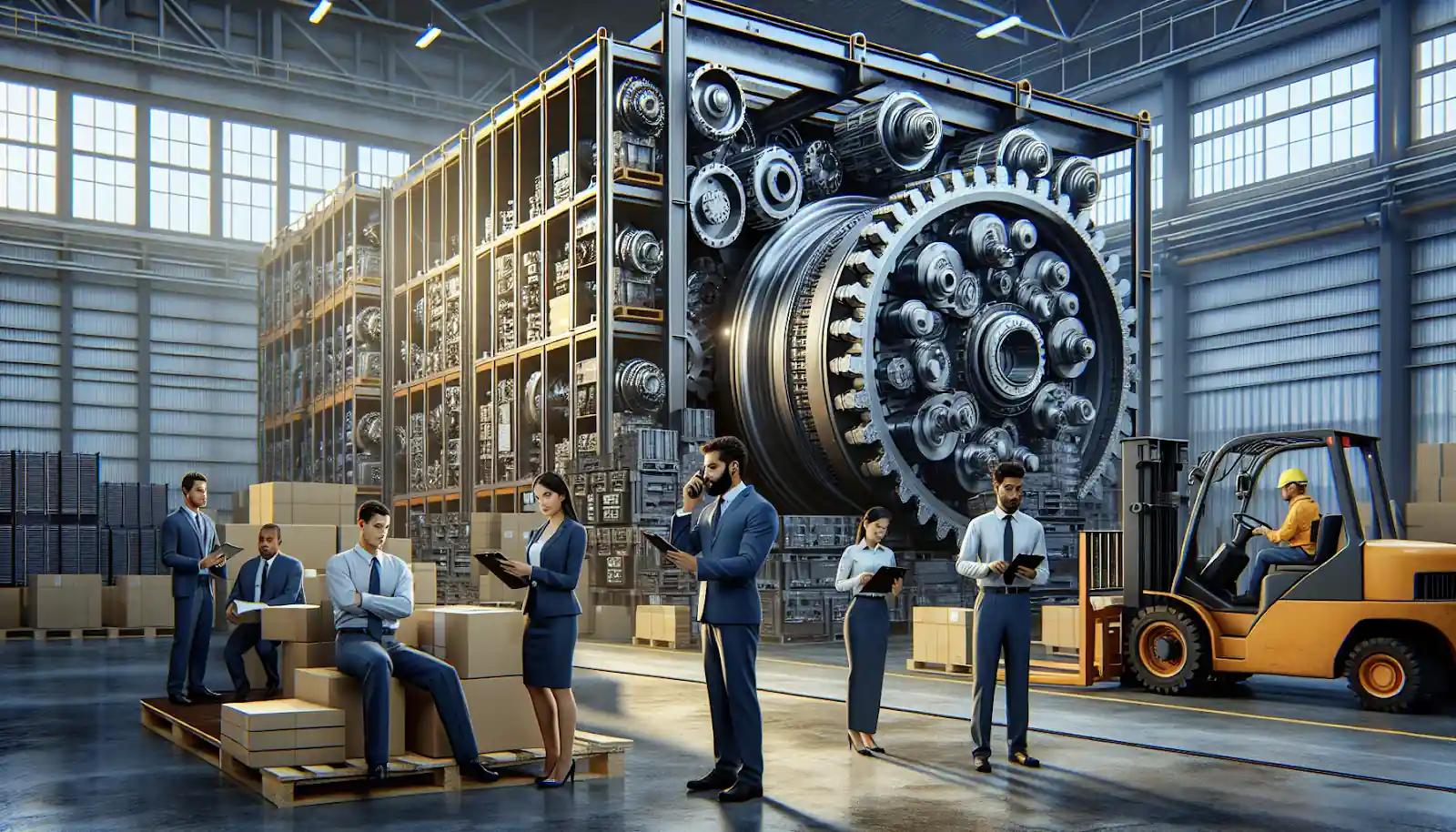
How to Source Mining Machinery Parts: Tips and Strategies
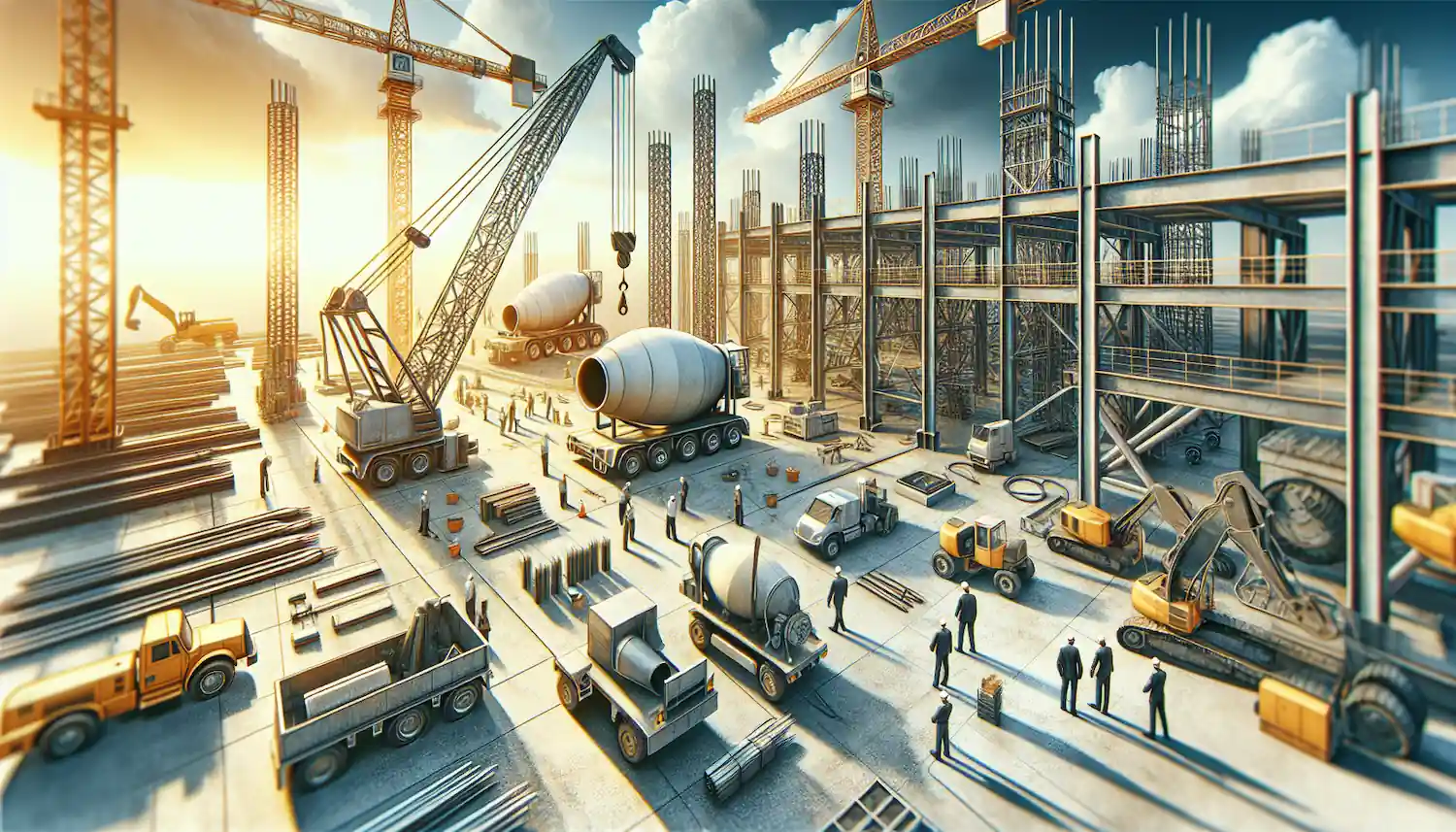